- お役立ち記事
- DX in Wire-Cut Machining Combines High Precision with Unmanned Operation
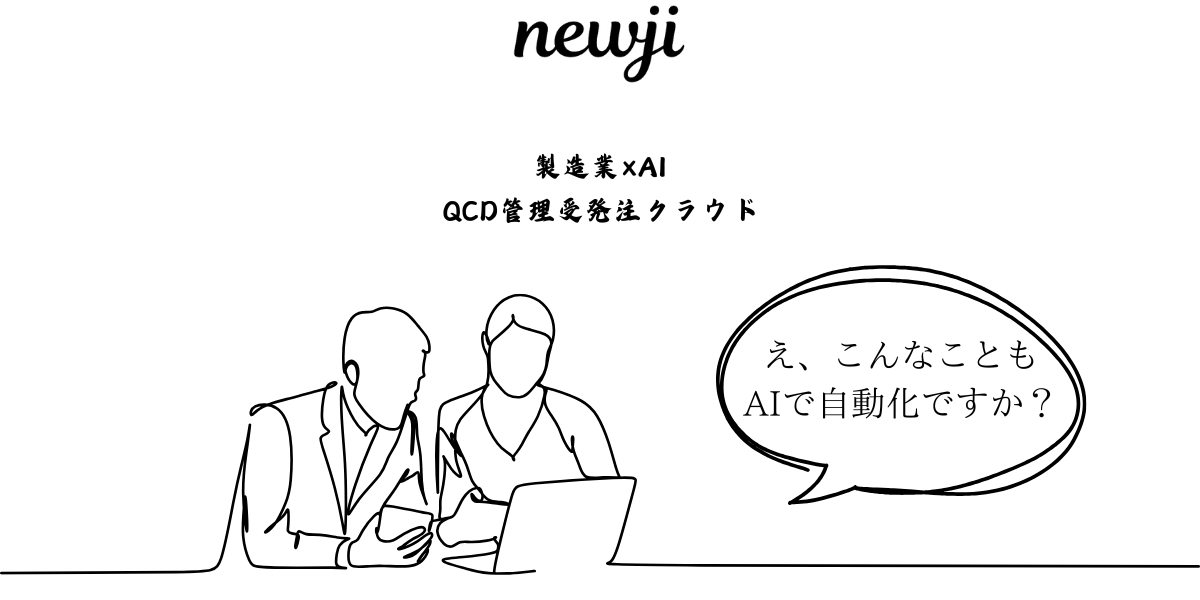
DX in Wire-Cut Machining Combines High Precision with Unmanned Operation
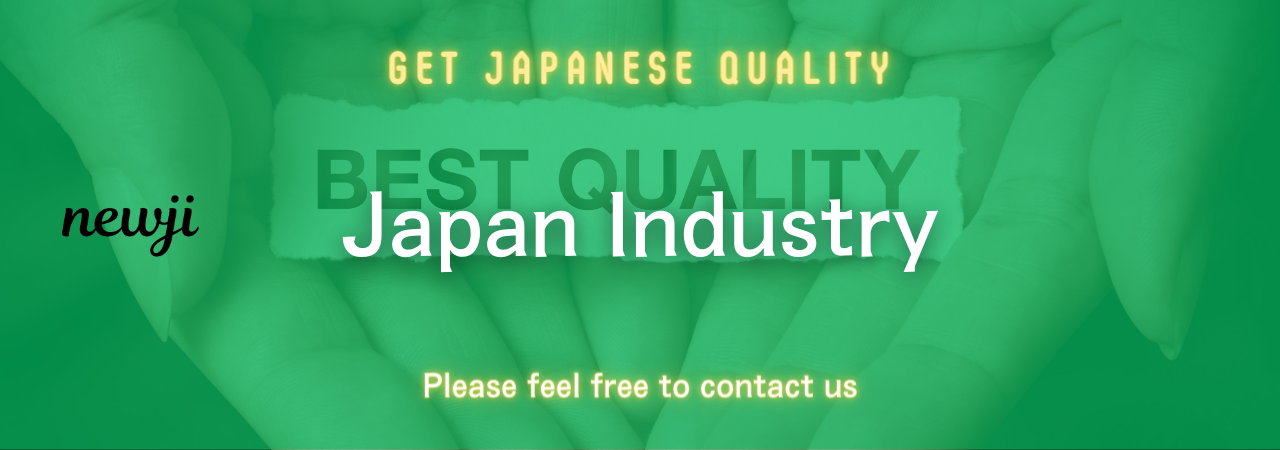
In the world of manufacturing, precision is key.
Wire-cut machining, also known as wire electrical discharge machining (EDM), is a technology that provides the high level of accuracy needed for intricate component manufacturing.
However, the integration of digital transformation (DX) into wire-cut machining is revolutionizing the field in unique ways.
Combining high precision with unmanned operation, DX is ushering in a new era for the industry.
目次
Understanding Wire-Cut Machining
Before diving into the impact of DX, it is essential to grasp the basics of wire-cut machining.
Wire-cut EDM uses a thin, electrically charged wire to cut intricate shapes from a piece of metal.
The process involves creating sparks between the wire and the workpiece, which melts away small amounts of material.
This allows for extremely precise cuts that are virtually impossible to achieve through traditional machining methods.
Wire-cut machining is particularly beneficial for creating complex molds, dies, and components used in industries such as aerospace, automotive, and medical device manufacturing.
The accuracy and tight tolerances that wire-cut EDM offers make it indispensable for these applications.
What is Digital Transformation (DX)?
Digital transformation, or DX, involves the integration of digital technology into all areas of a business.
It profoundly changes how businesses operate and deliver value to customers.
By incorporating advanced technologies like artificial intelligence (AI), big data, and the Internet of Things (IoT), DX optimizes processes and enhances productivity.
In manufacturing, DX can significantly improve efficiency, reduce errors, and streamline operations.
The Role of DX in Wire-Cut Machining
Integrating DX into wire-cut machining offers numerous advantages.
One of the most significant benefits is the ability to enable unmanned or automated operations.
Here’s how DX influences wire-cut machining in various aspects:
1. Enhanced Precision and Accuracy
Precision is a hallmark of wire-cut machining.
By leveraging DX, manufacturers can achieve even higher accuracy levels.
Advanced sensors and real-time data analytics constantly monitor the machining process.
These technologies provide immediate feedback, allowing adjustments to be made on the fly.
As a result, there is a substantial reduction in deviations and errors.
2. Unmanned Operations and Increased Efficiency
DX facilitates the automation of wire-cut machining, making unmanned operations possible.
Automated systems can operate continuously, significantly increasing productivity and efficiency.
Machine learning algorithms predict when maintenance is needed, reducing downtime and extending machine lifespan.
With an automated setup, manufacturers can produce more parts in less time while maintaining high standards of quality.
3. Remote Monitoring and Control
One of the most remarkable advantages of integrating DX into wire-cut machining is the ability to monitor and control operations remotely.
Via IoT-enabled devices, operators can access real-time data and make adjustments from anywhere.
This flexibility ensures that machines are always performing optimally, reducing the need for on-site supervision.
4. Data-Driven Decision Making
Data analytics plays a pivotal role in digital transformation.
In wire-cut machining, collected data can provide insights into the performance of machines and processes.
Historical data analysis helps identify trends and predict future outcomes.
This information is invaluable for making informed decisions, optimizing machining processes, and improving overall productivity.
5. Precision in Complex Geometries
Wire-cut machining already excels in producing complex geometries.
However, DX takes this capability a step further by incorporating CAD/CAM (Computer-Aided Design/Computer-Aided Manufacturing) technologies.
Operators can create and simulate intricate designs on a computer before actual production.
This minimizes the risk of errors and ensures that the final product matches the intended specifications.
Challenges and Considerations
While the integration of DX into wire-cut machining brings numerous benefits, there are challenges to consider.
Implementing digital transformation requires a significant investment in technology and training.
Manufacturers must be willing to adopt new methodologies and continuously update their technological infrastructure.
Additionally, ensuring data security is crucial.
As wire-cut machines become interconnected through IoT, there is an increased risk of cyber threats.
Protecting sensitive information and maintaining system integrity are essential components of successful DX integration.
The Future of Wire-Cut Machining
As digital transformation continues to evolve, the future of wire-cut machining looks promising.
Ongoing advancements in AI, machine learning, and IoT will further enhance the capabilities of wire-cut machines.
These technologies will become more accessible, allowing even small manufacturers to benefit from the advantages of DX.
Moreover, as the demand for precision components in industries like aerospace, medical, and electronics grows, wire-cut machining will remain a vital technology.
By embracing digital transformation, manufacturers can stay competitive, meet stringent industry standards, and deliver superior products to their customers.
Conclusion
The intersection of digital transformation and wire-cut machining is transforming the manufacturing landscape.
By combining high precision with unmanned operation, DX offers unparalleled advantages in terms of accuracy, efficiency, and productivity.
As technology continues to advance, the potential for wire-cut machining will only expand, setting new benchmarks in the industry.
資料ダウンロード
QCD調達購買管理クラウド「newji」は、調達購買部門で必要なQCD管理全てを備えた、現場特化型兼クラウド型の今世紀最高の購買管理システムとなります。
ユーザー登録
調達購買業務の効率化だけでなく、システムを導入することで、コスト削減や製品・資材のステータス可視化のほか、属人化していた購買情報の共有化による内部不正防止や統制にも役立ちます。
NEWJI DX
製造業に特化したデジタルトランスフォーメーション(DX)の実現を目指す請負開発型のコンサルティングサービスです。AI、iPaaS、および先端の技術を駆使して、製造プロセスの効率化、業務効率化、チームワーク強化、コスト削減、品質向上を実現します。このサービスは、製造業の課題を深く理解し、それに対する最適なデジタルソリューションを提供することで、企業が持続的な成長とイノベーションを達成できるようサポートします。
オンライン講座
製造業、主に購買・調達部門にお勤めの方々に向けた情報を配信しております。
新任の方やベテランの方、管理職を対象とした幅広いコンテンツをご用意しております。
お問い合わせ
コストダウンが利益に直結する術だと理解していても、なかなか前に進めることができない状況。そんな時は、newjiのコストダウン自動化機能で大きく利益貢献しよう!
(Β版非公開)