- お役立ち記事
- Role and Effectiveness of Gate Stacking in Manufacturing
Role and Effectiveness of Gate Stacking in Manufacturing
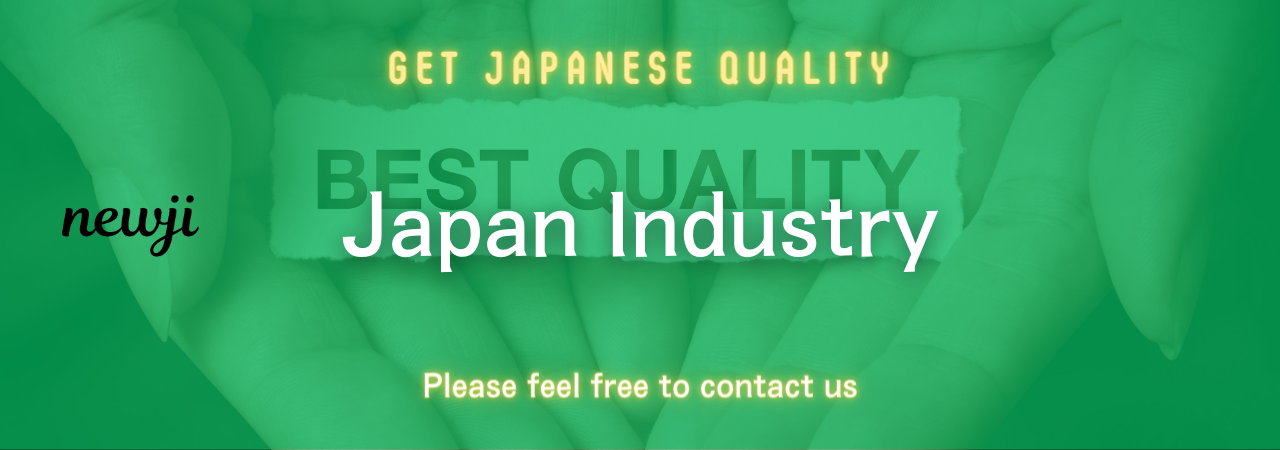
Gate stacking has become a significant innovation in the manufacturing sector.
It is a technique that enhances the performance and efficiency of microchips and other electronic components.
In this article, we’ll explore the role and effectiveness of gate stacking in manufacturing.
目次
What is Gate Stacking?
Gate stacking is a process used in semiconductor manufacturing.
It involves layering multiple gate materials over each other to create a gate electrode.
The gate electrode controls the flow of electricity in transistors.
These are fundamental components in microchips.
With gate stacking, manufacturers can create smaller, more efficient transistors.
These transistors have improved performance compared to traditional single-layer gates.
Why is Gate Stacking Important?
Gate stacking offers several advantages that make it crucial in modern electronics:
1. **Enhanced Performance**: By stacking gates, the performance of transistors is significantly boosted.
This allows for faster processing speeds and improved electrical efficiency.
2. **Size Reduction**: Gate stacking enables the production of smaller transistors.
This is essential as devices continue to shrink in size.
It allows for more components to be packed into a single microchip.
3. **Energy Efficiency**: Smaller and more efficient transistors consume less power.
This results in longer battery life for portable electronics and reduced energy costs for larger systems.
The Process of Gate Stacking
Gate stacking involves several steps.
It starts with the deposition of various materials onto a semiconductor substrate.
These materials often include metals, dielectrics, and other conductive or insulating substances.
Material Selection
Choosing the right materials is essential.
The materials must have specific electrical properties to ensure optimal performance.
1. **High-k Dielectrics**: These are used to isolate the gate electrode from the semiconductor substrate.
They have a high dielectric constant, which helps reduce leakage currents and power consumption.
2. **Metal Gates**: Different metals can be used for the gate electrode, each with its unique properties.
Common choices include titanium nitride (TiN) and tantalum nitride (TaN).
Deposition Techniques
Once the materials are selected, they need to be deposited onto the substrate.
Several techniques can be used for this, including:
1. **Physical Vapor Deposition (PVD)**: This involves vaporizing the material and then condensing it onto the substrate.
2. **Chemical Vapor Deposition (CVD)**: In this method, chemical reactions are used to deposit the material onto the substrate.
3. **Atomic Layer Deposition (ALD)**: This is a more precise technique that allows for the deposition of extremely thin layers.
It’s especially useful for creating the high-k dielectric layer.
Challenges and Solutions in Gate Stacking
While gate stacking offers many benefits, it also presents several challenges.
Integration Issues
Integrating multiple layers of different materials can be complex.
The materials must be compatible with each other and with the semiconductor substrate.
To overcome this, advanced modeling and simulation tools are used.
These tools help predict how the materials will interact and ensure optimal performance.
Cost Concerns
The materials and techniques used in gate stacking can be expensive.
However, the long-term benefits often outweigh the initial costs.
Energy savings and enhanced performance can lead to significant cost reductions over time.
Manufacturing Precision
Achieving the necessary precision in layer thickness and uniformity can be difficult.
State-of-the-art fabrication equipment and rigorous quality control measures are essential.
These ensure that the layers are deposited accurately and consistently.
Applications of Gate Stacking
Gate stacking is used in a variety of applications, ranging from consumer electronics to industrial systems.
Microprocessors
Gate stacking is extensively used in the production of microprocessors.
These are the brains of computers and other electronic devices.
The performance improvements offered by gate stacking result in faster and more efficient computing.
Memory Chips
Memory chips also benefit from gate stacking.
These chips store data in electronic devices.
Smaller and more efficient transistors allow for greater data storage capacity.
Mobile Devices
Mobile devices, such as smartphones and tablets, rely heavily on gate-stacked microchips.
These chips contribute to the compact size and long battery life of modern mobile electronics.
Automotive Electronics
The automotive industry also utilizes gate stacking in various electronic systems.
These include engine control units, infotainment systems, and advanced driver-assistance systems (ADAS).
The increased performance and reliability of gate-stacked components enhance the functionality and safety of vehicles.
The Future of Gate Stacking
The potential for gate stacking in manufacturing is immense.
As technology continues to advance, we can expect further innovations and improvements.
Scaling Down
One of the key trends is the continued scaling down of transistor sizes.
Gate stacking will play a crucial role in enabling this miniaturization.
This will lead to even more powerful and energy-efficient electronic devices.
New Materials
Research is ongoing into new materials that can be used in gate stacking.
These materials could offer even better performance and compatibility.
Developments in this area promise to further enhance the effectiveness of gate stacking.
Integration with Other Technologies
Gate stacking is expected to integrate with other advanced technologies.
These include 3D chip stacking and quantum computing.
Such integrations could revolutionize the electronics industry.
In conclusion, gate stacking plays a vital role in modern manufacturing.
It offers numerous benefits, including enhanced performance, size reduction, and energy efficiency.
Despite its challenges, the future of gate stacking looks promising, with ongoing research and innovations paving the way.
This technology will continue to have a profound impact on the manufacturing and electronics sectors.
資料ダウンロード
QCD調達購買管理クラウド「newji」は、調達購買部門で必要なQCD管理全てを備えた、現場特化型兼クラウド型の今世紀最高の購買管理システムとなります。
ユーザー登録
調達購買業務の効率化だけでなく、システムを導入することで、コスト削減や製品・資材のステータス可視化のほか、属人化していた購買情報の共有化による内部不正防止や統制にも役立ちます。
NEWJI DX
製造業に特化したデジタルトランスフォーメーション(DX)の実現を目指す請負開発型のコンサルティングサービスです。AI、iPaaS、および先端の技術を駆使して、製造プロセスの効率化、業務効率化、チームワーク強化、コスト削減、品質向上を実現します。このサービスは、製造業の課題を深く理解し、それに対する最適なデジタルソリューションを提供することで、企業が持続的な成長とイノベーションを達成できるようサポートします。
オンライン講座
製造業、主に購買・調達部門にお勤めの方々に向けた情報を配信しております。
新任の方やベテランの方、管理職を対象とした幅広いコンテンツをご用意しております。
お問い合わせ
コストダウンが利益に直結する術だと理解していても、なかなか前に進めることができない状況。そんな時は、newjiのコストダウン自動化機能で大きく利益貢献しよう!
(Β版非公開)