- お役立ち記事
- Optimization of Intake Manifold Design and Manufacturing Technologies
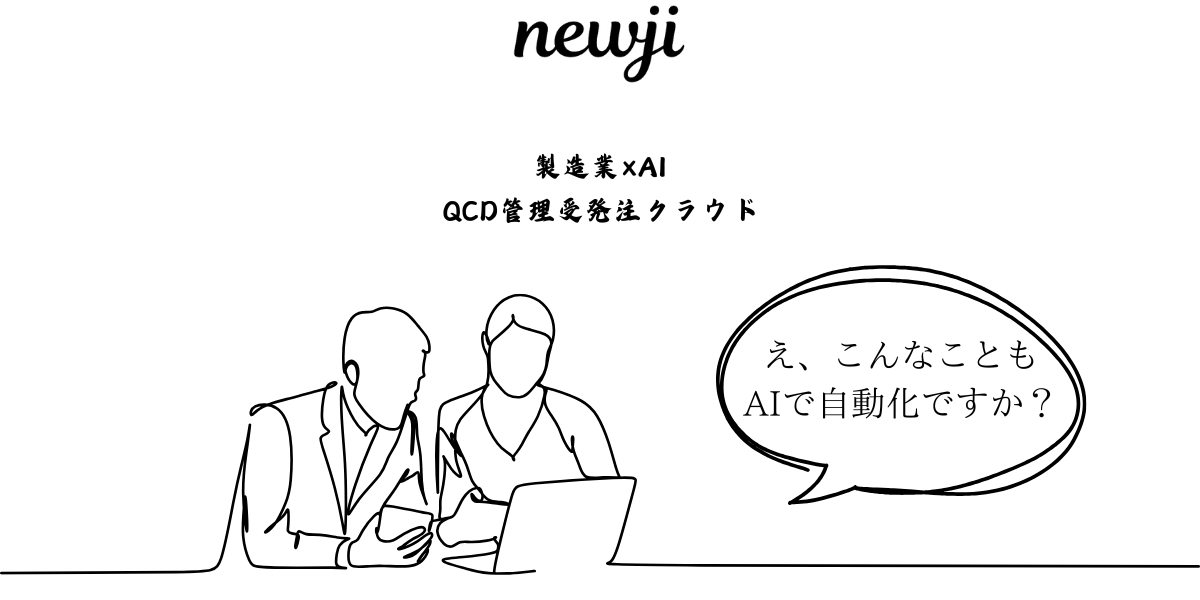
Optimization of Intake Manifold Design and Manufacturing Technologies
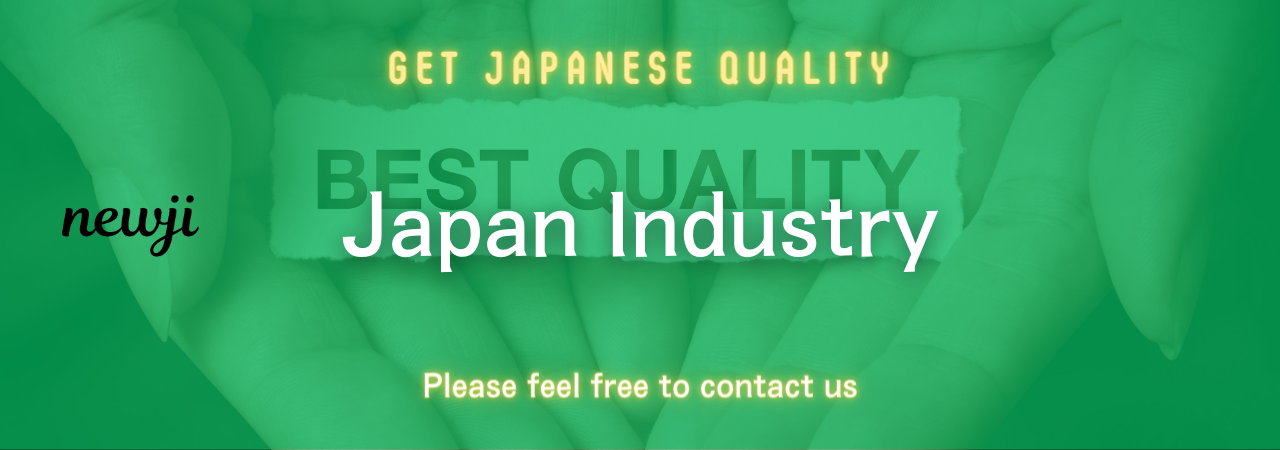
The intake manifold is an essential component in an internal combustion engine.
It ensures the proper delivery of air to the engine cylinders, contributing significantly to an engine’s efficiency and performance.
As technology advances, optimizing the design and manufacturing of intake manifolds has become increasingly important.
In this article, we will explore the various aspects of intake manifold design and the technologies that enhance their manufacturing.
目次
Understanding Intake Manifold Design
The primary function of an intake manifold is to distribute the air-fuel mixture uniformly to the cylinders.
A well-designed intake manifold can have a profound impact on an engine’s power output and fuel efficiency.
There are several critical considerations when designing an intake manifold.
Airflow Efficiency
Maximizing airflow efficiency is crucial for optimizing performance.
Engineers focus on minimizing resistance and maximization of the flow rate.
The shape, size, and length of the intake runners, which are the pathways in the manifold, play a significant role in determining airflow efficiency.
Straight and smooth runners create less turbulence and facilitate better air distribution.
Material Selection
Choosing the right material for an intake manifold can affect durability, weight, and thermal characteristics.
Traditionally, manifolds were made from cast iron or aluminum.
However, modern engines often use composite materials that are lighter and exhibit superior heat resistance.
These materials reduce the overall weight of the engine, contributing to better fuel economy.
Variable Geometry
To adapt to different engine speeds and loads, some intake manifolds feature variable geometry designs.
This means that the length or cross-sectional area of the intake runners can be altered depending on the performance requirements.
At lower speeds, longer runners can help improve torque, whereas shorter runners can enhance airflow at higher speeds.
Advanced Manufacturing Technologies
Innovation in manufacturing technologies has enabled more precise and efficient production of intake manifolds.
These advanced techniques help engineers achieve optimal designs that were previously unattainable.
3D Printing
Additive manufacturing, commonly known as 3D printing, allows for rapid prototyping and the creation of complex geometries that are difficult to achieve through traditional methods.
3D printing also enables the customization of intake manifolds for specific engines, improving performance and efficiency.
Additionally, 3D-printed manifolds can reduce waste material, making the process more sustainable.
Die Casting
For large-scale production, die casting is a popular method used to manufacture intake manifolds.
This process involves injecting molten metal into a mold under high pressure, ensuring consistent quality and accuracy.
Modern die casting techniques have improved, allowing for the production of lighter and more robust components.
Computer-Aided Design (CAD) and Simulation
Modern intake manifold design heavily relies on CAD software and simulation tools.
Engineers can create detailed models of intake manifolds and test different designs virtually.
Simulation tools can predict how changes in design will affect airflow, temperature distribution, and overall engine performance.
This virtual testing helps engineers fine-tune designs before creating physical prototypes, reducing development time and costs.
Case Studies and Real-World Applications
To illustrate the impact of optimized intake manifold design and manufacturing technologies, let’s examine a few real-world examples.
These case studies highlight how advancements have led to significant improvements in engine performance.
Automotive Industry
In the automotive industry, manufacturers are constantly striving to improve engine efficiency and performance.
One noteworthy example is the development of variable intake manifolds for high-performance sports cars.
By employing a variable geometry design, these intake manifolds optimize airflow at different engine speeds, resulting in better acceleration and fuel economy.
Manufacturing such manifolds using 3D printing has also enabled the production of lightweight and customized components, thereby enhancing overall vehicle performance.
Motorsports
In the world of motorsports, every fraction of a second counts.
Racing teams invest heavily in optimizing engine components, including intake manifolds.
Using advanced simulation tools, engineers can design intake manifolds that maximize airflow and offer superior power output.
3D printing technology allows for rapid iterations and testing of different designs, ensuring that the best possible configuration is used during races.
Industrial Engines
Industrial engines, such as those used in power generation and heavy machinery, also benefit from optimized intake manifold designs.
Improved airflow efficiency leads to better fuel combustion, resulting in lower emissions and higher energy output.
Modern manufacturing technologies enable the production of highly efficient intake manifolds that can withstand harsh operating conditions, prolonging the engine’s lifespan and reducing maintenance costs.
Future Trends and Considerations
As technology continues to evolve, the optimization of intake manifold design and manufacturing will advance further.
Several trends are likely to shape the future of this field.
Integration of Smart Technologies
The integration of smart technologies, such as sensors and actuators, into intake manifolds can provide real-time data on airflow, temperature, and pressure.
This information can be used to make dynamic adjustments to the manifold, optimizing performance under varying conditions.
Smart intake manifolds could play a critical role in developing more efficient and responsive engines.
Sustainability Initiatives
As the automotive industry pushes towards more sustainable practices, the use of eco-friendly materials and manufacturing methods will become more prevalent.
Composite materials derived from renewable sources and recycling techniques can reduce the environmental impact of production.
Additionally, optimizing intake manifold designs for improved fuel efficiency contributes to lower emissions.
Collaboration and Interdisciplinary Approaches
Collaboration between engineers, material scientists, and data analysts will be key to unlocking new innovations in intake manifold design.
By combining expertise from different fields, more integrated and effective solutions can be developed.
Cross-industry collaboration can also lead to the transfer of successful technologies from one sector to another, accelerating advancements.
Conclusion
The optimization of intake manifold design and manufacturing technologies is a crucial area of focus for improving engine performance and efficiency.
Advancements in material selection, manufacturing techniques, and smart technologies have paved the way for innovative designs that were once considered impossible.
As we continue to explore new frontiers in this field, the future promises even greater strides in creating more powerful, efficient, and sustainable engines.
資料ダウンロード
QCD調達購買管理クラウド「newji」は、調達購買部門で必要なQCD管理全てを備えた、現場特化型兼クラウド型の今世紀最高の購買管理システムとなります。
ユーザー登録
調達購買業務の効率化だけでなく、システムを導入することで、コスト削減や製品・資材のステータス可視化のほか、属人化していた購買情報の共有化による内部不正防止や統制にも役立ちます。
NEWJI DX
製造業に特化したデジタルトランスフォーメーション(DX)の実現を目指す請負開発型のコンサルティングサービスです。AI、iPaaS、および先端の技術を駆使して、製造プロセスの効率化、業務効率化、チームワーク強化、コスト削減、品質向上を実現します。このサービスは、製造業の課題を深く理解し、それに対する最適なデジタルソリューションを提供することで、企業が持続的な成長とイノベーションを達成できるようサポートします。
オンライン講座
製造業、主に購買・調達部門にお勤めの方々に向けた情報を配信しております。
新任の方やベテランの方、管理職を対象とした幅広いコンテンツをご用意しております。
お問い合わせ
コストダウンが利益に直結する術だと理解していても、なかなか前に進めることができない状況。そんな時は、newjiのコストダウン自動化機能で大きく利益貢献しよう!
(Β版非公開)