- お役立ち記事
- Importance of quality control documentation and effective implementation techniques
Importance of quality control documentation and effective implementation techniques
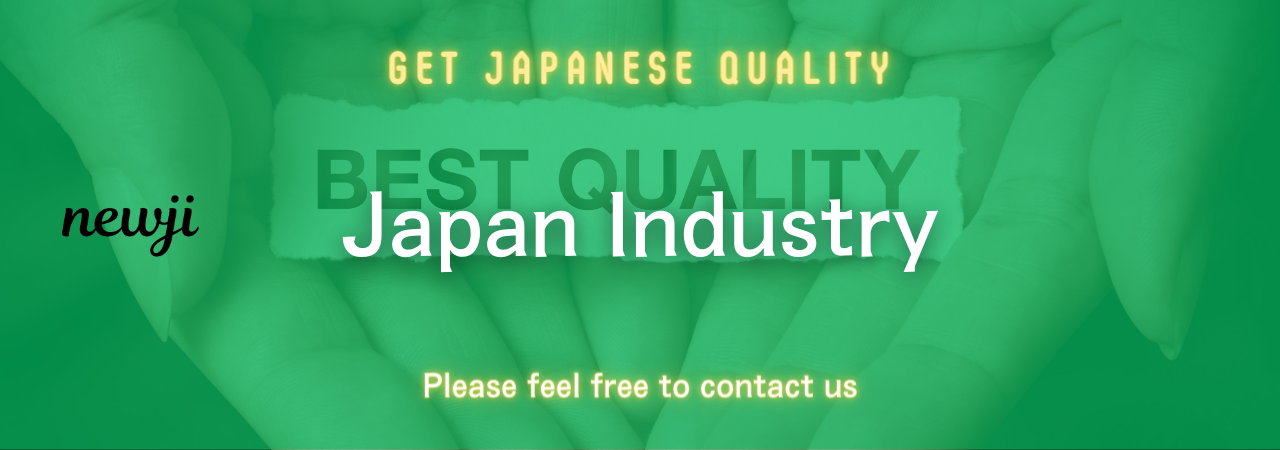
目次
Understanding Quality Control Documentation
Creating and maintaining quality control documentation is crucial for any organization that aims to ensure its products or services meet established standards and customer expectations.
Quality control documentation serves as a tangible record of all procedures and standards used in the production or service process.
When done correctly, it ensures consistency, reliability, and high-quality outcomes.
Proper documentation can also help in identifying and rectifying any issues that may arise.
For example, a manufacturing company might use quality control documents to record daily inspections, testing results, and feedback.
These documents can then be reviewed to identify patterns of defects or inconsistencies.
By addressing these issues promptly, the company can maintain high product quality and customer satisfaction.
Types of Quality Control Documentation
Standard Operating Procedures (SOPs)
Standard Operating Procedures are detailed, written instructions designed to achieve uniformity in the performance of specific functions.
These documents are essential for ensuring that every team member knows how to perform each task correctly.
For instance, in a pharmaceutical company, SOPs would detail how to measure and mix ingredients to ensure consistency in every batch produced.
Inspection Reports
Inspection reports document the results of inspections carried out at various stages of the production process.
These reports can help identify problems early, allowing for corrective actions to be taken before the product reaches the customer.
For example, an inspection report might note a slight variation in color in a batch of textiles, prompting further investigation.
Quality Manuals
A quality manual is a comprehensive document that outlines an organization’s quality policies, procedures, and practices.
It serves as a guide for employees to understand the quality expectations and how to meet them.
For example, the quality manual of an automotive company might cover everything from material selection to final vehicle inspection procedures.
Test Procedures and Test Results
Test procedures and results document the methods used to test products and the outcomes of these tests.
This documentation is crucial for verifying that products meet predefined quality standards.
For instance, a food processing company might perform microbiological tests on its products and record the results to ensure safety and quality.
Effective Implementation of Quality Control Documentation
Train Your Team
To implement quality control documentation effectively, it’s vital to train your team thoroughly.
Provide training sessions that cover the importance of quality control and how to use documentation correctly.
For example, conduct workshops on how to fill out inspection reports accurately, or use e-learning modules for training on SOPs.
Use Digital Tools
Incorporate digital tools to streamline the documentation process and make it more efficient.
Software solutions can help automate documentation, making it easier to update and access records.
For example, use a digital quality management system (QMS) to store and organize documents, ensuring they are easily retrievable when needed.
Regular Audits
Conduct regular audits to ensure all documentation is accurate and up to date.
Audits can help identify areas where improvements are needed and ensure compliance with quality standards.
For example, a monthly audit might reveal gaps in SOP adherence, prompting additional training sessions.
Encourage Feedback
Encourage team members to provide feedback on the quality control documentation process.
Their insights can help identify potential issues and areas for improvement.
For instance, employees might suggest changes to an SOP that make it more effective or easier to follow.
Benefits of Quality Control Documentation
Consistency
Quality control documentation ensures consistency in your products or services.
When everyone follows the same guidelines, the chances of deviations and errors reduce significantly.
For example, consistent use of SOPs in a bakery ensures every loaf of bread tastes the same.
Customer Satisfaction
High-quality products and services lead to increased customer satisfaction.
Quality control documentation helps organizations maintain high standards, which translates to happier customers.
For instance, a tech company that consistently delivers high-performing devices will likely enjoy higher customer satisfaction rates.
Problem Identification
Documentation helps in identifying and addressing problems quickly.
Detailed records make it easier to spot patterns and pinpoint the root causes of issues.
For example, if a factory repeatedly experiences defects in a particular product line, analysis of inspection reports can help identify the problem source.
Compliance
Many industries have strict regulatory requirements, and proper documentation is often essential for compliance.
Maintaining accurate records ensures that your organization meets all necessary regulations.
For instance, a medical device manufacturer must comply with FDA regulations, which require detailed documentation of all production processes.
Challenges in Quality Control Documentation
Time-Consuming
Creating and maintaining quality control documentation can be time-consuming.
This challenge can be mitigated by using digital tools and automating parts of the process.
For example, employing a QMS can save time by automating data entry and report generation.
Resistance to Change
Implementing new documentation practices can meet resistance from employees used to old methods.
Overcome this challenge by involving team members in the development process and highlighting the benefits of new procedures.
For instance, explain how digital documentation can save time and reduce errors.
Keeping Documents Up to Date
Ensuring that all documentation is up to date can be difficult, especially in large organizations.
Regular audits and a dedicated quality control team can help manage this challenge.
For example, set up a quarterly review process to update all relevant documents.
Conclusion
Quality control documentation is vital for maintaining high standards and ensuring customer satisfaction.
By understanding the types of documentation needed and implementing them effectively, organizations can reap numerous benefits, including consistency, problem identification, and compliance.
While challenges exist, they can be mitigated with proper training, digital tools, and regular audits.
Investing time and resources in quality control documentation is a proactive step toward achieving long-term success.
資料ダウンロード
QCD調達購買管理クラウド「newji」は、調達購買部門で必要なQCD管理全てを備えた、現場特化型兼クラウド型の今世紀最高の購買管理システムとなります。
ユーザー登録
調達購買業務の効率化だけでなく、システムを導入することで、コスト削減や製品・資材のステータス可視化のほか、属人化していた購買情報の共有化による内部不正防止や統制にも役立ちます。
NEWJI DX
製造業に特化したデジタルトランスフォーメーション(DX)の実現を目指す請負開発型のコンサルティングサービスです。AI、iPaaS、および先端の技術を駆使して、製造プロセスの効率化、業務効率化、チームワーク強化、コスト削減、品質向上を実現します。このサービスは、製造業の課題を深く理解し、それに対する最適なデジタルソリューションを提供することで、企業が持続的な成長とイノベーションを達成できるようサポートします。
オンライン講座
製造業、主に購買・調達部門にお勤めの方々に向けた情報を配信しております。
新任の方やベテランの方、管理職を対象とした幅広いコンテンツをご用意しております。
お問い合わせ
コストダウンが利益に直結する術だと理解していても、なかなか前に進めることができない状況。そんな時は、newjiのコストダウン自動化機能で大きく利益貢献しよう!
(Β版非公開)