- お役立ち記事
- Turning Basics and Best Practices in Manufacturing
Turning Basics and Best Practices in Manufacturing
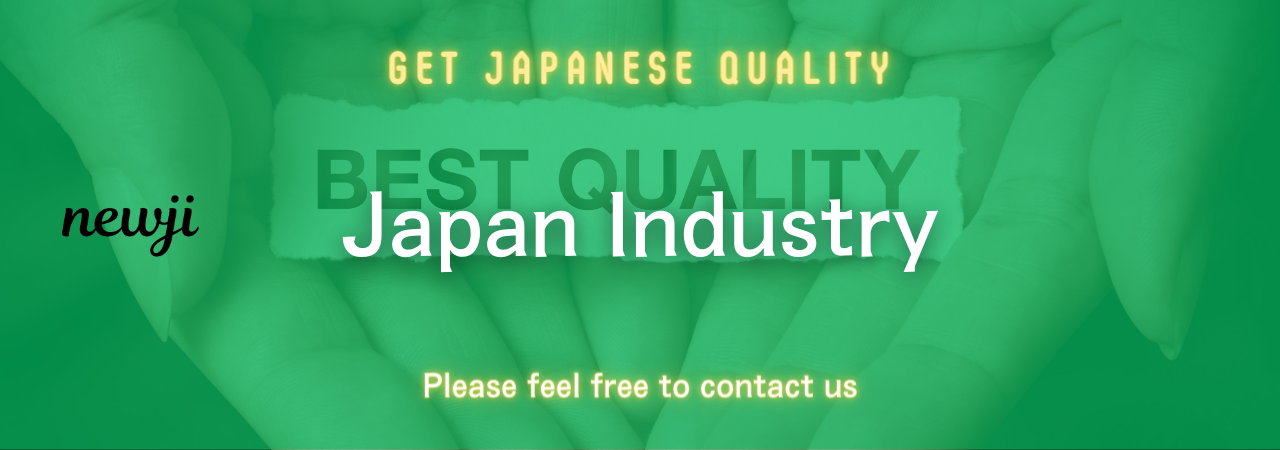
Turning is one of the most fundamental processes in the world of manufacturing.
It is a machining process in which a cutting tool removes material from a rotating workpiece to shape it into the desired form.
Whether you are new to the field or an experienced machinist, understanding the basics and best practices in turning is essential for producing high-quality components.
目次
What is Turning?
Turning is a machining process used to create cylindrical parts.
The workpiece, usually metal, is rotated on a lathe while a cutting tool moves along its surface to remove material.
This method is primarily used to produce parts with rotational symmetry, such as shafts, bolts, and various cylindrical components.
Types of Turning Operations
There are several types of turning operations, each serving a specific purpose:
– **Facing**: Involves cutting across the end of the workpiece to produce a flat surface.
– **Straight Turning**: Aims to reduce the diameter of the workpiece over a specific length.
– **Taper Turning**: Produces a conical shape by decreasing the diameter along the length.
– **Grooving**: Involves cutting a narrow channel into the workpiece.
– **Parting**: Separates a part of the workpiece by cutting through its diameter.
Equipment Used in Turning
The primary equipment used in turning is the lathe, which can be manual or CNC (Computer Numerical Control).
Manual Lathes
Manual lathes require the operator to control the cutting tool manually.
They are ideal for smaller jobs or prototypes.
Operators need to be highly skilled to achieve precision manually.
CNC Lathes
CNC lathes are controlled by computer programs, which makes them highly accurate and efficient.
They are suitable for mass production, offering consistent quality with minimal human intervention.
Materials Used in Turning
Various materials can be used in turning, each with specific characteristics that affect the machining process.
Metals
Metals such as steel, aluminum, brass, and copper are commonly used.
Each metal has different properties, such as hardness and melting point, which influence the turning process.
Plastics
Plastics are also used for turning, especially for creating parts that need to be lightweight or corrosion-resistant.
However, plastics can be more challenging to machine due to their lower melting points and tendency to deform.
Best Practices for Turning
To achieve high-quality results, following best practices is crucial.
Here are some essential tips:
Tool Selection
Choosing the right cutting tool is vital for efficient turning.
Tool material, geometry, and coating should match the workpiece material to ensure optimal cutting performance.
Cutting Parameters
Selecting the correct cutting parameters—such as cutting speed, feed rate, and depth of cut—can significantly impact the quality and efficiency of the turning process.
Adjust these parameters to suit the material and desired finish.
Lubrication and Cooling
Using appropriate lubrication and cooling fluids can extend tool life and improve surface finish.
Always use the recommended type and amount of coolant for the material you are machining.
Tool Maintenance
Regularly inspect and maintain your cutting tools to ensure they are sharp and in good condition.
Dull or damaged tools can lead to poor surface finish and increased wear on the workpiece.
Workpiece Mounting
Securely mounting the workpiece on the lathe is essential for safety and precision.
Use appropriate clamping methods to keep the workpiece stable during machining.
Quality Control
Quality control is crucial in turning operations to ensure the final product meets the required specifications.
Dimensional Accuracy
Use precision measuring instruments such as calipers, micrometers, and gauges to check the dimensions of the turned parts.
These tools help verify that the components meet the specified tolerances.
Surface Finish
The surface finish of the turned part is a critical quality parameter, especially for components that will interact with other parts.
Use profilometers to measure surface roughness and ensure it meets the required standards.
Defect Inspection
Regularly inspect the turned parts for defects such as cracks, scratches, or unwanted deformation.
Identify and address any issues promptly to maintain product quality.
Safety Measures
Safety should always be a priority in any machining operation.
Personal Protective Equipment (PPE)
Always wear appropriate PPE, including safety glasses, gloves, and hearing protection.
This equipment helps protect against flying debris, sharp edges, and high noise levels.
Machine Safety
Ensure all safety guards and emergency stop buttons on the lathe are in place and functioning correctly.
Never bypass safety features, and always follow the manufacturer’s guidelines.
Work Environment
Maintain a clean and organized work area to prevent accidents.
Keep tools and materials properly stored and ensure there is adequate lighting to see clearly.
Turning is a versatile and essential machining process in the manufacturing industry.
By understanding the basics and best practices, you can improve the efficiency, quality, and safety of your turning operations.
Whether you are working with metals or plastics, manual or CNC lathes, the principles remain the same.
Follow these guidelines to achieve the best results and continue honing your skills for a successful machining career.
資料ダウンロード
QCD調達購買管理クラウド「newji」は、調達購買部門で必要なQCD管理全てを備えた、現場特化型兼クラウド型の今世紀最高の購買管理システムとなります。
ユーザー登録
調達購買業務の効率化だけでなく、システムを導入することで、コスト削減や製品・資材のステータス可視化のほか、属人化していた購買情報の共有化による内部不正防止や統制にも役立ちます。
NEWJI DX
製造業に特化したデジタルトランスフォーメーション(DX)の実現を目指す請負開発型のコンサルティングサービスです。AI、iPaaS、および先端の技術を駆使して、製造プロセスの効率化、業務効率化、チームワーク強化、コスト削減、品質向上を実現します。このサービスは、製造業の課題を深く理解し、それに対する最適なデジタルソリューションを提供することで、企業が持続的な成長とイノベーションを達成できるようサポートします。
オンライン講座
製造業、主に購買・調達部門にお勤めの方々に向けた情報を配信しております。
新任の方やベテランの方、管理職を対象とした幅広いコンテンツをご用意しております。
お問い合わせ
コストダウンが利益に直結する術だと理解していても、なかなか前に進めることができない状況。そんな時は、newjiのコストダウン自動化機能で大きく利益貢献しよう!
(Β版非公開)