- お役立ち記事
- Practical Kaizen Activities
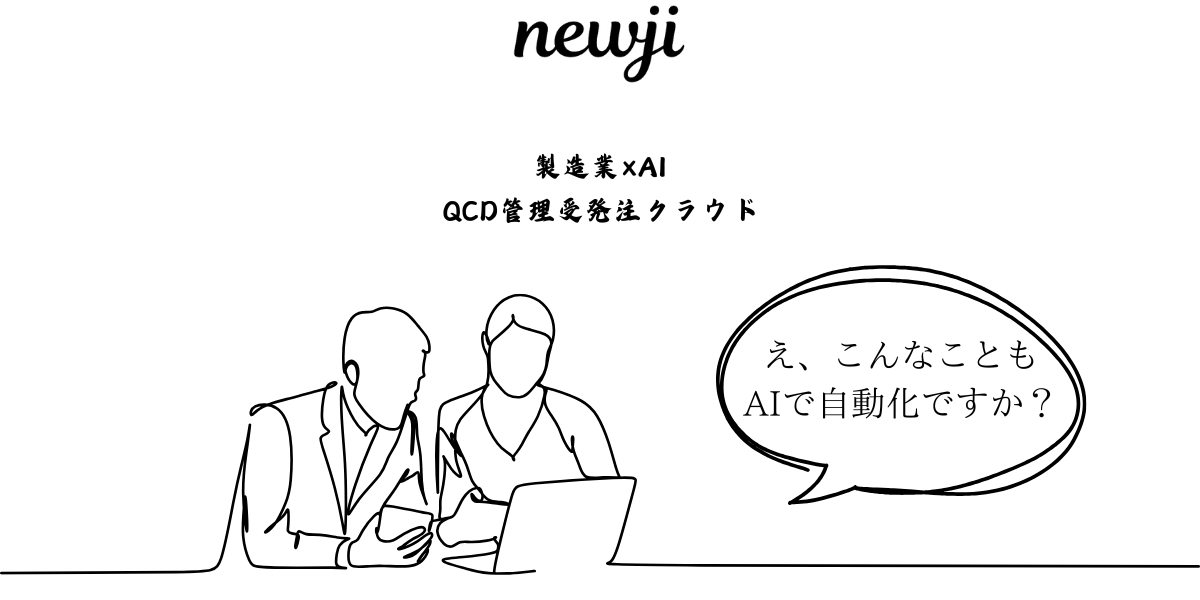
Practical Kaizen Activities
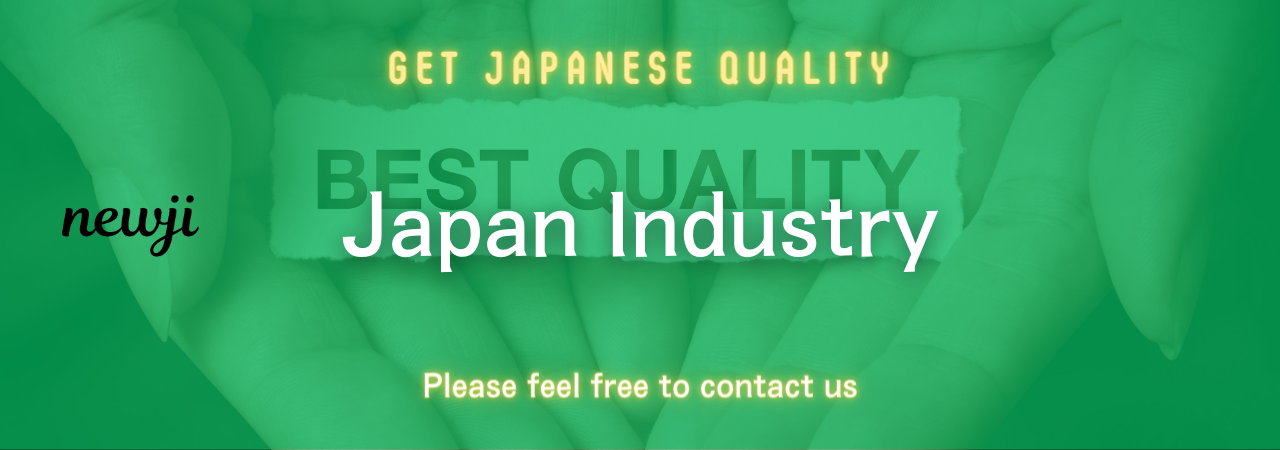
Kaizen is a Japanese term that translates to “continuous improvement.” It’s a practice that involves making small, incremental changes regularly to improve processes, increase efficiency, and create better outcomes.
While the concept originated in Japan, it has become a popular strategy worldwide, especially in business and production environments.
Understanding how to implement practical Kaizen activities can bring significant benefits to organizations and individuals alike.
目次
What is Kaizen?
Kaizen is not just a methodology but also a mindset.
It promotes the idea that everything can be improved, from daily work tasks to complex projects.
The focus is on gradually improving processes rather than making one-time, sweeping changes.
By fostering a culture of continuous improvement, organizations can create an environment where employees are encouraged to contribute ideas and solutions.
The Principles of Kaizen
Continuous Improvement
At the heart of Kaizen lies the principle of continuous improvement.
No matter how efficient a process is, there’s always room for enhancement.
This principle encourages small, manageable changes rather than significant overhauls.
Employee Involvement
Kaizen emphasizes the importance of every team member’s input.
Employees at all levels should be encouraged to suggest improvements.
By involving everyone, organizations tap into a wide range of insights and ideas that can lead to meaningful changes.
Focus on Processes
Rather than blaming individuals for issues, Kaizen focuses on processes.
The belief is that poor processes are usually the root of problems and should be identified and improved.
Standardization
Once an improvement is made, it should be standardized so that it becomes a part of the regular workflow.
Standardization ensures that successful practices are consistently followed and applied.
Practical Kaizen Activities
Now that you understand the principles of Kaizen, let’s look at some practical activities that can be implemented to foster continuous improvement in your organization.
Identify Areas for Improvement
Begin by pinpointing areas that require improvement.
It could be anything from reducing waste to streamlining a particular process.
Gather feedback from employees to identify pain points and inefficiencies that need to be addressed.
Set Clear Goals
Once areas for improvement have been identified, set clear and achievable goals.
These goals should be specific, measurable, attainable, relevant, and time-bound (SMART).
Having clear objectives helps in measuring progress and evaluating the success of Kaizen activities.
Use the PDCA Cycle
The Plan-Do-Check-Act (PDCA) cycle is a fundamental tool in Kaizen activities.
Here’s how it works:
– **Plan**: Identify the problem and devise a plan to address it.
– **Do**: Implement the plan on a small scale.
– **Check**: Monitor the results to see if the plan worked.
– **Act**: If successful, implement the plan on a larger scale, and if not, refine and try again.
Conduct Regular Kaizen Events
Kaizen events, also known as “Kaizen blitz,” are short-term, focused activities designed to improve a part of the process quickly.
These events typically last from a few days to a week and involve cross-functional teams working together to identify and implement changes.
Empower Employees
Empowering employees means giving them the tools, resources, and authority to implement changes.
Encourage team members to take ownership of their work and suggest improvements.
This creates a sense of involvement and pride, leading to better outcomes.
The Benefits of Kaizen
Implementing practical Kaizen activities offers numerous benefits to both organizations and employees.
Here are some of the most significant advantages:
Increased Efficiency
Continually improving processes leads to increased efficiency.
As processes become more streamlined, organizations can accomplish more with fewer resources.
Higher Employee Morale
When employees are involved in the improvement process, they feel valued and more engaged.
Higher morale often leads to better performance and job satisfaction.
Better Quality
Kaizen aims to eliminate defects and improve quality at every step.
By focusing on incremental changes, organizations can consistently produce high-quality products or services.
Cost Savings
Reducing waste and improving processes can lead to significant cost savings.
Efficiency gains often result in lower operational costs and increased profitability.
Enhanced Customer Satisfaction
Better quality and efficiency translate to improved customer experiences.
Satisfied customers are likely to return and recommend the organization to others.
Challenges in Implementing Kaizen
While the benefits of Kaizen are substantial, implementing it is not without challenges.
Understanding these hurdles can help in overcoming them effectively.
Resistance to Change
People are often resistant to change, especially if they are comfortable with the status quo.
Overcoming this resistance requires effective communication, training, and involving employees in the improvement process.
Lack of Commitment
For Kaizen to succeed, commitment from leadership is crucial.
Without top management’s support, Kaizen activities may lack the necessary resources and authority to be effectively implemented.
Conclusion
Kaizen is a powerful strategy for continuous improvement that can bring significant benefits to organizations of all sizes.
By involving employees, focusing on processes, and implementing small, manageable changes, organizations can achieve long-term success.
Embracing the Kaizen mindset and integrating practical activities into daily operations can lead to higher efficiency, better quality, and increased employee satisfaction.
資料ダウンロード
QCD調達購買管理クラウド「newji」は、調達購買部門で必要なQCD管理全てを備えた、現場特化型兼クラウド型の今世紀最高の購買管理システムとなります。
ユーザー登録
調達購買業務の効率化だけでなく、システムを導入することで、コスト削減や製品・資材のステータス可視化のほか、属人化していた購買情報の共有化による内部不正防止や統制にも役立ちます。
NEWJI DX
製造業に特化したデジタルトランスフォーメーション(DX)の実現を目指す請負開発型のコンサルティングサービスです。AI、iPaaS、および先端の技術を駆使して、製造プロセスの効率化、業務効率化、チームワーク強化、コスト削減、品質向上を実現します。このサービスは、製造業の課題を深く理解し、それに対する最適なデジタルソリューションを提供することで、企業が持続的な成長とイノベーションを達成できるようサポートします。
オンライン講座
製造業、主に購買・調達部門にお勤めの方々に向けた情報を配信しております。
新任の方やベテランの方、管理職を対象とした幅広いコンテンツをご用意しております。
お問い合わせ
コストダウンが利益に直結する術だと理解していても、なかなか前に進めることができない状況。そんな時は、newjiのコストダウン自動化機能で大きく利益貢献しよう!
(Β版非公開)