- お役立ち記事
- OEM Manufacturing of Interior Products to Achieve High-Quality Standards
OEM Manufacturing of Interior Products to Achieve High-Quality Standards
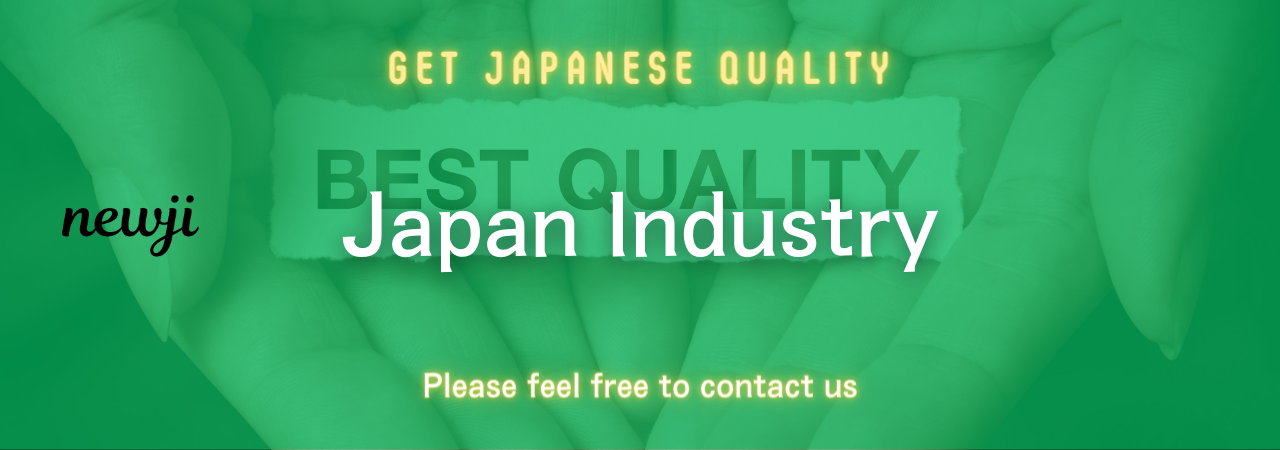
In today’s competitive market, achieving high-quality standards for interior products is crucial.
OEM manufacturing, or Original Equipment Manufacturing, provides a viable solution for companies seeking to ensure that their products meet these standards.
OEM manufacturing involves outsourcing the production of goods to specialized factories that have the expertise, technology, and capacity to produce high-quality interior products.
目次
What is OEM Manufacturing?
OEM manufacturing is a process where companies design products and then contract other manufacturers to produce them.
These manufacturers, known as OEMs, have the necessary skills and equipment to manufacture products that meet specific standards and requirements.
This approach allows businesses to focus on their core competencies, such as design and marketing, while relying on OEMs for production.
Benefits of OEM Manufacturing for Interior Products
Quality Assurance
One of the significant benefits of OEM manufacturing is the high level of quality assurance.
OEM manufacturers specialize in producing specific types of products and often have stringent quality control measures in place.
This ensures that the interior products meet or exceed the required standards, leading to increased customer satisfaction.
Cost Efficiency
OEM manufacturing can be more cost-efficient than producing goods in-house.
By outsourcing production, companies can reduce their overhead costs, such as labor, equipment, and facility maintenance.
OEM manufacturers often have economies of scale that allow them to produce goods at a lower cost, translating to savings for the contracting company.
Focus on Core Competencies
By partnering with OEM manufacturers, companies can focus on their core competencies, such as design, marketing, and customer service.
This enables them to allocate resources more effectively and drive innovation in their products.
It also allows them to respond more quickly to market trends and customer needs, giving them a competitive edge.
Access to Advanced Technology
OEM manufacturers often invest in advanced technology and equipment to stay competitive.
By outsourcing production to these manufacturers, companies can leverage cutting-edge technology without making significant capital investments.
This access to advanced technology can result in higher-quality interior products and improved production efficiency.
Steps to Achieve High-Quality Standards with OEM Manufacturing
Identify Reputable OEM Manufacturers
The first step in achieving high-quality standards with OEM manufacturing is identifying reputable manufacturers.
Companies should conduct thorough research, review customer testimonials, and evaluate potential manufacturers’ production capabilities.
Choosing an OEM with a proven track record of quality and reliability is essential.
Clear Communication of Specifications and Standards
Effective communication is crucial in OEM manufacturing.
Companies must clearly communicate their product specifications and quality standards to the OEM manufacturer.
This includes providing detailed drawings, material requirements, and any specific production processes that need to be followed.
Clear communication helps ensure that the final products meet the desired quality standards.
Implement Rigorous Quality Control Measures
To achieve high-quality standards, companies must work closely with the OEM manufacturer to implement rigorous quality control measures.
This may include regular inspections, testing, and audits at various stages of production.
Collaborating with the OEM to establish quality control protocols helps maintain consistency and ensures that any issues are identified and addressed promptly.
Ongoing Collaboration and Feedback
Maintaining ongoing collaboration and providing feedback throughout the production process is essential in OEM manufacturing.
Regular communication with the OEM manufacturer helps address any concerns or adjustments required to meet quality standards.
Establishing a strong working relationship with the OEM can lead to continuous improvement and higher-quality interior products over time.
Challenges in OEM Manufacturing
Quality Control Issues
While OEM manufacturing offers many benefits, there can be challenges related to quality control.
Delegating production to an external manufacturer involves some risks, such as variations in quality or non-compliance with specified standards.
Therefore, rigorous quality control measures and communication are crucial to mitigate these risks.
Intellectual Property Concerns
Another challenge in OEM manufacturing is protecting intellectual property (IP).
When outsourcing production, companies need to ensure that their designs and proprietary processes are safeguarded.
It’s essential to establish clear agreements with the OEM manufacturer regarding the use and protection of IP to prevent any potential infringements or unauthorized use.
Logistical Considerations
Outsourcing production to OEM manufacturers may involve logistical challenges, such as coordinating production schedules, shipping, and managing inventory.
Companies need to have robust logistical plans and clear communication with the OEM to ensure timely delivery and availability of interior products.
Case Studies: Successful OEM Manufacturing of Interior Products
Automotive Interiors
Many leading automotive companies use OEM manufacturing to produce high-quality interior components.
For example, luxury car manufacturers often partner with specialized OEMs to produce leather seats, dashboards, and consoles that adhere to strict quality standards.
This collaboration ensures that the final vehicles offer premium quality and comfort to customers.
Furniture Industry
In the furniture industry, OEM manufacturing plays a significant role in producing high-quality home and office furniture.
Many furniture brands design their products in-house but rely on OEM manufacturers to produce them.
This approach allows them to maintain quality standards while meeting market demands efficiently.
Consumer Electronics
Consumer electronics companies also benefit from OEM manufacturing for interior components such as enclosures, displays, and circuit boards.
By outsourcing production to specialized OEMs, these companies can maintain the high standards required for their products while focusing on innovation and customer experience.
In conclusion, OEM manufacturing offers numerous advantages for companies seeking to achieve high-quality standards for interior products.
By partnering with reputable OEM manufacturers, businesses can ensure quality assurance, cost-efficiency, and access to advanced technology.
Effective communication, rigorous quality control, and ongoing collaboration are essential to successful OEM manufacturing.
While there are challenges, such as quality control issues and logistical considerations, the benefits outweigh the risks when managed effectively.
OEM manufacturing continues to play a pivotal role in producing high-quality interior products across various industries.
資料ダウンロード
QCD調達購買管理クラウド「newji」は、調達購買部門で必要なQCD管理全てを備えた、現場特化型兼クラウド型の今世紀最高の購買管理システムとなります。
ユーザー登録
調達購買業務の効率化だけでなく、システムを導入することで、コスト削減や製品・資材のステータス可視化のほか、属人化していた購買情報の共有化による内部不正防止や統制にも役立ちます。
NEWJI DX
製造業に特化したデジタルトランスフォーメーション(DX)の実現を目指す請負開発型のコンサルティングサービスです。AI、iPaaS、および先端の技術を駆使して、製造プロセスの効率化、業務効率化、チームワーク強化、コスト削減、品質向上を実現します。このサービスは、製造業の課題を深く理解し、それに対する最適なデジタルソリューションを提供することで、企業が持続的な成長とイノベーションを達成できるようサポートします。
オンライン講座
製造業、主に購買・調達部門にお勤めの方々に向けた情報を配信しております。
新任の方やベテランの方、管理職を対象とした幅広いコンテンツをご用意しております。
お問い合わせ
コストダウンが利益に直結する術だと理解していても、なかなか前に進めることができない状況。そんな時は、newjiのコストダウン自動化機能で大きく利益貢献しよう!
(Β版非公開)