- お役立ち記事
- Managing Collections and Their Use in Manufacturing
Managing Collections and Their Use in Manufacturing
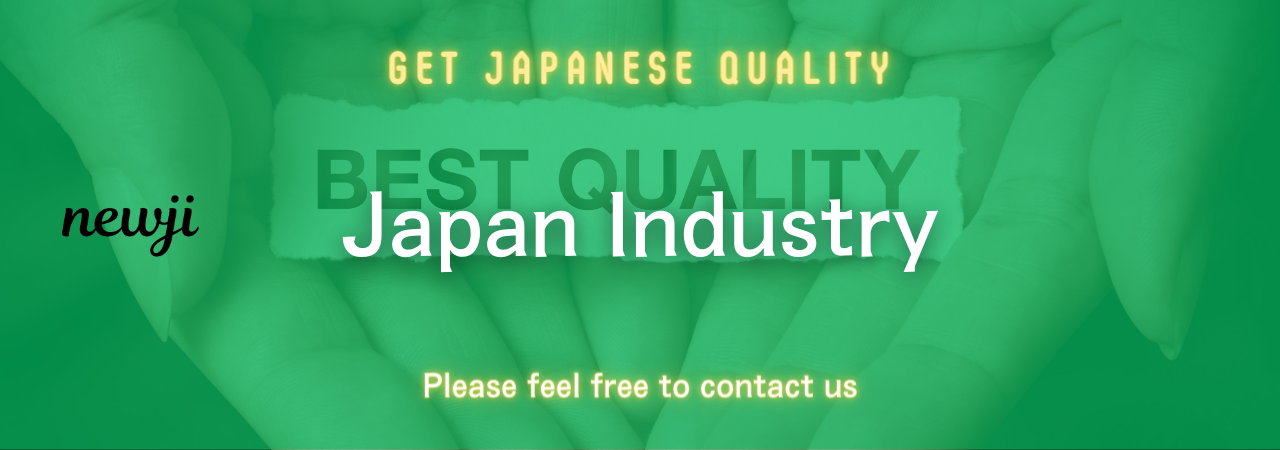
Managing collections and their use in manufacturing is a crucial task for any company looking to maintain efficiency and ensure resource optimization.
Effective collection management involves organizing, storing, and utilizing various materials, tools, and data in a way that minimizes waste and maximizes productivity.
目次
What is Collection Management?
Collection management refers to the systematic approach of gathering, organizing, storing, and using various items or data within a manufacturing setting.
It includes everything from raw materials to finished products, machinery parts, and even the digital data that inform various processes.
Efficient collection management helps ensure that nothing goes to waste and that everything is where it should be when it’s needed.
Why is Collection Management Important in Manufacturing?
Effective collection management is essential for several reasons.
First, it enhances productivity by ensuring that every tool, material, and piece of data is easily accessible.
Second, it minimizes waste and reduces costs by ensuring that materials are used efficiently.
Finally, it helps in maintaining high quality, as organized collections make it easier to follow procedural guidelines and maintain standards.
Enhancing Productivity
When collections like tools, raw materials, and data are well-organized, workers spend less time searching for what they need.
This optimization directly leads to increased productivity.
Having everything in its proper place means less downtime and smoother operations.
Reducing Waste and Costs
Efficient collection management minimizes waste by ensuring that materials and resources are used appropriately.
Moreover, it reduces storage costs by preventing overstocking and spoilage of perishable items.
By using only what is needed and keeping track of inventory, companies can reduce unnecessary expenditures.
Maintaining High Quality
Quality control is easier to maintain when collections are well-organized.
Procedural guidelines can be followed more easily, and issues can be identified and resolved quicker.
This results in a high-quality manufacturing process that meets industry standards and customer expectations.
Best Practices for Managing Collections
Adopting best practices for managing collections in manufacturing can yield significant benefits.
Here are some strategies to follow:
Inventory Management Systems
Investing in a robust inventory management system is crucial.
Such systems help track raw materials, finished products, and other essential items in real-time.
These tools not only record the quantities of items but also note their locations, making it easier to find them as needed.
Regular Audits
Conducting regular audits of collections helps identify discrepancies between recorded inventory and actual stock.
These audits are crucial for maintaining accuracy and ensuring that resources are managed properly.
Training
Training employees on the importance of collection management and how to use inventory systems efficiently is essential.
Well-trained staff are better equipped to manage collections effectively and contribute to efficient manufacturing processes.
Utilize Technology
Embracing technology, such as RFID tags and IoT devices, can significantly enhance the efficiency of collection management.
These technologies help in tracking inventory levels and the location of items, reducing manual errors and saving time.
Challenges in Collection Management
Despite its importance, managing collections in manufacturing comes with its own set of challenges.
Understanding these challenges can help in developing effective strategies to overcome them.
Overstocking and Understocking
One of the most common challenges is finding the right balance between overstocking and understocking.
Overstocking results in high storage costs and potential spoilage, while understocking can lead to production delays.
Effective inventory management can help strike this balance.
Inaccurate Record Keeping
Inaccurate record-keeping can lead to mismatches between physical stock and recorded inventory, creating confusion and inefficiencies.
Regular audits and the use of advanced inventory management systems can mitigate this issue.
Employee Compliance
Ensuring that all employees comply with collection management procedures is crucial.
Non-compliance can disrupt the entire system, leading to inefficiencies and errors.
Training and regular monitoring can help in maintaining compliance.
The Role of Data in Collection Management
Data plays a vital role in the effective management of collections.
Accurate data helps in forecasting demand, optimizing inventory levels, and improving overall efficiency.
Forecasting Demand
Accurate data allows companies to forecast demand more effectively.
By understanding trends and patterns, manufacturers can ensure they have the right amount of stock at the right time, thus reducing the risk of overstocking or understocking.
Optimizing Inventory Levels
Data-driven insights enable companies to optimize their inventory levels.
Companies can maintain efficient stock levels by analyzing usage patterns and past data, reducing waste and storage costs.
Improving Efficiency
Utilizing data helps in identifying bottlenecks and inefficiencies in the manufacturing process.
By addressing these issues, companies can improve overall operational efficiency and productivity.
Conclusion
Managing collections and their use in manufacturing is a multifaceted task that requires attention to detail, the implementation of best practices, and the effective use of technology.
By focusing on enhancing productivity, reducing waste and costs, maintaining high quality, and leveraging data, manufacturers can achieve optimal efficiency and sustained success.
Implementing robust inventory systems, conducting regular audits, and training staff thoroughly are essential steps in mastering collection management.
By diligently managing collections, manufacturers can ensure they are well-prepared to meet the challenges of today and tomorrow, paving the way for continued growth and efficiency.
資料ダウンロード
QCD調達購買管理クラウド「newji」は、調達購買部門で必要なQCD管理全てを備えた、現場特化型兼クラウド型の今世紀最高の購買管理システムとなります。
ユーザー登録
調達購買業務の効率化だけでなく、システムを導入することで、コスト削減や製品・資材のステータス可視化のほか、属人化していた購買情報の共有化による内部不正防止や統制にも役立ちます。
NEWJI DX
製造業に特化したデジタルトランスフォーメーション(DX)の実現を目指す請負開発型のコンサルティングサービスです。AI、iPaaS、および先端の技術を駆使して、製造プロセスの効率化、業務効率化、チームワーク強化、コスト削減、品質向上を実現します。このサービスは、製造業の課題を深く理解し、それに対する最適なデジタルソリューションを提供することで、企業が持続的な成長とイノベーションを達成できるようサポートします。
オンライン講座
製造業、主に購買・調達部門にお勤めの方々に向けた情報を配信しております。
新任の方やベテランの方、管理職を対象とした幅広いコンテンツをご用意しております。
お問い合わせ
コストダウンが利益に直結する術だと理解していても、なかなか前に進めることができない状況。そんな時は、newjiのコストダウン自動化機能で大きく利益貢献しよう!
(Β版非公開)