- お役立ち記事
- Efficient Procurement Guide for Inner Windings
Efficient Procurement Guide for Inner Windings
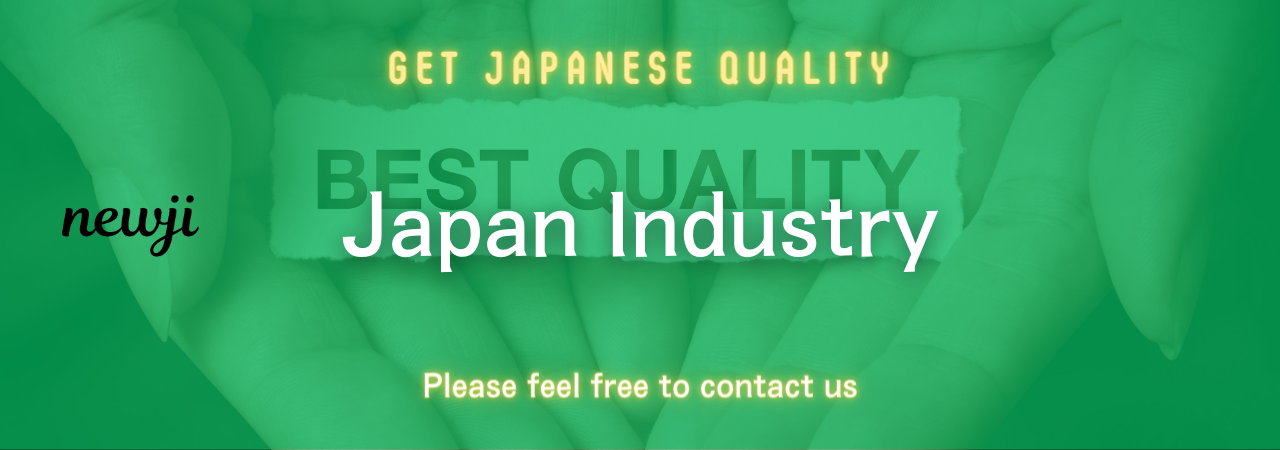
Efficient procurement is crucial for businesses involved in manufacturing, especially those requiring inner windings for transformers, motors, and other electrical components.
Inner windings play a critical role in the functionality and efficiency of these devices.
Therefore, obtaining high-quality materials at the best price is essential.
Here’s an in-depth guide to help you navigate the procurement process for inner windings efficiently.
目次
Understanding Inner Windings
Inner windings refer to the coils within electrical devices responsible for generating magnetic fields or converting electrical energy.
They are usually made from conductive materials like copper or aluminum.
The quality and specifications of these materials can significantly impact the performance and lifespan of electrical devices.
Before diving into procurement, it’s important to have a thorough understanding of the types, materials, and specifications you need.
Types of Inner Windings
There are various types of windings, each serving a unique purpose.
The most common types include:
– **Layered Windings:** Windings arranged in multiple layers, providing better insulation and high efficiency.
– **Helical Windings:** Wound in a helical formation, often used in high-voltage applications.
– **Disc Windings:** Consist of disc-shaped coils, suitable for high-current applications.
Materials Used
The choice of material is crucial for the efficiency of inner windings.
Common materials include:
– **Copper:** Offers excellent conductivity and efficiency but is more expensive.
– **Aluminum:** Less expensive and more lightweight but offers slightly lower conductivity compared to copper.
Setting Clear Specifications
Before reaching out to suppliers, it’s essential to have a clear understanding of the specifications required.
This includes the type of winding, material, dimensions, and other technical parameters.
Clear specifications ensure that you receive exactly what you need, reducing the risk of costly errors.
Technical Parameters
Here are some important technical parameters to consider:
– **Conductor Size:** The size of the conductor affects the winding’s current-carrying capacity.
– **Insulation Type:** The type of insulation used can impact the winding’s durability and performance in different environments.
– **Thermal Rating:** The maximum temperature the winding can handle without degrading.
Compliance and Standards
Ensure your specifications comply with industry standards and regulations.
Compliance ensures the windings are safe, efficient, and durable.
Look for certifications like ISO or UL when selecting materials.
Finding Reliable Suppliers
An efficient procurement process involves finding reliable suppliers who offer high-quality materials at competitive prices.
Here are some steps to help you find the right suppliers:
Conduct Thorough Research
Start by conducting thorough research to identify potential suppliers.
Use online directories, industry forums, and trade shows to gather information.
Compare their offerings, prices, and reputations.
Request for Quotations (RFQs)
Once you have a list of potential suppliers, send out RFQs with detailed specifications.
Compare the quotations based on quality, price, and delivery timelines.
It’s also beneficial to request samples for quality assessment.
Evaluate Supplier Reliability
Evaluate the reliability of suppliers by considering factors like:
– **Experience:** Suppliers with a track record in providing inner windings are more likely to deliver quality products.
– **Certifications:** Ensure the supplier has the necessary certifications.
– **Customer Reviews:** Look at customer feedback and reviews to gauge the supplier’s reputation.
Negotiating Contracts
Effective negotiation is key to securing the best deals.
Here are some tips for negotiating contracts with suppliers:
Discuss Terms Clearly
Clearly discuss the terms of the contract, including pricing, delivery schedules, and payment terms.
Ensure there are no ambiguities to avoid misunderstandings later.
Negotiate for Better Terms
Don’t hesitate to negotiate for better terms.
This could include bulk discounts, longer payment terms, or faster delivery schedules.
Be respectful and professional during negotiations to build a positive relationship with your supplier.
Quality Assurance
Ensuring the quality of inner windings is vital for the efficiency and longevity of your electrical devices.
Here are some steps for quality assurance:
Conduct Regular Inspections
Conduct regular inspections of the windings upon delivery.
Check for any signs of damage, inconsistencies, or defects.
Use tools like multimeters to measure conductivity and resistance.
Test Samples
Request that the supplier provides sample windings for testing before full-scale production.
This allows you to verify the quality and performance of the materials.
Optimizing Inventory Management
Efficient procurement also involves optimizing inventory management.
Proper inventory management ensures a steady supply of materials without overstocking or understocking.
Utilize Inventory Management Software
Use inventory management software to track your stock levels, orders, and deliveries.
This helps in making informed decisions about when to reorder materials.
Implement Just-in-Time (JIT) Inventory
Consider implementing JIT inventory management to reduce holding costs.
This involves ordering materials only when needed, based on production schedules.
Conclusion
Efficient procurement of inner windings requires a thorough understanding of the materials, clear specifications, finding reliable suppliers, negotiating favorable contracts, ensuring quality, and optimizing inventory management.
By following these steps, you can ensure a steady supply of high-quality inner windings, contributing to the efficiency and reliability of your electrical devices.
資料ダウンロード
QCD調達購買管理クラウド「newji」は、調達購買部門で必要なQCD管理全てを備えた、現場特化型兼クラウド型の今世紀最高の購買管理システムとなります。
ユーザー登録
調達購買業務の効率化だけでなく、システムを導入することで、コスト削減や製品・資材のステータス可視化のほか、属人化していた購買情報の共有化による内部不正防止や統制にも役立ちます。
NEWJI DX
製造業に特化したデジタルトランスフォーメーション(DX)の実現を目指す請負開発型のコンサルティングサービスです。AI、iPaaS、および先端の技術を駆使して、製造プロセスの効率化、業務効率化、チームワーク強化、コスト削減、品質向上を実現します。このサービスは、製造業の課題を深く理解し、それに対する最適なデジタルソリューションを提供することで、企業が持続的な成長とイノベーションを達成できるようサポートします。
オンライン講座
製造業、主に購買・調達部門にお勤めの方々に向けた情報を配信しております。
新任の方やベテランの方、管理職を対象とした幅広いコンテンツをご用意しております。
お問い合わせ
コストダウンが利益に直結する術だと理解していても、なかなか前に進めることができない状況。そんな時は、newjiのコストダウン自動化機能で大きく利益貢献しよう!
(Β版非公開)