- お役立ち記事
- Manufacturing Innovation Techniques to Achieve Both Quality and Cost Productivity Improvement Measures Learned from Experts
Manufacturing Innovation Techniques to Achieve Both Quality and Cost Productivity Improvement Measures Learned from Experts
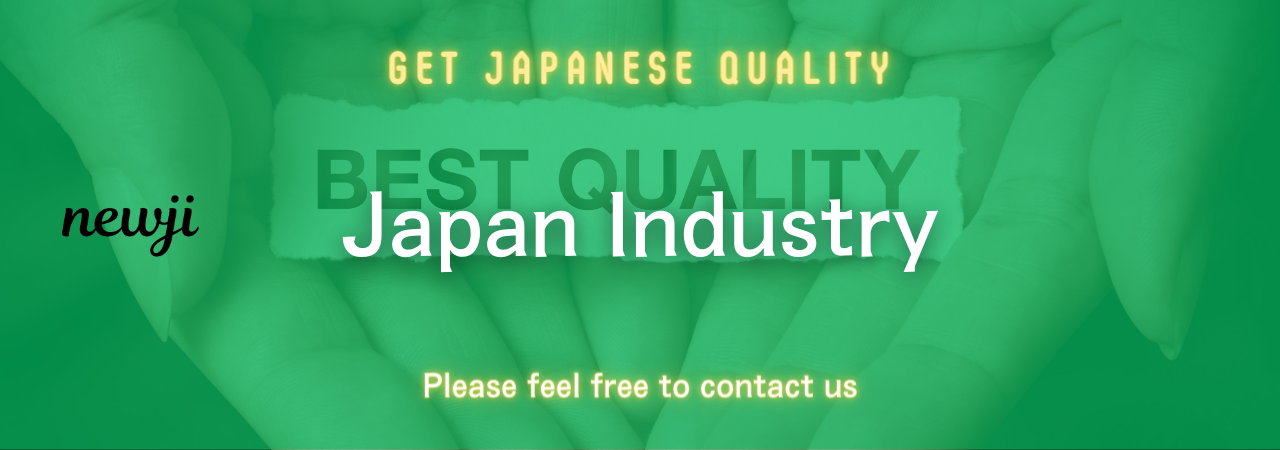
Manufacturing is an industry that continually evolves, driven by technological advancements and a competitive market.
To stay ahead, manufacturers must embrace innovation techniques that balance quality and cost productivity.
Quality and cost are often seen as conflicting goals, but with expert guidance, it’s possible to achieve both.
目次
Understanding the Need for Innovation
In today’s competitive marketplace, the demand for high-quality products at lower costs is ever-growing.
Companies that fail to innovate risk falling behind their competitors.
Innovation drives improvements across the board, from production methods to supply chain management.
Focusing on innovation doesn’t just mean investing in the latest technology.
It also involves rethinking processes, fostering a culture of continuous improvement, and strategically aligning business goals.
The Role of Technology in Manufacturing Innovation
Technology is a significant enabler of innovation within manufacturing.
Automation, artificial intelligence (AI), and the Internet of Things (IoT) are reshaping the industry.
These technologies provide manufacturers with new tools to enhance productivity and maintain high standards of quality.
Automation streamlines routine tasks, freeing human workers to focus on more complex activities.
AI can predict maintenance needs, reducing downtime and ensuring consistent production quality.
IoT devices offer real-time monitoring, allowing for immediate adjustments to optimize processes.
Implementing Lean Manufacturing Principles
Lean manufacturing principles aim to minimize waste without compromising quality.
By identifying and eliminating non-value-added activities, manufacturers can boost efficiency and reduce costs.
Value Stream Mapping
Value stream mapping is a lean tool that visually maps out all steps in a process, from raw material to finished product.
This tool helps identify areas where waste can be reduced and efficiency can be increased.
Kaizen
Kaizen, or continuous improvement, encourages small, incremental changes rather than large-scale transformations.
This approach involves all employees and fosters a culture of constant evaluation and improvement.
5S Methodology
The 5S methodology — Sort, Set in order, Shine, Standardize, and Sustain — provides a framework for organizing the workplace.
A clean, well-organized environment enhances productivity and helps maintain quality standards.
Enhancing Quality Management Systems
Quality management systems (QMS) are essential for ensuring that products meet or exceed customer expectations.
A robust QMS can prevent defects, reduce rework, and enhance customer satisfaction.
Statistical Process Control (SPC)
Statistical Process Control involves using statistical methods to monitor and control production processes.
By analyzing data, manufacturers can identify trends, detect issues early, and maintain high-quality standards.
Six Sigma
Six Sigma focuses on eliminating defects and improving process quality.
It uses a structured methodology, DMAIC (Define, Measure, Analyze, Improve, Control), to drive improvements.
Six Sigma aims for near perfection, with a goal of 3.4 defects per million opportunities.
Adopting Agile Manufacturing Techniques
Agile manufacturing emphasizes flexibility and rapid response to changes in demand.
This approach allows manufacturers to adapt quickly to market needs, enhancing both productivity and quality.
Modular Production Systems
Modular production systems involve creating standardized, interchangeable modules that can be quickly assembled and reconfigured.
This flexibility helps manufacturers respond efficiently to changes in production requirements or customer specifications.
Just-In-Time (JIT) Production
Just-In-Time production minimizes inventory costs by producing goods only as they are needed.
This approach reduces waste and ensures that resources are used efficiently.
Investing in Employee Training and Development
Employees play a vital role in the manufacturing process.
Providing ongoing training and development opportunities ensures that they have the skills and knowledge to contribute to innovation efforts.
Cross-Training
Cross-training involves teaching employees multiple skills so they can perform various roles.
This increases workforce flexibility and can lead to more efficient use of human resources.
Continuous Learning
Encouraging a culture of continuous learning ensures that employees stay up-to-date with the latest industry developments and technologies.
This makes the workforce more adaptable and capable of driving innovation.
Optimizing Supply Chain Management
An efficient supply chain is essential for maintaining cost productivity and quality.
Optimizing supply chain management involves improving coordination, reducing lead times, and minimizing disruptions.
Supplier Collaboration
Working closely with suppliers can lead to better quality materials, timely deliveries, and cost savings.
Strong relationships with suppliers foster trust and open communication, making it easier to address issues and implement improvements.
Integrating Technology
Technology integration, such as using enterprise resource planning (ERP) systems, can enhance supply chain visibility.
Real-time data provides insights into every stage of the supply chain, enabling better decision-making and reducing inefficiencies.
Measuring and Analyzing Performance
Continuous improvement requires regular measurement and analysis of performance.
Using metrics and key performance indicators (KPIs) helps manufacturers identify areas for improvement and track progress.
Defining Relevant Metrics
Manufacturers should identify metrics that align with their goals, such as production efficiency, defect rates, and customer satisfaction.
Relevant metrics provide meaningful insights into performance and highlight areas that need attention.
Regular Performance Reviews
Conducting regular performance reviews allows manufacturers to evaluate their progress and adjust strategies as needed.
These reviews should involve examining data, discussing challenges, and celebrating successes.
Achieving both quality and cost productivity in manufacturing is a challenging but attainable goal.
By adopting innovation techniques, leveraging technology, improving processes, investing in employees, and optimizing supply chains, manufacturers can drive significant improvements.
Continuous evaluation and commitment to improvement are key to maintaining a competitive edge in the evolving manufacturing landscape.
資料ダウンロード
QCD調達購買管理クラウド「newji」は、調達購買部門で必要なQCD管理全てを備えた、現場特化型兼クラウド型の今世紀最高の購買管理システムとなります。
ユーザー登録
調達購買業務の効率化だけでなく、システムを導入することで、コスト削減や製品・資材のステータス可視化のほか、属人化していた購買情報の共有化による内部不正防止や統制にも役立ちます。
NEWJI DX
製造業に特化したデジタルトランスフォーメーション(DX)の実現を目指す請負開発型のコンサルティングサービスです。AI、iPaaS、および先端の技術を駆使して、製造プロセスの効率化、業務効率化、チームワーク強化、コスト削減、品質向上を実現します。このサービスは、製造業の課題を深く理解し、それに対する最適なデジタルソリューションを提供することで、企業が持続的な成長とイノベーションを達成できるようサポートします。
オンライン講座
製造業、主に購買・調達部門にお勤めの方々に向けた情報を配信しております。
新任の方やベテランの方、管理職を対象とした幅広いコンテンツをご用意しております。
お問い合わせ
コストダウンが利益に直結する術だと理解していても、なかなか前に進めることができない状況。そんな時は、newjiのコストダウン自動化機能で大きく利益貢献しよう!
(Β版非公開)