- お役立ち記事
- Selection and Use of Sine Wave Inverters in Manufacturing
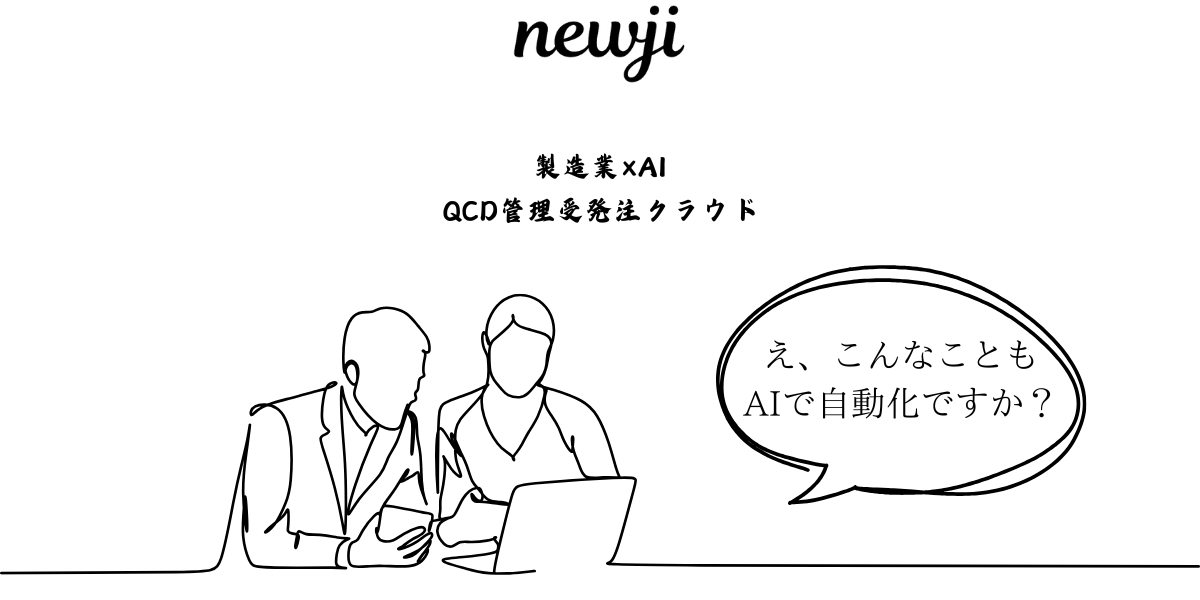
Selection and Use of Sine Wave Inverters in Manufacturing
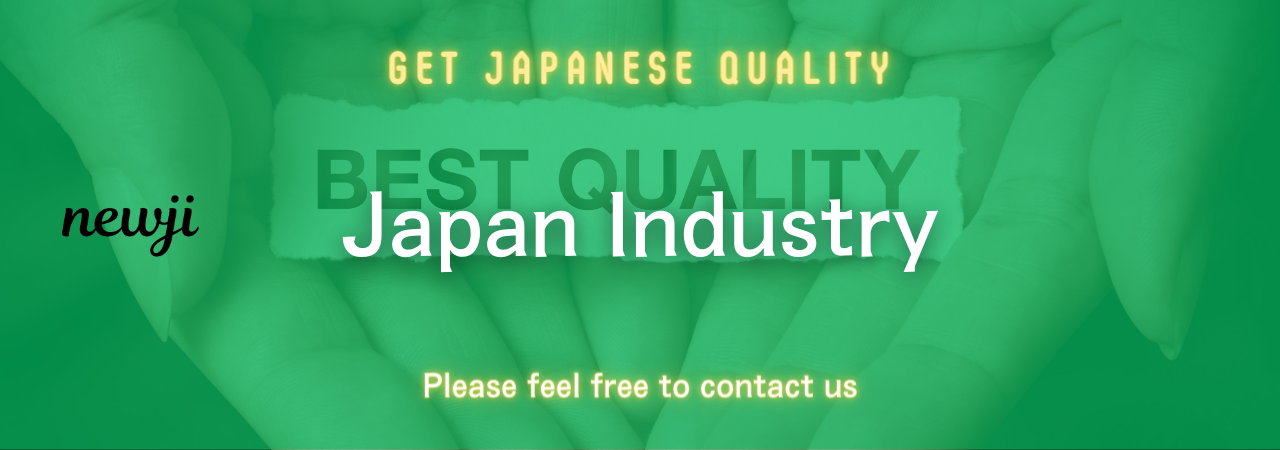
Manufacturing processes require various types of electronic equipment to operate efficiently.
One crucial component that ensures smooth functioning is a reliable power supply.
A sine wave inverter, in particular, is essential for converting DC (Direct Current) power to AC (Alternating Current) power.
In this article, we will explore the importance of sine wave inverters in manufacturing and guide you on how to select and use them effectively.
目次
What is a Sine Wave Inverter?
A sine wave inverter converts DC power, typically from batteries or solar panels, into AC power.
The output resembles a smooth and uniform wave, similar to the power supplied by utility companies.
This waveform is essential for running sensitive electronic devices, such as computers, medical equipment, and precision tools found in manufacturing.
Pure Sine Wave vs. Modified Sine Wave
There are two main types of sine wave inverters: pure sine wave and modified sine wave.
Pure sine wave inverters produce a cleaner and smoother waveform, making them ideal for sensitive electronics.
Modified sine wave inverters, on the other hand, generate a rough approximation of a true sine wave.
While they are more affordable, modified sine wave inverters can cause issues with certain equipment.
This is why pure sine wave inverters are preferred in manufacturing settings where precision and reliability are paramount.
Why Use Sine Wave Inverters in Manufacturing?
Protecting Sensitive Equipment
Manufacturing facilities often rely on specialized machinery and devices that need a stable and clean power supply.
Using a pure sine wave inverter ensures that these devices receive the appropriate power, reducing the risk of damage and extending their lifespan.
Power surges, sags, and electrical noise can be particularly harmful to sensitive equipment, which is why an inverter that produces a smooth sine wave is crucial.
Maintaining Consistent Performance
In a manufacturing environment, consistent performance is key.
Fluctuations in power can lead to interruptions, reducing productivity and possibly causing defects in products.
Sine wave inverters eliminate these fluctuations, providing a steady stream of power that keeps machinery operating at optimal levels.
How to Choose the Right Sine Wave Inverter
Determine Your Power Needs
The first step in selecting a sine wave inverter is to determine the power requirements of your manufacturing equipment.
Calculate the total wattage of all devices that will be connected to the inverter.
Add at least 20% to this total to account for any power surges or unexpected increases in demand.
This buffer ensures that your inverter can handle the load without being overstressed.
Consider Battery Capacity
If you are using batteries as your DC power source, consider their capacity and how long you need to run your equipment during power outages.
Ensure that your battery system can support your power needs for the desired duration.
This will help you select an inverter that matches the voltage and capacity of your batteries.
Evaluate Inverter Features
Look for additional features that can benefit your manufacturing operations.
Some sine wave inverters come with built-in protections against overloading, over-voltage, and overheating.
Others may include remote monitoring and control capabilities, which can be useful for managing the inverter from a central location.
Assess your specific needs and choose an inverter with features that enhance reliability and convenience.
Check Manufacturer’s Reputation
When investing in a sine wave inverter, it’s essential to choose a reputable manufacturer known for producing high-quality products.
Research reviews, ratings, and testimonials from other users.
A well-established brand is more likely to offer reliable customer support, and their products tend to be more durable and efficient.
Installing and Using Sine Wave Inverters
Proper Installation
Proper installation is key to ensuring the effective and safe operation of sine wave inverters.
If you’re not confident in your ability to install the inverter, hire a qualified electrician or technician.
Follow the manufacturer’s instructions carefully, paying attention to specifications like wiring, grounding, and ventilation.
Improper installation can lead to malfunctions, void warranties, and even pose safety hazards.
Regular Maintenance
Like any other equipment in your manufacturing facility, sine wave inverters require regular maintenance to perform optimally.
Check connections for corrosion, ensure that cooling fans are functioning, and keep the unit free from dust and debris.
Regularly test the output voltage to ensure it matches the specifications.
If you notice any irregularities, consult the manufacturer’s guidelines or contact customer support.
Monitoring Usage
Keep track of how much power your equipment consumes and monitor the inverter’s performance.
Some inverters come with monitoring systems that provide real-time data.
This information can help you optimize energy use, identify potential issues before they become major problems, and make informed decisions about when to scale up your power capacity.
Training Staff
Ensure that your staff is adequately trained on the operation and maintenance of sine wave inverters.
They should know how to respond to alarms, reset the system, and perform basic troubleshooting.
Proper training minimizes downtime and ensures that the inverter’s benefits are fully realized.
Conclusion
Sine wave inverters are vital components in manufacturing environments, providing the stable and clean power necessary for sensitive equipment.
By understanding your power needs, evaluating inverter features, and ensuring proper installation and maintenance, you can enhance the efficiency and reliability of your manufacturing operations.
Investing in a high-quality sine wave inverter not only protects your equipment but also contributes to consistent performance and productivity.
If chosen and used correctly, a sine wave inverter can be a critical asset in maintaining the smooth operation of your manufacturing processes.
資料ダウンロード
QCD調達購買管理クラウド「newji」は、調達購買部門で必要なQCD管理全てを備えた、現場特化型兼クラウド型の今世紀最高の購買管理システムとなります。
ユーザー登録
調達購買業務の効率化だけでなく、システムを導入することで、コスト削減や製品・資材のステータス可視化のほか、属人化していた購買情報の共有化による内部不正防止や統制にも役立ちます。
NEWJI DX
製造業に特化したデジタルトランスフォーメーション(DX)の実現を目指す請負開発型のコンサルティングサービスです。AI、iPaaS、および先端の技術を駆使して、製造プロセスの効率化、業務効率化、チームワーク強化、コスト削減、品質向上を実現します。このサービスは、製造業の課題を深く理解し、それに対する最適なデジタルソリューションを提供することで、企業が持続的な成長とイノベーションを達成できるようサポートします。
オンライン講座
製造業、主に購買・調達部門にお勤めの方々に向けた情報を配信しております。
新任の方やベテランの方、管理職を対象とした幅広いコンテンツをご用意しております。
お問い合わせ
コストダウンが利益に直結する術だと理解していても、なかなか前に進めることができない状況。そんな時は、newjiのコストダウン自動化機能で大きく利益貢献しよう!
(Β版非公開)