- お役立ち記事
- The Role and Challenges of Purchasing Departments in Manufacturing: Supply Chain Management and Cost Efficiency Perspectives
The Role and Challenges of Purchasing Departments in Manufacturing: Supply Chain Management and Cost Efficiency Perspectives
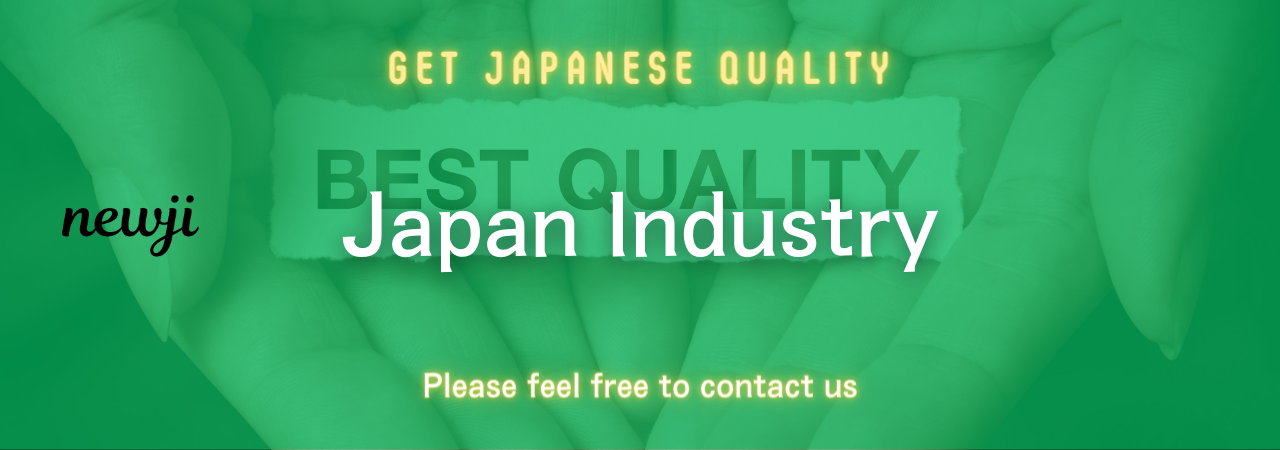
In the dynamic world of manufacturing, purchasing departments play a pivotal role in ensuring that operations run smoothly and efficiently.
They are responsible for acquiring the necessary materials and services needed for production.
Without the diligent work of these departments, the manufacturing process could come to a standstill, causing delays, increased costs, and a host of other issues.
Let’s delve deeper into the role of purchasing departments in manufacturing, their challenges, and how they contribute to supply chain management and cost efficiency.
目次
Understanding the Role of Purchasing Departments
Purchasing departments are at the heart of a manufacturing organization’s supply chain.
Their primary responsibility is to procure raw materials, components, machinery, and other essentials required for production.
They work to identify and partner with reliable suppliers, negotiate pricing and contracts, and ensure timely delivery of goods.
Supplier Selection and Relationship Management
Selecting the right suppliers is crucial.
Purchasing departments assess potential suppliers based on quality, cost, reliability, and delivery performance.
Forging strong relationships with suppliers helps in building trust and ensures that both parties can work seamlessly together.
This relationship management is vital for fostering long-term collaboration and achieving mutual benefits.
Contract Negotiation and Management
Negotiating favorable terms and conditions in contracts is another key task.
This includes pricing, delivery schedules, payment terms, and quality standards.
Effective contract management ensures that the company gets value for money and that suppliers meet their commitments.
It’s a delicate balance of ensuring competitive prices while maintaining high quality.
Inventory Management
Maintaining an optimal level of inventory is crucial for continuous production.
Purchasing departments analyze consumption patterns and forecast demand to avoid overstocking or stockouts.
Proper inventory management helps in minimizing storage costs and potential wastage.
Challenges Facing Purchasing Departments
Despite their importance, purchasing departments face several challenges that can impact their efficiency and effectiveness.
Supplier Reliability and Quality Issues
One of the most significant challenges is ensuring supplier reliability and product quality.
Any deviation from agreed standards can disrupt the production process.
Managing this requires constant monitoring and sometimes even visiting supplier facilities to ensure compliance with quality standards.
Market Volatility
Fluctuations in the market can affect the availability and cost of raw materials.
Purchasing departments must stay informed about market trends and adapt their strategies accordingly.
This may involve seeking alternative suppliers or renegotiating terms to manage costs effectively.
Cost Pressures
Manufacturing companies constantly strive to reduce costs without compromising on quality.
Purchasing departments play a crucial role in this by securing the best deals and optimizing the supply chain.
However, balancing cost efficiency with quality can be challenging.
Impact on Supply Chain Management
The purchasing department’s actions have far-reaching impacts on the entire supply chain.
Effective purchasing ensures a smooth flow of materials, which is essential for maintaining production schedules and meeting customer demands.
Supply Chain Coordination
Purchasing departments work closely with other departments, such as production and logistics, to coordinate the supply chain.
This coordination is vital for aligning procurement activities with production plans and ensuring timely delivery of finished products to customers.
Risk Management
Identifying and mitigating risks in the supply chain is another crucial role.
This includes assessing the reliability of suppliers, managing fluctuations in material availability, and developing contingency plans for unforeseen disruptions.
Effective risk management helps in maintaining the resilience of the supply chain.
Technology Integration
Integrating advanced technologies, such as Enterprise Resource Planning (ERP) systems, can enhance the efficiency of purchasing departments.
These systems provide real-time data on inventory levels, supplier performance, and market trends, enabling more informed decision-making.
This technological enhancement leads to better coordination and streamlined processes.
Contribution to Cost Efficiency
Purchasing departments have a direct impact on a company’s bottom line.
Their efforts in securing cost-effective supplies, managing inventory, and negotiating contracts contribute significantly to cost efficiency.
Strategic Sourcing
By adopting strategic sourcing practices, purchasing departments can identify the most cost-effective sources of materials.
This involves analyzing the total cost of ownership, including purchase price, transportation costs, and potential risks.
Strategic sourcing helps in achieving long-term cost savings.
Lean Inventory Practices
Implementing lean inventory practices, such as just-in-time (JIT) inventory, can reduce excess stock and associated holding costs.
This approach focuses on receiving goods only when needed for production, thus minimizing storage costs and reducing the risk of obsolescence.
Supplier Development
Investing in supplier development programs can enhance the quality and efficiency of the supply chain.
Purchasing departments can work with suppliers to improve their processes, reduce costs, and enhance product quality.
This collaborative approach leads to mutual benefits and improved cost efficiency.
In conclusion, purchasing departments play an integral role in the success of manufacturing organizations.
By effectively managing suppliers, negotiating contracts, and optimizing inventory, they ensure a smooth and efficient supply chain.
Despite the challenges they face, their contributions to supply chain management and cost efficiency are invaluable.
As technology continues to evolve, purchasing departments must adapt and leverage new tools to enhance their operations and drive continued success in the manufacturing industry.
資料ダウンロード
QCD調達購買管理クラウド「newji」は、調達購買部門で必要なQCD管理全てを備えた、現場特化型兼クラウド型の今世紀最高の購買管理システムとなります。
ユーザー登録
調達購買業務の効率化だけでなく、システムを導入することで、コスト削減や製品・資材のステータス可視化のほか、属人化していた購買情報の共有化による内部不正防止や統制にも役立ちます。
NEWJI DX
製造業に特化したデジタルトランスフォーメーション(DX)の実現を目指す請負開発型のコンサルティングサービスです。AI、iPaaS、および先端の技術を駆使して、製造プロセスの効率化、業務効率化、チームワーク強化、コスト削減、品質向上を実現します。このサービスは、製造業の課題を深く理解し、それに対する最適なデジタルソリューションを提供することで、企業が持続的な成長とイノベーションを達成できるようサポートします。
オンライン講座
製造業、主に購買・調達部門にお勤めの方々に向けた情報を配信しております。
新任の方やベテランの方、管理職を対象とした幅広いコンテンツをご用意しております。
お問い合わせ
コストダウンが利益に直結する術だと理解していても、なかなか前に進めることができない状況。そんな時は、newjiのコストダウン自動化機能で大きく利益貢献しよう!
(Β版非公開)