- お役立ち記事
- Importance and Practice of Preventive/Corrective Action: Quality Problem Solving and Process Improvement Techniques
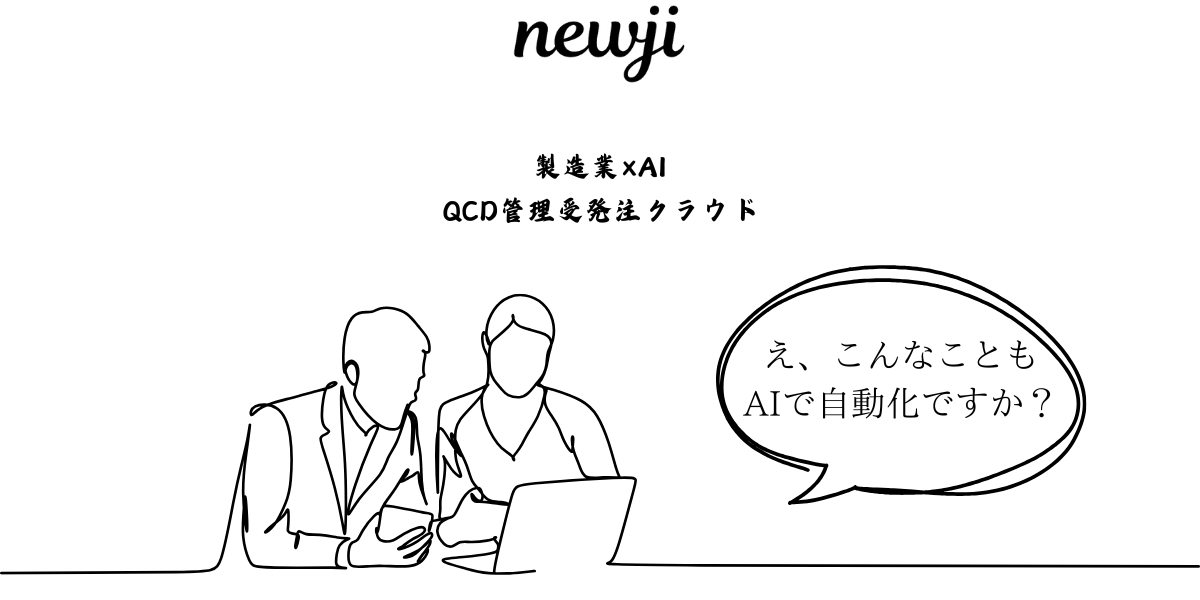
Importance and Practice of Preventive/Corrective Action: Quality Problem Solving and Process Improvement Techniques
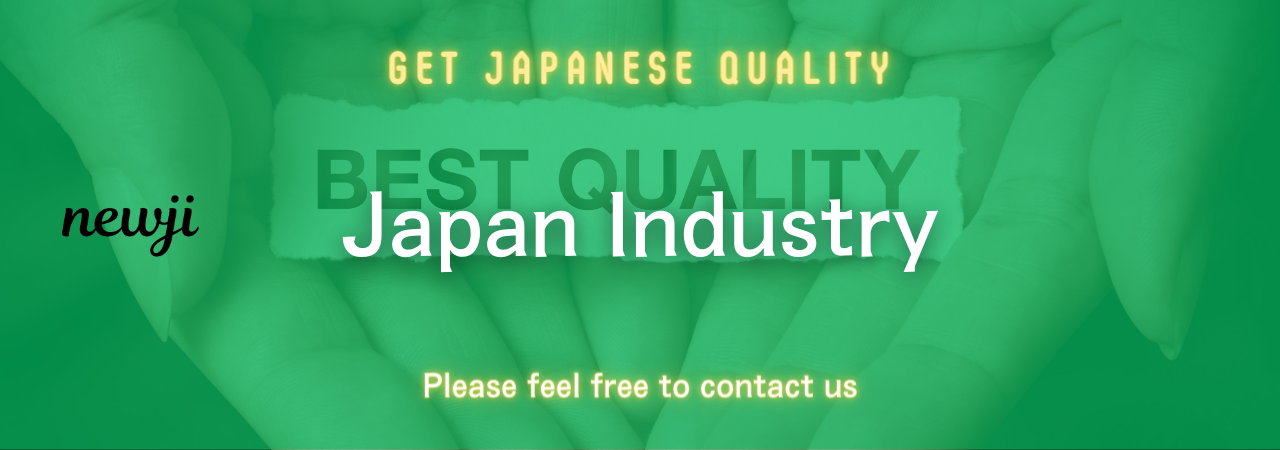
Quality is crucial in any business or manufacturing process, and maintaining it requires attention to detail and proactive measures.
One way to ensure high standards are met is through preventive and corrective actions.
These actions involve identifying potential problems before they occur and addressing existing issues efficiently.
Understanding and implementing these techniques can significantly improve your process and problem-solving abilities.
目次
What is Preventive Action?
Preventive action refers to the measures taken to avoid potential nonconformities or issues before they happen.
It’s about foreseeing possible troubles and taking steps to avert them.
This proactive approach helps in maintaining quality and efficiency in processes.
Benefits of Preventive Action
Firstly, preventive action helps in saving time and money.
By addressing potential issues early, you minimize the risk of larger, more costly problems down the line.
It also enhances customer satisfaction, ensuring that products or services meet or exceed expectations consistently.
Examples of Preventive Action
An example of preventive action could be regular maintenance checks of machinery in a manufacturing plant.
It ensures that equipment is functioning correctly and can prevent breakdowns that might disrupt production.
Another example is training employees adequately.
Well-trained staff are less likely to make mistakes, thereby reducing the chances of defects.
What is Corrective Action?
Corrective action, on the other hand, deals with problems that have already occurred.
It involves identifying the root cause of an issue and implementing a solution to prevent its recurrence.
Corrective actions are essential for continuous improvement and long-term success.
Benefits of Corrective Action
Corrective actions are vital for addressing customer complaints and nonconformities.
This approach helps regain customer trust and ensures that similar problems do not arise in the future.
It also contributes to better process management and enhances overall quality.
Examples of Corrective Action
Suppose there’s a recurring defect in a product due to a fault in the production process.
A corrective action would involve thoroughly investigating the issue, identifying the root cause, and adjusting the process to eliminate the defect.
Another example is addressing customer feedback.
If a customer points out an area for improvement, taking corrective action shows that their opinion is valued and that the business is committed to quality.
Steps to Implement Preventive and Corrective Actions
Implementing these actions involves a systematic approach.
Step 1: Identify Potential and Existing Issues
Start by identifying potential problems or current issues in your processes.
This can be done through regular audits, inspections, and feedback from customers and employees.
Step 2: Analyze the Root Cause
Once an issue is identified, delve into its root cause.
Ask questions like “Why did this happen?” and “What can we do to prevent it?”
Root cause analysis is crucial for both preventive and corrective actions.
Step 3: Plan and Implement Actions
For preventive action, develop a plan to address potential issues.
For corrective action, create a strategy to resolve the existing problem and prevent recurrence.
Implement these plans efficiently and monitor their effectiveness.
Step 4: Monitor and Review
Continually monitor the processes to ensure the actions are effective.
Conduct regular reviews and update the plans as necessary to adapt to new challenges.
The Role of Documentation
Documenting preventive and corrective actions is vital for several reasons.
It helps in tracking the progress, provides a reference for future issues, and ensures transparency within the organization.
Creating Effective Documentation
Ensure that the documentation includes details of the identified issues, the root cause analysis, the planned actions, and the results after implementation.
This comprehensive record will be invaluable for continuous improvement.
Engaging the Team
Quality problem-solving and process improvement are not tasks for a single person.
Engaging your team is crucial for the successful implementation of preventive and corrective actions.
Communication and Training
Communicate the importance of these actions to your team.
Ensure they are well-trained and understand their roles in maintaining and improving quality.
Regular training sessions and meetings can help keep everyone on the same page.
Utilizing Technology
In today’s digital age, technology plays a significant role in quality management.
Leveraging technology can streamline the process of implementing preventive and corrective actions.
Software Solutions
Quality management software can help in tracking issues, documenting actions, and analyzing data.
These tools provide an organized and efficient way to manage preventive and corrective measures.
Conclusion
Preventive and corrective actions are integral to maintaining and improving quality in any process.
By identifying potential and existing issues, analyzing their root causes, and implementing effective measures, you can ensure high standards consistently.
Documenting these actions, engaging your team, and utilizing technology further enhance the efficiency and effectiveness of these techniques.
Ultimately, a proactive approach to quality management fosters a culture of continuous improvement and customer satisfaction.
By adopting preventive and corrective actions, businesses can avoid costly disruptions, minimize defects, and build a reputation for reliability and excellence.
資料ダウンロード
QCD調達購買管理クラウド「newji」は、調達購買部門で必要なQCD管理全てを備えた、現場特化型兼クラウド型の今世紀最高の購買管理システムとなります。
ユーザー登録
調達購買業務の効率化だけでなく、システムを導入することで、コスト削減や製品・資材のステータス可視化のほか、属人化していた購買情報の共有化による内部不正防止や統制にも役立ちます。
NEWJI DX
製造業に特化したデジタルトランスフォーメーション(DX)の実現を目指す請負開発型のコンサルティングサービスです。AI、iPaaS、および先端の技術を駆使して、製造プロセスの効率化、業務効率化、チームワーク強化、コスト削減、品質向上を実現します。このサービスは、製造業の課題を深く理解し、それに対する最適なデジタルソリューションを提供することで、企業が持続的な成長とイノベーションを達成できるようサポートします。
オンライン講座
製造業、主に購買・調達部門にお勤めの方々に向けた情報を配信しております。
新任の方やベテランの方、管理職を対象とした幅広いコンテンツをご用意しております。
お問い合わせ
コストダウンが利益に直結する術だと理解していても、なかなか前に進めることができない状況。そんな時は、newjiのコストダウン自動化機能で大きく利益貢献しよう!
(Β版非公開)