- お役立ち記事
- Spot Welding Technology and Its Application in Manufacturing
Spot Welding Technology and Its Application in Manufacturing
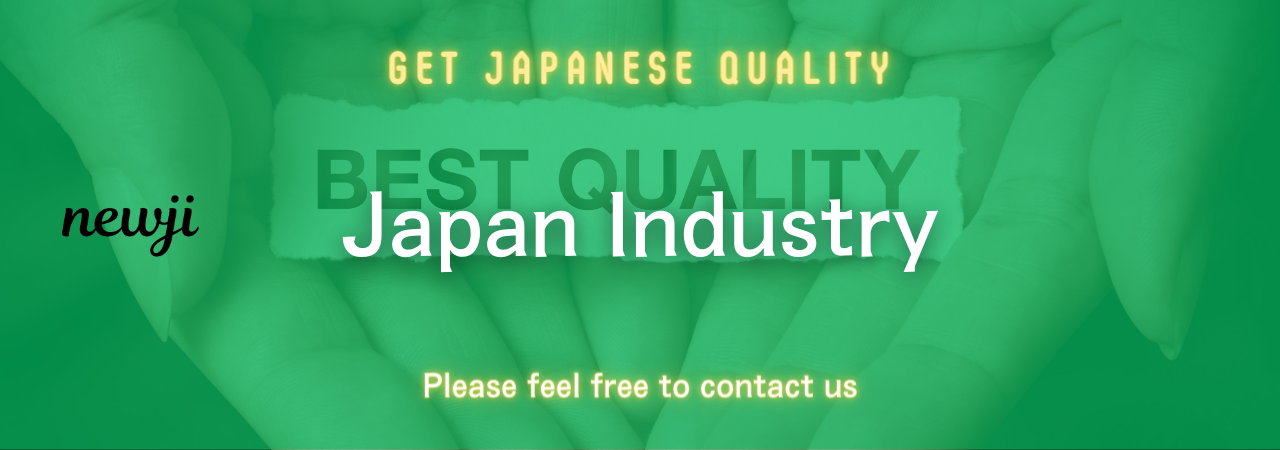
Spot welding technology plays a pivotal role in modern manufacturing processes. This versatile technique is commonly used in various industries, particularly the automotive and electronics sectors, to join thin sheets of metal. Its success can be attributed to its efficiency, cost-effectiveness, and the strong welds it produces.
目次
What is Spot Welding?
Spot welding is a type of resistance welding that produces coalescence of metals by the heat obtained from resistance to electric current flow. This heat is applied to the workpieces, which are held together under pressure by electrode tips. The entire process usually takes just a few seconds, resulting in a strong and reliable weld.
The Basic Principle
The key principle behind spot welding lies in the generation of heat through electrical resistance. When a high electrical current is passed through the metal sheets, the resistance at the point of contact generates heat. This heat causes the metals to melt and fuse together. Once the current stops, the melted metal solidifies, forming a strong bond.
Advantages of Spot Welding
Spot welding offers numerous benefits that make it a preferred method in many manufacturing applications.
Efficiency
One of the biggest advantages of spot welding is its speed. The actual welding process only takes a few seconds, allowing for rapid production. This efficiency is particularly beneficial in mass production settings.
Cost-Effectiveness
Spot welding is also economically advantageous. The equipment and materials used are relatively inexpensive, and the short welding time reduces labor costs. This makes it a cost-effective option for manufacturers looking to maximize their profit margins.
Strong and Reliable Welds
The welds produced by spot welding are strong and durable. This is crucial in applications where the integrity of the welded joints is critical, such as in the automotive industry. The reliability of spot welds ensures the safety and longevity of the final product.
Applications of Spot Welding
Spot welding is widely utilized across various industries due to its versatility and efficiency.
Automotive Industry
In the automotive sector, spot welding is extensively used for joining thin metal sheets. It is a key technique in the manufacture of car bodies, frames, and other components. The speed and reliability of spot welding are essential in this high-volume industry.
Electronics Manufacturing
Spot welding is also prevalent in the electronics industry, where it is used to connect electrical components and create reliable joints. This is particularly important in the production of batteries, connectors, and other electronic assemblies.
Household Appliances
Many household appliances, such as washing machines and refrigerators, rely on spot welding for their construction. The technique ensures strong and durable joints that can withstand the rigors of everyday use.
Factors Affecting Spot Welding Quality
Several factors influence the quality of spot welds, and understanding these can help optimize the welding process.
Material Properties
The type and thickness of the materials being welded significantly impact the welding quality. Different metals have distinct conductivity and thermal properties, which affect how they respond to the welding process. Ensuring compatibility of materials is crucial for achieving strong welds.
Electrode Force
The pressure applied by the electrode tips plays a vital role in the welding process. Insufficient or excessive pressure can lead to weak welds or deformation of the workpieces. Proper calibration of electrode force is essential for achieving optimal results.
Welding Current and Time
The magnitude of the welding current and the duration for which it is applied are critical parameters. These settings must be carefully controlled to ensure adequate heat generation and proper fusion of the materials. Adjusting the welding current and time based on the material properties and thickness is key to achieving high-quality welds.
Innovations in Spot Welding Technology
Advancements in technology continue to enhance the capabilities and applications of spot welding.
Automated Spot Welding Systems
Automation has revolutionized spot welding, making it more efficient and precise. Automated spot welding systems use robotics and computer control to perform welds with high accuracy and consistency. This has significantly improved productivity and reduced the likelihood of errors.
Advanced Monitoring and Control
Modern spot welding equipment is equipped with advanced monitoring and control systems. These systems can detect variations in the welding process and make real-time adjustments to ensure optimal quality. This level of precision is particularly beneficial in industries where high-quality standards are required.
Conclusion
Spot welding technology is an indispensable tool in modern manufacturing. Its efficiency, cost-effectiveness, and ability to produce strong and reliable welds make it a preferred choice across various industries. As technology continues to advance, we can expect further innovations that will enhance the capabilities of spot welding, ensuring its relevance and importance in the manufacturing landscape for years to come.
資料ダウンロード
QCD調達購買管理クラウド「newji」は、調達購買部門で必要なQCD管理全てを備えた、現場特化型兼クラウド型の今世紀最高の購買管理システムとなります。
ユーザー登録
調達購買業務の効率化だけでなく、システムを導入することで、コスト削減や製品・資材のステータス可視化のほか、属人化していた購買情報の共有化による内部不正防止や統制にも役立ちます。
NEWJI DX
製造業に特化したデジタルトランスフォーメーション(DX)の実現を目指す請負開発型のコンサルティングサービスです。AI、iPaaS、および先端の技術を駆使して、製造プロセスの効率化、業務効率化、チームワーク強化、コスト削減、品質向上を実現します。このサービスは、製造業の課題を深く理解し、それに対する最適なデジタルソリューションを提供することで、企業が持続的な成長とイノベーションを達成できるようサポートします。
オンライン講座
製造業、主に購買・調達部門にお勤めの方々に向けた情報を配信しております。
新任の方やベテランの方、管理職を対象とした幅広いコンテンツをご用意しております。
お問い合わせ
コストダウンが利益に直結する術だと理解していても、なかなか前に進めることができない状況。そんな時は、newjiのコストダウン自動化機能で大きく利益貢献しよう!
(Β版非公開)