- お役立ち記事
- Revolutionizing Japanese Manufacturing: The Power of AI Anomaly Detection Services
Revolutionizing Japanese Manufacturing: The Power of AI Anomaly Detection Services
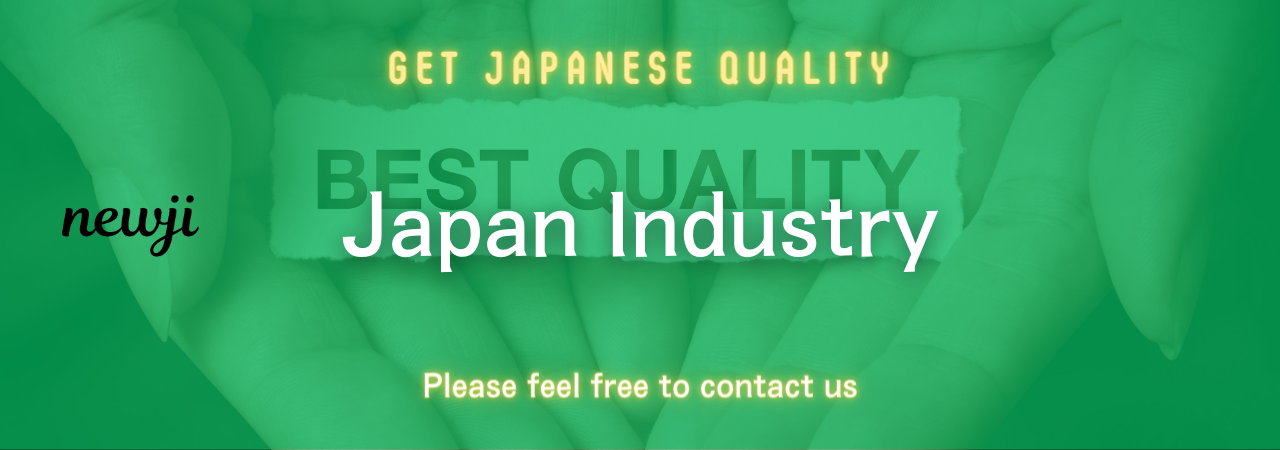
目次
Introduction
Japanese manufacturing has long been celebrated for its quality, precision, and efficiency.
Over the decades, the industry has consistently set benchmarks through innovations in technology and processes, ensuring its leading position on the global stage.
However, as the landscape continues to evolve, new challenges and opportunities arise.
One transformative innovation making waves in the industry is AI anomaly detection services.
This technology holds the potential to further elevate Japanese manufacturing standards, reduce costs, and significantly improve operational efficiency.
The Evolution of AI in Manufacturing
AI, or Artificial Intelligence, has revolutionized various industries, and manufacturing is no exception.
In its essence, AI leverages advanced algorithms and machine learning techniques to mimic human cognitive functions.
In the manufacturing sector, AI’s applications range from predictive maintenance to quality control and demand forecasting.
The Role of AI Anomaly Detection in Manufacturing
AI anomaly detection services identify deviations from the norm within a dataset that could indicate issues or anomalies.
In manufacturing, this can apply to a wide range of data points, including machine performance, product quality, and supply chain metrics.
By quickly detecting these anomalies, manufacturers can address potential problems before they result in significant downtime or product defects.
Practical Applications of AI Anomaly Detection in Japanese Manufacturing
Enhanced Quality Control
Japanese manufacturing is synonymous with high-quality products.
AI anomaly detection can take this commitment to quality even further.
By continuously monitoring the production process, AI systems can detect even the slightest deviations that might compromise quality.
For example, in an automotive assembly line, AI can identify minute variations in part dimensions or assembly torque that could lead to future issues.
This real-time detection allows for immediate adjustments, ensuring the final product maintains the highest standards.
Predictive Maintenance
Manufacturing equipment is costly and often operates around the clock.
Unexpected breakdowns can result in significant financial losses and operational disruptions.
AI anomaly detection can help predict these breakdowns before they occur.
By analyzing patterns in machine data, the system can flag unusual behaviors indicative of wear or potential failure.
This allows maintenance teams to address issues proactively, reducing downtime and extending the equipment’s lifespan.
Supply Chain Optimization
AI anomaly detection isn’t limited to the production floor.
It can also enhance supply chain efficiency.
For instance, it can monitor logistics data to identify inconsistencies in delivery times or shipping conditions that might affect raw material quality.
By ensuring materials arrive in optimal condition and on schedule, manufacturers can avoid production delays and maintain steady output.
Advantages of Using AI Anomaly Detection in Japanese Manufacturing
Increased Efficiency
Efficiency is at the core of Japanese manufacturing principles, and AI anomaly detection takes this to new heights.
By automating the detection of irregularities, the technology reduces the need for manual inspections and interventions.
This streamlines operations and frees up human resources to focus on more strategic tasks.
Cost Savings
While the initial investment in AI technology can be significant, the long-term cost savings are substantial.
Preventing equipment failures, reducing waste, and optimizing supply chain operations all contribute to lower operational costs.
In addition, the ability to maintain high-quality standards reduces the incidence of costly product recalls or rework.
Enhanced Decision-Making
AI provides manufacturers with valuable insights derived from vast amounts of data.
These insights enable more informed decision-making.
Whether it’s adjusting production parameters or planning maintenance schedules, manufacturers can base their decisions on accurate, real-time data.
Challenges and Considerations
Initial Investment
One of the primary challenges of implementing AI anomaly detection services is the initial investment.
This includes not only the cost of the technology itself but also the expenses related to integrating it with existing systems and training staff.
However, manufacturers should view this as a strategic investment with significant long-term returns.
Data Quality
The effectiveness of AI systems hinges on the quality of the data they analyze.
Incomplete or inaccurate data can lead to erroneous conclusions and undermine the system’s reliability.
Manufacturers must ensure they have robust data collection and management practices in place.
Change Management
Adopting new technologies often requires a cultural shift within an organization.
Employees may be resistant to change, particularly if they fear that AI could replace their roles.
Companies must approach implementation with a clear communication strategy, emphasizing that AI is a tool to enhance human capabilities rather than replace them.
Best Practices for Implementing AI Anomaly Detection
Start Small and Scale
It’s advisable to begin with a small-scale pilot project to test the technology’s effectiveness and identify any potential issues.
This allows manufacturers to refine their approach before a full-scale rollout.
Once the pilot proves successful, the system can be scaled up incrementally across the organization.
Collaborate with Experts
Working with experts in AI and machine learning can significantly ease the implementation process.
These professionals can provide valuable guidance on choosing the right technology, setting up systems, and training staff to use the new tools effectively.
Continuous Monitoring and Improvement
AI systems require ongoing monitoring and refinement to ensure they remain effective.
Regularly reviewing the system’s performance and making necessary adjustments will help manufacturers continue to reap the benefits of AI anomaly detection.
Supplier Negotiation Techniques in the AI Era
Leveraging Data for Better Terms
Incorporating AI into manufacturing processes provides a wealth of data that can be used in supplier negotiations.
For example, manufacturers can use data on material consumption patterns and operational efficiency to negotiate better pricing or delivery terms.
This data-driven approach builds stronger cases and can lead to more favorable contract terms.
Demonstrating Commitment to Quality
AI anomaly detection underscores a manufacturer’s commitment to quality and precision.
This can be a valuable bargaining chip in negotiations with suppliers.
Suppliers are more likely to offer competitive terms to businesses they view as reliable and committed to maintaining high standards.
Market Conditions and the Future of AI in Japanese Manufacturing
Technology Trends
The global market for AI in manufacturing is growing rapidly, driven by the need for improved efficiency, quality, and cost savings.
In Japan, this trend is bolstered by the country’s strong technological infrastructure and commitment to innovation.
Manufacturers that adopt AI technologies now are likely to gain a competitive advantage in the years to come.
Regulatory Environment
As AI becomes more integrated into manufacturing processes, regulatory frameworks will evolve to address new challenges.
Manufacturers must stay informed about regulatory developments and ensure their AI implementations comply with all relevant standards and guidelines.
Workforce Development
As AI technology advances, the skills required in the manufacturing workforce will also evolve.
Companies must invest in training and development programs to equip their employees with the necessary skills to work alongside AI systems.
This includes not only technical skills but also the ability to interpret and act on AI-generated insights.
Conclusion
AI anomaly detection services represent a significant opportunity for Japanese manufacturing to cement its position as a global leader in quality and efficiency.
By enhancing quality control, predicting equipment maintenance needs, and optimizing supply chains, AI can drive substantial improvements across the manufacturing process.
However, successful implementation requires careful planning, investment, and a commitment to continuous improvement.
As manufacturers navigate these challenges and leverage the benefits of AI, they will be well-positioned to thrive in an increasingly competitive global market.
資料ダウンロード
QCD調達購買管理クラウド「newji」は、調達購買部門で必要なQCD管理全てを備えた、現場特化型兼クラウド型の今世紀最高の購買管理システムとなります。
ユーザー登録
調達購買業務の効率化だけでなく、システムを導入することで、コスト削減や製品・資材のステータス可視化のほか、属人化していた購買情報の共有化による内部不正防止や統制にも役立ちます。
NEWJI DX
製造業に特化したデジタルトランスフォーメーション(DX)の実現を目指す請負開発型のコンサルティングサービスです。AI、iPaaS、および先端の技術を駆使して、製造プロセスの効率化、業務効率化、チームワーク強化、コスト削減、品質向上を実現します。このサービスは、製造業の課題を深く理解し、それに対する最適なデジタルソリューションを提供することで、企業が持続的な成長とイノベーションを達成できるようサポートします。
オンライン講座
製造業、主に購買・調達部門にお勤めの方々に向けた情報を配信しております。
新任の方やベテランの方、管理職を対象とした幅広いコンテンツをご用意しております。
お問い合わせ
コストダウンが利益に直結する術だと理解していても、なかなか前に進めることができない状況。そんな時は、newjiのコストダウン自動化機能で大きく利益貢献しよう!
(Β版非公開)