- お役立ち記事
- Innovative Target Material Techniques for Blackening Wiring Films in Japanese Metal Mesh Manufacturing
Innovative Target Material Techniques for Blackening Wiring Films in Japanese Metal Mesh Manufacturing
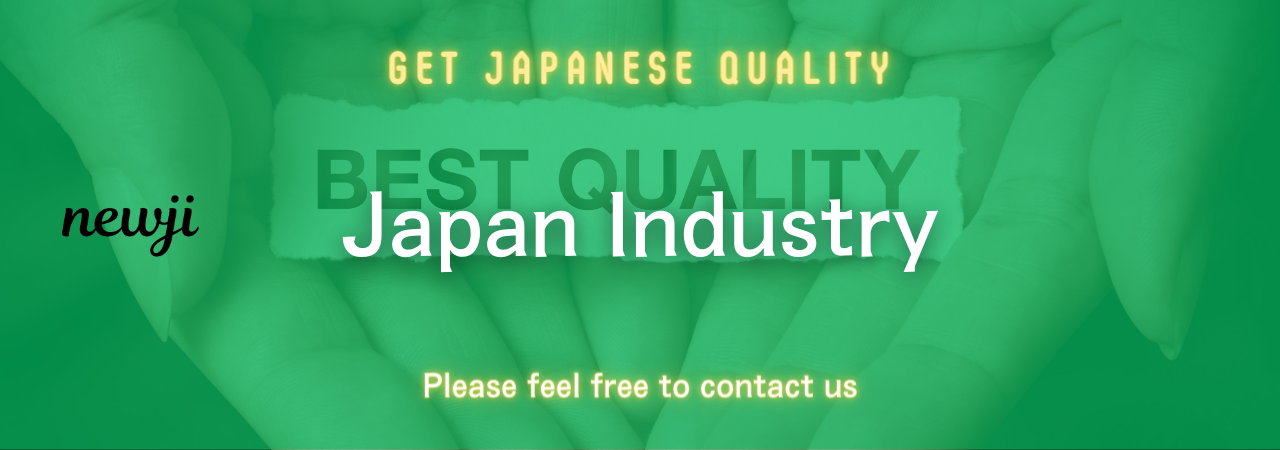
目次
Introduction
In the constantly evolving world of electronics and display technology, the need for advanced materials and innovative techniques is paramount. One such area of innovation is the blackening of wiring films in metal mesh manufacturing.
Metal mesh technology, used extensively in touch screens and other display technologies, requires precise control of light reflection and transmission. Blackening the wiring films can significantly enhance the visual clarity and performance of these displays.
In Japan, renowned for its meticulous manufacturing standards, there have been significant advancements in this field. This article delves into the innovative target material techniques for blackening wiring films in Japanese metal mesh manufacturing, focusing on their benefits, practical applications, and the competitive edge they offer to global manufacturers.
Understanding Metal Mesh Technology
Metal mesh technology involves the creation of fine conductive grids that are embedded within touchscreens and LCD displays. These grids are crucial for the functionality of the touch interface, enabling precise touch recognition and signal transmission.
However, one of the challenges with metal mesh wiring is the reflection of light, which can hamper the display quality. To address this, techniques to blacken the wiring films have been developed, significantly reducing glare and improving readability.
Importance of Blackening Wiring Films
Blackening wiring films in metal mesh technology serves several critical functions:
– **Reduces Reflectivity:** By reducing the reflection of ambient light, blackened films improve screen visibility and readability, particularly in brightly lit environments.
– **Enhances Display Contrast:** Blackened films enhance the contrast of the display, making visuals crisper and more vivid.
– **Improves Aesthetic Appeal:** Blackened films contribute to a sleek, premium look, aligning with the high standards of modern electronic devices.
Innovative Techniques from Japanese Manufacturers
Japan’s manufacturing sector is renowned for its precision and innovation. Several Japanese companies have pioneered advanced techniques for blackening wiring films in metal mesh manufacturing, leveraging their expertise in material science and engineering.
Advanced Coating Processes
One of the primary methods employed by Japanese manufacturers involves advanced coating processes. These processes typically include:
– **Sputter Coating:** This technique uses a high-energy argon ion beam to eject particles from a target material, which then deposits a thin, uniform layer of a blackening material on the wiring film. The precision of this method ensures uniform coverage and high adhesion.
– **Chemical Vapor Deposition (CVD):** In this technique, gaseous precursors form a solid film on the substrate through chemical reactions. This method allows for the deposition of highly conformal and uniform blackening layers, essential for optimal performance.
– **Electroless Plating:** This method involves the chemical deposition of a blackening material onto the wiring film without the use of an electric current. It offers excellent coverage and adhesion, often used for creating highly conductive and corrosion-resistant layers.
Nanomaterial Integration
Nanotechnology has revolutionized many aspects of materials science, and Japanese manufacturers have been at the forefront of integrating nanomaterials into metal mesh blackening processes. Techniques include:
– **Carbon Nanotubes (CNTs):** CNTs are used for their exceptional electrical conductivity and ability to absorb light, providing an efficient way to blacken wiring films while enhancing their electrical properties.
– **Graphene:** Graphene’s remarkable mechanical and conductive properties make it an ideal candidate for blackening films. Its application ensures minimal impact on the electrical conductivity of the metal mesh.
– **Nanoparticle Dispersions:** Using dispersions of metal or oxide nanoparticles, which possess light-absorbing properties, results in effective blackening of wiring films.
Advantages of Japanese Blackening Techniques
Implementing Japanese blackening techniques in metal mesh manufacturing offers several advantages:
Superior Optical Properties
Japanese techniques provide excellent control over light reflection and absorption, ensuring superior optical properties. This results in displays with improved contrast, brightness, and overall visual performance.
Enhanced Durability and Reliability
The advanced coating and nanomaterial integration methods employed by Japanese manufacturers result in wiring films that are more durable and reliable. They exhibit enhanced resistance to wear and environmental factors, maintaining performance over prolonged use.
Customization and Flexibility
Japanese manufacturers offer high levels of customization, tailoring blackening processes to meet the specific requirements of different applications. This flexibility ensures optimal performance across a range of devices and environments.
Challenges and Considerations
While the benefits of these innovative techniques are clear, there are also challenges and considerations to keep in mind:
Cost Implications
Advanced blackening techniques, particularly those involving nanomaterials and high-precision coatings, can be costly. Manufacturers need to weigh the benefits against the potential increase in production costs, ensuring cost-effectiveness.
Technical Complexity
Implementing these techniques requires a high level of technical expertise and sophisticated equipment. Companies must invest in training and infrastructure to effectively adopt these methods.
Compatibility and Integration
Ensuring compatibility with existing production processes and materials is essential. Manufacturers must carefully evaluate how these blackening techniques integrate with their current manufacturing workflow.
Supplier Negotiation Techniques
Negotiating with Japanese suppliers to adopt these advanced techniques requires a strategic approach:
Emphasize Long-Term Benefits
Highlight the long-term benefits of adopting these techniques, such as improved product performance, increased customer satisfaction, and potential for higher market share. Emphasizing the strategic value can make suppliers more open to investing in these methods.
Build Strong Relationships
Japanese business culture places a strong emphasis on relationships and trust. Building a strong, respectful relationship with suppliers can facilitate smoother negotiations and collaboration.
Leverage Case Studies and Success Stories
Showcase successful implementations of these techniques by other manufacturers. Case studies and success stories can provide concrete examples of the benefits and feasibility of adoption.
Best Practices for Implementation
For manufacturers looking to implement these innovative blackening techniques, adhering to best practices is crucial:
Conduct Thorough Testing
Before fully integrating any new technique, conduct thorough testing to ensure it meets the desired performance standards. This includes evaluating optical properties, durability, and compatibility with existing materials and processes.
Start with Pilot Projects
Initiate pilot projects to test the implementation on a smaller scale. This allows manufacturers to identify potential issues and refine the process before full-scale production.
Invest in Training and Development
Proper training for technical staff is essential. Ensure that employees are well-versed in the new techniques and understand the specific requirements and procedures.
Conclusion
Innovative target material techniques for blackening wiring films in Japanese metal mesh manufacturing represent a significant advancement in display technology. By leveraging advanced coating processes, nanomaterial integration, and meticulous manufacturing standards, Japanese manufacturers have set a high benchmark in the industry.
While the adoption of these techniques comes with challenges, the long-term benefits in terms of optical performance, durability, and customization options make them a worthwhile investment. Strategic negotiations with suppliers and adherence to best practices can facilitate successful implementation, ultimately enhancing the performance and appeal of electronic devices.
As the demand for high-performance displays continues to grow, staying abreast of these innovative techniques and incorporating them into production processes will be crucial for manufacturers aiming to maintain a competitive edge.
By learning from and collaborating with Japanese suppliers, manufacturers worldwide can harness the full potential of these cutting-edge advancements in metal mesh technology.
資料ダウンロード
QCD調達購買管理クラウド「newji」は、調達購買部門で必要なQCD管理全てを備えた、現場特化型兼クラウド型の今世紀最高の購買管理システムとなります。
ユーザー登録
調達購買業務の効率化だけでなく、システムを導入することで、コスト削減や製品・資材のステータス可視化のほか、属人化していた購買情報の共有化による内部不正防止や統制にも役立ちます。
NEWJI DX
製造業に特化したデジタルトランスフォーメーション(DX)の実現を目指す請負開発型のコンサルティングサービスです。AI、iPaaS、および先端の技術を駆使して、製造プロセスの効率化、業務効率化、チームワーク強化、コスト削減、品質向上を実現します。このサービスは、製造業の課題を深く理解し、それに対する最適なデジタルソリューションを提供することで、企業が持続的な成長とイノベーションを達成できるようサポートします。
オンライン講座
製造業、主に購買・調達部門にお勤めの方々に向けた情報を配信しております。
新任の方やベテランの方、管理職を対象とした幅広いコンテンツをご用意しております。
お問い合わせ
コストダウンが利益に直結する術だと理解していても、なかなか前に進めることができない状況。そんな時は、newjiのコストダウン自動化機能で大きく利益貢献しよう!
(Β版非公開)