- お役立ち記事
- DX of the quenching process ensures optimal quality without waste
DX of the quenching process ensures optimal quality without waste
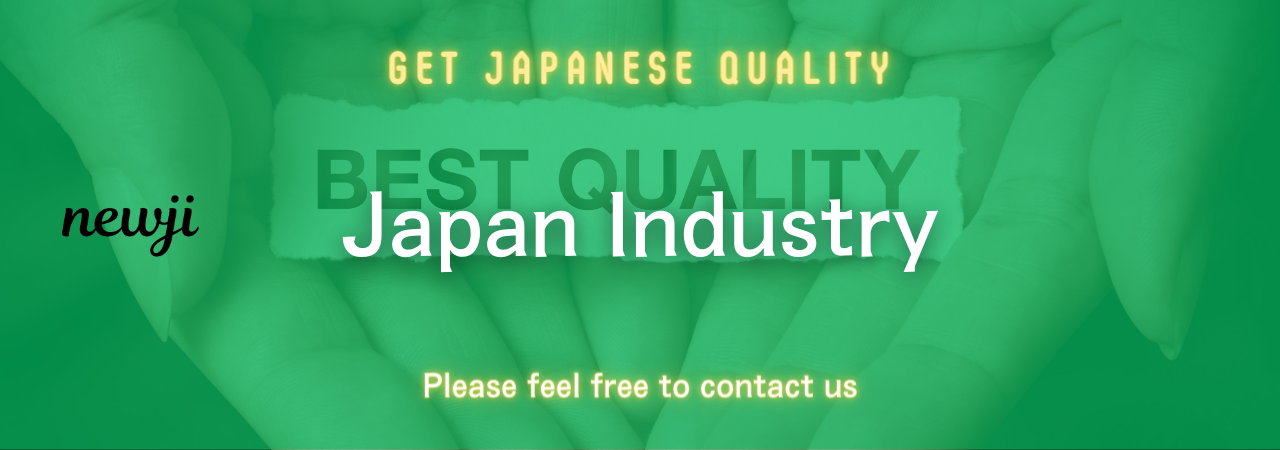
The process of digital transformation, commonly referred to as DX, is revolutionizing industries across the globe, including the quenching process in manufacturing.
Quenching, a heat treatment process to harden materials, particularly metals, has traditionally posed challenges in terms of maintaining quality and efficiency.
By integrating digital tools and technologies, companies can enhance the quenching process, ensuring optimal results with minimal waste.
This article delves into how DX impacts the quenching process and the benefits it brings to the industry.
目次
Understanding the Quenching Process
Quenching is a critical step in manufacturing, especially in industries like automotive, aerospace, and tool making.
The process involves heating metal to a high temperature and then rapidly cooling it in water, oil, or another cooling medium.
This rapid cooling transforms the metal’s structure, increasing its hardness and strength.
However, quenching is a complex process that requires precise control over temperature, cooling rates, and timing.
If not properly managed, it can lead to defects like warping, cracking, or uneven hardness, which compromise the material’s integrity and performance.
The Role of Digital Transformation in Quenching
Digital transformation leverages advanced technologies to improve existing processes and create new efficiencies.
In the context of quenching, DX involves the adoption of digital tools such as sensors, data analytics, and automation.
These technologies help in monitoring and controlling the quenching process more accurately, ensuring consistent quality across all batches.
Real-Time Monitoring with Sensors
One of the key advancements in DX for quenching is the use of sensors to monitor the process in real-time.
Sensors can measure critical parameters like temperature, cooling rate, and medium flow rate with high precision.
This real-time data allows operators to make immediate adjustments, preventing potential defects before they occur.
Data Analytics for Enhanced Decision Making
Collecting data is only part of the equation.
With data analytics, companies can gain deeper insights into the quenching process.
Advanced analytical tools can process vast amounts of data to identify patterns and trends.
This enables manufacturers to predict outcomes and make data-driven decisions to optimize the process.
For instance, by analyzing historical data, it can be determined which cooling rates yield the best hardness for a specific type of metal.
Automation and Process Control
Automation plays a crucial role in integrating DX into the quenching process.
Automated systems can execute precise control over heating and cooling phases, ensuring consistency in every batch.
Automated process control eliminates human errors, reduces variability, and enhances the reproducibility of results.
Moreover, automated systems can operate continuously, increasing productivity and reducing downtime.
Benefits of DX in the Quenching Process
The integration of digital technologies in the quenching process offers numerous benefits.
These advantages extend beyond just improving product quality to include operational efficiency and cost-effectiveness.
Improved Product Quality
Digital tools ensure that the quenching process is consistently executed according to specified parameters.
This eliminates variability and defects, resulting in high-quality, reliable products.
Consistent quality also means fewer rejected batches and less rework, which can be costly and time-consuming.
Enhanced Predictability and Control
With real-time data and advanced analytics, manufacturers can predict and control outcomes with greater accuracy.
This predictability helps in planning and managing production schedules more effectively.
Operators can foresee issues and take proactive measures to mitigate them, ensuring smoother operations.
Cost Savings and Efficiency
Implementing DX in quenching leads to significant cost savings.
Automation reduces labor costs by minimizing the need for manual monitoring and adjustments.
Efficient resource utilization, such as optimized use of cooling media and energy, further cuts costs.
Reduced defect rates and rework also translate to savings in materials and time.
Sustainability and Environmental Impact
Efficiency gains from DX contribute to sustainability.
Optimized processes consume less energy and resources, reducing the environmental footprint of manufacturing operations.
Precise control over the quenching process also minimizes waste, making operations more eco-friendly.
Challenges and Considerations in Implementing DX
While the benefits of DX in the quenching process are substantial, companies may face challenges in implementation.
It’s essential to consider these challenges and develop strategies to address them effectively.
Initial Investment and Costs
Integrating digital technologies requires significant initial investment.
Costs for sensors, data analytics tools, and automation systems can be high.
However, these costs should be viewed as a long-term investment that will yield substantial returns in terms of quality, efficiency, and cost savings.
Technical Expertise and Training
Successful implementation of DX requires technical expertise.
Manufacturing personnel need to be trained to operate and maintain new digital tools and systems.
Companies may need to invest in training programs or hire specialized professionals to manage DX initiatives.
Data Management and Security
Digitization results in the generation of vast amounts of data.
Effective data management practices must be in place to store, analyze, and utilize this data.
Data security is another critical concern, and companies must implement robust security measures to protect sensitive information from cyber threats.
Future Trends in DX for Quenching
The future of DX in the quenching process looks promising, with continuous advancements in technology.
Emerging trends include the use of artificial intelligence (AI) and machine learning (ML) for predictive maintenance and optimization.
AI-driven systems can analyze data more intelligently, offering predictive insights and automating decision-making processes.
Virtual and augmented reality (VR and AR) tools are also being explored for training and process visualization.
In conclusion, digital transformation is reshaping the quenching process in manufacturing, ensuring optimal quality and efficiency.
While there are challenges to overcome, the long-term benefits far outweigh the initial hurdles.
By embracing DX, companies can stay competitive, produce higher-quality products, and contribute to a sustainable future.
資料ダウンロード
QCD調達購買管理クラウド「newji」は、調達購買部門で必要なQCD管理全てを備えた、現場特化型兼クラウド型の今世紀最高の購買管理システムとなります。
ユーザー登録
調達購買業務の効率化だけでなく、システムを導入することで、コスト削減や製品・資材のステータス可視化のほか、属人化していた購買情報の共有化による内部不正防止や統制にも役立ちます。
NEWJI DX
製造業に特化したデジタルトランスフォーメーション(DX)の実現を目指す請負開発型のコンサルティングサービスです。AI、iPaaS、および先端の技術を駆使して、製造プロセスの効率化、業務効率化、チームワーク強化、コスト削減、品質向上を実現します。このサービスは、製造業の課題を深く理解し、それに対する最適なデジタルソリューションを提供することで、企業が持続的な成長とイノベーションを達成できるようサポートします。
オンライン講座
製造業、主に購買・調達部門にお勤めの方々に向けた情報を配信しております。
新任の方やベテランの方、管理職を対象とした幅広いコンテンツをご用意しております。
お問い合わせ
コストダウンが利益に直結する術だと理解していても、なかなか前に進めることができない状況。そんな時は、newjiのコストダウン自動化機能で大きく利益貢献しよう!
(Β版非公開)