- お役立ち記事
- The Quality Quest: How Japanese Companies Lead the Global Market
The Quality Quest: How Japanese Companies Lead the Global Market
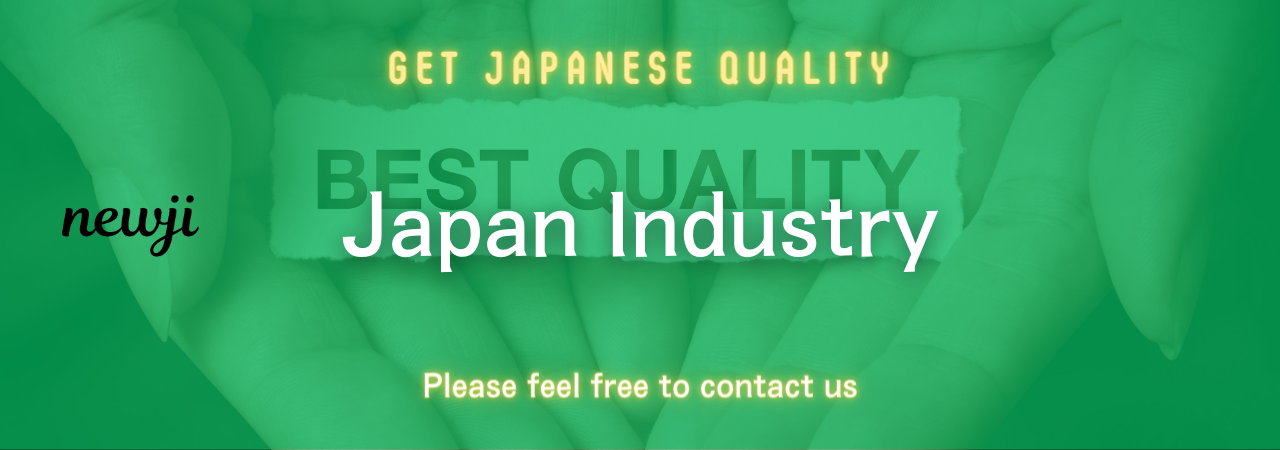
Quality is a crucial factor for any business aiming to thrive in the global market.
When it comes to setting high standards in manufacturing and services, Japanese companies often serve as a benchmark.
This article dives into what makes Japanese companies excel in quality and how their quest for perfection impacts the global market landscape.
目次
A Legacy of Craftsmanship
The emphasis on quality in Japan can be traced back to centuries-old traditions of craftsmanship.
From intricate samurai swords to delicate tea ceremonies, the culture itself has long celebrated meticulous attention to detail and perfection.
During the post-war period, Japan’s economy skyrocketed, and the country shifted its focus to industrial production. However, the traditional commitment to craftsmanship remained deeply ingrained in the society.
This cultural background laid the groundwork for the development of a quality-first mindset in modern industries.
TQM: Total Quality Management
One of the fundamental aspects of Japanese business culture is the focus on Total Quality Management (TQM).
TQM is a comprehensive approach that ensures all members of an organization participate in improving processes, products, and services.
Japanese companies like Toyota and Sony have taken TQM principles to heart, integrating them deeply into their corporate policies.
For instance, Toyota’s famed production system, The Toyota Way, emphasizes continuous improvement (Kaizen) and respect for people.
These practices have not only enhanced product quality but also optimized operational efficiency.
Kaizen: Continuous Improvement
The concept of Kaizen, meaning “change for the better,” is another cornerstone of Japanese quality management.
Kaizen involves everyone from top-level executives to factory floor workers, encouraging a culture where employees constantly seek ways to improve their work processes.
This relentless pursuit of improvement has allowed Japanese companies to adapt quickly to new challenges and consistently elevate their standards.
For example, workers are encouraged to suggest small, incremental changes that can result in significant improvements over time.
Customer-Centric Approach
Japanese companies place a strong emphasis on understanding and meeting customer needs.
Customer feedback plays a crucial role in shaping product development and services.
Companies like Panasonic and Sony invest heavily in market research to gain insights into consumer preferences and expectations.
By prioritizing customer satisfaction, these businesses can maintain a loyal customer base and create products that consistently meet high standards.
Strong Supply Chain Management
Quality doesn’t end at the production line; it extends throughout the entire supply chain.
Japanese companies are known for their rigorous supply chain management practices.
Toyota’s Just-In-Time (JIT) inventory system is a prime example.
By receiving goods only as they are needed in the production process, Toyota minimizes waste and enhances efficiency.
Moreover, Japanese firms ensure that their suppliers also adhere to high-quality standards, creating a cohesive network that prioritizes quality at every stage.
Innovation and Technology
Innovation is at the heart of Japan’s approach to quality.
Japanese companies invest significantly in research and development to produce cutting-edge technology and innovative solutions.
Firms like Sony, Canon, and Mitsubishi continually push the boundaries in their respective fields, setting new benchmarks for quality and performance.
By staying ahead of technological trends, these companies can develop sophisticated products that provide exceptional value to consumers worldwide.
Employee Training and Development
Employees are the backbone of any organization, and Japanese companies invest considerably in their workforce.
Training and development programs ensure that employees possess the skills and knowledge needed to maintain high-quality standards.
Companies like Toyota and Honda offer extensive training programs to cultivate a highly skilled workforce.
Employees are trained not just in their specific roles, but also in the principles of TQM and Kaizen.
This comprehensive approach empowers workers to contribute meaningfully to the company’s quality initiatives.
Global Influence
The success of Japanese companies in achieving high-quality standards has influenced businesses around the world.
Many international companies have adopted Japanese practices like TQM, Kaizen, and JIT to improve their operations.
For example, American car manufacturers like Ford and General Motors have implemented these strategies to enhance their own production processes.
Japanese standards have also influenced global quality certifications, such as ISO standards, which many companies adhere to today.
These certifications emphasize similar principles of continuous improvement and comprehensive quality management.
Challenges and Future Outlook
Despite their success, Japanese companies face ongoing challenges.
Global competition, fluctuating economic conditions, and rapid technological advancements require constant adaptation.
However, the principles that have brought Japanese companies this far are likely to continue guiding them into the future.
Fostering a culture of continuous improvement, prioritizing customer satisfaction, and investing in innovation will remain critical.
Moreover, Japanese firms are increasingly focusing on sustainable practices, integrating environmental considerations into their quest for quality.
Conclusion
Japanese companies have set a high bar in the global market by prioritizing quality in every aspect of their operations.
Through principles like TQM, Kaizen, and robust supply chain management, they’ve created a legacy of excellence that resonates worldwide.
As they navigate future challenges, their unwavering commitment to quality ensures they will remain leaders in the global market.
By understanding and adopting these practices, other businesses can also aspire to achieve similar levels of success and customer satisfaction.
資料ダウンロード
QCD調達購買管理クラウド「newji」は、調達購買部門で必要なQCD管理全てを備えた、現場特化型兼クラウド型の今世紀最高の購買管理システムとなります。
ユーザー登録
調達購買業務の効率化だけでなく、システムを導入することで、コスト削減や製品・資材のステータス可視化のほか、属人化していた購買情報の共有化による内部不正防止や統制にも役立ちます。
NEWJI DX
製造業に特化したデジタルトランスフォーメーション(DX)の実現を目指す請負開発型のコンサルティングサービスです。AI、iPaaS、および先端の技術を駆使して、製造プロセスの効率化、業務効率化、チームワーク強化、コスト削減、品質向上を実現します。このサービスは、製造業の課題を深く理解し、それに対する最適なデジタルソリューションを提供することで、企業が持続的な成長とイノベーションを達成できるようサポートします。
オンライン講座
製造業、主に購買・調達部門にお勤めの方々に向けた情報を配信しております。
新任の方やベテランの方、管理職を対象とした幅広いコンテンツをご用意しております。
お問い合わせ
コストダウンが利益に直結する術だと理解していても、なかなか前に進めることができない状況。そんな時は、newjiのコストダウン自動化機能で大きく利益貢献しよう!
(Β版非公開)