- お役立ち記事
- Integrating Production Processes in Manufacturing with CIM (Computer Integrated Manufacturing)
Integrating Production Processes in Manufacturing with CIM (Computer Integrated Manufacturing)
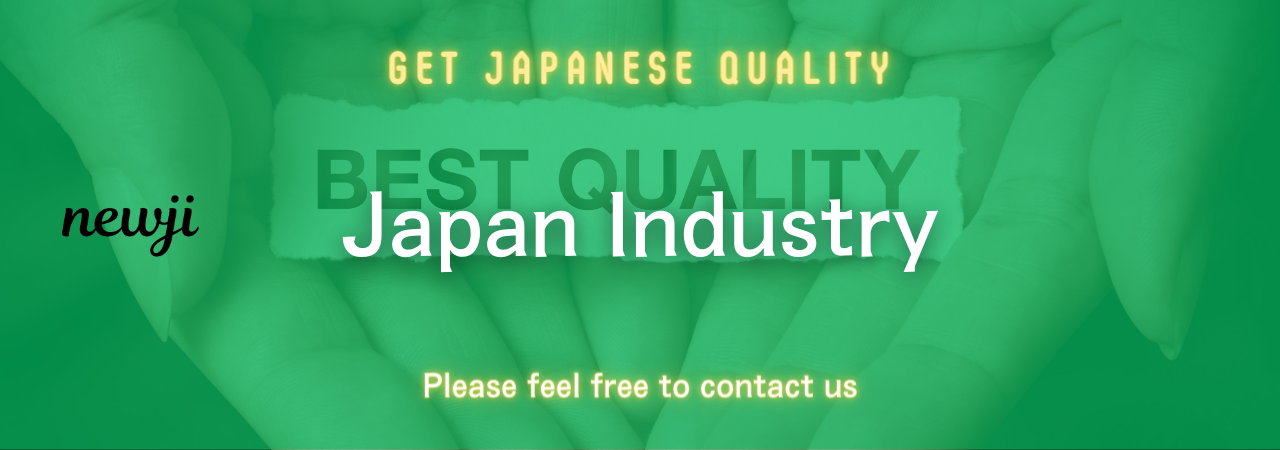
Computer Integrated Manufacturing (CIM) is a crucial concept in the field of manufacturing that leverages computer technology to integrate and streamline various production processes.
In today’s competitive market, manufacturers are constantly seeking ways to enhance efficiency, reduce costs, and improve product quality.
CIM systems offer a solution by blending computer technology with traditional manufacturing operations.
目次
What is Computer Integrated Manufacturing (CIM)?
Computer Integrated Manufacturing (CIM) refers to the utilization of computers to control the entire production process.
This integration allows for the seamless interconnection of various subsystems within a manufacturing facility.
The goal is to create a unified system where all production processes, from design and development to actual manufacturing and quality control, are interconnected.
CIM encompasses various aspects of production, including machine control, robotics, logistics, and even managerial functions such as planning and scheduling.
With a CIM system in place, manufacturers can achieve a higher level of automation, leading to reduced manual intervention and human error.
Key Components of CIM Systems
1. Computer-Aided Design (CAD)
CAD is the use of computer systems to assist in the creation, modification, and optimization of a design.
CAD software allows designers to create 2D and 3D models of products, which can be easily modified and refined without the need for physical prototypes.
This not only saves time and resources but also enhances the accuracy and precision of the designs.
2. Computer-Aided Manufacturing (CAM)
CAM involves the use of computer systems to control and manage manufacturing machinery and processes.
CAM software translates CAD models into instructions for manufacturing equipment, such as CNC machines and robots.
This ensures that the final product is manufactured exactly as designed, with minimal deviations.
3. Robotics
Robotics play a significant role in CIM systems by automating various tasks within the production process.
Robots can perform repetitive and labor-intensive tasks with high precision and consistency, leading to enhanced productivity and quality.
Additionally, robotics can be integrated with other systems, such as CAD and CAM, to create a fully automated manufacturing process.
4. Manufacturing Execution Systems (MES)
MES are software systems that manage and monitor the production process in real-time.
They provide valuable insights into the performance of manufacturing operations, including machine efficiency, production rates, and quality control.
MES systems enable manufacturers to make informed decisions and optimize production processes for maximum efficiency.
5. Enterprise Resource Planning (ERP)
ERP systems integrate various business processes, including procurement, inventory management, production planning, and human resources.
By integrating ERP with CIM, manufacturers can achieve a holistic view of their operations, ensuring that all processes are aligned and working towards common goals.
Benefits of Integrating Production Processes with CIM
1. Improved Efficiency
CIM systems enhance efficiency by automating repetitive and time-consuming tasks.
This reduces the need for manual intervention, allowing workers to focus on more critical and value-added activities.
Automation also ensures that processes are executed consistently and accurately, leading to higher productivity.
2. Cost Reduction
By streamlining production processes and reducing manual labor, CIM systems help lower operational costs.
Automation minimizes errors and rework, reducing material waste and improving resource utilization.
Additionally, real-time monitoring and control enable manufacturers to identify and address inefficiencies promptly.
3. Enhanced Quality
CIM systems contribute to improved product quality by ensuring that manufacturing processes are executed precisely as designed.
Automated systems can detect and correct deviations in real-time, reducing the likelihood of defects and ensuring consistent product quality.
Moreover, detailed data on production processes allows manufacturers to identify and address quality issues proactively.
4. Faster Time-to-Market
CIM systems enable faster design and production cycles, reducing the time required to bring a product to market.
Automation and real-time monitoring allow for quicker adjustments and optimizations, ensuring that products are manufactured efficiently and on schedule.
5. Increased Flexibility
CIM systems offer greater flexibility in manufacturing operations, allowing for quick adjustments to changes in demand or production requirements.
This adaptability is particularly valuable in today’s dynamic market, where manufacturers must respond swiftly to evolving customer needs and preferences.
Challenges of Implementing CIM Systems
1. High Initial Investment
The implementation of CIM systems requires significant investment in hardware, software, and infrastructure.
While the long-term benefits outweigh the initial costs, the upfront expenditure can be a barrier for some manufacturers, particularly small and medium-sized enterprises (SMEs).
2. Technical Complexity
CIM systems involve the integration of various technologies, each with its own set of complexities.
Implementing and maintaining these systems requires specialized knowledge and expertise.
Manufacturers must invest in training and development to ensure that their workforce can effectively operate and manage CIM systems.
3. Risk of Obsolescence
Technology evolves rapidly, and there is always a risk that existing CIM systems may become obsolete.
Manufacturers must stay abreast of technological advancements and be prepared to upgrade or replace their systems to remain competitive.
Conclusion
Integrating production processes in manufacturing with Computer Integrated Manufacturing (CIM) offers numerous benefits, including enhanced efficiency, cost reduction, improved quality, and increased flexibility.
While the implementation of CIM systems presents certain challenges, the long-term advantages make it a worthwhile investment for manufacturers seeking to stay competitive in today’s fast-paced market.
By leveraging CIM technology, manufacturers can achieve a higher level of automation and coordination, ensuring that their operations are optimized for success.
Whether you are a small business or a large enterprise, embracing CIM can lead to significant improvements in your manufacturing processes and overall business performance.
資料ダウンロード
QCD調達購買管理クラウド「newji」は、調達購買部門で必要なQCD管理全てを備えた、現場特化型兼クラウド型の今世紀最高の購買管理システムとなります。
ユーザー登録
調達購買業務の効率化だけでなく、システムを導入することで、コスト削減や製品・資材のステータス可視化のほか、属人化していた購買情報の共有化による内部不正防止や統制にも役立ちます。
NEWJI DX
製造業に特化したデジタルトランスフォーメーション(DX)の実現を目指す請負開発型のコンサルティングサービスです。AI、iPaaS、および先端の技術を駆使して、製造プロセスの効率化、業務効率化、チームワーク強化、コスト削減、品質向上を実現します。このサービスは、製造業の課題を深く理解し、それに対する最適なデジタルソリューションを提供することで、企業が持続的な成長とイノベーションを達成できるようサポートします。
オンライン講座
製造業、主に購買・調達部門にお勤めの方々に向けた情報を配信しております。
新任の方やベテランの方、管理職を対象とした幅広いコンテンツをご用意しております。
お問い合わせ
コストダウンが利益に直結する術だと理解していても、なかなか前に進めることができない状況。そんな時は、newjiのコストダウン自動化機能で大きく利益貢献しよう!
(Β版非公開)