- お役立ち記事
- DX in the intertwining process enables production of high-strength twisted yarns
DX in the intertwining process enables production of high-strength twisted yarns
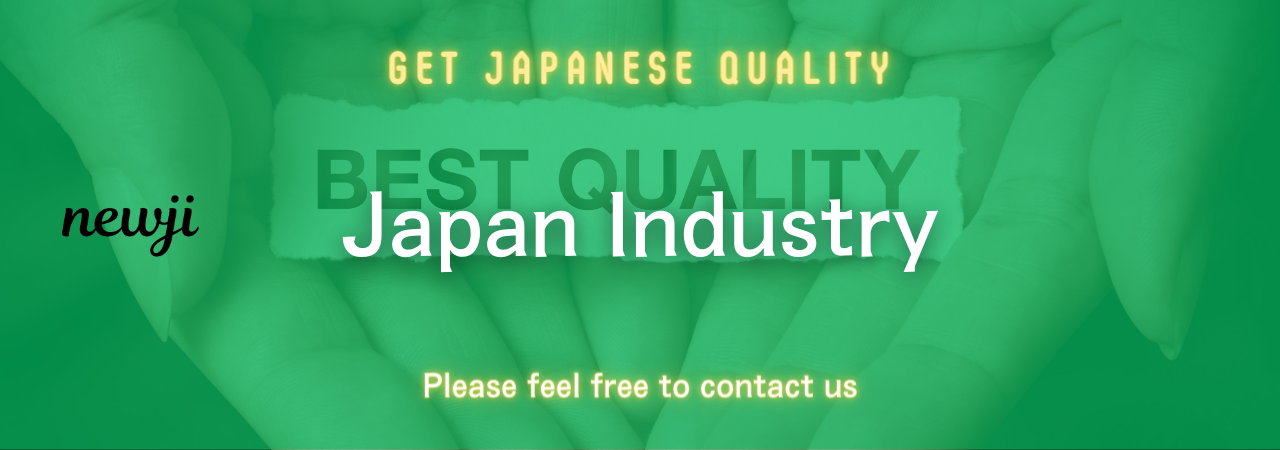
In an age dominated by innovation and efficiency, the textile industry is not left behind.
Digital transformation, known as DX, is revolutionizing traditional practices, offering new opportunities and improving existing processes.
One such significant process in the textile world is the production of high-strength twisted yarns, which is undergoing impressive changes through the adoption of digital tools and methodologies.
目次
Understanding Twisted Yarn Production
Twisted yarn, also referred to as ply yarn, is created by twisting two or more single yarns together.
This process not only enhances the yarn’s strength but also adds to its durability and elasticity.
These characteristics make twisted yarns a preferred choice in various applications, including sewing, knitting, and weaving.
However, achieving the desired quality in twisted yarn involves several intricate steps.
Traditional methods rely heavily on human expertise and manual adjustments, which can yield inconsistent results and require significant labor and time.
The Role of Digital Transformation (DX)
Digital transformation (DX) refers to integrating digital technology into all areas of a business, fundamentally changing how it operates and delivers value to customers.
In the context of twisted yarn production, DX offers several benefits:
1. Automation and Precision
Automated systems equipped with sensors and advanced algorithms ensure that the twisting process is controlled with high precision.
This reduces human error, leading to more consistent yarn quality.
2. Data-Driven Insights
Modern machinery can collect vast amounts of data during production.
This data helps in gaining insights into various factors affecting the yarn’s quality, such as tension, twist angle, and environmental conditions.
Analyzing this data allows improvements to the process, ensuring optimal yarn strength and consistency.
3. Enhanced Efficiency
Digital tools can streamline steps in the production process, reducing time and labor costs.
For instance, processes like spinning, twisting, and winding can be integrated into a seamless operation.
This increases overall productivity.
4. Real-Time Monitoring and Adjustments
Real-time monitoring systems enable immediate detection and correction of any deviations.
This ensures that all yarns produced meet the required specifications without having to halt production frequently.
Implementing DX in Twisted Yarn Production
Implementing DX in twisted yarn production involves adopting various technologies and practices:
1. Advanced Machinery
Adopting modern spinning and twisting machines equipped with sensors and control systems is crucial.
These machines are designed for precision and efficiency, allowing for exact control over the twisting process and ensuring uniformity in the yarn.
2. IoT Integration
The Internet of Things (IoT) connects equipment to a central system, allowing for real-time data collection and communication between machines.
Interconnected machines can adjust operations based on the data gathered, optimizing the production process dynamically.
3. Predictive Maintenance
With data analytics, it’s possible to predict when a machine might fail or require maintenance.
This approach reduces unexpected downtimes and keeps production running smoothly.
4. Machine Learning Algorithms
Machine learning algorithms can analyze production data to identify patterns and suggest improvements.
These algorithms can optimize parameters such as speed, tension, and temperature to produce high-quality yarn consistently.
Challenges and Considerations
While DX offers numerous advantages, its implementation comes with challenges that need to be addressed:
1. Initial Investment
Upgrading or replacing traditional machinery with advanced systems requires significant investment.
However, considering the long-term benefits in quality and efficiency, this investment can pay off over time.
2. Training and Skill Development
Workers need to be trained to operate and maintain new digital systems.
Investing in training programs ensures that employees can handle advanced machinery effectively.
3. Data Security
With increased digitization, the risk of cyber-attacks also rises.
Ensuring robust cybersecurity measures is essential to protect sensitive production data and maintain operational integrity.
4. Integration with Existing Processes
Integrating new technologies with current processes can be complex.
A phased approach, starting with pilot projects, can help in smooth integration and minimal disruption.
The Future of Twisted Yarn Production
The future of twisted yarn production looks promising with ongoing advancements in digital technologies:
1. Artificial Intelligence
AI can provide deeper insights and automate more complex decision-making processes.
In twisted yarn production, AI can help in predicting quality issues and suggesting real-time adjustments.
2. Augmented Reality (AR) and Virtual Reality (VR)
AR and VR can be used for training workers in a virtual environment, providing hands-on experience without the risks of actual production scenarios.
This can improve skill levels and reduce learning curves.
3. Blockchain Technology
Blockchain can offer transparency and traceability in the production process.
Consumers can verify the origin and authenticity of the yarn, ensuring ethical sourcing and manufacturing practices.
4. Sustainable Practices
DX enables more efficient use of resources, reducing waste and energy consumption.
Incorporating sustainable practices in the production process can lead to eco-friendly and cost-effective operations.
Digital transformation in the intertwining process of producing high-strength twisted yarns exemplifies how technological advancements can improve traditional industries.
Through precise automation, data-driven insights, and real-time monitoring, DX not only enhances the quality and consistency of yarn but also boosts efficiency and reduces costs.
Although there are challenges, the long-term rewards make the investment worthwhile.
As technologies like AI, AR, VR, and blockchain continue to evolve, the future of twisted yarn production is set to become even more innovative, efficient, and sustainable.
資料ダウンロード
QCD調達購買管理クラウド「newji」は、調達購買部門で必要なQCD管理全てを備えた、現場特化型兼クラウド型の今世紀最高の購買管理システムとなります。
ユーザー登録
調達購買業務の効率化だけでなく、システムを導入することで、コスト削減や製品・資材のステータス可視化のほか、属人化していた購買情報の共有化による内部不正防止や統制にも役立ちます。
NEWJI DX
製造業に特化したデジタルトランスフォーメーション(DX)の実現を目指す請負開発型のコンサルティングサービスです。AI、iPaaS、および先端の技術を駆使して、製造プロセスの効率化、業務効率化、チームワーク強化、コスト削減、品質向上を実現します。このサービスは、製造業の課題を深く理解し、それに対する最適なデジタルソリューションを提供することで、企業が持続的な成長とイノベーションを達成できるようサポートします。
オンライン講座
製造業、主に購買・調達部門にお勤めの方々に向けた情報を配信しております。
新任の方やベテランの方、管理職を対象とした幅広いコンテンツをご用意しております。
お問い合わせ
コストダウンが利益に直結する術だと理解していても、なかなか前に進めることができない状況。そんな時は、newjiのコストダウン自動化機能で大きく利益貢献しよう!
(Β版非公開)