- お役立ち記事
- Improving Waste Reduction in Manufacturing Sites
Improving Waste Reduction in Manufacturing Sites
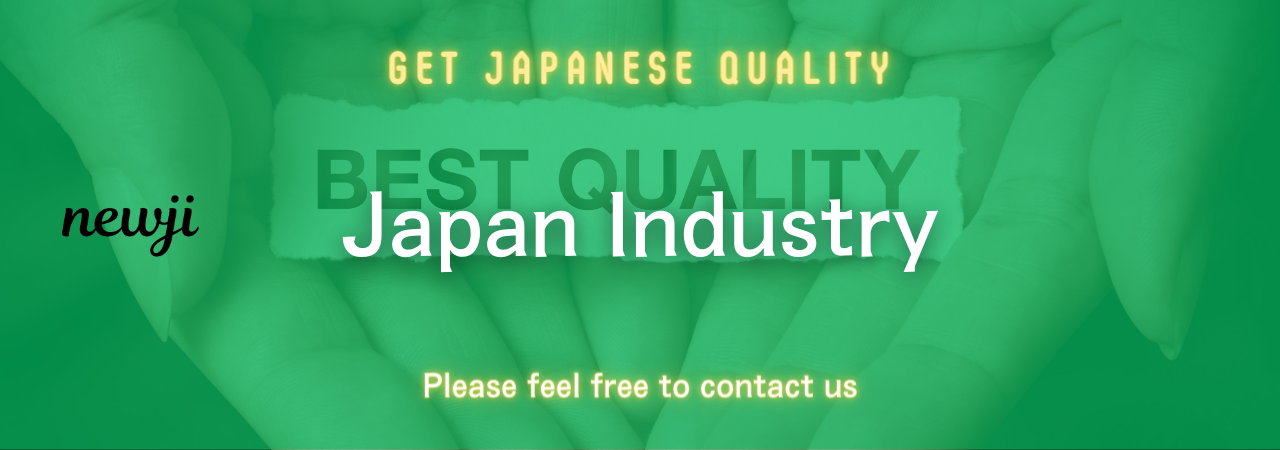
Manufacturers are continually looking for ways to reduce waste and improve efficiency in their production processes.
Reducing waste not only helps the environment but also saves money and increases the overall efficiency of operations.
In this article, we will explore several strategies that manufacturing sites can implement to improve waste reduction.
目次
Understanding Waste in Manufacturing
The first step in reducing waste in manufacturing is understanding the different types of waste that can occur.
Waste can be classified into several categories, including material waste, energy waste, time waste, and resource waste.
By identifying the specific types of waste present, manufacturers can target their efforts more effectively.
Material Waste
Material waste occurs when raw materials are not fully utilized in the production process.
This can happen due to overproduction, defects, or inefficient use of materials.
Material waste not only leads to higher costs but also contributes to environmental pollution.
Energy Waste
Energy waste refers to the inefficient use of energy resources.
This can include excess energy consumption due to outdated equipment, poor maintenance practices, or inefficient production processes.
Reducing energy waste can significantly lower operating costs and reduce a facility’s carbon footprint.
Time Waste
Time waste occurs when production processes are delayed or inefficient.
This can result from poor planning, equipment breakdowns, or inefficient workflows.
Reducing time waste can improve productivity and lead to faster delivery of products to customers.
Resource Waste
Resource waste includes the unnecessary use of resources such as water, chemicals, and labor.
It can also involve the overuse of packaging materials.
By minimizing resource waste, manufacturers can save money and reduce their environmental impact.
Strategies for Reducing Waste in Manufacturing
There are several strategies that manufacturers can employ to reduce waste across their operations.
These strategies focus on improving efficiency, adopting sustainable practices, and utilizing advanced technologies.
Lean Manufacturing
Lean manufacturing is a production methodology that emphasizes the elimination of waste and continuous improvement.
By adopting lean practices, manufacturers can streamline their processes and reduce waste across all areas of production.
Some key principles of lean manufacturing include just-in-time production, continuous improvement, and waste reduction.
Implementing 5S
The 5S method is a lean tool that helps to organize and maintain a clean and efficient workspace.
The five steps of 5S are Sort, Set in Order, Shine, Standardize, and Sustain.
By following these steps, manufacturers can reduce clutter, improve productivity, and minimize waste.
Adopting Sustainable Practices
Sustainable manufacturing practices aim to reduce the environmental impact of production activities.
This can include using renewable energy sources, recycling materials, and reducing emissions.
By adopting sustainable practices, manufacturers can meet regulatory requirements and improve their reputation with environmentally-conscious consumers.
Utilizing Advanced Technologies
Advanced technologies, such as automation and data analytics, can help manufacturers identify and reduce waste.
Automation can improve efficiency by reducing human error and increasing production speed.
Data analytics can provide insights into production processes, helping to identify areas of waste and opportunities for improvement.
Case Studies: Successful Waste Reduction Initiatives
Many manufacturing sites have successfully implemented waste reduction initiatives with positive results.
Here are a few case studies that highlight successful strategies.
Toyota and Lean Manufacturing
Toyota is a well-known example of a company that has successfully implemented lean manufacturing principles.
By focusing on continuous improvement and waste reduction, Toyota has been able to enhance productivity, lower costs, and deliver high-quality products.
The company’s commitment to lean manufacturing has been a key factor in its success and sustainability.
Unilever and Sustainable Practices
Unilever has made significant strides in reducing waste through sustainable manufacturing practices.
The company has set ambitious targets for reducing waste and has implemented initiatives such as zero-waste-to-landfill programs and water-saving technologies.
Unilever’s commitment to sustainability has helped the company reduce its environmental impact and improve its brand image.
GE and Advanced Technologies
General Electric (GE) has utilized advanced technologies to reduce waste in its manufacturing operations.
By implementing automation and data analytics, GE has been able to optimize production processes, reduce energy consumption, and minimize material waste.
The use of advanced technologies has enabled GE to improve efficiency and maintain a competitive edge.
Conclusion
Reducing waste in manufacturing is an essential goal for companies looking to improve efficiency, save costs, and protect the environment.
By understanding the different types of waste and implementing strategies such as lean manufacturing, the 5S method, sustainable practices, and advanced technologies, manufacturers can make significant progress in waste reduction.
Successful case studies from companies like Toyota, Unilever, and GE demonstrate the potential benefits of these initiatives.
Manufacturers that prioritize waste reduction will not only enhance their operations but also contribute to a more sustainable future.
資料ダウンロード
QCD調達購買管理クラウド「newji」は、調達購買部門で必要なQCD管理全てを備えた、現場特化型兼クラウド型の今世紀最高の購買管理システムとなります。
ユーザー登録
調達購買業務の効率化だけでなく、システムを導入することで、コスト削減や製品・資材のステータス可視化のほか、属人化していた購買情報の共有化による内部不正防止や統制にも役立ちます。
NEWJI DX
製造業に特化したデジタルトランスフォーメーション(DX)の実現を目指す請負開発型のコンサルティングサービスです。AI、iPaaS、および先端の技術を駆使して、製造プロセスの効率化、業務効率化、チームワーク強化、コスト削減、品質向上を実現します。このサービスは、製造業の課題を深く理解し、それに対する最適なデジタルソリューションを提供することで、企業が持続的な成長とイノベーションを達成できるようサポートします。
オンライン講座
製造業、主に購買・調達部門にお勤めの方々に向けた情報を配信しております。
新任の方やベテランの方、管理職を対象とした幅広いコンテンツをご用意しております。
お問い合わせ
コストダウンが利益に直結する術だと理解していても、なかなか前に進めることができない状況。そんな時は、newjiのコストダウン自動化機能で大きく利益貢献しよう!
(Β版非公開)