- お役立ち記事
- Digital Manufacturing Benefits and Implementation in Industry
Digital Manufacturing Benefits and Implementation in Industry
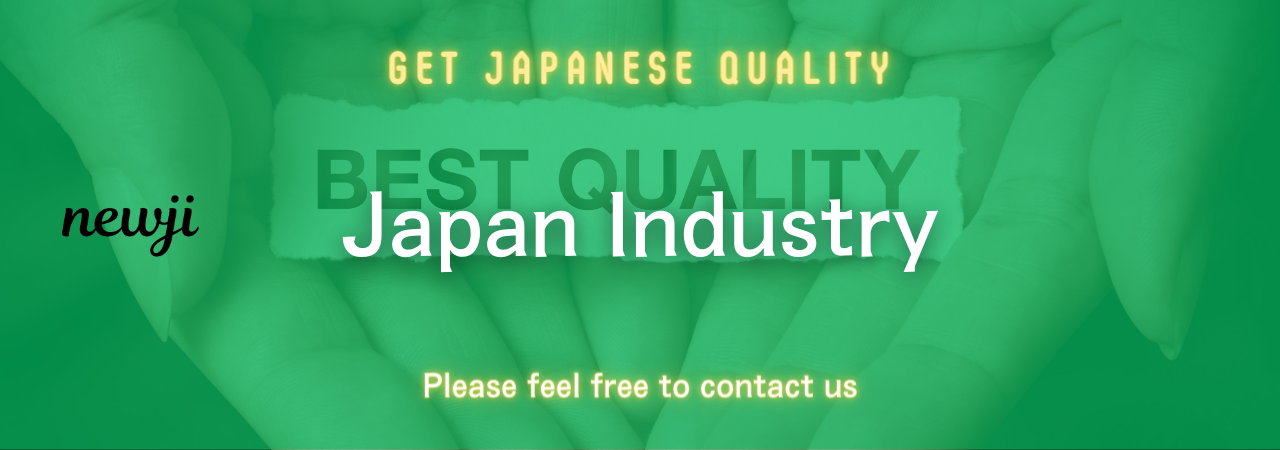
目次
What is Digital Manufacturing?
Digital manufacturing is a method where advanced technologies like the Internet of Things (IoT), artificial intelligence (AI), and big data are used to improve the manufacturing process.
These technologies help in making better decisions, streamlining operations, and reducing costs.
By integrating digital solutions, manufacturers can enhance productivity and efficiency.
Benefits of Digital Manufacturing
Improved Efficiency
One of the main advantages of digital manufacturing is improved efficiency.
Automated processes and real-time data analysis help in identifying bottlenecks and improving them.
This leads to faster production times and reduced waste.
Cost Reduction
Digital manufacturing reduces costs in various ways.
First, by automating various tasks, the need for manual labor is minimized, which saves money.
Second, predictive maintenance can be done using IoT and sensors, reducing unexpected breakdowns and associated costs.
Higher Quality Products
With digital manufacturing, quality control is easier to manage.
Real-time monitoring ensures that defects are detected early, allowing quick corrective actions.
AI algorithms can predict quality issues before they happen, ensuring that the end products meet high standards.
Better Flexibility
A digital approach allows manufacturers to be more flexible.
Changing production lines for new products becomes simpler and faster.
Digital designs and simulations enable quick adjustments without needing extensive rework.
Enhanced Data Analysis
Data is a valuable asset in digital manufacturing.
Advanced analytics can provide insights into various aspects of the manufacturing process.
Understanding patterns and trends helps in making informed decisions, ultimately leading to optimized operations.
How to Implement Digital Manufacturing in Industry
Assess Current Capabilities
Before implementing digital manufacturing, it is crucial to assess the current capabilities.
Understand the existing processes, equipment, and technology.
Identify areas that would benefit the most from digital enhancements.
Develop a Clear Strategy
A well-defined strategy is essential for successful implementation.
Outline the goals and objectives of transitioning to digital manufacturing.
This plan should include timelines, budgets, and key performance indicators (KPIs) to measure success.
Invest in Technology
Invest in the right technologies that align with the goals of digital manufacturing.
This may include IoT devices, AI software, data analytics tools, and cloud computing.
Ensure that the technology integrates seamlessly with existing systems.
Train Staff
Human resources are as crucial as technology for digital manufacturing.
Conduct training sessions for employees to familiarize them with new tools and processes.
An informed workforce is better equipped to leverage digital solutions effectively.
Implement Gradually
Instead of a massive overhaul, implement digital manufacturing gradually.
Start with pilot projects to test the new technologies and processes.
Learn from these small-scale implementations and refine the approach before scaling up.
Monitor and Optimize
Once digital manufacturing is implemented, continuous monitoring is vital.
Use data analytics to track performance and identify areas for improvement.
Regularly update the technology and processes to stay competitive.
Common Challenges and How to Overcome Them
Initial Costs
One of the significant barriers is the initial investment required for digital manufacturing.
While the long-term benefits outweigh the costs, the upfront expenditure can be substantial.
To overcome this, consider phased implementation and explore financing options.
Security Concerns
With increased connectivity, the risk of cyber threats also rises.
Implement robust cybersecurity measures to protect sensitive data and systems.
Regularly update security protocols and conduct audits to ensure safety.
Resistance to Change
Employees and management may resist transitioning from traditional methods to digital manufacturing.
Address this by fostering a culture of innovation and continuous improvement.
Communicate the benefits clearly and involve all stakeholders in the transition process.
Complexity
The complexity of integrating various technologies can be daunting.
Work with experienced vendors and consultants who specialize in digital manufacturing to simplify the process.
Choose scalable solutions that can grow with your business needs.
Lack of Expertise
A shortage of skilled professionals in digital manufacturing is another challenge.
Invest in training programs, and consider partnering with educational institutions to develop the required expertise.
Upskilling existing employees can also bridge this gap.
Success Stories of Digital Manufacturing
Automotive Industry
The automotive industry has been a frontrunner in adopting digital manufacturing.
Companies use digital twins and simulations to design and test vehicles before production, reducing time and cost.
Robust IoT systems ensure predictive maintenance, enhancing the longevity of machinery.
Aerospace Sector
In the aerospace sector, digital manufacturing aids in producing complex components with high precision.
3D printing and advanced simulations are utilized to create parts that meet stringent safety standards.
These technologies also enable rapid prototyping, accelerating innovation.
Consumer Electronics
Consumer electronics manufacturers benefit from digital manufacturing through enhanced flexibility.
Quick adjustments to production lines enable them to keep up with fast-changing market trends.
Real-time quality control ensures that devices meet the high expectations of consumers.
The Future of Digital Manufacturing
The future of digital manufacturing is promising, with continuous advancements in technology.
AI and machine learning will play a more significant role in decision-making processes.
The increased adoption of 5G networks will further enhance connectivity and data transfer speeds.
Moreover, sustainable manufacturing practices can be integrated with digital solutions, creating an eco-friendly industry.
In conclusion, digital manufacturing offers numerous benefits, from cost reduction to improved quality and flexibility.
By carefully planning and strategically implementing digital solutions, industries can stay competitive and innovative.
While challenges exist, they can be overcome with the right approach and resources.
The future of manufacturing is digital, and embracing this trend will lead to sustainable growth and success.
資料ダウンロード
QCD調達購買管理クラウド「newji」は、調達購買部門で必要なQCD管理全てを備えた、現場特化型兼クラウド型の今世紀最高の購買管理システムとなります。
ユーザー登録
調達購買業務の効率化だけでなく、システムを導入することで、コスト削減や製品・資材のステータス可視化のほか、属人化していた購買情報の共有化による内部不正防止や統制にも役立ちます。
NEWJI DX
製造業に特化したデジタルトランスフォーメーション(DX)の実現を目指す請負開発型のコンサルティングサービスです。AI、iPaaS、および先端の技術を駆使して、製造プロセスの効率化、業務効率化、チームワーク強化、コスト削減、品質向上を実現します。このサービスは、製造業の課題を深く理解し、それに対する最適なデジタルソリューションを提供することで、企業が持続的な成長とイノベーションを達成できるようサポートします。
オンライン講座
製造業、主に購買・調達部門にお勤めの方々に向けた情報を配信しております。
新任の方やベテランの方、管理職を対象とした幅広いコンテンツをご用意しております。
お問い合わせ
コストダウンが利益に直結する術だと理解していても、なかなか前に進めることができない状況。そんな時は、newjiのコストダウン自動化機能で大きく利益貢献しよう!
(Β版非公開)