- お役立ち記事
- Design and Applications of Stages in Manufacturing
Design and Applications of Stages in Manufacturing
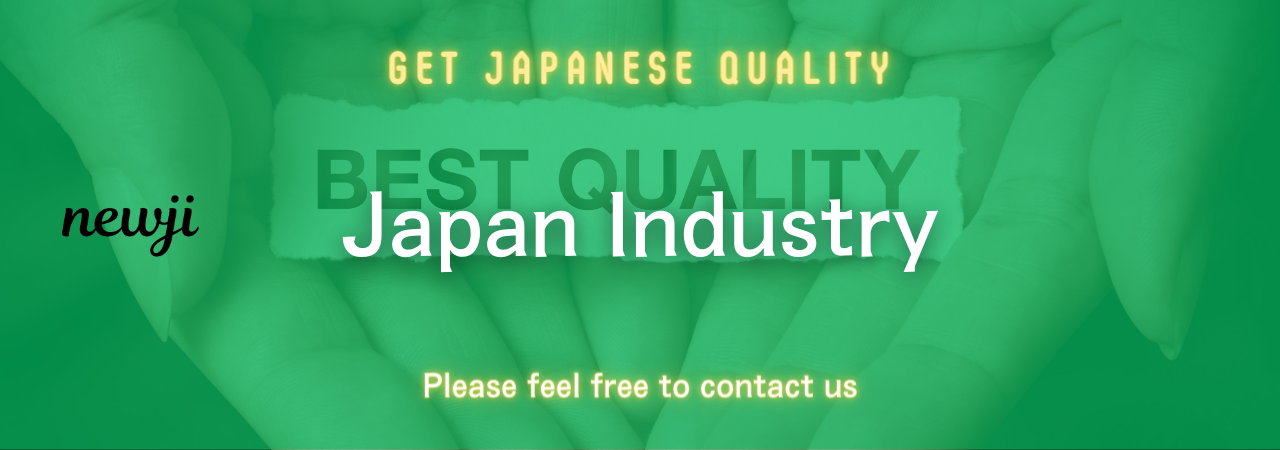
In the realm of manufacturing, the design and application of stages are crucial for the creation and assembly of various products.
Manufacturers rely on stages to improve efficiency, maintain precision, and ensure smooth production processes.
These stages often involve the use of mechanical and electrical components that work seamlessly.
We will delve into the multiple aspects of this topic to gain a clear perspective.
目次
Understanding Manufacturing Stages
Manufacturing stages are individual steps through which raw materials are transformed into final products.
Each stage has a specific function and often involves specialized machinery.
Concept and Importance
The concept of stages in manufacturing is akin to following a recipe.
Just as each ingredient and step in cooking are necessary for a delicious dish, each stage in manufacturing is critical for the quality and functionality of the final product.
The stages ensure that production is methodical and systematic.
This systematic approach minimizes errors and enhances quality control.
Breaking Down the Stages
Each stage in manufacturing serves a unique purpose.
Common stages include material preparation, machining, assembly, and quality control.
Material preparation involves collecting and processing raw materials.
Machining transforms these materials into parts or components through processes such as cutting, drilling, and milling.
Assembly is the stage where various parts are put together to form the final product.
Finally, quality control checks for any defects or discrepancies, ensuring the product meets specific standards.
Design Considerations in Manufacturing Stages
Designing manufacturing stages requires careful planning and consideration of various factors.
Engineers must ensure that every component and process is optimized for efficiency and effectiveness.
Raw Material Selection
Choosing the right raw materials is foundational for a successful manufacturing process.
The materials must align with the product’s specifications and performance requirements.
Selecting high-quality materials minimizes issues later in the production stages.
Machine Selection
The choice of machinery significantly impacts the manufacturing stages.
Machines must be versatile and capable of handling different tasks.
They should also be energy-efficient and easy to maintain.
Process Optimization
Optimization ensures that each stage runs smoothly and efficiently.
This involves streamlining processes to reduce waste and improve speed.
Technological advancements such as automation can play a significant role in optimizing manufacturing stages.
Advantages of Well-Designed Manufacturing Stages
Implementing well-designed manufacturing stages offers numerous benefits.
These benefits extend beyond mere production efficiency to encompass broader business objectives.
Quality Improvement
Effective stages contribute to consistent product quality.
Regular inspections and checks during the stages ensure that defects are identified early.
This prevents defective products from proceeding to the next stage.
Cost-Efficiency
Properly designed stages can reduce overall production costs.
Efficient use of materials and resources minimizes waste.
Automation and optimized processes also cut down on labor costs and increase output.
Flexibility and Scalability
Well-thought-out manufacturing stages are adaptable.
They can be modified to accommodate changes in product design or production volume.
This flexibility is crucial for businesses looking to scale up operations or meet varying market demands.
Applications of Manufacturing Stages
Manufacturing stages find applications across various industries.
Their relevance spans from simple consumer goods to complex aerospace components.
Automotive Industry
In the automotive industry, manufacturing stages are pivotal.
Stages like welding, painting, and assembly are integral to car production.
The meticulous design of these stages ensures that vehicles are safe and reliable.
Electronics Manufacturing
Electronics manufacturing relies heavily on precise stages.
From circuit board production to final assembly, each stage requires a high degree of accuracy.
This is essential to ensure the functionality and durability of electronic devices.
Aerospace Industry
Aerospace manufacturing involves some of the most sophisticated stages.
The need for precision and reliability is paramount.
Stages in this industry include complex machining and rigorous testing protocols.
Consumer Goods
Even in consumer goods production, stages play a crucial role.
Whether it’s the assembly of furniture or the bottling of beverages, each stage ensures a high-quality end product.
These stages contribute to the consistency and dependability of everyday items.
Future Trends in Manufacturing Stages
The future of manufacturing stages looks promising with emerging trends and technologies poised to revolutionize the industry.
Automation and Robotics
The integration of automation and robotics is becoming increasingly prevalent.
These technologies can perform repetitive tasks with high precision.
They also improve safety and operational efficiency.
Artificial Intelligence
Artificial intelligence (AI) is finding its way into manufacturing stages.
AI can optimize processes by predicting maintenance needs and reducing downtime.
It also aids in real-time monitoring and quality control.
Sustainable Practices
Sustainability is becoming a key consideration in manufacturing.
Environmental regulations and consumer demand are driving the adoption of eco-friendly practices.
Stages are being redesigned to reduce waste and energy consumption.
Conclusion
The design and application of stages in manufacturing are fundamental to producing high-quality products.
Each stage, from material preparation to quality control, plays a vital role in transforming raw materials into finished goods.
Well-thought-out stages improve efficiency, assure product quality, and make for cost-effective production processes.
With advancements in technology and a growing emphasis on sustainability, the future of manufacturing stages holds tremendous potential.
資料ダウンロード
QCD調達購買管理クラウド「newji」は、調達購買部門で必要なQCD管理全てを備えた、現場特化型兼クラウド型の今世紀最高の購買管理システムとなります。
ユーザー登録
調達購買業務の効率化だけでなく、システムを導入することで、コスト削減や製品・資材のステータス可視化のほか、属人化していた購買情報の共有化による内部不正防止や統制にも役立ちます。
NEWJI DX
製造業に特化したデジタルトランスフォーメーション(DX)の実現を目指す請負開発型のコンサルティングサービスです。AI、iPaaS、および先端の技術を駆使して、製造プロセスの効率化、業務効率化、チームワーク強化、コスト削減、品質向上を実現します。このサービスは、製造業の課題を深く理解し、それに対する最適なデジタルソリューションを提供することで、企業が持続的な成長とイノベーションを達成できるようサポートします。
オンライン講座
製造業、主に購買・調達部門にお勤めの方々に向けた情報を配信しております。
新任の方やベテランの方、管理職を対象とした幅広いコンテンツをご用意しております。
お問い合わせ
コストダウンが利益に直結する術だと理解していても、なかなか前に進めることができない状況。そんな時は、newjiのコストダウン自動化機能で大きく利益貢献しよう!
(Β版非公開)