- お役立ち記事
- Unlocking Innovation: How Ceramic Injection Molding Technology is Shaping Japanese Manufacturing
Unlocking Innovation: How Ceramic Injection Molding Technology is Shaping Japanese Manufacturing
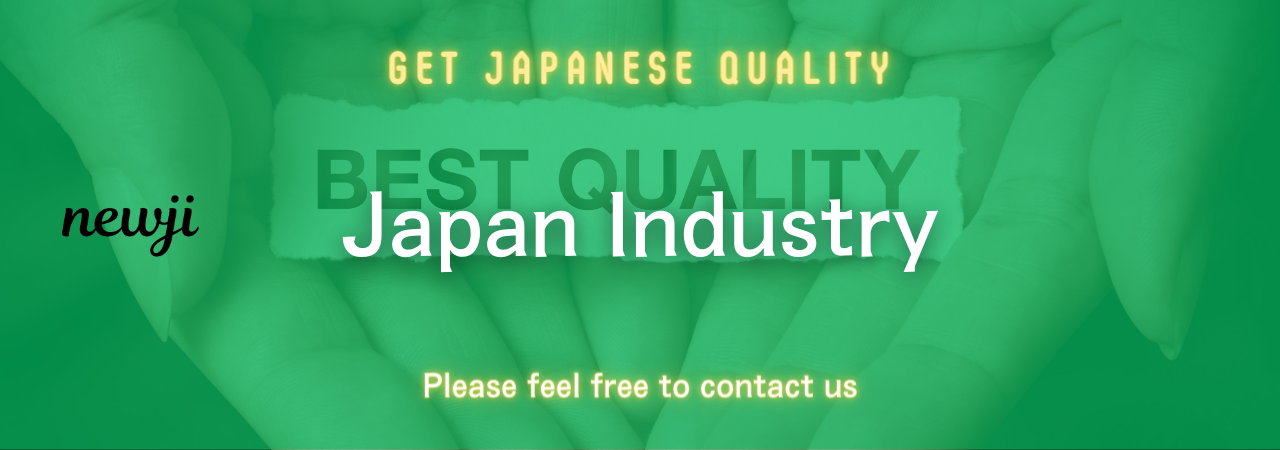
目次
Introduction
Ceramic Injection Molding (CIM) has emerged as a groundbreaking technology that is gradually transforming the landscape of manufacturing in Japan.
By combining the benefits of ceramic materials with the versatility of injection molding, this technology offers unprecedented opportunities for innovation.
In this article, we will delve into the world of CIM, exploring its practical applications, advantages, and disadvantages, as well as supplier negotiation techniques and market conditions.
We will also offer best practices for leveraging this technology effectively in your procurement and purchasing strategies.
The Basics of Ceramic Injection Molding
Ceramic Injection Molding is a form of material processing that combines powdered ceramic materials with polymer binders to produce complex shapes.
The process involves several stages, including feedstock preparation, injection molding, debinding, and sintering.
Feedstock Preparation
In this stage, ceramic powders are mixed with polymer binders to create a homogeneous feedstock.
This mixture is designed to have the right viscosity and flow characteristics for injection molding.
Injection Molding
The prepared feedstock is then injected into a mold cavity at high pressure.
This process allows for the creation of intricate shapes and fine details that would be difficult to achieve with traditional ceramic processing methods.
Debinding
After molding, the binder is removed through a debinding process.
This can be done either thermally or chemically, depending on the specific requirements of the ceramic material and end application.
Sintering
Finally, the debound ceramic part is sintered at high temperatures to achieve its final properties.
Sintering involves densifying the material by heating it just below its melting point, resulting in a solid, robust finished product.
Advantages of Ceramic Injection Molding
The adoption of Ceramic Injection Molding in manufacturing offers several key advantages.
Complex Geometries
CIM enables the production of highly complex and intricate geometries that would be challenging or impossible to achieve through conventional methods.
This capability is particularly advantageous in industries such as aerospace, medical devices, and automotive, where precision and intricate designs are paramount.
Material Properties
Ceramics are known for their excellent mechanical properties, including high hardness, wear resistance, and thermal stability.
CIM allows these properties to be harnessed in the production of components with high performance and durability.
Cost-Effectiveness
While the initial setup costs for CIM can be high, the technology offers significant cost advantages in mass production.
Once the molds are created, large quantities of parts can be produced relatively cheaply and consistently, making it an economically viable option for many applications.
Environmental Impact
Ceramic materials are inherently more environmentally friendly compared to metals and plastics, as they are often derived from abundant natural resources.
Furthermore, CIM processes generate less waste and require fewer secondary operations, contributing to a more sustainable manufacturing approach.
Disadvantages of Ceramic Injection Molding
Despite its numerous benefits, CIM does have some disadvantages that must be considered.
High Initial Costs
The initial costs associated with CIM can be substantial.
These include the cost of designing and manufacturing molds, as well as the development of suitable feedstock materials.
However, these costs can be amortized over large production runs, making the technology more cost-effective in the long term.
Processing Complexity
The CIM process involves several stages, each of which requires precise control to achieve the desired properties in the final product.
Mistakes at any stage can result in defects or rejection of parts, making quality control and process optimization critical.
Material Limitations
Not all ceramic materials are suitable for injection molding.
The choice of materials is limited by the need for compatible binders and the ability to achieve the required properties after sintering.
This can restrict the range of applications for CIM.
Supplier Negotiation Techniques
When dealing with Japanese suppliers for Ceramic Injection Molding, several negotiation techniques can be particularly effective.
Understand Cultural Nuances
Japanese business culture places a high value on relationships and trust.
Spending time to build a strong rapport with your suppliers can pay dividends in negotiations.
This often involves frequent visits, social interactions, and demonstrating a long-term commitment to the partnership.
Focus on Quality
Japanese manufacturers are renowned for their commitment to quality.
Emphasizing your company’s dedication to maintaining high standards can help align your objectives with those of your supplier, facilitating smoother negotiations.
Leverage Technology and Innovation
Highlighting your interest in cutting-edge technologies and innovative practices can resonate well with Japanese suppliers, who often pride themselves on their technological prowess.
Expressing a genuine interest in collaborative development and continuous improvement can foster a more cooperative relationship.
Be Transparent and Consistent
Transparency and consistency in communication are crucial when negotiating with Japanese suppliers.
Providing clear and detailed information about your requirements, expectations, and constraints can help build trust and avoid misunderstandings.
Market Conditions
The market for Ceramic Injection Molding in Japan is influenced by several factors, including technological advancements, industry demand, and economic conditions.
Technological Advancements
Japan has a strong tradition of innovation in manufacturing technologies.
Ongoing research and development efforts continue to push the boundaries of what is possible with CIM, leading to improved processes and materials.
Staying abreast of these advancements can give you a competitive edge in the market.
Industry Demand
The demand for CIM components is driven by various industries, including aerospace, automotive, electronics, and medical devices.
Understanding the specific needs and trends within these industries can help you identify opportunities and tailor your procurement strategies accordingly.
Economic Conditions
Economic factors such as exchange rates, labor costs, and trade policies can impact the cost and availability of CIM components.
Monitoring these conditions can help you anticipate changes in the market and adjust your sourcing strategies as needed.
Best Practices for Leveraging CIM Technology
To maximize the benefits of Ceramic Injection Molding, consider the following best practices.
Invest in Early Collaboration
Engage with your suppliers early in the design process to ensure that your product designs are optimized for CIM.
This can help identify potential challenges and opportunities for improvement, leading to better outcomes and reduced costs.
Implement Rigorous Quality Control
Given the complexity of the CIM process, robust quality control measures are essential.
Work with your suppliers to establish clear quality standards and inspection procedures to ensure that your products meet the required specifications.
Foster Continuous Improvement
Encourage a culture of continuous improvement within your procurement and manufacturing teams.
Regularly review and refine your processes to identify areas for enhancement, leveraging feedback from your suppliers and customers.
Stay Informed About Technological Trends
Keep up to date with the latest developments in CIM technology and materials.
Participate in industry conferences, workshops, and trade shows to gain insights and network with leading experts and suppliers.
Conclusion
Ceramic Injection Molding technology is shaping the future of Japanese manufacturing, offering transformative benefits for a wide range of industries.
By understanding the fundamentals of CIM, recognizing its advantages and disadvantages, and employing effective supplier negotiation techniques, you can unlock the full potential of this innovative technology.
With careful planning and a commitment to continuous improvement, you can leverage CIM to drive efficiency, quality, and innovation in your manufacturing operations.
資料ダウンロード
QCD調達購買管理クラウド「newji」は、調達購買部門で必要なQCD管理全てを備えた、現場特化型兼クラウド型の今世紀最高の購買管理システムとなります。
ユーザー登録
調達購買業務の効率化だけでなく、システムを導入することで、コスト削減や製品・資材のステータス可視化のほか、属人化していた購買情報の共有化による内部不正防止や統制にも役立ちます。
NEWJI DX
製造業に特化したデジタルトランスフォーメーション(DX)の実現を目指す請負開発型のコンサルティングサービスです。AI、iPaaS、および先端の技術を駆使して、製造プロセスの効率化、業務効率化、チームワーク強化、コスト削減、品質向上を実現します。このサービスは、製造業の課題を深く理解し、それに対する最適なデジタルソリューションを提供することで、企業が持続的な成長とイノベーションを達成できるようサポートします。
オンライン講座
製造業、主に購買・調達部門にお勤めの方々に向けた情報を配信しております。
新任の方やベテランの方、管理職を対象とした幅広いコンテンツをご用意しております。
お問い合わせ
コストダウンが利益に直結する術だと理解していても、なかなか前に進めることができない状況。そんな時は、newjiのコストダウン自動化機能で大きく利益貢献しよう!
(Β版非公開)