- お役立ち記事
- Causes and Solutions for Thermal Cracking in Manufacturing
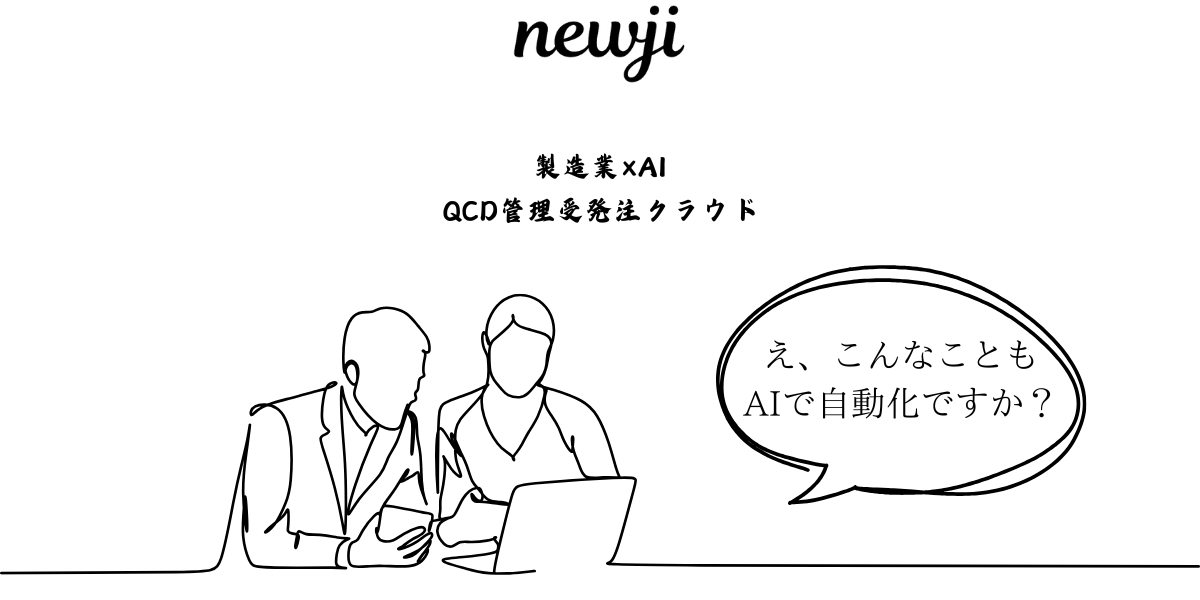
Causes and Solutions for Thermal Cracking in Manufacturing
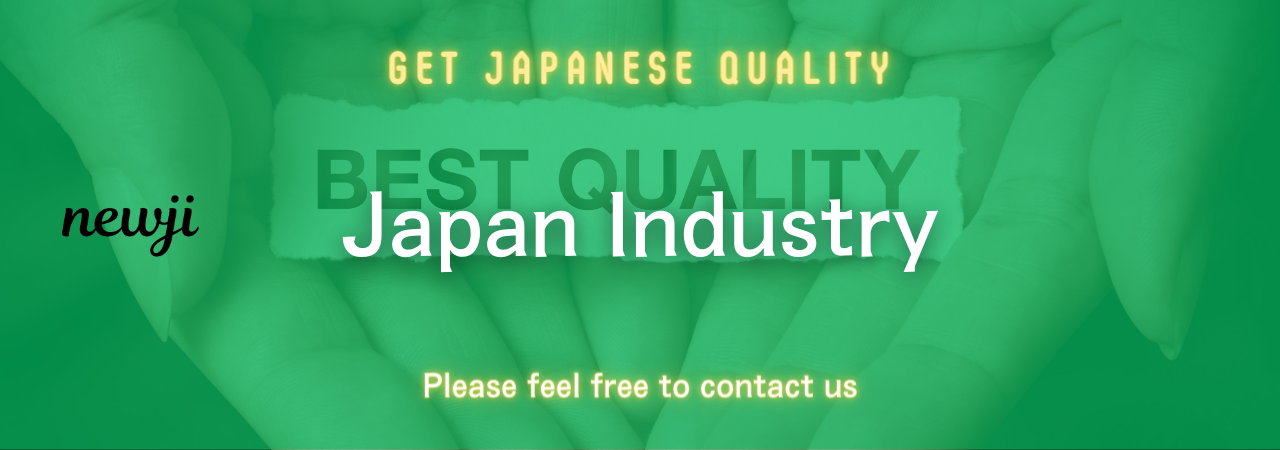
Thermal cracking is a significant challenge that manufacturing industries often face.
It affects various materials, reducing their structural integrity and lifespan.
Understanding the causes and solutions for thermal cracking is essential for ensuring the longevity and reliability of manufactured products.
目次
What is Thermal Cracking?
Thermal cracking refers to the formation of cracks in materials due to temperature fluctuations.
When materials are subjected to rapid heating and cooling cycles, the thermal stress can cause cracks to develop.
These cracks can compromise the material’s strength and lead to potential failures.
Causes of Thermal Cracking
Temperature Variations
One of the primary causes of thermal cracking is the variation in temperature experienced by materials.
Rapid heating and cooling can cause thermal expansion and contraction, leading to stress within the material.
If the stress exceeds the material’s tolerance, cracks can form.
Material Properties
Different materials respond to temperature changes in different ways.
Materials with low thermal conductivity or high coefficients of thermal expansion are more prone to thermal cracking.
Understanding the properties of the materials used in manufacturing is crucial for predicting and preventing thermal cracking.
Manufacturing Processes
Certain manufacturing processes involve high-temperature operations, such as welding, casting, and heat treatment.
These processes can introduce thermal stresses, leading to cracking if not properly managed.
Adjusting the parameters of these processes can reduce the risk of thermal cracking.
Environmental Factors
External environmental conditions, such as ambient temperature changes, can also contribute to thermal cracking.
For instance, materials exposed to outdoor conditions may experience thermal fatigue due to daily temperature cycles, leading to cracks over time.
Residual Stresses
Residual stresses are stresses that remain in a material after it has been manufactured or processed.
These stresses can interact with thermal stresses, exacerbating the risk of cracking.
Properly managing residual stresses is essential to prevent thermal cracking.
Solutions for Thermal Cracking
Material Selection
Choosing the right material for the specific application is the first step in preventing thermal cracking.
Materials with high thermal conductivity and low thermal expansion coefficients are less likely to crack under temperature fluctuations.
Consulting with materials scientists or engineers can provide valuable insights into the best material choices.
Controlled Heating and Cooling
Implementing controlled heating and cooling practices during manufacturing processes can significantly reduce the risk of thermal cracking.
Gradual heating and cooling allow the material to adjust to temperature changes, minimizing thermal stress.
Using techniques like preheating and postheating can also help manage thermal stress.
Stress Relief Techniques
Applying stress relief techniques, such as annealing or tempering, can help reduce residual stresses in materials.
These processes involve heating the material to a specific temperature and then cooling it slowly to relieve internal stresses.
Stress relief treatments should be tailored to the specific material and application.
Environmental Control
Controlling the environmental conditions in which materials are stored and used can prevent thermal cracking.
For outdoor applications, materials should be protected from extreme temperature variations.
Using insulation or coatings can help maintain a stable temperature around the material, reducing the risk of cracking.
Quality Control and Inspection
Regular quality control and inspection are essential for identifying and addressing potential thermal cracking before it leads to failure.
Non-destructive testing methods, such as ultrasonic testing and radiography, can detect internal cracks that are not visible to the naked eye.
Implementing a robust inspection regime can ensure the longevity and reliability of manufactured products.
Case Studies
Aerospace Industry
In the aerospace industry, thermal cracking poses a significant risk due to the extreme temperature variations experienced by aircraft components.
By selecting high-performance materials and implementing controlled heating and cooling processes, manufacturers have successfully reduced the incidence of thermal cracking.
Regular inspections and stress relief treatments are also standard practices to ensure the safety and performance of aerospace components.
Automotive Industry
Thermal cracking is a common issue in the automotive industry, particularly in engine components subjected to high temperatures.
Automakers have addressed this challenge by using advanced alloys and ceramics with high thermal stability.
Controlled cooling processes and regular inspections help mitigate the risk of thermal cracking in critical engine parts.
Construction Industry
In construction, materials such as concrete and steel are often exposed to environmental temperature fluctuations.
To prevent thermal cracking, construction companies use materials with appropriate thermal properties and apply protective coatings.
Stress relief techniques, such as post-tensioning in concrete structures, further reduce the risk of thermal cracking.
Conclusion
Thermal cracking is a common and challenging issue in manufacturing that can compromise the integrity of materials.
By understanding the causes and implementing effective solutions, manufacturers can significantly reduce the risk of thermal cracking.
Material selection, controlled heating and cooling, stress relief techniques, environmental control, and regular inspections are key strategies in preventing thermal cracking.
Adopting these practices will ensure the longevity and reliability of manufactured products, contributing to the overall success of various industries.
資料ダウンロード
QCD調達購買管理クラウド「newji」は、調達購買部門で必要なQCD管理全てを備えた、現場特化型兼クラウド型の今世紀最高の購買管理システムとなります。
ユーザー登録
調達購買業務の効率化だけでなく、システムを導入することで、コスト削減や製品・資材のステータス可視化のほか、属人化していた購買情報の共有化による内部不正防止や統制にも役立ちます。
NEWJI DX
製造業に特化したデジタルトランスフォーメーション(DX)の実現を目指す請負開発型のコンサルティングサービスです。AI、iPaaS、および先端の技術を駆使して、製造プロセスの効率化、業務効率化、チームワーク強化、コスト削減、品質向上を実現します。このサービスは、製造業の課題を深く理解し、それに対する最適なデジタルソリューションを提供することで、企業が持続的な成長とイノベーションを達成できるようサポートします。
オンライン講座
製造業、主に購買・調達部門にお勤めの方々に向けた情報を配信しております。
新任の方やベテランの方、管理職を対象とした幅広いコンテンツをご用意しております。
お問い合わせ
コストダウンが利益に直結する術だと理解していても、なかなか前に進めることができない状況。そんな時は、newjiのコストダウン自動化機能で大きく利益貢献しよう!
(Β版非公開)