- お役立ち記事
- How to promote kaizen activities and best practices in quality control in the manufacturing industry
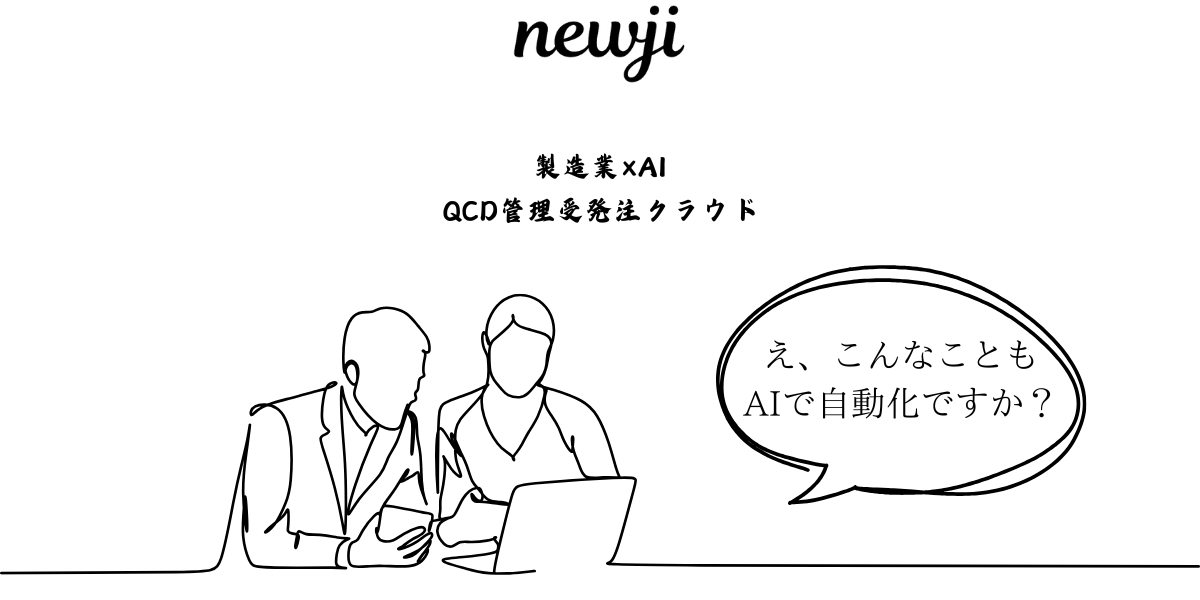
How to promote kaizen activities and best practices in quality control in the manufacturing industry
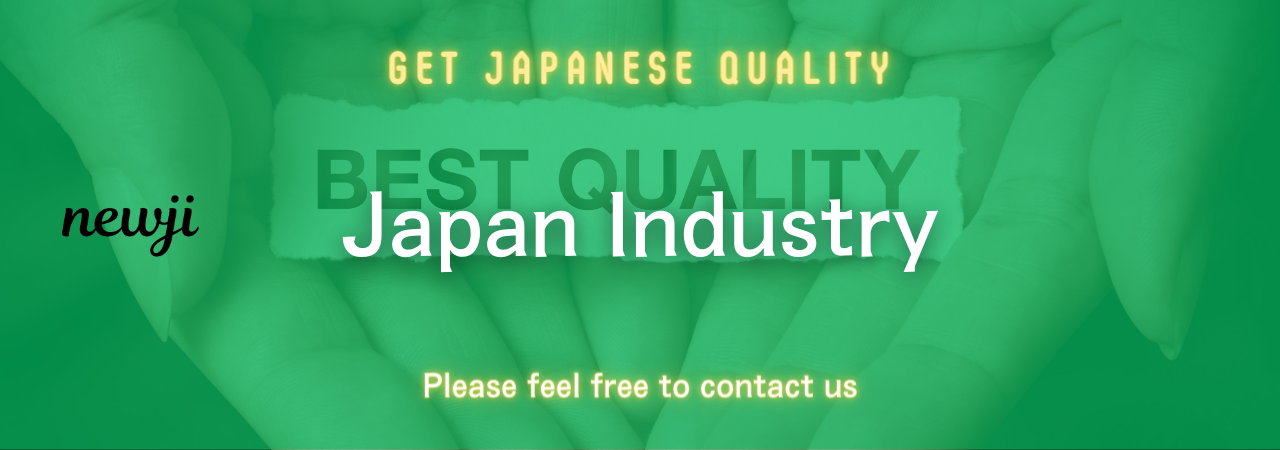
Kaizen is a foundational concept in the manufacturing industry, originating from Japan and meaning “continuous improvement.” This philosophy emphasizes ongoing, incremental improvements in processes, fostering a culture of efficiency and quality.
Adopting kaizen activities and best practices in quality control can lead to significant benefits such as increased productivity, reduced waste, and improved employee morale.
目次
Understanding Kaizen and Its Importance
Kaizen is more than just a strategy; it’s a mindset that encourages everyone in the organization to strive for betterment. In the manufacturing sector, this could include refining production processes, enhancing product quality, and ensuring worker safety.
The core principle behind kaizen is that small, consistent changes can lead to substantial improvements over time. By focusing on incremental gains, companies can adapt swiftly to new challenges and maintain high standards of quality.
The Philosophy of Kaizen
At its heart, kaizen involves everyone in the organization, from top executives to line workers. It’s about recognizing that each employee has a valuable perspective on how to improve the workplace. Encouraging input at all levels ensures that improvements are practical and implementable.
Another essential aspect is waste reduction. By identifying and eliminating unnecessary steps or materials, companies can streamline operations and save resources. This focus on efficiency is crucial in maintaining competitiveness in the manufacturing industry.
Implementing Kaizen in Your Manufacturing Processes
Introducing kaizen activities involves several steps designed to engage employees and build a culture focused on continuous improvement. Here’s how to promote kaizen effectively:
1. Educate and Train Your Team
Start by educating your workforce about the principles and benefits of kaizen. Training sessions can help employees understand how their contributions can lead to substantial improvements. This awareness motivates staff and encourages participation.
Provide ongoing training so that your team stays updated on the latest kaizen techniques and tools. This continuous learning approach ensures that the organization remains agile and capable of adopting new strategies quickly.
2. Encourage Employee Participation
Create an environment where employees feel comfortable sharing their ideas for improvement. Establish suggestion systems or regular meetings where staff can voice their thoughts without fear of criticism. Recognize and reward valuable contributions to foster a sense of ownership.
Employee involvement is crucial for identifying inefficiencies and generating innovative solutions. By leveraging the collective intelligence of your team, you can uncover areas for improvement that might be overlooked from a top-down perspective.
3. Implement Small-Scale Changes
Focus on making small, manageable changes rather than attempting large-scale overhauls. These incremental improvements are easier to implement and less disruptive to operations. Small successes build momentum and demonstrate the effectiveness of kaizen.
When a change proves successful, document the process and share the knowledge with the entire organization. This practice not only celebrates achievements but also creates a repository of best practices that can be referenced in the future.
4. Monitor and Measure Progress
Track the impact of kaizen activities through regular monitoring and evaluation. Use key performance indicators (KPIs) to assess improvements in quality, productivity, and waste reduction. Regularly reviewing these metrics helps ensure that the implemented changes are achieving the desired outcomes.
Encourage transparency by sharing these metrics with your team. This practice keeps everyone informed about the progress and reinforces the importance of continuous improvement.
Best Practices in Quality Control
Quality control is a critical aspect of the manufacturing process, ensuring that products meet specified standards and customer expectations. Integrating kaizen activities with quality control practices can enhance the overall effectiveness of your operations.
1. Standardize Processes
Standardization is crucial for maintaining consistency in production. Documenting procedures and creating standard operating instructions ensure that everyone follows the same steps, reducing variability and errors.
Regularly review and update these standards based on feedback and observed inefficiencies. This dynamic approach allows your processes to evolve and adapt over time, maintaining high levels of quality.
2. Conduct Regular Inspections
Implement routine inspections throughout the production process. By catching defects early, you can address issues before they escalate, reducing waste and rework. These inspections can be automated or manual, depending on the complexity of the task.
Train employees to perform self-inspections and peer reviews. This practice not only improves quality but also empowers workers to take ownership of their work and contribute to the overall goals of the organization.
3. Use Root Cause Analysis
When defects or issues are identified, use root cause analysis to determine the underlying problem. Tools like the “Five Whys” or fishbone diagrams can help systematically trace the issue to its source.
Addressing the root cause prevents recurrence and leads to more sustainable improvements. This method aligns with kaizen principles by emphasizing problem-solving and continuous refinement.
4. Implement Total Quality Management (TQM)
TQM is a comprehensive approach that integrates quality management principles into every aspect of the organization. By fostering a culture where quality is everyone’s responsibility, TQM aligns well with the kaizen philosophy.
Encourage cross-functional teams to work together on quality initiatives. This collaboration promotes knowledge sharing and creates a more cohesive approach to problem-solving and improvement.
Case Studies of Successful Kaizen Implementation
Understanding how other companies have successfully implemented kaizen can provide valuable insights and inspiration for your own initiatives.
Toyota’s Kaizen Journey
Toyota is often cited as a benchmark for kaizen practices. The company’s commitment to continuous improvement is evident in its Toyota Production System, which emphasizes efficiency, quality, and employee involvement. By adopting kaizen, Toyota has achieved significant reductions in waste and improved production quality.
3M’s Culture of Innovation
3M has integrated kaizen into its innovation strategy, encouraging employees to contribute ideas for new products and process improvements. This approach has led to a steady stream of innovations and a culture that values and rewards creativity.
Conclusion
Promoting kaizen activities and integrating best practices in quality control can transform your manufacturing operations. By fostering a culture of continuous improvement, you can achieve higher productivity, better quality, and reduced waste. Engaging employees at all levels, implementing small-scale changes, and continuously measuring progress are key to successful kaizen adoption.
Learn from industry leaders like Toyota and 3M to understand how effective kaizen implementation can drive significant improvements. By embracing these principles and practices, your organization can remain competitive and responsive in an ever-evolving market.
資料ダウンロード
QCD調達購買管理クラウド「newji」は、調達購買部門で必要なQCD管理全てを備えた、現場特化型兼クラウド型の今世紀最高の購買管理システムとなります。
ユーザー登録
調達購買業務の効率化だけでなく、システムを導入することで、コスト削減や製品・資材のステータス可視化のほか、属人化していた購買情報の共有化による内部不正防止や統制にも役立ちます。
NEWJI DX
製造業に特化したデジタルトランスフォーメーション(DX)の実現を目指す請負開発型のコンサルティングサービスです。AI、iPaaS、および先端の技術を駆使して、製造プロセスの効率化、業務効率化、チームワーク強化、コスト削減、品質向上を実現します。このサービスは、製造業の課題を深く理解し、それに対する最適なデジタルソリューションを提供することで、企業が持続的な成長とイノベーションを達成できるようサポートします。
オンライン講座
製造業、主に購買・調達部門にお勤めの方々に向けた情報を配信しております。
新任の方やベテランの方、管理職を対象とした幅広いコンテンツをご用意しております。
お問い合わせ
コストダウンが利益に直結する術だと理解していても、なかなか前に進めることができない状況。そんな時は、newjiのコストダウン自動化機能で大きく利益貢献しよう!
(Β版非公開)