- お役立ち記事
- DX for Pareto charts enables drastic quality improvement
DX for Pareto charts enables drastic quality improvement
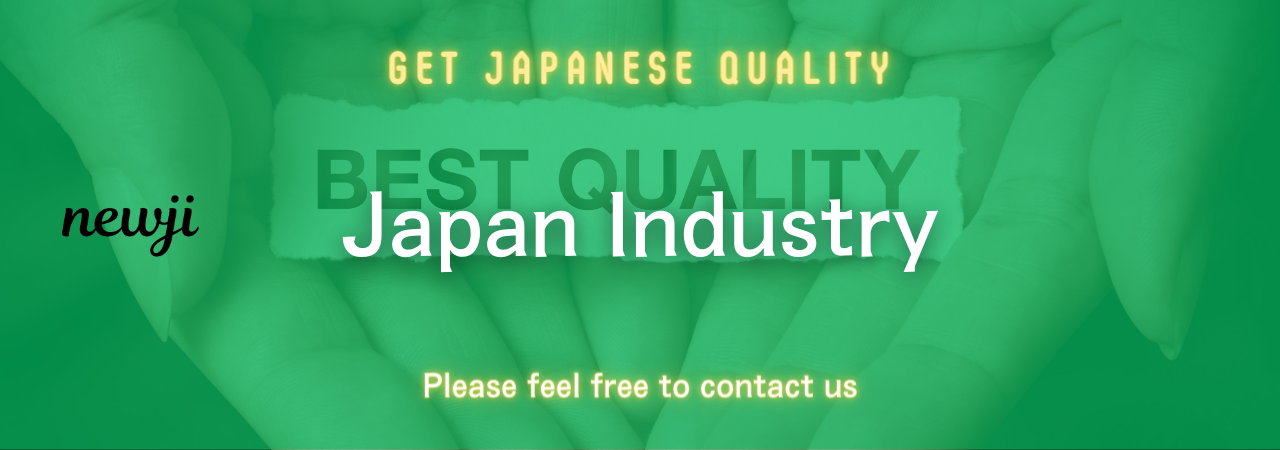
Digital Transformation (DX) is revolutionizing various industries, and quality control is no exception. One key tool in the realm of quality improvement is the Pareto chart. This powerful chart, named after the Italian economist Vilfredo Pareto, helps identify the most significant factors affecting quality. By integrating DX with Pareto charts, businesses can achieve drastic quality improvements.
目次
Understanding Pareto Charts
A Pareto chart is a type of bar graph that displays values in descending order. The tallest bars on the left represent the most significant factors, while the shorter bars on the right show lesser factors. This visual representation helps businesses identify the “vital few” causes that lead to the majority of problems.
The principle behind Pareto charts is the 80/20 rule. This rule suggests that 80% of problems are caused by 20% of the issues. By focusing on this critical 20%, businesses can make significant strides in quality improvement.
The Role of Digital Transformation
Digital Transformation (DX) involves the integration of digital technology into all areas of a business. This transformation results in fundamental changes to how businesses operate and deliver value to customers. When applied to quality control, DX can enhance the effectiveness of Pareto charts.
Data Collection and Analysis
One of the challenges with traditional Pareto charts is data collection and analysis. Gathering accurate and comprehensive data can be time-consuming and prone to errors. However, DX simplifies this process. By utilizing IoT devices and sensors, businesses can collect real-time data on various processes.
This data can be automatically fed into software that generates Pareto charts. Advanced analytics tools can then provide deeper insights into the causes of quality issues. This integration of technology ensures that businesses have accurate and up-to-date information for their quality improvement initiatives.
Automated Reporting
Another advantage of DX in the context of Pareto charts is automated reporting. Traditional Pareto analysis often requires manual data entry and report generation. This process can be labor-intensive and error-prone.
DX automates these tasks, allowing for real-time updates and reports. Software solutions can generate Pareto charts automatically based on the latest data. This immediacy ensures that businesses can quickly identify and address quality issues.
Enhanced Visualization
Digital tools offer enhanced visualization options for Pareto charts. Traditional charts can be static and limited in their ability to convey information. However, digital solutions provide interactive and dynamic charts.
Users can drill down into specific data points, zoom in on particular sections of the chart, and explore various aspects of the data. This interactivity improves understanding and allows for more informed decision-making.
Case Studies of DX-Enhanced Pareto Charts
Let’s explore some real-world examples of how businesses have leveraged DX to enhance their Pareto charts and improve quality.
Manufacturing Industry
In the manufacturing industry, quality control is paramount. A leading automotive manufacturer implemented IoT sensors throughout their production line. These sensors collected real-time data on various aspects of the production process.
Using advanced analytics software, the data was automatically fed into Pareto charts. The charts highlighted the most significant causes of defects in the production line. With this information, the manufacturer was able to target specific areas for improvement, resulting in a significant reduction in defects and an increase in overall quality.
Healthcare Sector
The healthcare sector also benefits from DX-enhanced Pareto charts. A major hospital implemented electronic health records (EHR) and other digital tools to collect data on patient care.
This data was analyzed using Pareto charts to identify the most common causes of medical errors. By focusing on these critical areas, the hospital was able to implement targeted interventions. As a result, they saw a notable decrease in medical errors and an improvement in patient outcomes.
Best Practices for Implementing DX with Pareto Charts
To achieve drastic quality improvements through the integration of DX with Pareto charts, businesses should follow these best practices:
Invest in Advanced Technology
Investing in advanced technology is crucial. This includes IoT devices, sensors, data analytics tools, and automation software. These technologies ensure accurate data collection, real-time analysis, and automated reporting.
Train Employees
Proper training is essential for successful DX implementation. Employees should be trained to use new technologies and understand the importance of data-driven decision-making. This ensures that everyone is on the same page and can contribute effectively to quality improvement initiatives.
Regularly Update Systems
Regular updates to systems and software are necessary to keep up with the latest advancements. Technology is constantly evolving, and staying updated ensures that businesses can continue to benefit from the latest tools and capabilities.
Start Small and Scale Up
It’s advisable to start small and gradually scale up the implementation. Begin with a pilot project to test the integration of DX with Pareto charts. Once successful, gradually expand the implementation to other areas of the business.
Conclusion
Digital Transformation (DX) is a game-changer in the field of quality control. Integrating DX with Pareto charts enables businesses to achieve drastic quality improvements. Through enhanced data collection and analysis, automated reporting, and interactive visualization, businesses can effectively identify and address the most significant quality issues.
Real-world examples from the manufacturing and healthcare sectors demonstrate the tangible benefits of this integration. By following best practices and harnessing the power of advanced technology, businesses can revolutionize their quality control processes and deliver superior value to their customers.
資料ダウンロード
QCD調達購買管理クラウド「newji」は、調達購買部門で必要なQCD管理全てを備えた、現場特化型兼クラウド型の今世紀最高の購買管理システムとなります。
ユーザー登録
調達購買業務の効率化だけでなく、システムを導入することで、コスト削減や製品・資材のステータス可視化のほか、属人化していた購買情報の共有化による内部不正防止や統制にも役立ちます。
NEWJI DX
製造業に特化したデジタルトランスフォーメーション(DX)の実現を目指す請負開発型のコンサルティングサービスです。AI、iPaaS、および先端の技術を駆使して、製造プロセスの効率化、業務効率化、チームワーク強化、コスト削減、品質向上を実現します。このサービスは、製造業の課題を深く理解し、それに対する最適なデジタルソリューションを提供することで、企業が持続的な成長とイノベーションを達成できるようサポートします。
オンライン講座
製造業、主に購買・調達部門にお勤めの方々に向けた情報を配信しております。
新任の方やベテランの方、管理職を対象とした幅広いコンテンツをご用意しております。
お問い合わせ
コストダウンが利益に直結する術だと理解していても、なかなか前に進めることができない状況。そんな時は、newjiのコストダウン自動化機能で大きく利益貢献しよう!
(Β版非公開)