- お役立ち記事
- Connector Selection and Uses in OEM Manufacturing
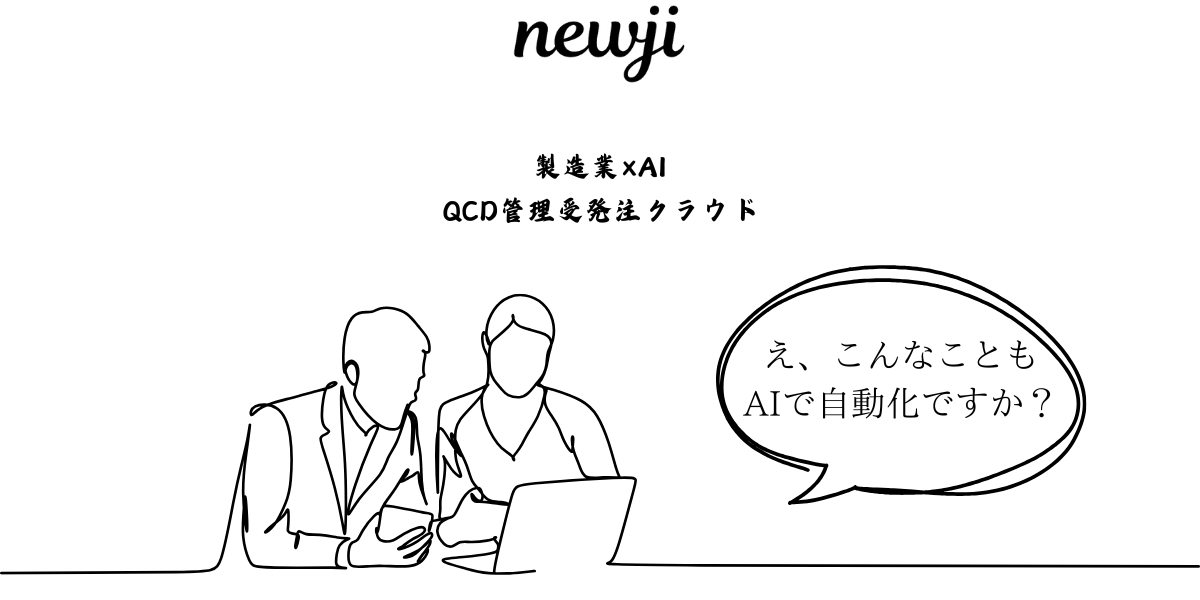
Connector Selection and Uses in OEM Manufacturing
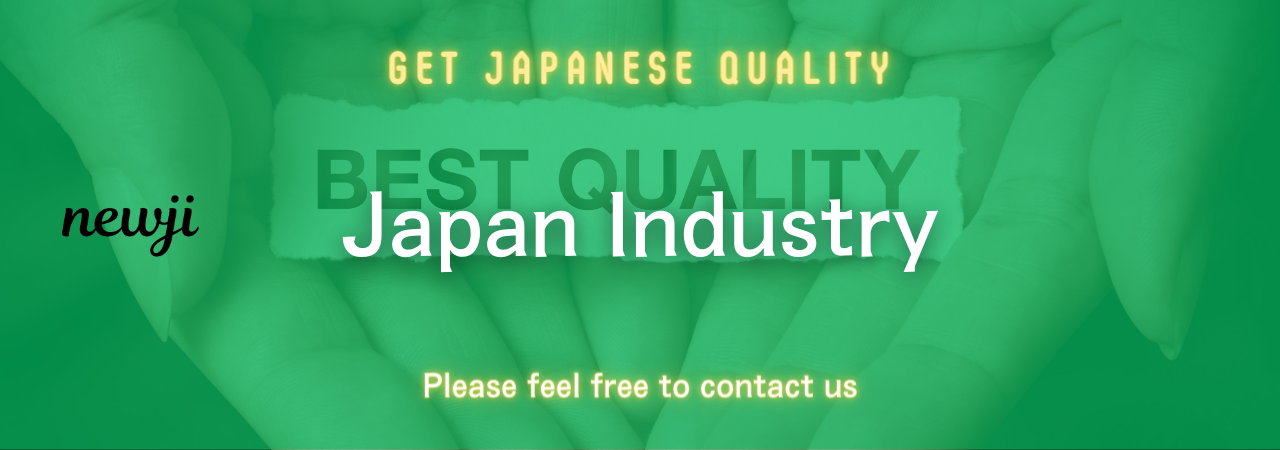
When it comes to Original Equipment Manufacturer (OEM) manufacturing, connectors play a crucial role in ensuring that the products perform as expected.
Connectors are essential components that link circuits together, facilitating the flow of electricity and signals.
Choosing the right connector can significantly impact the efficiency, reliability, and safety of the final product.
In this article, we’ll explore different types of connectors, their applications, and tips for selecting the appropriate connector for OEM manufacturing.
目次
Understanding Connectors
Connectors are devices used to join electrical circuits together.
Their primary function is to establish a temporary connection that can be removed and reconnected as needed.
Connectors come in various sizes, shapes, and functionalities, adapting to a wide range of applications from consumer electronics to industrial machinery.
Picking the right connector can simplify assembly, enhance product durability, and improve performance.
Types of Connectors
There are several types of connectors commonly used in OEM manufacturing, each suited for specific tasks and environments.
Here are a few of the most popular ones:
1. PCB Connectors
Printed Circuit Board (PCB) connectors are used to connect wires and components to the PCB.
They come in different forms such as board-to-board, cable-to-board, or wire-to-board connectors.
These connectors are beneficial for their compact size and ease of use in electronics like computers and smartphones.
2. Wire-to-Wire Connectors
These connectors are designed to link two wires together.
They are commonly used in automotive applications and other areas where the electrical connection needs to withstand conditions such as vibrations and heat.
These connectors provide a secure and stable connection, essential for safety.
3. Coaxial Connectors
Coaxial connectors are used in applications requiring high-frequency signal transmissions, like TV antennas, internet modems, and radio communications.
They are designed to protect against signal loss and external interference, ensuring that the signal remains strong and clear.
4. RFID Connectors
Radio Frequency Identification (RFID) connectors are used in systems for tracking and identification, such as inventory management, access control, and toll collection.
These connectors are crucial for linking RFID tags to the reader and ensuring data is accurately transmitted.
5. Fiber Optic Connectors
Fiber optic connectors are designed for transmitting light signals through optical fibers.
They are widely used in telecommunication networks and data centers due to their high-speed data transmission capability and low signal loss.
These connectors ensure robust and efficient data communication over long distances.
Factors to Consider When Selecting Connectors
Choosing the right connector for OEM manufacturing involves several considerations.
Here are some key factors to keep in mind:
Electrical Requirements
The connector must meet the specific electrical requirements of the application, such as voltage, current, and signal type.
It’s crucial to ensure that the connector can handle the electrical specifications without causing any interference or signal loss.
Environmental Conditions
The operating environment significantly influences the choice of connector.
Factors such as temperature, humidity, and potential exposure to elements like dust or water should be considered.
Selecting a connector with the appropriate sealing and materials can prolong the product’s lifespan and enhance its reliability.
Mechanical Properties
Mechanical properties such as insertion and extraction forces, durability, and mating cycles are important.
The connector should be easy to connect and disconnect, yet secure enough to prevent accidental disconnection.
Durability is especially vital for products that undergo frequent use or harsh conditions.
Size and Form Factor
Connectors come in various sizes and shapes, and the appropriate size and form factor depend on the application’s requirements.
For compact devices, a smaller connector might be necessary to save space.
On the other hand, industrial applications may require larger and more robust connectors.
Compliance and Standards
Ensure that the chosen connector complies with relevant industry standards and regulations.
Compliance ensures that the connector meets safety and performance criteria, reducing the risk of failures and enhancing the product’s marketability.
Cost
Lastly, cost is an important consideration in OEM manufacturing.
While it’s tempting to opt for the least expensive option, balancing cost with quality and reliability is crucial.
A cheaper connector may save money in the short term but could lead to failures and additional expenses in the long run.
Applications of Connectors in OEM Manufacturing
Connectors are used in a vast range of applications across different industries.
Here’s how they are utilized in some common sectors:
Consumer Electronics
In consumer electronics, connectors are used in devices like smartphones, laptops, and home appliances.
Their role is to ensure seamless connections between various components, affecting the overall performance and user experience.
Automotive
The automotive industry relies heavily on connectors to link different electrical systems within a vehicle.
Connectors in automobiles must withstand challenging conditions such as high temperatures, vibrations, and exposure to fluids.
Telecommunications
In telecommunications, connectors are vital for ensuring high-speed data transfer and robust network connections.
Fiber optic and coaxial connectors are commonly used to maintain signal integrity over long distances, crucial for internet and communication services.
Medical Devices
Medical devices require reliable and precise connectors to ensure the accuracy and safety of medical procedures.
Connectors in this sector must adhere to stringent standards and regulations to guarantee patient safety and device efficacy.
Industrial Equipment
Industrial machinery uses connectors for power distribution, signal transmission, and control systems.
These connectors must be robust and durable to handle the demanding conditions of industrial environments.
Conclusion
Selecting the right connector for OEM manufacturing is a critical decision that affects the product’s performance, safety, and reliability.
Understanding the types of connectors available—such as PCB, wire-to-wire, coaxial, RFID, and fiber optic connectors—helps in making an informed choice.
Considering factors like electrical requirements, environmental conditions, mechanical properties, size, compliance, and cost will ensure the chosen connector meets the application’s demands.
By carefully selecting the appropriate connectors, OEM manufacturers can enhance their products’ quality and reliability, ensuring customer satisfaction and long-term success.
資料ダウンロード
QCD調達購買管理クラウド「newji」は、調達購買部門で必要なQCD管理全てを備えた、現場特化型兼クラウド型の今世紀最高の購買管理システムとなります。
ユーザー登録
調達購買業務の効率化だけでなく、システムを導入することで、コスト削減や製品・資材のステータス可視化のほか、属人化していた購買情報の共有化による内部不正防止や統制にも役立ちます。
NEWJI DX
製造業に特化したデジタルトランスフォーメーション(DX)の実現を目指す請負開発型のコンサルティングサービスです。AI、iPaaS、および先端の技術を駆使して、製造プロセスの効率化、業務効率化、チームワーク強化、コスト削減、品質向上を実現します。このサービスは、製造業の課題を深く理解し、それに対する最適なデジタルソリューションを提供することで、企業が持続的な成長とイノベーションを達成できるようサポートします。
オンライン講座
製造業、主に購買・調達部門にお勤めの方々に向けた情報を配信しております。
新任の方やベテランの方、管理職を対象とした幅広いコンテンツをご用意しております。
お問い合わせ
コストダウンが利益に直結する術だと理解していても、なかなか前に進めることができない状況。そんな時は、newjiのコストダウン自動化機能で大きく利益貢献しよう!
(Β版非公開)