- お役立ち記事
- Arc Welding Technologies and Their Applications in Manufacturing
Arc Welding Technologies and Their Applications in Manufacturing
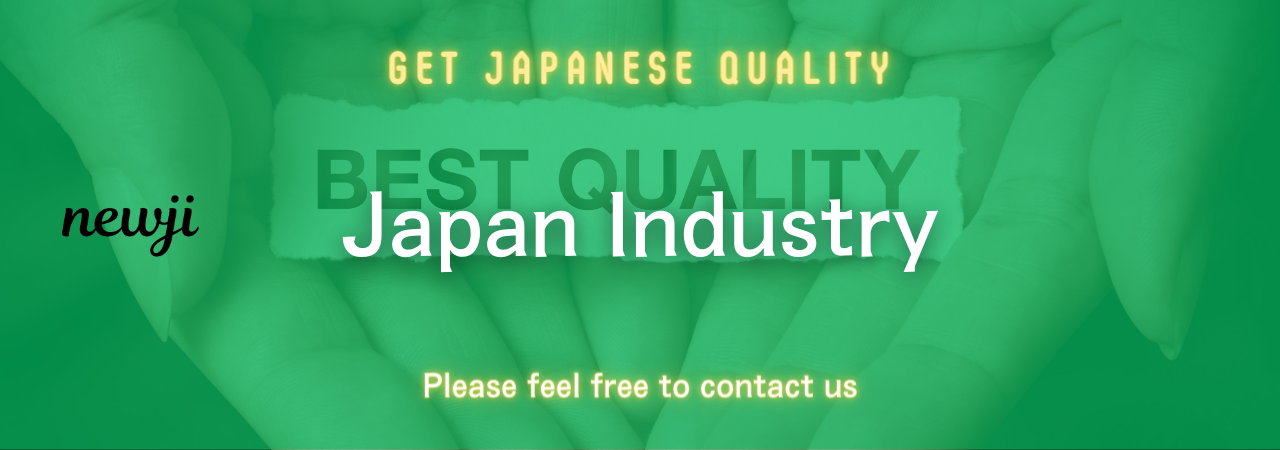
Arc welding is a powerful and versatile technology used in the manufacturing industry. It joins metals by using an electric arc to generate heat. This process has revolutionized how we fabricate metal structures and products. Let’s explore the various arc welding technologies and their applications in manufacturing.
目次
What is Arc Welding?
Arc welding is a type of welding that uses an electric arc to create heat. This heat melts metals so that they can be joined together. The electric arc is formed between an electrode and the base material. This process requires a power supply to generate the electric arc. The power can be either alternating current (AC) or direct current (DC).
Arc welding is popular because it can create strong, precise welds. It’s also adaptable, working with a wide range of metals and thicknesses.
Types of Arc Welding Technologies
1. Shielded Metal Arc Welding (SMAW)
Shielded Metal Arc Welding, also known as stick welding, is one of the most common and oldest methods.
In this process, a consumable electrode coated in flux is used. The flux coating disintegrates during welding, producing gases and a layer of slag. These protect the weld area from contaminants.
SMAW is versatile and can be used for welding many types of metals, including steel and iron. It is widely used in construction, pipeline work, and shipbuilding.
2. Gas Metal Arc Welding (GMAW)
Gas Metal Arc Welding, or MIG (Metal Inert Gas) welding, uses a continuous wire feed as the electrode. An inert gas, typically argon, is also used to shield the weld zone from contaminants.
MIG welding is known for its speed and efficiency. It creates a clean and strong weld with minimal spattering.
This process is commonly used in automotive, aerospace, and construction industries. It’s particularly popular for welding non-ferrous metals like aluminum.
3. Flux-Cored Arc Welding (FCAW)
Flux-Cored Arc Welding is similar to MIG welding but uses a special tubular wire filled with flux. This flux generates a shielding gas. Depending on the specific method, an additional shielding gas may sometimes be used.
FCAW is effective for welding thick materials and can be used outdoors in windy conditions because it produces its own shielding gas. It is commonly used in heavy equipment manufacturing, shipbuilding, and construction.
4. Gas Tungsten Arc Welding (GTAW)
Gas Tungsten Arc Welding, or TIG (Tungsten Inert Gas) welding, uses a non-consumable tungsten electrode. An inert gas like argon or helium shields the weld area.
TIG welding is known for producing high-quality, precise welds. It is slower compared to other methods but offers superior control.
This method is often used in high-quality applications such as aerospace, nuclear, and piping industries. It is also preferable for welding thin materials like stainless steel and non-ferrous metals.
5. Submerged Arc Welding (SAW)
Submerged Arc Welding involves forming an arc between a consumable electrode and the base metal beneath a blanket of granular flux.
The flux shields the weld zone from contamination and usually leaves a slag that must be removed after welding.
SAW is highly efficient and ideal for welding thick steel plates. It’s commonly used in shipbuilding, pressure vessel fabrication, and structural steel manufacturing.
Applications of Arc Welding in Manufacturing
1. Automotive Industry
Arc welding plays a crucial role in the automotive industry. It is used to weld car frames, bodies, and components. MIG welding, in particular, is widely used for its speed and efficiency. Automotive manufacturers rely on automated robotic welding systems for mass production. This ensures consistent quality and precision.
2. Construction Industry
The construction industry benefits significantly from arc welding technologies. Structural steel frameworks of buildings, bridges, and infrastructure projects are often welded using SMAW and FCAW. The strength and durability of arc-welded joints are essential for ensuring the safety and longevity of structures.
3. Aerospace Industry
Precision and quality are paramount in the aerospace industry. GTAW, or TIG welding, is preferred for its ability to create high-quality welds. Aircraft frames, engine components, and other critical parts are often welded using TIG welding. The exact control offered by this method is essential for avoiding defects and ensuring safety.
4. Shipbuilding Industry
In shipbuilding, arc welding technologies like SMAW, FCAW, and SAW are commonly used. Welding is essential for joining the thick steel plates used in ship construction. These welds need to be strong and durable to withstand the harsh marine environment. Automated welding systems are also used in shipyards to improve productivity and consistency.
5. Pipeline Industry
The pipeline industry relies heavily on SMAW and GMAW for welding pipelines. These technologies are suitable for different types of materials, including steel and stainless steel. Welded pipelines are used for transporting oil, gas, and water. Ensuring the integrity of these welds is vital for preventing leaks and environmental hazards.
Advantages of Arc Welding
Arc welding offers several advantages that make it a preferred choice in various industries.
1. Versatility
Arc welding can be used to weld a wide range of metals, including ferrous and non-ferrous materials. It is suitable for different thicknesses and can be applied in various positions.
2. Strength
Welds made through arc welding are strong and durable. They provide structural integrity to the fabricated parts, ensuring they can withstand various stresses and loads.
3. Precision
Technologies like TIG welding offer precise control, making them ideal for applications requiring high-quality welds. This precision is crucial for industries like aerospace and nuclear.
4. Efficiency
Certain arc welding methods, such as MIG welding, can be automated, improving production speed and consistency. Automated systems are essential for mass production in industries like automotive and shipbuilding.
Challenges and Considerations
Despite its advantages, arc welding also comes with challenges that need to be addressed.
1. Skill Requirement
Welding requires skilled operators to ensure the quality and safety of welds. Proper training and certification are essential for welding professionals.
2. Safety Concerns
Arc welding involves high temperatures, electric currents, and potentially harmful gases. Proper safety measures, including protective gear and ventilation, are crucial for preventing accidents and health hazards.
3. Material Limitations
Certain materials, like reactive metals, may be challenging to weld using conventional arc welding methods. Advanced techniques and specialized equipment may be required for these materials.
In conclusion, arc welding technologies are integral to the manufacturing industry. They have diverse applications across various sectors, providing strong, precise, and durable welds. Understanding the different methods and their uses can help industry professionals choose the best welding technique for their specific needs.
資料ダウンロード
QCD調達購買管理クラウド「newji」は、調達購買部門で必要なQCD管理全てを備えた、現場特化型兼クラウド型の今世紀最高の購買管理システムとなります。
ユーザー登録
調達購買業務の効率化だけでなく、システムを導入することで、コスト削減や製品・資材のステータス可視化のほか、属人化していた購買情報の共有化による内部不正防止や統制にも役立ちます。
NEWJI DX
製造業に特化したデジタルトランスフォーメーション(DX)の実現を目指す請負開発型のコンサルティングサービスです。AI、iPaaS、および先端の技術を駆使して、製造プロセスの効率化、業務効率化、チームワーク強化、コスト削減、品質向上を実現します。このサービスは、製造業の課題を深く理解し、それに対する最適なデジタルソリューションを提供することで、企業が持続的な成長とイノベーションを達成できるようサポートします。
オンライン講座
製造業、主に購買・調達部門にお勤めの方々に向けた情報を配信しております。
新任の方やベテランの方、管理職を対象とした幅広いコンテンツをご用意しております。
お問い合わせ
コストダウンが利益に直結する術だと理解していても、なかなか前に進めることができない状況。そんな時は、newjiのコストダウン自動化機能で大きく利益貢献しよう!
(Β版非公開)