- お役立ち記事
- Procedures and significance of FAI (First Article Inspection) in manufacturing
Procedures and significance of FAI (First Article Inspection) in manufacturing
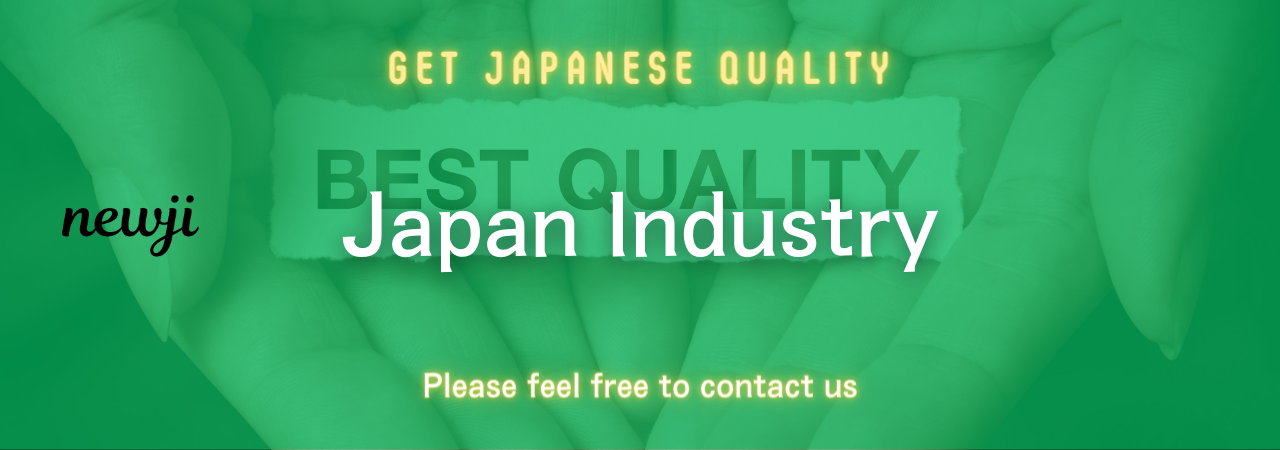
In the world of manufacturing, processes are set in place to ensure product quality and consistency.
One such significant process is First Article Inspection (FAI).
FAI plays a crucial role in the production cycle and helps manufacturers maintain high standards.
Today, we will dive deep into understanding FAI, its procedures, and its importance in the manufacturing industry.
目次
What is First Article Inspection (FAI)?
First Article Inspection (FAI) is a rigorous, detailed examination and testing process carried out on the first item produced in a batch.
This initial item, referred to as the “first article,” is scrutinized to ensure that it meets all specified design and quality requirements.
FAI is not limited to one industry and is widely used in aerospace, automotive, electronics, and other precision-based industries.
The main objective of FAI is to confirm that every aspect of the product aligns with the design specifications before mass production begins.
This process helps to detect and correct any discrepancies early, avoiding potential production issues and ensuring customer satisfaction.
FAI Procedures
The FAI process comprises several key steps that must be carefully followed.
These steps ensure a comprehensive evaluation and validation of the product compared to its design specifications.
1. Planning and Preparation
Before initiating the FAI, a detailed plan is necessary.
The plan includes the inspection criteria, test methods, and measurement tools required for the inspection.
Gathering all relevant design documents, specifications, and drawing plans is essential at this stage.
2. First Article Production
The first actual production piece is manufactured following standard procedures.
This item serves as the “first article” and must be identical in all respects to the specifications outlined in the production documentation.
3. Documentation Review
An in-depth review of all design and manufacturing documents is conducted to verify compliance with the specified requirements.
This includes drawings, bill of materials, and any customer-specific requirements.
Every aspect of the documentation must be rigorously checked to ensure accuracy and completeness.
4. Dimensional Inspection
During this step, a thorough dimensional inspection of the first article is carried out using calibrated measurement tools.
All critical dimensions are measured and compared with the design specifications.
Any deviations are documented, and corrective actions are taken if necessary.
5. Functional Testing
Functional testing ensures that the first article operates as intended.
This step involves simulating real-world conditions and testing the product’s performance.
Failures or deviations are analyzed, and necessary adjustments are made to rectify any issues.
6. Material and Process verification
The materials used in the first article are verified to ensure they meet the specified requirements.
This involves checking certificates of conformity and, if necessary, performing material tests.
Additionally, the manufacturing processes used to produce the first article are evaluated for consistency and compliance.
7. Final Inspection and Approval
Once all inspections and tests are complete, a final review and approval of the first article is conducted.
This step ensures that all identified non-conformities have been addressed, and the first article meets all design and quality requirements.
If approved, the first article serves as a reference for all subsequent production items.
Importance of FAI in Manufacturing
1. Quality Assurance
FAI is vital for ensuring product quality and consistency.
By conducting a thorough inspection and testing of the first article, manufacturers can identify and rectify any potential issues at an early stage.
This proactive approach prevents defects and non-conformities from being carried into mass production, resulting in high-quality final products.
2. Cost Savings
Detecting and addressing issues during the FAI process can help manufacturers avoid costly rework, scrap, and production delays.
By identifying problems early, corrective actions can be taken before full-scale production begins, reducing the risk of producing defective products and minimizing financial losses.
3. Customer Satisfaction
FAI ensures that products meet the customer’s design and quality requirements.
By delivering high-quality, compliant products, manufacturers can enhance customer satisfaction and build long-term relationships.
FAI helps to instill confidence in customers that the manufacturer can consistently deliver reliable products.
4. Compliance with Standards
In many industries, compliance with specific standards and regulations is mandatory.
FAI helps manufacturers meet these requirements by providing documented evidence of product conformity.
This is particularly important in industries such as aerospace and automotive, where safety and reliability are paramount.
5. Process Improvement
The FAI process provides valuable insights into the manufacturing process.
By analyzing the results of the first article inspection, manufacturers can identify areas for improvement and implement corrective actions to enhance their processes.
This continuous improvement approach leads to increased efficiency and overall better production practices.
FAI Documentation
A critical aspect of the FAI process is proper documentation.
The FAI report is a comprehensive document that includes all the inspection and test results, along with any deviations and corrective actions taken.
This report serves as a reference for future production and provides traceability in case of any issues.
The report typically includes the following sections:
1. Part Information
Details about the first article, including part number, description, and revision level.
2. Design Documents
Copies of relevant design drawings, specifications, and other documents used during the FAI process.
3. Dimensional Inspection Results
Detailed measurements of all critical dimensions, along with any deviations and corrective actions.
4. Functional Test Results
Results of all functional tests conducted on the first article, including any issues identified and corrective actions taken.
5. Material Verification
Certificates of conformity and any material test results.
6. Process Verification
Details of the manufacturing processes used, including any evaluations and improvements made.
7. Final Approval
Signatures and approval from responsible parties, confirming that the first article meets all design and quality requirements.
First Article Inspection (FAI) is a crucial step in the manufacturing process.
It ensures that products are produced to the highest quality standards and meet all specified requirements.
Manufacturers can achieve significant benefits by following the FAI procedures, including cost savings, improved customer satisfaction, and compliance with industry standards.
Proper documentation and continuous process improvement are essential to reaping the full benefits of FAI and maintaining a competitive edge in the manufacturing industry.
資料ダウンロード
QCD調達購買管理クラウド「newji」は、調達購買部門で必要なQCD管理全てを備えた、現場特化型兼クラウド型の今世紀最高の購買管理システムとなります。
ユーザー登録
調達購買業務の効率化だけでなく、システムを導入することで、コスト削減や製品・資材のステータス可視化のほか、属人化していた購買情報の共有化による内部不正防止や統制にも役立ちます。
NEWJI DX
製造業に特化したデジタルトランスフォーメーション(DX)の実現を目指す請負開発型のコンサルティングサービスです。AI、iPaaS、および先端の技術を駆使して、製造プロセスの効率化、業務効率化、チームワーク強化、コスト削減、品質向上を実現します。このサービスは、製造業の課題を深く理解し、それに対する最適なデジタルソリューションを提供することで、企業が持続的な成長とイノベーションを達成できるようサポートします。
オンライン講座
製造業、主に購買・調達部門にお勤めの方々に向けた情報を配信しております。
新任の方やベテランの方、管理職を対象とした幅広いコンテンツをご用意しております。
お問い合わせ
コストダウンが利益に直結する術だと理解していても、なかなか前に進めることができない状況。そんな時は、newjiのコストダウン自動化機能で大きく利益貢献しよう!
(Β版非公開)