- お役立ち記事
- Optimizing the Purchase Order Process: Purchasing Management Methods to Ensure Product Availability and Cost Efficiency
Optimizing the Purchase Order Process: Purchasing Management Methods to Ensure Product Availability and Cost Efficiency
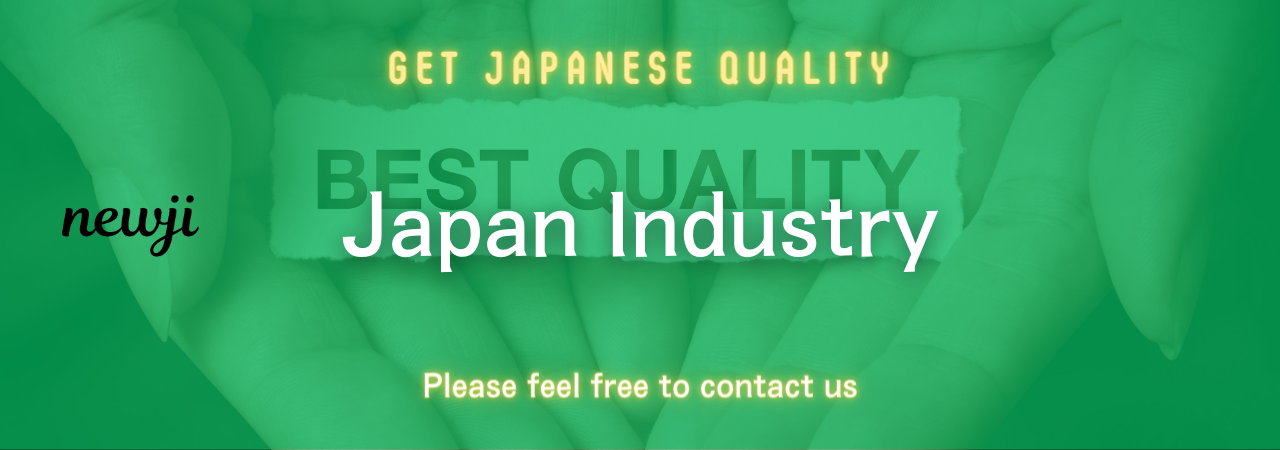
The purchase order process is a core aspect of effective supply chain management.
Ensuring product availability while maintaining cost efficiency can make or break a business.
Optimizing this process involves both strategic planning and tactical execution.
In this article, we will delve into methods that can help you manage your purchasing processes more efficiently.
目次
Understanding the Purchase Order Process
A purchase order (PO) is a document that tells a supplier exactly what products or services your company needs.
It includes details like the type, quantity, and price of the product being purchased.
An effective purchase order process ensures that you have the right products at the right time and at the right cost.
The Basics of Creating a Purchase Order
Creating a purchase order usually begins with identifying the need for a product or service.
Once the need is identified, the next step is to select a supplier.
After selecting a supplier, a formal PO is created and sent to the supplier.
The supplier then confirms the PO and delivers the goods or services.
Finally, the company receives the goods and processes the invoice for payment.
Challenges in the Purchase Order Process
Despite its importance, the purchase order process can be fraught with challenges.
These may include long lead times, inaccuracies in the order, supplier reliability issues, and complexities in managing large volumes of POs.
Addressing these challenges requires a well-thought-out strategy and proper execution.
Strategies for Optimizing the Purchase Order Process
Use of Technology
Leveraging technology is one of the most effective ways to optimize the PO process.
Software solutions offer real-time tracking of orders, automated invoice processing, and seamless communication with suppliers.
These features reduce errors and improve efficiency.
Efficient Supplier Management
Building strong relationships with reliable suppliers is crucial.
This can be achieved by regularly evaluating supplier performance based on factors like delivery time, quality of products, and price competitiveness.
Good communication and mutually beneficial agreements also contribute to better supplier relationships.
Just-In-Time (JIT) Purchasing
Just-In-Time purchasing is a strategy where you order goods only when they are needed.
This minimizes inventory costs and reduces the risk of overstocking.
However, this requires a reliable supply chain and robust forecasting capabilities.
Bulk Purchasing and Contract Purchasing
Purchasing in bulk often allows for discounted prices, thereby saving costs.
On the other hand, contract purchasing involves negotiating long-term agreements with suppliers to lock in prices and ensure a steady supply.
Both strategies have their benefits and can be chosen based on specific business needs.
Cost Efficiency in the Purchase Order Process
Improve Forecasting Accuracy
Accurate forecasting helps to balance supply and demand effectively.
Using historical data and market trends, businesses can predict future needs more accurately.
This reduces the instances of rush orders or over-ordering, both of which can incur additional costs.
Negotiation Skills
Strong negotiation skills can significantly impact cost efficiency.
Negotiating better payment terms, lower prices, or additional services can save costs.
Good negotiators can also build better supplier relationships, which further supports cost efficiency.
Regular Audits
Regularly auditing the purchase order process can identify inefficiencies or discrepancies.
These can then be addressed to streamline the process and cut down unnecessary costs.
Audits also help ensure that the terms of purchase agreements are being met.
Implementing Performance Metrics
Using Key Performance Indicators (KPIs) to measure the efficiency of the purchase order process is essential.
Metrics like order cycle time, order accuracy, and supplier lead time can provide valuable insights.
These insights can guide strategic decisions to improve the purchase order process.
Ensuring Product Availability
Effective Inventory Management
Efficient inventory management ensures that products are available when needed.
This can be achieved through methods such as ABC analysis, which classifies inventory items based on their importance.
Other techniques include safety stock levels and reorder points that trigger new orders when inventory falls below a certain threshold.
Supplier Diversification
Relying on a single supplier can be risky.
Diversifying suppliers reduces the risk of supply chain disruptions.
If one supplier faces issues, another can step in to ensure product availability.
Supplier Relationship Management
Effective communication and collaboration with suppliers can prevent stockouts.
Regular updates on stock levels, demand forecasts, and potential supply chain disruptions help suppliers meet your needs better.
A good relationship with suppliers can also lead to preferential treatment in times of high demand.
Lead Time Management
Understanding and managing lead times can improve product availability.
Lead time includes the time taken to place an order, the supplier’s processing time, and the delivery time.
Reducing lead times through efficient processes ensures quicker replenishment of stocks.
Conclusion
Optimizing the purchase order process is crucial for any business aiming to achieve cost efficiency and product availability.
Implementing the right strategies can overcome common challenges in the purchase order process.
By leveraging technology, managing suppliers effectively, and focusing on cost-efficient practices, businesses can streamline their purchasing operations.
Regular audits and performance tracking further ensure ongoing improvement.
With these methods, companies can create a more efficient and reliable purchase order process, benefiting both the business and its customers.
資料ダウンロード
QCD調達購買管理クラウド「newji」は、調達購買部門で必要なQCD管理全てを備えた、現場特化型兼クラウド型の今世紀最高の購買管理システムとなります。
ユーザー登録
調達購買業務の効率化だけでなく、システムを導入することで、コスト削減や製品・資材のステータス可視化のほか、属人化していた購買情報の共有化による内部不正防止や統制にも役立ちます。
NEWJI DX
製造業に特化したデジタルトランスフォーメーション(DX)の実現を目指す請負開発型のコンサルティングサービスです。AI、iPaaS、および先端の技術を駆使して、製造プロセスの効率化、業務効率化、チームワーク強化、コスト削減、品質向上を実現します。このサービスは、製造業の課題を深く理解し、それに対する最適なデジタルソリューションを提供することで、企業が持続的な成長とイノベーションを達成できるようサポートします。
オンライン講座
製造業、主に購買・調達部門にお勤めの方々に向けた情報を配信しております。
新任の方やベテランの方、管理職を対象とした幅広いコンテンツをご用意しております。
お問い合わせ
コストダウンが利益に直結する術だと理解していても、なかなか前に進めることができない状況。そんな時は、newjiのコストダウン自動化機能で大きく利益貢献しよう!
(Β版非公開)