- お役立ち記事
- Revolutionizing Japanese Manufacturing: AI-Powered Visual Inspection and Quality Enhancement
Revolutionizing Japanese Manufacturing: AI-Powered Visual Inspection and Quality Enhancement
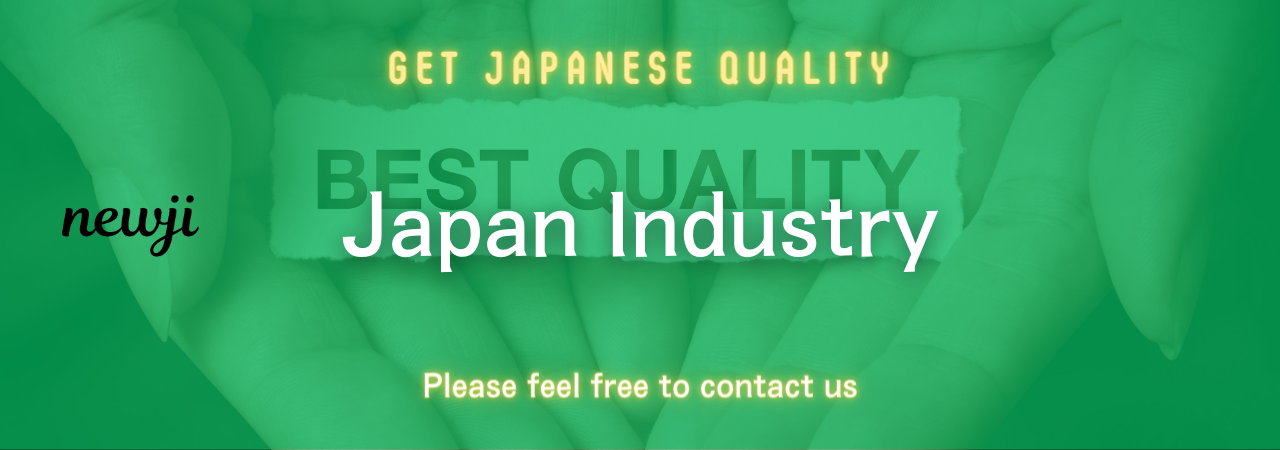
目次
Introduction to AI-Powered Visual Inspection in Japanese Manufacturing
Japanese manufacturing has long been revered for its uncompromising commitment to quality and precision.
Yet, as the industry faces increasing global competition and rising consumer expectations, maintaining these high standards becomes ever more challenging.
Enter AI-powered visual inspection, a technological advancement poised to revolutionize quality control processes in factories across Japan.
In this article, we will delve into the intricacies of AI-powered visual inspection, explore its benefits and limitations, discuss techniques for effective supplier negotiations, and examine best practices from a practical field perspective.
Understanding AI-Powered Visual Inspection
AI-powered visual inspection combines machine learning algorithms with computer vision technology to detect defects and anomalies in manufactured products.
This innovative approach supersedes traditional manual inspection methods that are often prone to human error and are time-consuming.
By leveraging AI, manufacturers can achieve higher accuracy, consistency, and speed in identifying quality issues.
The Mechanics of AI-Powered Visual Inspection
At its core, AI-powered visual inspection involves training machine learning models on vast datasets of images.
These datasets consist of both defective and defect-free products.
Through iterative training, the AI system learns to recognize patterns and features associated with various types of defects.
Once trained, the AI system can process real-time images captured from production lines to identify and flag defective items.
Advantages of AI-Powered Visual Inspection
Implementing AI-powered visual inspection offers multiple benefits:
Improved Accuracy: AI systems can consistently detect minute defects that may be overlooked by the human eye, ensuring a higher level of product quality.
Increased Speed: Automated inspection processes can keep pace with high-speed production lines, minimizing bottlenecks and boosting overall efficiency.
Cost Savings: By reducing the need for manual inspections and minimizing product recalls due to undetected defects, manufacturers can achieve significant cost savings.
Data-Driven Insights: AI systems generate valuable data on defect types and frequencies, enabling continuous improvement in manufacturing processes.
Challenges and Limitations
While AI-powered visual inspection holds immense promise, it is not without challenges.
Manufacturers must carefully consider these limitations to fully leverage the technology.
High Initial Investment
The implementation of AI-powered visual inspection systems requires substantial upfront investment in hardware, software, and skilled personnel.
Smaller manufacturers may find the cost prohibitive, highlighting the need for careful cost-benefit analysis.
Complex Integration
Integrating AI systems into existing production lines can be complex and may require significant time and effort.
Manufacturers must ensure that the AI system seamlessly communicates with other automation and quality control systems.
Data Quality
The effectiveness of AI-powered visual inspection hinges on the quality and quantity of training data.
Manufacturers must invest in creating comprehensive and accurate datasets to train their AI models, which can be a time-consuming and resource-intensive process.
Supplier Negotiation Techniques
Effective supplier negotiation is crucial for implementing AI-powered visual inspection systems in manufacturing.
Here are some techniques to consider:
Research and Preparation
Thorough research on potential suppliers is the foundation of successful negotiation.
Manufacturers should evaluate the supplier’s expertise, industry reputation, and ability to provide customized solutions tailored to their specific needs.
Value-Based Negotiation
Rather than focusing solely on price, manufacturers should emphasize the value that AI-powered inspection systems bring to their operations.
Highlighting the long-term cost savings, quality improvements, and competitive advantages can create a compelling case for investment.
Collaborative Approach
Adopting a collaborative approach fosters a positive relationship between manufacturers and suppliers.
Engaging suppliers as partners in the implementation process can lead to mutually beneficial outcomes, including tailored solutions and shared risk.
Trial and Evaluation
Negotiating trial periods for AI-powered inspection systems allows manufacturers to evaluate the technology’s effectiveness before committing to a full-scale implementation.
This approach reduces risk and builds confidence in the supplier’s capabilities.
Market Conditions for AI-Powered Visual Inspection
The market for AI-powered visual inspection systems is evolving rapidly, driven by advancements in AI technology and increasing demand for quality assurance in manufacturing.
Emerging Trends
Several trends are shaping the market landscape:
Customization: Manufacturers are seeking tailored AI solutions that address their unique inspection needs.
Edge Computing: Edge computing technologies enable real-time processing of visual data at the production line, reducing latency and enhancing efficiency.
Cloud Integration: Cloud-based AI platforms offer scalability and facilitate remote monitoring and analysis of inspection data.
Competitive Landscape
The competitive landscape is characterized by a growing number of AI solution providers offering diverse capabilities.
Manufacturers must carefully evaluate and select providers based on their expertise, track record, and ability to deliver reliable and scalable solutions.
Regulatory Considerations
Regulatory compliance is a critical aspect of implementing AI-powered visual inspection systems.
Manufacturers must ensure that their chosen solutions adhere to industry standards and regulatory requirements to avoid potential legal and compliance issues.
Best Practices for Implementing AI-Powered Visual Inspection
To maximize the benefits of AI-powered visual inspection, manufacturers should follow best practices that ensure successful implementation and sustained operational improvements.
Define Clear Objectives
Manufacturers should establish clear objectives for implementing AI-powered visual inspection, such as reducing defect rates, improving throughput, or enhancing product quality.
These objectives will guide the selection and deployment of the AI system.
Invest in Training and Development
Skilled personnel are essential for the successful implementation and operation of AI-powered visual inspection systems.
Investing in training and development programs ensures that employees are equipped with the necessary skills to manage and maintain the technology.
Focus on Data Quality
High-quality training data is crucial for the effectiveness of AI models.
Manufacturers should prioritize data collection processes that capture accurate and comprehensive images of both defective and defect-free products.
Continuous Monitoring and Improvement
Regular monitoring and evaluation of AI-powered inspection systems are essential to identify performance gaps and opportunities for improvement.
Manufacturers should establish feedback loops to continuously refine and enhance the AI models.
Collaborate with Experts
Partnering with AI solution providers and industry experts can provide valuable insights and support throughout the implementation process.
Collaboration ensures that manufacturers leverage the latest advancements and best practices in AI technology.
Case Studies and Success Stories
Examining real-world examples of AI-powered visual inspection can provide valuable insights into its practical application and benefits.
Case Study: Automotive Industry
An automotive manufacturer implemented AI-powered visual inspection to enhance the quality control of its assembly line.
By using AI to detect defects in components and assemblies, the manufacturer achieved a significant reduction in defect rates, leading to improved customer satisfaction and reduced warranty claims.
Case Study: Electronics Manufacturing
In the electronics industry, a manufacturer adopted AI-powered visual inspection to detect soldering defects in printed circuit boards (PCBs).
The AI system’s ability to identify even the smallest defects resulted in higher product reliability and decreased rework costs.
Case Study: Consumer Goods
A consumer goods manufacturer implemented AI-powered visual inspection to ensure the consistency of product packaging.
The AI system’s accuracy in identifying packaging defects led to enhanced brand reputation and customer trust.
Future Prospects and Innovations
The future of AI-powered visual inspection holds exciting possibilities, driven by ongoing technological advancements and evolving industry demands.
Next-Generation AI Models
The development of next-generation AI models, such as deep learning and neural networks, will further enhance the accuracy and capabilities of visual inspection systems.
These models will be able to handle more complex inspection tasks and deliver even higher levels of precision.
Integration with Other Technologies
AI-powered visual inspection systems will increasingly integrate with other emerging technologies, such as IoT, robotics, and blockchain.
These integrations will create more comprehensive and interconnected quality control solutions.
Expansion into New Industries
While AI-powered visual inspection has already made significant inroads in industries like automotive, electronics, and consumer goods, its adoption will expand into new sectors.
Industries such as pharmaceuticals, aerospace, and food and beverage will increasingly leverage AI for quality assurance.
Enhanced Human-AI Collaboration
Future AI-powered visual inspection systems will facilitate better collaboration between humans and AI.
Advanced interfaces and user-friendly tools will enable employees to easily interact with AI systems, enhancing overall productivity and decision-making.
Conclusion
AI-powered visual inspection represents a transformative leap in the evolution of quality control within Japanese manufacturing.
By harnessing the power of AI, manufacturers can achieve unparalleled levels of accuracy, efficiency, and cost-effectiveness.
While challenges and limitations exist, careful planning, effective supplier negotiations, and adherence to best practices can ensure successful implementation.
As the market for AI-powered visual inspection continues to evolve, manufacturers must stay abreast of emerging trends and innovations to maintain a competitive edge.
Ultimately, the fusion of Japanese manufacturing prowess with cutting-edge AI technology promises a future of superior product quality and sustained excellence.
資料ダウンロード
QCD調達購買管理クラウド「newji」は、調達購買部門で必要なQCD管理全てを備えた、現場特化型兼クラウド型の今世紀最高の購買管理システムとなります。
ユーザー登録
調達購買業務の効率化だけでなく、システムを導入することで、コスト削減や製品・資材のステータス可視化のほか、属人化していた購買情報の共有化による内部不正防止や統制にも役立ちます。
NEWJI DX
製造業に特化したデジタルトランスフォーメーション(DX)の実現を目指す請負開発型のコンサルティングサービスです。AI、iPaaS、および先端の技術を駆使して、製造プロセスの効率化、業務効率化、チームワーク強化、コスト削減、品質向上を実現します。このサービスは、製造業の課題を深く理解し、それに対する最適なデジタルソリューションを提供することで、企業が持続的な成長とイノベーションを達成できるようサポートします。
オンライン講座
製造業、主に購買・調達部門にお勤めの方々に向けた情報を配信しております。
新任の方やベテランの方、管理職を対象とした幅広いコンテンツをご用意しております。
お問い合わせ
コストダウンが利益に直結する術だと理解していても、なかなか前に進めることができない状況。そんな時は、newjiのコストダウン自動化機能で大きく利益貢献しよう!
(Β版非公開)