- お役立ち記事
- Importance of OEE (Overall Equipment Effectiveness) in manufacturing and how to improve it
Importance of OEE (Overall Equipment Effectiveness) in manufacturing and how to improve it
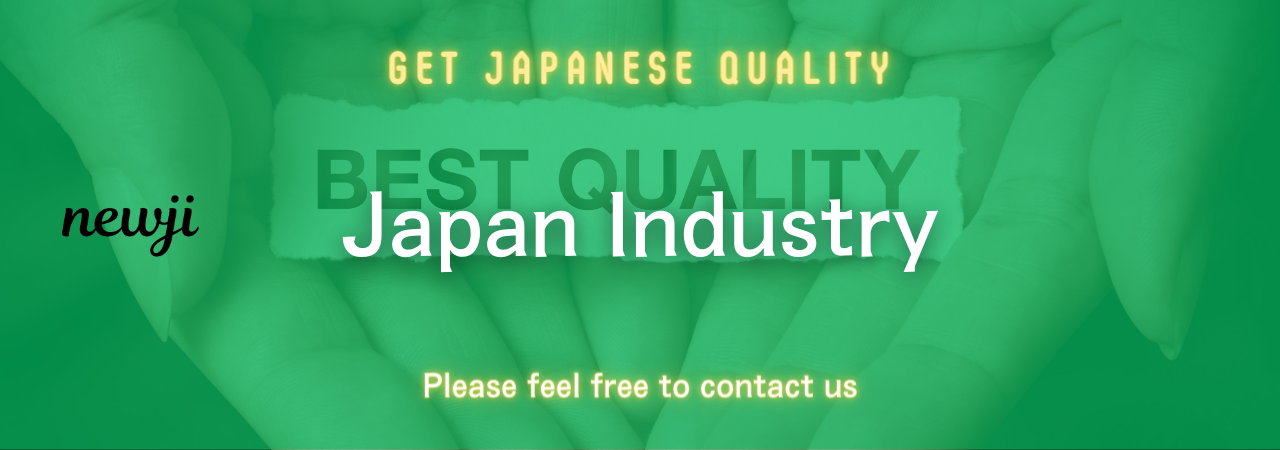
In today’s competitive manufacturing landscape, businesses need to optimize every aspect of their operations to stay ahead. One essential metric that helps manufacturers understand and improve the efficiency of their production processes is Overall Equipment Effectiveness (OEE).
OEE is a comprehensive measure that evaluates how effectively a manufacturing process operates by considering three key factors: availability, performance, and quality. By monitoring and improving OEE, businesses can significantly enhance productivity, reduce downtime, and increase profitability.
目次
What is OEE?
OEE stands for Overall Equipment Effectiveness. It is a widely recognized metric used to gauge the efficiency and productivity of manufacturing equipment.
OEE takes into account three primary components:
Availability, Performance, and Quality. When combined, these factors provide a clear picture of how effective a production process is.
Availability
Availability measures the percentage of scheduled time that the equipment is actually operating. It accounts for any downtime that the equipment experiences, such as maintenance, breakdowns, or setup adjustments.
By minimizing downtime, businesses can increase the availability of their equipment and improve overall productivity.
Performance
Performance measures the speed at which the equipment operates compared to its maximum potential. This factor accounts for any slowdowns, minor stops, or reduced speed that may occur during production.
Optimizing the performance of manufacturing equipment ensures that it operates at its full capacity, leading to higher output and efficiency.
Quality
Quality measures the percentage of good parts produced compared to the total number of parts manufactured. It accounts for any defects, rework, or scrap that may occur during production.
By improving the quality of the products, businesses can reduce waste, increase customer satisfaction, and enhance profitability.
Why is OEE Important in Manufacturing?
Understanding and improving OEE is crucial for several reasons. Here’s why OEE is important in manufacturing:
Identifies Areas for Improvement
OEE provides a detailed analysis of the production process by breaking it down into availability, performance, and quality. This breakdown helps identify specific areas that need improvement. For instance, if availability is low, it may indicate frequent breakdowns or maintenance issues. If performance is lacking, it may point to inefficiencies in the production process. And if quality is subpar, it could highlight problems with the manufacturing process or raw materials.
Enhances Productivity
By monitoring and improving OEE, manufacturers can significantly enhance productivity. Higher OEE means that equipment is operating at its full potential, with minimal downtime and defects. This leads to increased output, better resource utilization, and higher profitability.
Reduces Costs
Improving OEE helps reduce various costs associated with manufacturing. By minimizing downtime, manufacturers can decrease maintenance expenses and reduce the need for spare parts. Enhancing performance can lead to lower energy consumption and optimized use of raw materials. And by improving quality, businesses can reduce the costs associated with rework, scrap, and customer returns.
Increases Profitability
Better productivity, lower costs, and higher quality all contribute to increased profitability. By continuously monitoring and improving OEE, manufacturers can achieve sustained growth and outperform competitors. Higher OEE leads to more efficient use of resources, allowing businesses to produce more with less.
How to Improve OEE?
Improving OEE requires a systematic approach to identify and address the root causes of inefficiencies. Here are some practical steps to enhance OEE in manufacturing:
Conduct Regular Maintenance
Preventive and predictive maintenance are essential to ensure that equipment operates at its best. Regular maintenance helps prevent unexpected breakdowns and reduces downtime. Implementing a robust maintenance schedule and using condition-monitoring tools can keep equipment in optimal condition and improve availability.
Streamline Production Processes
Analyzing and refining production processes can help eliminate inefficiencies and boost performance. Evaluate the entire production workflow, identify bottlenecks, and implement Lean manufacturing principles to streamline processes. Reducing setup times, eliminating unnecessary steps, and optimizing layouts can enhance performance and increase OEE.
Implement Training Programs
Well-trained operators are crucial for maintaining equipment efficiency and quality. Implement comprehensive training programs to ensure that operators understand the best practices for operating and maintaining equipment. Provide ongoing training and support to keep operators up-to-date with the latest techniques and technologies.
Utilize Technology and Automation
Investing in advanced technology and automation can significantly improve OEE. Modern equipment with built-in sensors and IoT capabilities can provide real-time data on performance, availability, and quality. Use data analytics to monitor equipment performance and identify trends and anomalies. Automation can also reduce human error, improve consistency, and enhance overall productivity.
Implement Continuous Improvement Programs
Adopting a culture of continuous improvement is essential for sustained OEE enhancement. Implement methodologies such as Six Sigma or Total Productive Maintenance (TPM) to identify and address inefficiencies systematically. Encourage employees to participate in improvement initiatives and provide incentives for innovative solutions.
Monitor and Analyze OEE Data
Regularly monitor and analyze OEE data to track progress and identify areas for further improvement. Use OEE software tools to collect, analyze, and visualize data. Set benchmarks and targets to measure performance against industry standards. Use the insights gained from OEE data to make informed decisions and drive continuous improvement.
Conclusion
Overall Equipment Effectiveness (OEE) is a vital metric for manufacturers aiming to optimize their production processes. By understanding and improving availability, performance, and quality, businesses can enhance productivity, reduce costs, and increase profitability.
Implementing preventive maintenance, streamlining production processes, investing in technology, and fostering a culture of continuous improvement are all essential steps to boost OEE.
Regularly monitoring and analyzing OEE data ensures that manufacturers can make informed decisions and stay competitive in an ever-evolving market. By prioritizing OEE, manufacturers can achieve operational excellence and drive sustainable growth.
資料ダウンロード
QCD調達購買管理クラウド「newji」は、調達購買部門で必要なQCD管理全てを備えた、現場特化型兼クラウド型の今世紀最高の購買管理システムとなります。
ユーザー登録
調達購買業務の効率化だけでなく、システムを導入することで、コスト削減や製品・資材のステータス可視化のほか、属人化していた購買情報の共有化による内部不正防止や統制にも役立ちます。
NEWJI DX
製造業に特化したデジタルトランスフォーメーション(DX)の実現を目指す請負開発型のコンサルティングサービスです。AI、iPaaS、および先端の技術を駆使して、製造プロセスの効率化、業務効率化、チームワーク強化、コスト削減、品質向上を実現します。このサービスは、製造業の課題を深く理解し、それに対する最適なデジタルソリューションを提供することで、企業が持続的な成長とイノベーションを達成できるようサポートします。
オンライン講座
製造業、主に購買・調達部門にお勤めの方々に向けた情報を配信しております。
新任の方やベテランの方、管理職を対象とした幅広いコンテンツをご用意しております。
お問い合わせ
コストダウンが利益に直結する術だと理解していても、なかなか前に進めることができない状況。そんな時は、newjiのコストダウン自動化機能で大きく利益貢献しよう!
(Β版非公開)