- お役立ち記事
- Effective purchasing department organization design and management in manufacturing
Effective purchasing department organization design and management in manufacturing
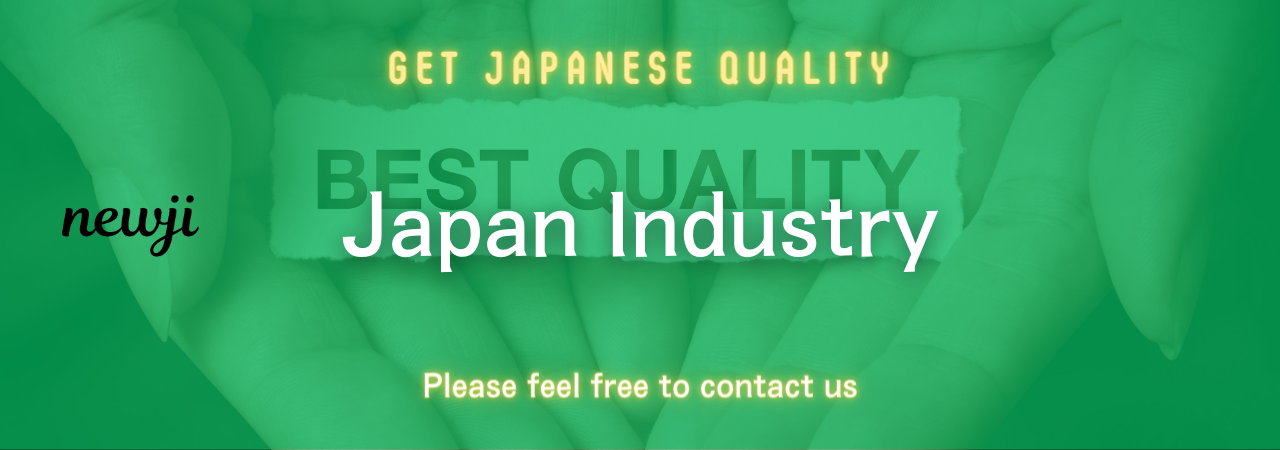
In the dynamic world of manufacturing, having an efficiently organized purchasing department can significantly impact the overall performance and profitability of a company.
A well-structured purchasing department is vital in managing cost control, supplier relationships, and ensuring the continuous flow of materials necessary for production.
This article delves into some key strategies for effective purchasing department organization and management, which can bolster the manufacturing process.
目次
Understanding the Role of the Purchasing Department
The purchasing department is responsible for procuring materials, products, and services needed for manufacturing.
Their role extends beyond merely buying items to managing supplier relationships, negotiating contracts, and ensuring timely delivery of quality materials.
By doing so, they help in maintaining product quality, reducing costs, and contributing to the overall operational efficiency of the manufacturing process.
Structural Organization of the Purchasing Department
Centralized vs. Decentralized Structure
One essential aspect to consider is whether the purchasing function should be centralized or decentralized.
A centralized purchasing department consolidates all procurement activities under one roof, providing uniformity and better control over purchases.
It offers advantages such as economies of scale, improved negotiation power, and consistency in procurement policies.
On the other hand, a decentralized purchasing structure allows individual departments or units within the company to manage their own purchasing needs.
This can lead to more responsive and quicker decision-making, as well as tailored procurement strategies specific to the needs of different departments.
Defining Roles and Responsibilities
Clearly defining roles and responsibilities within the purchasing department is crucial.
Typically, the department may include roles such as purchasing managers, buyers, contract administrators, and supplier relationship managers.
Purchasing managers oversee the department’s operations, ensuring compliance with procurement policies and strategies.
Buyers are tasked with sourcing and negotiating the purchase of materials and services.
Contract administrators manage procurement contracts, ensuring terms and conditions are met by suppliers.
Supplier relationship managers work to maintain and improve relationships with suppliers, fostering cooperation and addressing any issues that may arise.
Implementing Effective Strategies
Supplier Management and Development
An essential strategy for effective purchasing department management involves robust supplier management.
Establishing strong relationships with reliable suppliers can ensure a steady and quality supply of materials, thus reducing production delays.
Developing a supplier performance evaluation system can help in identifying the strengths and weaknesses of suppliers.
This, in turn, aids in making informed decisions regarding future collaborations.
Furthermore, creating a supplier development program can foster better supplier performance.
Training and assisting suppliers in meeting the company’s standards can lead to a more efficient supply chain.
Negotiation and Contract Management
Effective negotiation skills are the backbone of a successful purchasing department.
Negotiating favorable terms can result in cost savings and better material quality.
Continuous training and skill development of the purchasing team in negotiation techniques can yield long-term benefits for the company.
Alongside negotiation, effective contract management is indispensable.
Ensuring that contracts are clear, comprehensive, and beneficial requires attention to detail and a thorough understanding of legal and commercial aspects.
Regularly reviewing contracts can help in identifying any areas that need amendments, ensuring that the company’s interests are always protected.
Utilizing Technology
Leveraging technology is critical in today’s competitive manufacturing environment.
Implementing procurement software can streamline the purchasing process, providing real-time data, and facilitating better decision-making.
Such software can automate routine tasks, manage vendor data, track orders, and generate reports, thereby enhancing the efficiency and productivity of the purchasing department.
Additionally, using data analytics can help in identifying trends, forecasting demands, and optimizing inventory management.
Predictive analytics, for instance, can provide insights into future material requirements, helping in better planning and resource allocation.
Cost Control and Financial Management
Budgeting and Financial Planning
Effective cost control begins with meticulous budgeting and financial planning.
Setting clear budgets for procurement activities helps in monitoring expenses and identifying any deviations at an early stage.
Regular financial analysis and auditing ensure that the purchasing department stays within budgetary constraints and contributes to the company’s financial health.
Inventory Management
Efficient inventory management is another critical aspect of cost control.
Maintaining the right balance between excess and shortage is key.
Excess inventory ties up capital and increases storage costs, while shortages can disrupt production and lead to missed opportunities.
Implementing an inventory management system that tracks stock levels and turnover rates can help in maintaining optimal inventory levels.
Just-in-time inventory systems, for instance, can reduce the holding costs by ordering materials only when needed for production.
Developing a Skilled Purchasing Team
Investing in the development of the purchasing team is essential for sustained success.
Providing continuous training on market trends, negotiation skills, and the use of procurement technologies can enhance the team’s capabilities.
Encouraging professional certifications and memberships in relevant industry associations can also foster a culture of continuous improvement and professional growth.
Aligning Purchasing Strategies with Organizational Goals
Finally, ensuring that the purchasing strategies align with the broader organizational goals is crucial.
Collaborating with other departments, such as production, finance, and quality control, can provide a comprehensive understanding of the organization’s needs and priorities.
This holistic approach ensures that the purchasing department contributes positively to the company’s overall objectives, driving long-term success.
In conclusion, effective purchasing department organization and management are pivotal in the manufacturing sector.
By implementing a well-defined structure, leveraging technology, managing supplier relations, controlling costs, and developing a skilled team, companies can significantly enhance their operational efficiency and profitability.
The strategic alignment of purchasing activities with organizational goals ultimately drives success in the competitive manufacturing landscape.
資料ダウンロード
QCD調達購買管理クラウド「newji」は、調達購買部門で必要なQCD管理全てを備えた、現場特化型兼クラウド型の今世紀最高の購買管理システムとなります。
ユーザー登録
調達購買業務の効率化だけでなく、システムを導入することで、コスト削減や製品・資材のステータス可視化のほか、属人化していた購買情報の共有化による内部不正防止や統制にも役立ちます。
NEWJI DX
製造業に特化したデジタルトランスフォーメーション(DX)の実現を目指す請負開発型のコンサルティングサービスです。AI、iPaaS、および先端の技術を駆使して、製造プロセスの効率化、業務効率化、チームワーク強化、コスト削減、品質向上を実現します。このサービスは、製造業の課題を深く理解し、それに対する最適なデジタルソリューションを提供することで、企業が持続的な成長とイノベーションを達成できるようサポートします。
オンライン講座
製造業、主に購買・調達部門にお勤めの方々に向けた情報を配信しております。
新任の方やベテランの方、管理職を対象とした幅広いコンテンツをご用意しております。
お問い合わせ
コストダウンが利益に直結する術だと理解していても、なかなか前に進めることができない状況。そんな時は、newjiのコストダウン自動化機能で大きく利益貢献しよう!
(Β版非公開)