- お役立ち記事
- Dry Etching Processing OEM: Providing High-Precision Components
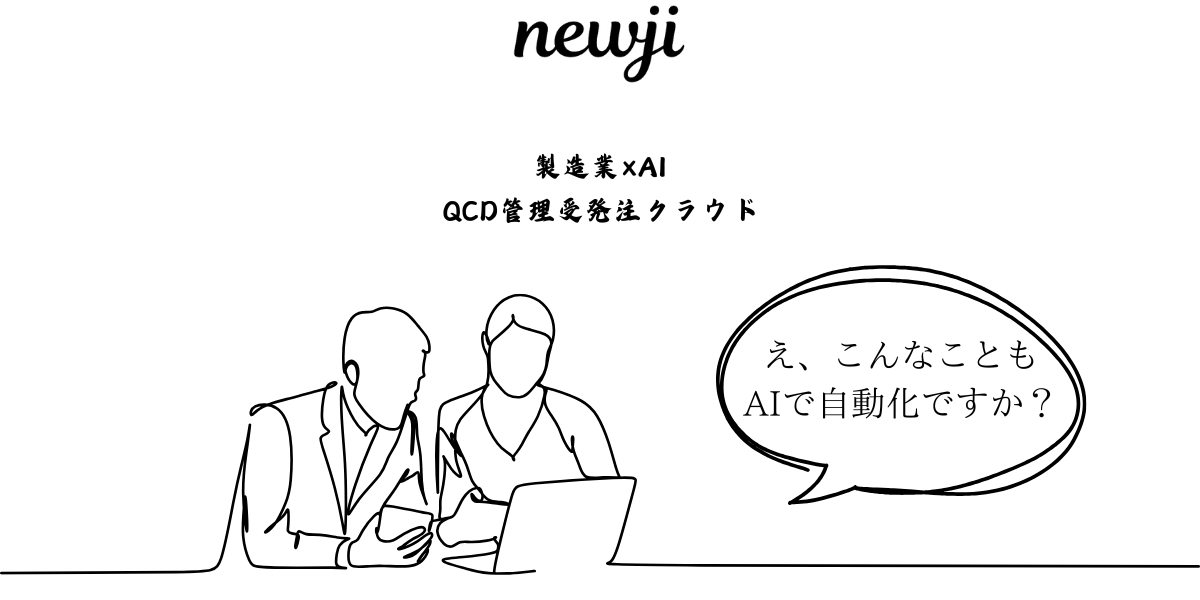
Dry Etching Processing OEM: Providing High-Precision Components
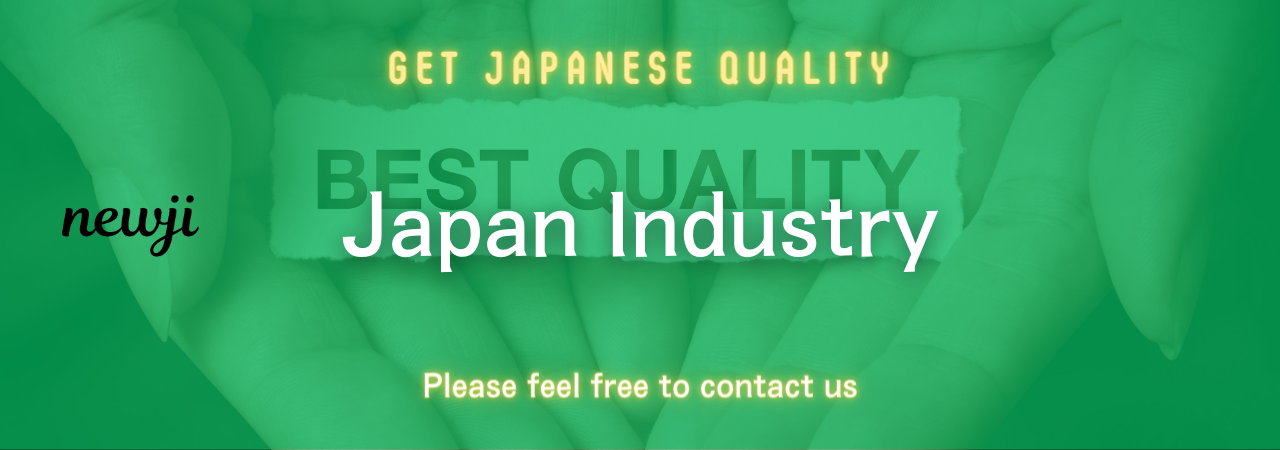
Dry etching is a critical technique used in the manufacturing of high-precision components, especially in the fields of semiconductors and microelectronics.
Dry etching processing allows for the meticulous shaping and designing of materials at a microscopic level, which is essential for creating detailed and exact components.
With the advancement of technology and increasing demands for smaller, more efficient devices, the role of dry etching has become indispensable.
目次
What is Dry Etching?
Dry etching is a process that uses reactive gases to remove material from a surface.
Unlike wet etching, which uses liquid chemicals, dry etching utilizes gases that react with the material to etch away precise patterns.
This method is particularly useful for applications where high precision and accuracy are required.
The Science Behind Dry Etching
Dry etching involves placing the material to be etched in a reaction chamber.
A plasma is generated by applying an electric field to a gas, converting it into ions and reactive radicals.
These reactive species interact with the surface of the material, selectively removing predefined areas without affecting the surrounding material.
The use of different gases can result in various etch profiles and depths, allowing for intricate designs and patterns.
Benefits of Dry Etching
High Precision and Accuracy
One of the primary advantages of dry etching is its ability to produce highly precise and accurate patterns.
This is crucial for industries that require meticulous component specifications, such as the semiconductor and microelectronics industries.
Dry etching ensures that each component is etched to exact dimensions, minimizing errors and improving overall quality.
Material Versatility
Dry etching is compatible with a wide range of materials, including metals, semiconductors, and dielectrics.
This versatility makes it a preferred choice for different applications, from creating microchips to developing medical devices.
The ability to etch various materials with precision allows manufacturers to innovate and push the boundaries of technology.
Controlled Etch Profiles
The advanced control over etch profiles that dry etching provides is another significant benefit.
Manufacturers can customize the etching process to achieve specific depths, shapes, and angles.
This control is critical for developing complex structures, such as microelectromechanical systems (MEMS) and nano-scale devices.
Applications of Dry Etching
Semiconductor Industry
The semiconductor industry heavily relies on dry etching to produce integrated circuits and microchips.
The ability to etch intricate patterns at a microscopic scale is crucial for developing smaller, faster, and more efficient electronic devices.
Dry etching enables the creation of multi-layered structures, essential for modern microprocessors and memory chips.
Microelectromechanical Systems (MEMS)
MEMS technology involves the integration of mechanical elements, sensors, and electronics on a common silicon substrate.
Dry etching plays a vital role in fabricating these complex structures, enabling the production of tiny components with high precision.
From accelerometers in smartphones to pressure sensors in automotive applications, MEMS devices benefit significantly from dry etching.
Display Technology
The fabrication of advanced display technologies, such as OLED and LCD screens, often utilizes dry etching.
The process allows for the precise patterning of pixels and circuitry, leading to high-resolution and energy-efficient displays.
This application extends to devices like televisions, smartphones, and tablets, where display quality is paramount.
OEM Dry Etching Services
What is OEM?
Original Equipment Manufacturer (OEM) refers to companies that produce parts or components that are used in another company’s end product.
OEM dry etching services provide specialized etching solutions to manufacturers who need high-precision components but may not have the necessary equipment or expertise in-house.
Advantages of OEM Dry Etching Services
Access to Expertise and Advanced Technology
OEM service providers have extensive experience and state-of-the-art equipment for dry etching.
By outsourcing dry etching needs, manufacturers can leverage the expertise and advanced technology of OEMs, ensuring high-quality results and staying competitive in their respective industries.
Cost-Effectiveness
Investing in dry etching equipment and maintaining a dedicated etching facility can be cost-prohibitive for many companies.
OEM services offer a cost-effective alternative, allowing manufacturers to access high-precision etching without significant capital investment.
This arrangement is particularly beneficial for small to mid-sized companies looking to innovate without breaking the bank.
Faster Time-to-Market
By utilizing OEM dry etching services, manufacturers can accelerate the development and production process.
OEMs can quickly turn around high-quality etched components, enabling faster time-to-market for new products.
This speed is crucial in industries where technological advancements and consumer demand drive rapid product cycles.
Choosing an OEM Dry Etching Service Provider
Reputation and Experience
When selecting an OEM dry etching service provider, it is essential to consider their reputation and experience.
Companies with a solid track record in the industry are more likely to deliver consistent and reliable results.
Look for providers with expertise in your specific application to ensure they can meet your unique requirements.
Technological Capabilities
Assess the technological capabilities of potential service providers.
Ensure they have access to advanced etching equipment and can handle the specific materials and designs you require.
Providers with cutting-edge technology are better equipped to deliver precise and high-quality components.
Quality Assurance
Quality assurance is critical in dry etching, where even minor errors can have significant implications.
Choose OEM service providers with stringent quality control measures and certifications to guarantee that your components meet the highest standards.
This assurance can help you avoid costly mistakes and maintain the integrity of your products.
Dry etching processing OEM services play a crucial role in the development and production of high-precision components.
With the ability to create intricate designs and achieve unparalleled accuracy, dry etching is invaluable across various industries.
By partnering with specialized OEM service providers, manufacturers can access cutting-edge technology, reduce costs, and accelerate their time-to-market, ultimately driving innovation and success.
資料ダウンロード
QCD調達購買管理クラウド「newji」は、調達購買部門で必要なQCD管理全てを備えた、現場特化型兼クラウド型の今世紀最高の購買管理システムとなります。
ユーザー登録
調達購買業務の効率化だけでなく、システムを導入することで、コスト削減や製品・資材のステータス可視化のほか、属人化していた購買情報の共有化による内部不正防止や統制にも役立ちます。
NEWJI DX
製造業に特化したデジタルトランスフォーメーション(DX)の実現を目指す請負開発型のコンサルティングサービスです。AI、iPaaS、および先端の技術を駆使して、製造プロセスの効率化、業務効率化、チームワーク強化、コスト削減、品質向上を実現します。このサービスは、製造業の課題を深く理解し、それに対する最適なデジタルソリューションを提供することで、企業が持続的な成長とイノベーションを達成できるようサポートします。
オンライン講座
製造業、主に購買・調達部門にお勤めの方々に向けた情報を配信しております。
新任の方やベテランの方、管理職を対象とした幅広いコンテンツをご用意しております。
お問い合わせ
コストダウンが利益に直結する術だと理解していても、なかなか前に進めることができない状況。そんな時は、newjiのコストダウン自動化機能で大きく利益貢献しよう!
(Β版非公開)