- お役立ち記事
- Welding robot technology and its application in industry
Welding robot technology and its application in industry
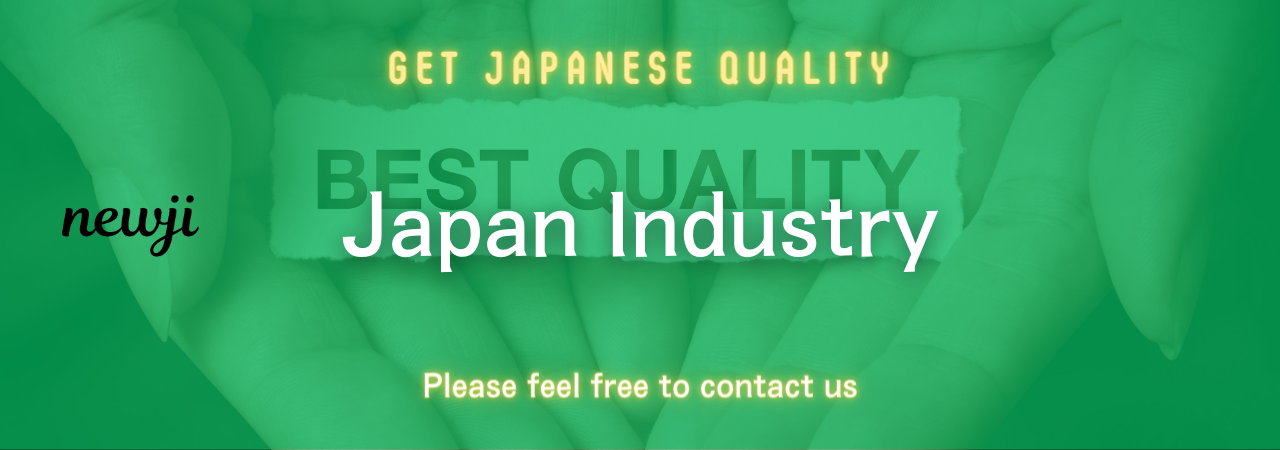
目次
What is Welding Robot Technology?
Welding robot technology refers to the use of automated machines designed to perform welding tasks.
These robots are equipped with advanced tools and software that allow them to weld various materials like metals and plastics with high precision.
The technology makes use of sensors, controllers, and actuators to complete tasks that usually require skilled human labor.
How Welding Robots Work
Welding robots typically consist of a robotic arm, welding head, power supply, control system, and positioning fixtures.
The arm can move in multiple directions to position the welding head exactly where it is needed.
The control system programs the movements and controls the welding parameters such as current, voltage, and speed.
Sensors help the robot to adapt to different work environments and materials, increasing efficiency and accuracy.
Types of Welding Robots
There are different types of welding robots designed to meet specific needs in various industries.
The most common types include arc welding robots, spot welding robots, and laser welding robots.
Arc welding robots use electric arcs to melt and join metals, while spot welding robots use electrical resistance to fuse metal surfaces together.
Laser welding robots use high-energy laser beams to make precise welds, often used in intricate applications like electronics and aerospace.
Benefits of Welding Robots
Welding robots offer numerous advantages, making them indispensable in modern manufacturing.
They ensure consistent quality with high precision, significantly reducing the chances of errors and defects.
Speed is another major benefit; welding robots can perform tasks much faster than human welders.
This improves productivity and reduces production time.
Additionally, they enhance safety in the workplace by performing dangerous tasks, thereby reducing the risk of accidents and injuries.
Long-term cost savings are also a notable benefit, as automation reduces the reliance on manual labor, minimizing labor costs.
Applications of Welding Robots in Industry
Welding robots are widely used across various industries to meet different manufacturing and production needs.
Automotive Industry
One of the most significant applications of welding robots is in the automotive industry.
Robots are used in the assembly lines to weld car frames, body panels, and components with high efficiency and accuracy.
Automation ensures that every weld is performed to a high standard, improving the strength and durability of vehicles.
The speed of robotic welding also enables car manufacturers to meet high production targets and adapt to changing market demands.
Aerospace Industry
The aerospace industry also benefits from welding robots, particularly in the manufacturing of aircraft components.
The precision offered by robotic welding is essential for ensuring the structural integrity and safety of aircraft.
Robots are used to weld parts of the fuselage, wings, and other critical components.
Moreover, their ability to work with advanced materials like titanium and composites makes them invaluable in this industry.
Electronics Industry
Welding robots are increasingly used in the electronics industry for tasks that require extreme precision.
They are employed to weld tiny components on circuit boards, connectors, and other electronic devices.
Laser welding robots, in particular, are well-suited for these applications as they can produce very fine welds without damaging delicate parts.
Automation ensures consistency and reliability, which are crucial for the performance of electronic products.
Future Trends in Welding Robot Technology
The future of welding robot technology is promising, with continuous advancements that are set to revolutionize manufacturing further.
Artificial Intelligence and Machine Learning
Artificial Intelligence (AI) and Machine Learning (ML) are playing an increasingly important role in welding robot technology.
AI-driven robots can analyze vast amounts of data to optimize welding parameters, adapt to new materials, and predict potential issues before they occur.
Machine learning algorithms enable these robots to improve over time, becoming more efficient and accurate with every task they perform.
Such advancements will further enhance the capabilities of welding robots, making them even more valuable in industrial applications.
Collaborative Robots
Collaborative robots, or cobots, are designed to work alongside human workers, combining the strengths of both.
These robots are equipped with advanced sensors and safety features that allow them to operate in close proximity to humans without causing harm.
Cobots can take on repetitive and physically demanding welding tasks, allowing human workers to focus on more complex and creative aspects of their jobs.
The use of collaborative robots is expected to increase productivity and improve working conditions in many industries.
Advanced Materials and Techniques
The development of new materials and welding techniques continues to push the boundaries of what welding robots can achieve.
Innovations in materials science are leading to the creation of stronger and lighter components, which require specialized welding processes.
Robotic welding systems are being updated to handle these advanced materials and techniques, ensuring that they remain at the forefront of industrial manufacturing.
This adaptability makes welding robots an essential part of the future industrial landscape.
Conclusion
Welding robot technology has become a cornerstone of modern manufacturing, offering numerous benefits such as increased productivity, precision, and safety.
Its applications span across various industries, from automotive to aerospace to electronics.
With ongoing advancements in AI, machine learning, and materials science, the capabilities of welding robots are set to grow even further.
As a result, they will continue to play a crucial role in shaping the future of industrial production, driving efficiency and innovation at every turn.
資料ダウンロード
QCD調達購買管理クラウド「newji」は、調達購買部門で必要なQCD管理全てを備えた、現場特化型兼クラウド型の今世紀最高の購買管理システムとなります。
ユーザー登録
調達購買業務の効率化だけでなく、システムを導入することで、コスト削減や製品・資材のステータス可視化のほか、属人化していた購買情報の共有化による内部不正防止や統制にも役立ちます。
NEWJI DX
製造業に特化したデジタルトランスフォーメーション(DX)の実現を目指す請負開発型のコンサルティングサービスです。AI、iPaaS、および先端の技術を駆使して、製造プロセスの効率化、業務効率化、チームワーク強化、コスト削減、品質向上を実現します。このサービスは、製造業の課題を深く理解し、それに対する最適なデジタルソリューションを提供することで、企業が持続的な成長とイノベーションを達成できるようサポートします。
オンライン講座
製造業、主に購買・調達部門にお勤めの方々に向けた情報を配信しております。
新任の方やベテランの方、管理職を対象とした幅広いコンテンツをご用意しております。
お問い合わせ
コストダウンが利益に直結する術だと理解していても、なかなか前に進めることができない状況。そんな時は、newjiのコストダウン自動化機能で大きく利益貢献しよう!
(Β版非公開)