- お役立ち記事
- DXing of the molding process to ensure quality and improve productivity
DXing of the molding process to ensure quality and improve productivity
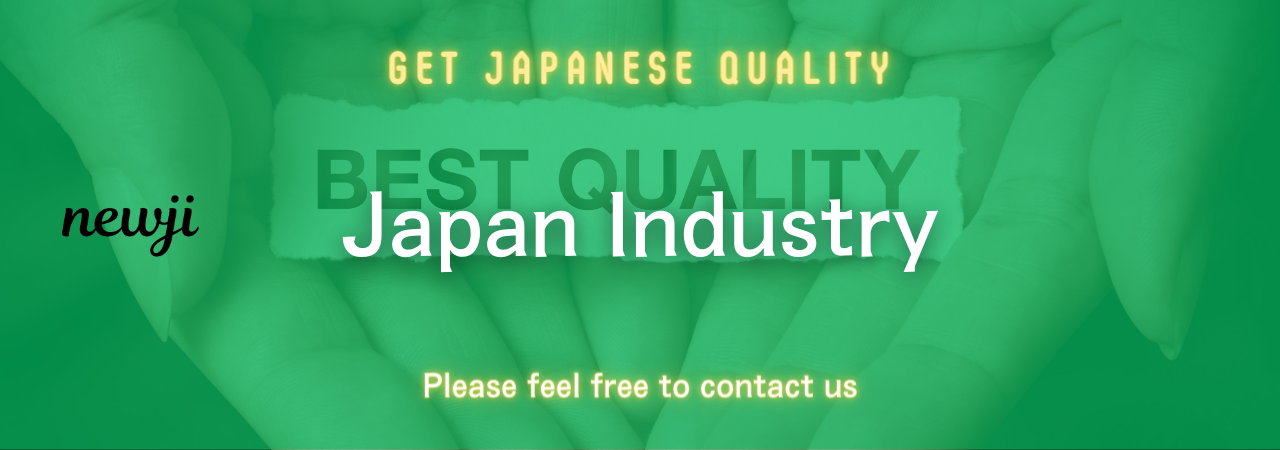
Digital transformation (DX) has revolutionized many aspects of manufacturing, and the molding process is no exception.
Implementing digital tools and innovative technologies can significantly enhance the quality and productivity of molding operations.
This article delves into various methods of DXing the molding process to ensure consistent quality and boost efficiency.
目次
Understanding the Molding Process
Before diving into digital transformation, it is essential to understand the basic steps in the molding process.
The molding process involves shaping raw materials into desired forms using molds.
Common methods include injection molding, blow molding, and compression molding.
The quality of the final product depends on several factors, such as material properties, mold design, and processing conditions.
Challenges in Traditional Molding
Traditional molding processes come with their share of challenges.
Maintaining consistent quality can be difficult due to variability in material properties and processing conditions.
Manual adjustments and inspections are often time-consuming and prone to human error.
Additionally, traditional methods might not be efficient enough to meet increasing production demands.
The Role of Digital Transformation in Molding
Digital transformation integrates advanced technologies, such as the Internet of Things (IoT), artificial intelligence (AI), and big data analytics, into manufacturing processes.
In the context of molding, DX can streamline operations and improve quality control.
Let’s explore some of the key technologies that can be leveraged for this purpose.
IoT and Smart Sensors
IoT involves connecting devices and systems through the internet to enable data exchange and automation.
In the molding process, IoT-enabled smart sensors can be used to monitor various parameters, such as temperature, pressure, and humidity.
These sensors provide real-time data, allowing for precise adjustments and ensuring optimal processing conditions.
This real-time monitoring helps in maintaining consistent quality and reducing the need for manual inspections.
Artificial Intelligence and Machine Learning
AI and machine learning can play a vital role in predicting and optimizing the molding process.
By analyzing historical data, AI algorithms can identify patterns and predict potential defects.
This predictive capability allows manufacturers to take preventive actions before defects occur.
Machine learning models can also optimize processing parameters to achieve the best quality and efficiency.
Big Data Analytics
Big data analytics involves analyzing large volumes of data to gain insights and make informed decisions.
In the molding process, data from sensors, machines, and production lines can be collected and analyzed.
By using big data analytics, manufacturers can identify trends, detect anomalies, and optimize production schedules.
This data-driven approach enhances decision-making and boosts overall productivity.
Implementing DX in the Molding Process
Implementing digital transformation in the molding process requires a systematic approach.
Here are some steps to consider:
Assessment and Planning
Begin by assessing the current state of your molding operations.
Identify areas that need improvement and determine how digital tools can address these challenges.
Develop a comprehensive plan that outlines the goals, required technologies, and implementation timeline.
Investing in Technology
Invest in the necessary technologies, such as IoT devices, AI software, and big data analytics platforms.
Ensure that these technologies are compatible with your existing systems and can be integrated seamlessly.
Training employees to use these tools effectively is also crucial.
Data Integration and Management
Data integration is a key aspect of digital transformation.
Consolidate data from various sources, such as sensors, machines, and ERP systems, into a centralized platform.
Implement robust data management practices to ensure data accuracy, security, and accessibility.
Continuous Monitoring and Improvement
Once the technologies are in place, establish a system for continuous monitoring and improvement.
Regularly analyze data to identify areas for optimization and implement corrective actions.
Continuous monitoring ensures that the molding process remains efficient and produces high-quality products.
Benefits of DXing the Molding Process
The benefits of digital transformation in the molding process are manifold.
Let’s explore some of the key advantages:
Enhanced Quality Control
Real-time monitoring and predictive analytics enable better quality control.
Manufacturers can detect and address issues before they impact the final product.
This results in higher-quality products and reduced defect rates.
Increased Productivity and Efficiency
DX streamlines operations and reduces the need for manual interventions.
Automated processes and optimized production schedules lead to increased productivity and efficiency.
Manufacturers can meet higher production demands without compromising on quality.
Cost Savings
While the initial investment in digital technologies might be significant, the long-term cost savings are substantial.
Improved quality control reduces waste and rework, while optimized operations lower production costs.
Data-Driven Decision Making
Access to real-time and historical data empowers manufacturers to make informed decisions.
Data-driven decision-making enhances strategic planning and operational efficiency.
Case Study: Successful Implementation of DX in Molding
Let’s look at a case study of a company that successfully implemented digital transformation in its molding process.
ABC Plastics, a leading manufacturer of plastic components, faced challenges in maintaining consistent quality and meeting production demands.
By integrating IoT sensors, AI algorithms, and big data analytics, ABC Plastics transformed its molding operations.
Real-time monitoring and predictive maintenance reduced downtime, while AI-driven process optimization improved product quality.
As a result, ABC Plastics saw a 20% increase in productivity and a 15% reduction in defect rates within the first year of implementation.
Conclusion
Digital transformation has the potential to revolutionize the molding process by enhancing quality control and boosting productivity.
By leveraging technologies such as IoT, AI, and big data analytics, manufacturers can achieve significant improvements in their operations.
A systematic approach to implementing DX can help overcome traditional challenges and unlock new opportunities for growth and efficiency.
Embracing digital transformation is not just a trend but a necessity for staying competitive in the modern manufacturing landscape.
資料ダウンロード
QCD調達購買管理クラウド「newji」は、調達購買部門で必要なQCD管理全てを備えた、現場特化型兼クラウド型の今世紀最高の購買管理システムとなります。
ユーザー登録
調達購買業務の効率化だけでなく、システムを導入することで、コスト削減や製品・資材のステータス可視化のほか、属人化していた購買情報の共有化による内部不正防止や統制にも役立ちます。
NEWJI DX
製造業に特化したデジタルトランスフォーメーション(DX)の実現を目指す請負開発型のコンサルティングサービスです。AI、iPaaS、および先端の技術を駆使して、製造プロセスの効率化、業務効率化、チームワーク強化、コスト削減、品質向上を実現します。このサービスは、製造業の課題を深く理解し、それに対する最適なデジタルソリューションを提供することで、企業が持続的な成長とイノベーションを達成できるようサポートします。
オンライン講座
製造業、主に購買・調達部門にお勤めの方々に向けた情報を配信しております。
新任の方やベテランの方、管理職を対象とした幅広いコンテンツをご用意しております。
お問い合わせ
コストダウンが利益に直結する術だと理解していても、なかなか前に進めることができない状況。そんな時は、newjiのコストダウン自動化機能で大きく利益貢献しよう!
(Β版非公開)