- お役立ち記事
- High-Precision Products through OEM Ion Beam Etching Processing
High-Precision Products through OEM Ion Beam Etching Processing
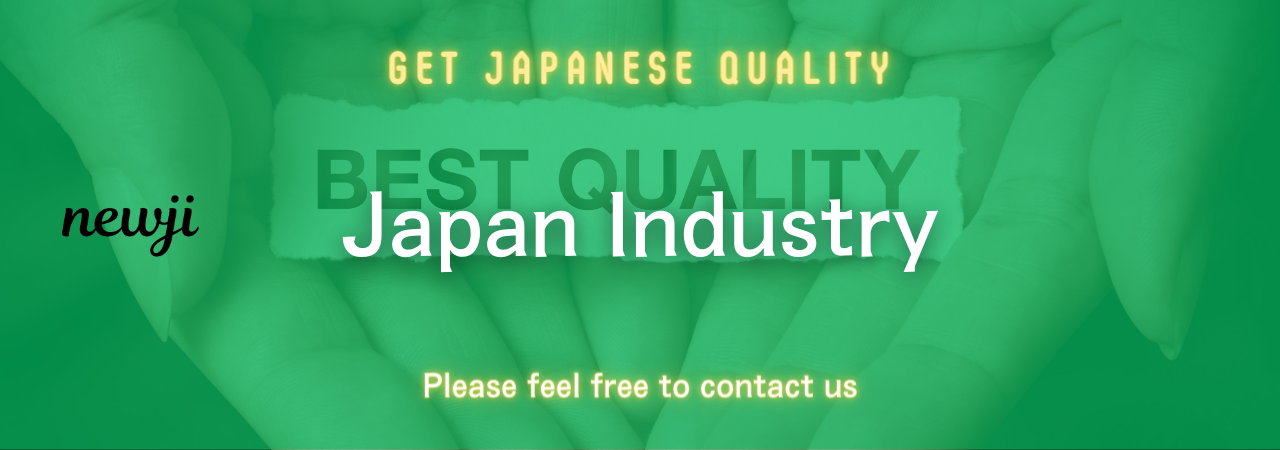
目次
Understanding OEM Ion Beam Etching
OEM Ion Beam Etching (IBE) is a versatile and highly precise technique used in various industries.
It involves the use of a focused ion beam to remove material from a surface at the atomic level.
This process is vital for creating intricate patterns and features on a wide range of substrates.
In the context of Original Equipment Manufacturing (OEM), IBE is indispensable for achieving the high standards of quality and precision required for developing advanced products.
From semiconductor devices to optical components, the efficacy of IBE ensures that products meet exacting specifications.
How Does Ion Beam Etching Work?
Ion Beam Etching relies on a stream of ions accelerated towards a target material.
The ions impinge on the surface, dislodging atoms or molecules in a tightly controlled manner.
This allows for the creation of features with nanometer-scale precision.
The ion source generates ions from gases, such as argon or oxygen.
These ions are then accelerated through an electric field and focused onto the target material.
The angle and energy of the ion beam can be precisely controlled to achieve the desired etching profile.
Advantages of Ion Beam Etching
One of the primary advantages of Ion Beam Etching is its ability to produce highly precise and intricate patterns.
Unlike other etching techniques, IBE does not rely on chemical reactions or masks, enabling direct etching of the target material.
This results in high fidelity features and the capability to etch a wide range of materials.
Another significant advantage is the flexibility of the process.
It can be utilized on various substrates, including metals, semiconductors, and dielectrics.
Additionally, IBE can achieve very fine line widths and pattern resolutions, making it ideal for applications that require nanoscale precision.
Applications in High-Tech Industries
The use of OEM Ion Beam Etching spans numerous high-tech industries.
In the semiconductor industry, IBE is crucial for manufacturing microprocessors, memory chips, and other integrated circuits.
The precision of IBE ensures that these components function correctly and reliably.
In the optics and photonics sectors, IBE is used to create intricate patterns on optical lenses and waveguides.
These components are essential for devices such as cameras, lasers, and fiber-optic communication systems.
The high level of control offered by IBE allows for the fabrication of components with exceptional performance characteristics.
Medical Devices and Biotechnology
Ion Beam Etching also finds applications in the medical and biotechnology fields.
For instance, it is used to create microarrays, which are critical for genetic testing and research.
The ability to etch fine features allows for the high-throughput analysis of biological samples.
In the development of medical implants, IBE can be used to improve the surface properties of materials.
This includes creating textured surfaces that enhance biocompatibility and promote better integration with biological tissues.
Enhancing Product Quality with OEM Ion Beam Etching
The integration of OEM Ion Beam Etching into the manufacturing process brings numerous benefits.
One of the most significant is the enhancement of product quality.
By utilizing IBE, manufacturers can achieve finer detail and tighter tolerances, resulting in products that perform better and last longer.
Furthermore, the precision of IBE minimizes the need for extensive post-processing.
This reduces production time and costs, leading to a more efficient manufacturing process.
The ability to directly etch a wide range of materials also broadens the scope of possible product designs.
Customization and Innovation
OEM Ion Beam Etching allows for a high degree of customization and innovation.
Manufacturers can tailor the etching process to meet specific requirements, enabling the development of unique products.
This is particularly valuable in industries where differentiation and performance are critical.
The ability to create complex patterns and structures opens up new possibilities for product development.
From advanced microelectronics to cutting-edge medical devices, IBE enables manufacturers to push the boundaries of what is possible.
Challenges and Considerations
While OEM Ion Beam Etching offers numerous advantages, it also presents certain challenges.
The process requires specialized equipment and expertise, which can be a significant investment for manufacturers.
Additionally, the high precision of IBE means that even small deviations can impact the final product quality.
Another consideration is the need for a clean and controlled environment.
Ion Beam Etching is sensitive to contamination, which can affect the etching process and result in defects.
Maintaining a cleanroom environment is crucial for ensuring consistent and reliable results.
Future Outlook
The demand for high-precision products continues to grow, driving advancements in Ion Beam Etching technology.
Future developments are likely to focus on improving the efficiency and versatility of the process.
This includes the integration of advanced ion sources and beam control systems to enhance etching performance.
Additionally, the expansion of IBE applications into new industries is anticipated.
Emerging fields such as nanotechnology and advanced materials science are expected to benefit from the precision and flexibility of Ion Beam Etching.
Conclusion
OEM Ion Beam Etching is a powerful tool for achieving high-precision products across a range of industries.
Its ability to create intricate patterns and features with nanometer-scale accuracy makes it indispensable for advanced manufacturing.
As technology continues to evolve, the role of IBE in producing innovative and high-quality products is set to grow further.
By understanding the benefits and challenges of Ion Beam Etching, manufacturers can leverage this technique to enhance product quality and drive innovation.
With its wide range of applications and potential for customization, OEM Ion Beam Etching remains at the forefront of precision manufacturing.
資料ダウンロード
QCD調達購買管理クラウド「newji」は、調達購買部門で必要なQCD管理全てを備えた、現場特化型兼クラウド型の今世紀最高の購買管理システムとなります。
ユーザー登録
調達購買業務の効率化だけでなく、システムを導入することで、コスト削減や製品・資材のステータス可視化のほか、属人化していた購買情報の共有化による内部不正防止や統制にも役立ちます。
NEWJI DX
製造業に特化したデジタルトランスフォーメーション(DX)の実現を目指す請負開発型のコンサルティングサービスです。AI、iPaaS、および先端の技術を駆使して、製造プロセスの効率化、業務効率化、チームワーク強化、コスト削減、品質向上を実現します。このサービスは、製造業の課題を深く理解し、それに対する最適なデジタルソリューションを提供することで、企業が持続的な成長とイノベーションを達成できるようサポートします。
オンライン講座
製造業、主に購買・調達部門にお勤めの方々に向けた情報を配信しております。
新任の方やベテランの方、管理職を対象とした幅広いコンテンツをご用意しております。
お問い合わせ
コストダウンが利益に直結する術だと理解していても、なかなか前に進めることができない状況。そんな時は、newjiのコストダウン自動化機能で大きく利益貢献しよう!
(Β版非公開)