- お役立ち記事
- Technology and Applications of DC Motors in Manufacturing
Technology and Applications of DC Motors in Manufacturing
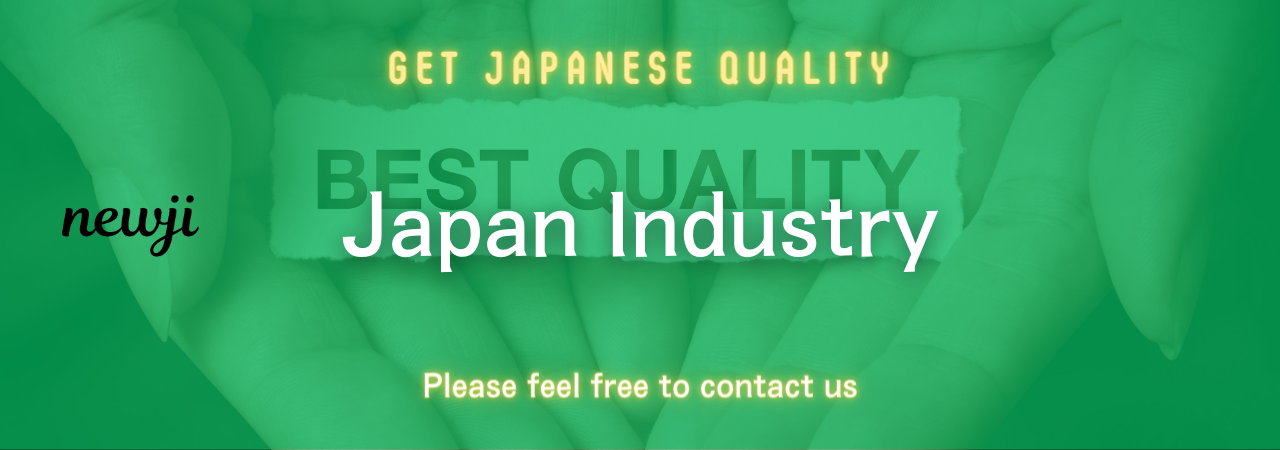
目次
Understanding DC Motors
DC motors, or direct current motors, are critical components in many manufacturing applications.
These motors convert direct electrical energy into mechanical energy, facilitating efficient and controllable motion.
By understanding the basics of DC motors, their applications, and their advantages, you can appreciate their role in modern manufacturing.
Components of DC Motors
At the heart of any DC motor, there are several key components that work together to create motion.
These include the rotor, stator, armature, commutator, and brushes.
Rotor
The rotor, sometimes called the armature, is the rotating part of the motor.
It carries the conductors that interact with the magnetic field to produce motion.
Stator
The stator is the stationary part of the motor that provides the magnetic field.
This field interacts with the rotor to generate a torque that rotates the rotor.
Armature
The armature consists of coils of wire wound around a core.
When current flows through these coils, it creates an electromagnetic force that results in rotation.
Commutator and Brushes
The commutator and brushes ensure that the current direction through the armature coils is always in the right direction to produce continuous rotation.
The commutator is a segmented ring attached to the rotor, while the brushes are static carbon components that maintain contact with the commutator segments.
Types of DC Motors
DC motors come in several types, each suitable for different applications based on their specific characteristics.
The three main types are series DC motors, shunt DC motors, and compound DC motors.
Series DC Motors
In series DC motors, the field windings are connected in series with the armature.
These motors provide high starting torque and are ideal for applications requiring large loads at startup, such as cranes and elevators.
Shunt DC Motors
Shunt DC motors have the field windings connected in parallel (or shunt) with the armature.
They offer better speed regulation and are suitable for applications where precise speed control is essential, like conveyor belts and machine tools.
Compound DC Motors
Compound DC motors incorporate both series and shunt winding configurations.
This hybrid design combines the high starting torque of series motors with the stable speed characteristics of shunt motors, making them versatile for various manufacturing processes.
Applications in Manufacturing
The diverse types of DC motors make them indispensable in the manufacturing industry.
Their specific characteristics cater to different requirements, boosting efficiency and performance across various applications.
Automated Production Lines
Automated production lines rely heavily on DC motors for precise and repeatable motion control.
They regulate the speed and torque of conveyor belts and robotic arms, ensuring seamless operation.
Consistent performance is vital for maintaining production speeds and product quality.
Material Handling Equipment
DC motors power various material handling equipment like forklifts, conveyors, and hoists.
Their ability to provide high starting torque ensures that heavy loads can be moved efficiently and safely.
Moreover, their robust performance helps in minimizing downtime, crucial for maintaining production schedules.
Precision Tools
In precision tools, DC motors offer excellent controllability.
Their fine speed regulation capabilities make them perfect for applications requiring high accuracy, such as lathes and milling machines.
These motors ensure that precision tools operate smoothly, delivering the necessary detail and accuracy.
Advantages of DC Motors in Manufacturing
DC motors bring several advantages to manufacturing, making them preferable in many applications.
Their benefits include high starting torque, excellent speed control, and simple design.
High Starting Torque
One of the standout features of DC motors is their high starting torque.
This capability is particularly beneficial in applications that require a significant initial force to start, making these motors ideal for heavy-lifting equipment and other demanding tasks in manufacturing.
Excellent Speed Control
DC motors offer precise speed control, which can be critical in manufacturing processes requiring consistent and adjustable speeds.
By adjusting the voltage applied to the motor, operators can finely regulate the speed, ensuring detailed and precise operation.
Simple Design
The straightforward design of DC motors contributes to their reliability and ease of maintenance.
Their construction allows for simple adjustments and repairs, making them convenient for manufacturing environments where machine uptime is vital.
Recent Innovations and Future Trends
Manufacturing technologies continue to evolve, driving innovations in DC motor design and application.
These advances are leading to more efficient, versatile, and reliable motors.
Brushless DC Motors
One significant innovation is the development of brushless DC motors.
These motors replace the traditional brushes and commutator with electronic control systems, reducing wear and increasing lifespan.
Brushless designs also enhance efficiency and performance, catering to more demanding precision applications.
Integration with IoT
The integration of DC motors with the Internet of Things (IoT) is another exciting trend.
By connecting motors to IoT networks, manufacturers can monitor performance in real-time, predict maintenance needs, and optimize operations.
This connectivity ensures higher efficiency and reduced downtime through proactive maintenance strategies.
Energy Efficiency
Innovations are also focusing on making DC motors more energy-efficient.
New materials, advanced designs, and improved control systems contribute to lower energy consumption, reducing operational costs and supporting sustainability initiatives.
Conclusion
DC motors play a crucial role in modern manufacturing.
Their versatility, high starting torque, excellent speed control, and simple design make them ideal for a wide range of applications.
Ongoing innovations continue to enhance their performance, making them even more valuable in the evolving manufacturing landscape.
Understanding these motors and their applications helps manufacturers leverage their full potential, driving productivity and efficiency in their operations.
資料ダウンロード
QCD調達購買管理クラウド「newji」は、調達購買部門で必要なQCD管理全てを備えた、現場特化型兼クラウド型の今世紀最高の購買管理システムとなります。
ユーザー登録
調達購買業務の効率化だけでなく、システムを導入することで、コスト削減や製品・資材のステータス可視化のほか、属人化していた購買情報の共有化による内部不正防止や統制にも役立ちます。
NEWJI DX
製造業に特化したデジタルトランスフォーメーション(DX)の実現を目指す請負開発型のコンサルティングサービスです。AI、iPaaS、および先端の技術を駆使して、製造プロセスの効率化、業務効率化、チームワーク強化、コスト削減、品質向上を実現します。このサービスは、製造業の課題を深く理解し、それに対する最適なデジタルソリューションを提供することで、企業が持続的な成長とイノベーションを達成できるようサポートします。
オンライン講座
製造業、主に購買・調達部門にお勤めの方々に向けた情報を配信しております。
新任の方やベテランの方、管理職を対象とした幅広いコンテンツをご用意しております。
お問い合わせ
コストダウンが利益に直結する術だと理解していても、なかなか前に進めることができない状況。そんな時は、newjiのコストダウン自動化機能で大きく利益貢献しよう!
(Β版非公開)