- お役立ち記事
- Transfer System Utilization Know-How: Streamlining Press Forming
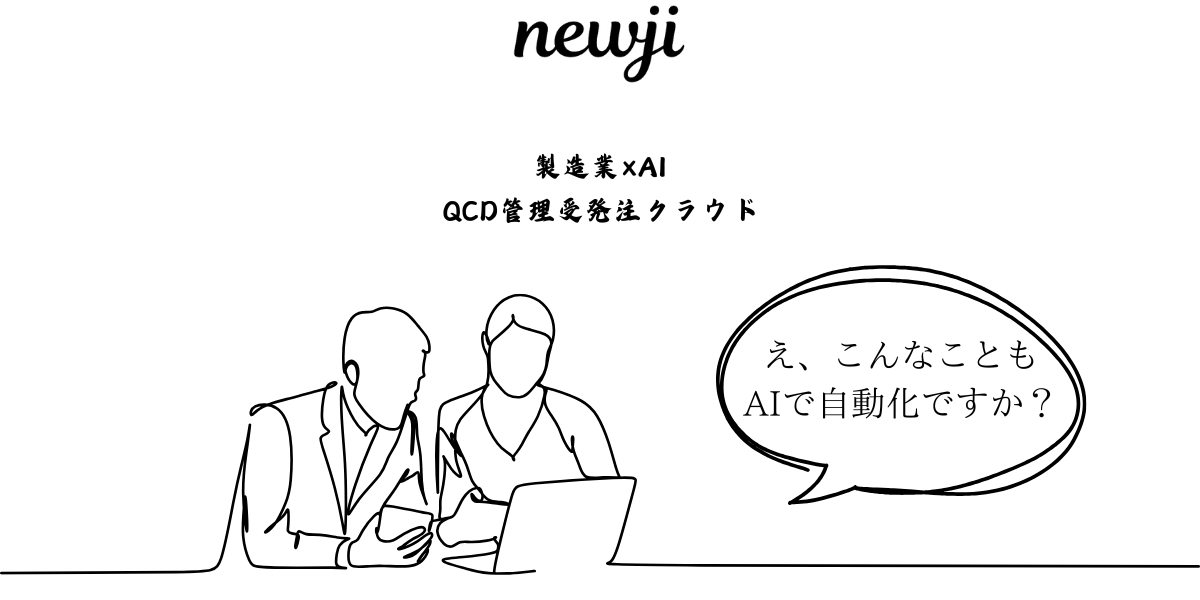
Transfer System Utilization Know-How: Streamlining Press Forming
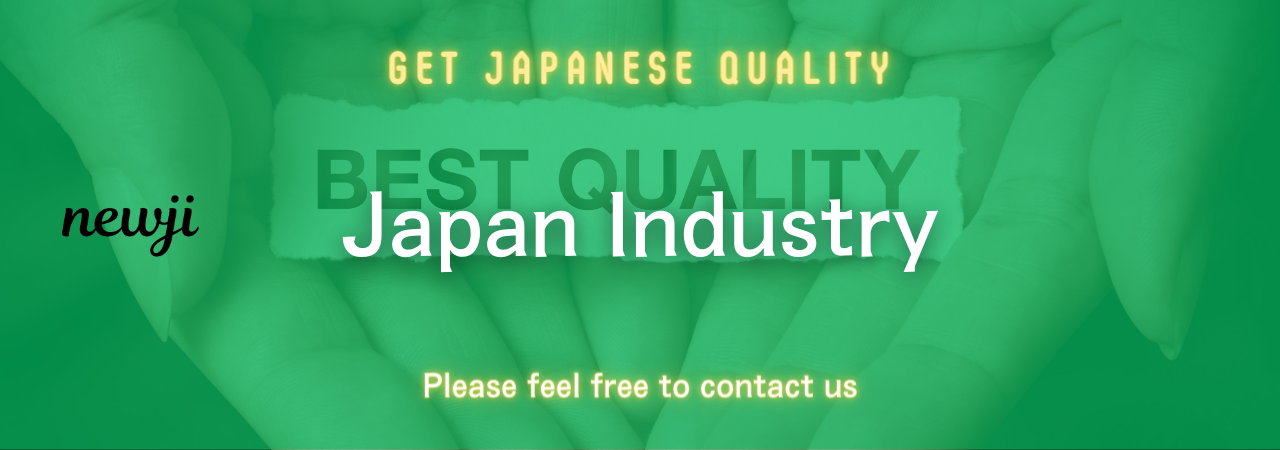
In the industrial world, efficiency is everything.
Meeting deadlines, maintaining quality, and reducing costs are crucial for every manufacturing process.
One such process that benefits significantly from these efficiency improvements is press forming.
The transfer system has emerged as a vital technological advancement, streamlining press forming and enhancing overall productivity.
This article delves into the utilization of a transfer system in press forming, highlighting how this technology transforms the manufacturing landscape.
目次
Understanding Press Forming
Press forming is a method used in manufacturing to shape metal sheets into desired forms.
It’s widely used in automotive, appliance, aerospace, and various other industries where precision and durability are paramount.
The process involves placing a sheet of metal into a press machine, which then shapes it using a die under high pressure.
This method can create complex shapes and maintain the structural integrity of metal workpieces, making it an indispensable process in modern industry.
Traditional methods of press forming, while effective, often involve manual handling, which can be time-consuming and error-prone.
Introducing the Transfer System
A transfer system in press forming is an automated mechanism that moves the workpieces through different stages of the forming process.
This system boosts the efficiency of press operations, minimizes human intervention, and reduces the likelihood of errors.
The transfer system typically consists of a series of automated conveyors, robots, or specialized transfer devices that work in tandem to move the metal sheets from one press to the next.
How It Works
The process begins with the loading of metal sheets into the system.
The transfer mechanism activates and moves the sheets to the first press station, where the initial forming takes place.
Once the first stage is complete, the system automatically transfers the partially formed metal to the next station for further processing.
This continues until the final product is completed.
The precisely timed movement and positioning of the workpieces ensure that each press operates at optimal efficiency, significantly reducing downtime and waste.
Benefits of Using a Transfer System
Increased Efficiency
One of the most significant benefits of a transfer system is the marked increase in operational efficiency.
By automating the movement of workpieces, the time taken between different stages of the press forming process is drastically reduced.
This results in a faster production cycle and higher throughput.
Automation also allows for continuous production with minimal interruptions, further boosting overall productivity.
With a transfer system, manufacturers can produce more units in less time, meeting higher demand without compromising on quality.
Improved Precision and Consistency
Manual handling in traditional press forming introduces variability and the potential for errors.
On the other hand, a transfer system ensures that each workpiece is accurately positioned and moved through the process without deviation.
This level of precision is crucial for maintaining the consistency and quality of the final product.
Enhanced Safety
The industrial environment often poses safety risks, particularly in processes involving heavy machinery and manual handling.
By automating the transfer of metal sheets, the transfer system minimizes human involvement in potentially hazardous tasks.
This reduces the risk of workplace accidents and injuries, creating a safer work environment for employees.
Cost Savings
While the initial investment in a transfer system may be significant, the long-term cost savings are substantial.
Increased efficiency, higher productivity, and reduced scrap rates all contribute to lower production costs.
Moreover, the improvement in safety can lead to fewer worker compensation claims and lower insurance premiums.
Implementing a Transfer System
Assessment and Planning
Before integrating a transfer system into the press forming process, a thorough assessment of the current operations is necessary.
Identify bottlenecks, inefficiencies, and areas that will benefit most from automation.
Based on this analysis, create a detailed plan outlining the implementation steps, required modifications, and expected outcomes.
Choosing the Right System
Several types of transfer systems are available, each suited to different needs and manufacturing environments.
Consider factors such as the size and complexity of the workpieces, space constraints, and budget when selecting a system.
Consulting with experts or vendors specializing in transfer systems can provide valuable insights and recommendations.
Integration and Training
Integrating a transfer system into existing operations requires careful coordination to minimize disruptions.
Work closely with the installation team to ensure a smooth transition and address any unforeseen issues promptly.
Additionally, invest in training for operators and maintenance staff to ensure they understand the new system and can operate it efficiently.
Future Trends in Transfer Systems
As technology continues to evolve, transfer systems are becoming more sophisticated and versatile.
Future advancements may include the integration of artificial intelligence and machine learning, further enhancing the automation and adaptability of these systems.
AI-powered transfer systems could predict maintenance needs, optimize scheduling, and even learn from past data to improve performance.
These innovations could revolutionize press forming, making it even more efficient and cost-effective.
Conclusion
The utilization of a transfer system in press forming represents a significant leap forward in manufacturing efficiency and productivity.
By automating the movement of workpieces, manufacturers can achieve faster production cycles, improved precision, enhanced safety, and substantial cost savings.
As technology continues to advance, the future of press forming looks even more promising, with smarter, more adaptable transfer systems leading the charge.
Embracing these innovations will undoubtedly empower industries to meet growing demands and maintain a competitive edge in the global market.
資料ダウンロード
QCD調達購買管理クラウド「newji」は、調達購買部門で必要なQCD管理全てを備えた、現場特化型兼クラウド型の今世紀最高の購買管理システムとなります。
ユーザー登録
調達購買業務の効率化だけでなく、システムを導入することで、コスト削減や製品・資材のステータス可視化のほか、属人化していた購買情報の共有化による内部不正防止や統制にも役立ちます。
NEWJI DX
製造業に特化したデジタルトランスフォーメーション(DX)の実現を目指す請負開発型のコンサルティングサービスです。AI、iPaaS、および先端の技術を駆使して、製造プロセスの効率化、業務効率化、チームワーク強化、コスト削減、品質向上を実現します。このサービスは、製造業の課題を深く理解し、それに対する最適なデジタルソリューションを提供することで、企業が持続的な成長とイノベーションを達成できるようサポートします。
オンライン講座
製造業、主に購買・調達部門にお勤めの方々に向けた情報を配信しております。
新任の方やベテランの方、管理職を対象とした幅広いコンテンツをご用意しております。
お問い合わせ
コストダウンが利益に直結する術だと理解していても、なかなか前に進めることができない状況。そんな時は、newjiのコストダウン自動化機能で大きく利益貢献しよう!
(Β版非公開)