- お役立ち記事
- Causes and Solutions for Sink Marks in Manufacturing
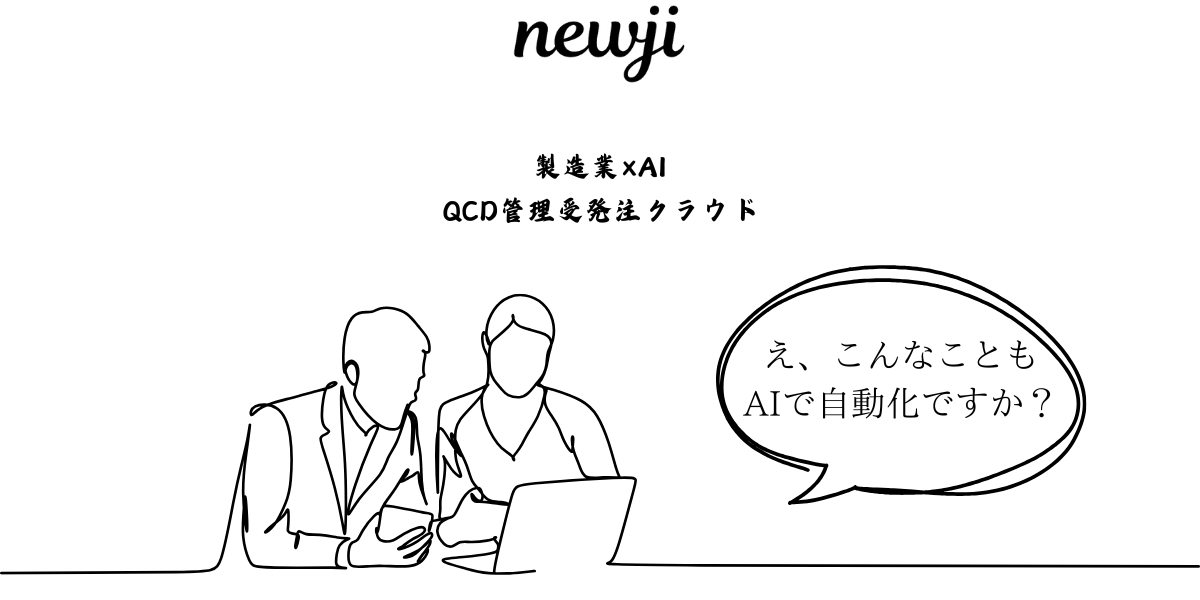
Causes and Solutions for Sink Marks in Manufacturing
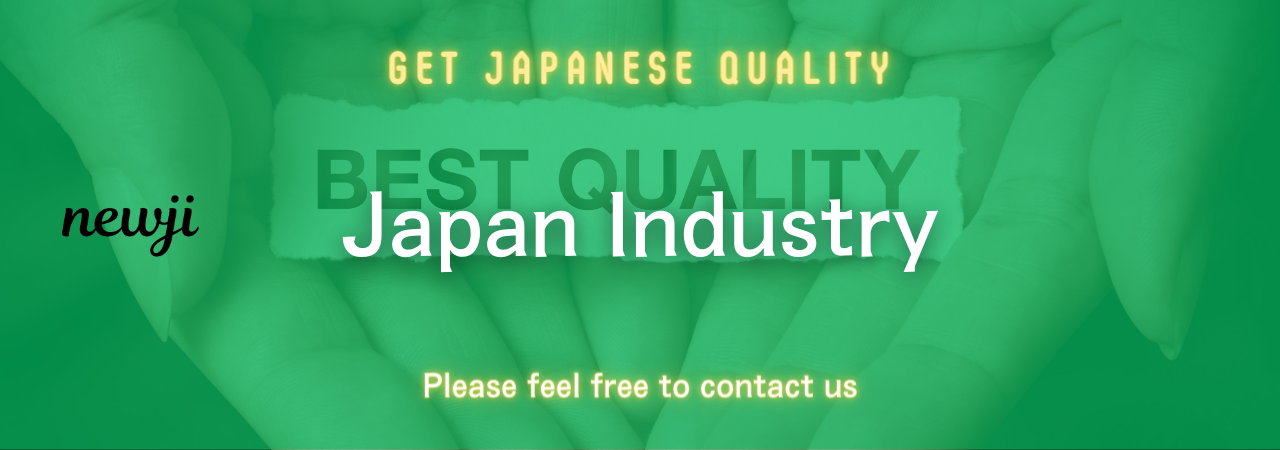
目次
What Are Sink Marks?
Sink marks are small depressions or indents that appear on the surface of manufactured products.
They are most commonly found in plastic parts but can occur in other materials as well.
These imperfections are typically a result of material shrinkage during the cooling process.
While they might seem insignificant, sink marks can affect the overall appearance, structural integrity, and functionality of a product.
Common Causes of Sink Marks
Material Shrinkage
One of the primary causes of sink marks is material shrinkage.
As the material cools and solidifies, it contracts.
If the contraction is uneven, it can create depressions or indentations on the surface of the product.
This issue is particularly prevalent in plastic manufacturing due to the thermal properties of polymers.
Inadequate Cooling
Another significant factor contributing to sink marks is inadequate cooling.
If the material does not cool uniformly, it can lead to shrinkage in certain areas.
This uneven cooling can be due to various factors, including improper mold design, lack of coolant channels, or inappropriate cooling time.
Poor Mold Design
The design of the mold itself plays a crucial role in determining the quality of the final product.
If the mold does not have sufficient support structures, the risk of sink marks increases.
Sharp corners, thick areas, and unsupported sections in the mold can exacerbate this issue.
Improper Flow Rate
The flow rate of the material entering the mold is another critical factor.
If the material flows too quickly or too slowly, it may not fill the mold evenly, resulting in sink marks.
Maintaining an optimal flow rate is essential for a uniform fill and to minimize shrinkage.
How to Prevent Sink Marks
Optimize Mold Design
Designing the mold correctly can significantly reduce the likelihood of sink marks.
Incorporating uniform wall thickness, rounded corners, and adequate support structures can help in achieving a more balanced cooling and shrinkage process.
Additionally, placing cooling channels strategically in the mold ensures uniform temperature distribution, which can mitigate uneven shrinkage.
Control Cooling Time
Adjusting the cooling time can also help prevent sink marks.
Allowing the material more time to cool and solidify uniformly can reduce the chances of surface indentations.
Using specialized cooling systems and materials that cool at a consistent rate can further enhance this process.
Regulate Flow Rate
Ensuring that the material flows into the mold at an optimal rate is a key step in avoiding sink marks.
This can be achieved by adjusting the injection speed, pressure, and temperature settings.
Careful monitoring and regulation of these parameters can help in maintaining an even fill and reducing shrinkage.
Select Appropriate Materials
Choosing materials with lower shrinkage properties can also make a significant difference.
Certain polymers are designed to minimize shrinkage during the cooling process, reducing the risk of sink marks.
Consulting with material suppliers and understanding the thermal properties of available materials can guide better material selection.
Advanced Solutions for Sink Marks
Use of Advanced Simulation Software
Modern manufacturing processes often utilize advanced simulation software to predict and rectify potential issues like sink marks.
These software tools can simulate the entire injection molding process, including material flow, cooling, and shrinkage.
Using these simulations, manufacturers can optimize their processes and design to minimize sink marks before actual production starts.
Adopt New Manufacturing Techniques
Innovative manufacturing techniques like gas-assisted or water-assisted injection molding can help in reducing sink marks.
These techniques improve the uniformity of material distribution and cooling, thereby lowering the chances of sink marks.
While these methods may require initial investments, they can lead to higher quality, more consistent products.
Real-Time Monitoring Systems
Implementing real-time monitoring systems in the production line can provide immediate feedback on various parameters, such as temperature, pressure, and flow rate.
These systems allow for on-the-fly adjustments to correct any anomalies that might lead to sink marks.
By continuously monitoring and adjusting the process, manufacturers can maintain higher quality standards.
Addressing Sink Marks in Existing Products
Surface Treatment Techniques
For products that already have sink marks, surface treatment techniques like sanding, filling, and painting can help in masking these imperfections.
While these methods do not eliminate the underlying issue, they can improve the aesthetic appearance of the product.
Rework and Remanufacture
In some cases, reworking or remanufacturing the affected parts may be necessary.
This approach can be resource-intensive but ensures that the final product meets quality standards.
Analyzing the root cause of sink marks during the rework process can also provide valuable insights for preventing future occurrences.
Quality Control Measures
Implementing stringent quality control measures throughout the manufacturing process can help in identifying sink marks early.
Using advanced inspection techniques like 3D scanning and non-destructive testing can detect even minor imperfections.
Early detection allows for timely corrective actions, reducing the impact on the final product.
Sink marks may seem like a minor issue, but they can have significant implications for the quality and performance of manufactured products.
By understanding the common causes and implementing preventive measures, manufacturers can minimize the occurrence of sink marks.
Additionally, adopting advanced technologies and maintaining stringent quality control can further enhance product quality and reduce the risk of surface imperfections.
資料ダウンロード
QCD調達購買管理クラウド「newji」は、調達購買部門で必要なQCD管理全てを備えた、現場特化型兼クラウド型の今世紀最高の購買管理システムとなります。
ユーザー登録
調達購買業務の効率化だけでなく、システムを導入することで、コスト削減や製品・資材のステータス可視化のほか、属人化していた購買情報の共有化による内部不正防止や統制にも役立ちます。
NEWJI DX
製造業に特化したデジタルトランスフォーメーション(DX)の実現を目指す請負開発型のコンサルティングサービスです。AI、iPaaS、および先端の技術を駆使して、製造プロセスの効率化、業務効率化、チームワーク強化、コスト削減、品質向上を実現します。このサービスは、製造業の課題を深く理解し、それに対する最適なデジタルソリューションを提供することで、企業が持続的な成長とイノベーションを達成できるようサポートします。
オンライン講座
製造業、主に購買・調達部門にお勤めの方々に向けた情報を配信しております。
新任の方やベテランの方、管理職を対象とした幅広いコンテンツをご用意しております。
お問い合わせ
コストダウンが利益に直結する術だと理解していても、なかなか前に進めることができない状況。そんな時は、newjiのコストダウン自動化機能で大きく利益貢献しよう!
(Β版非公開)