- お役立ち記事
- DXing of the joint leaving process ensures uniformity in product quality
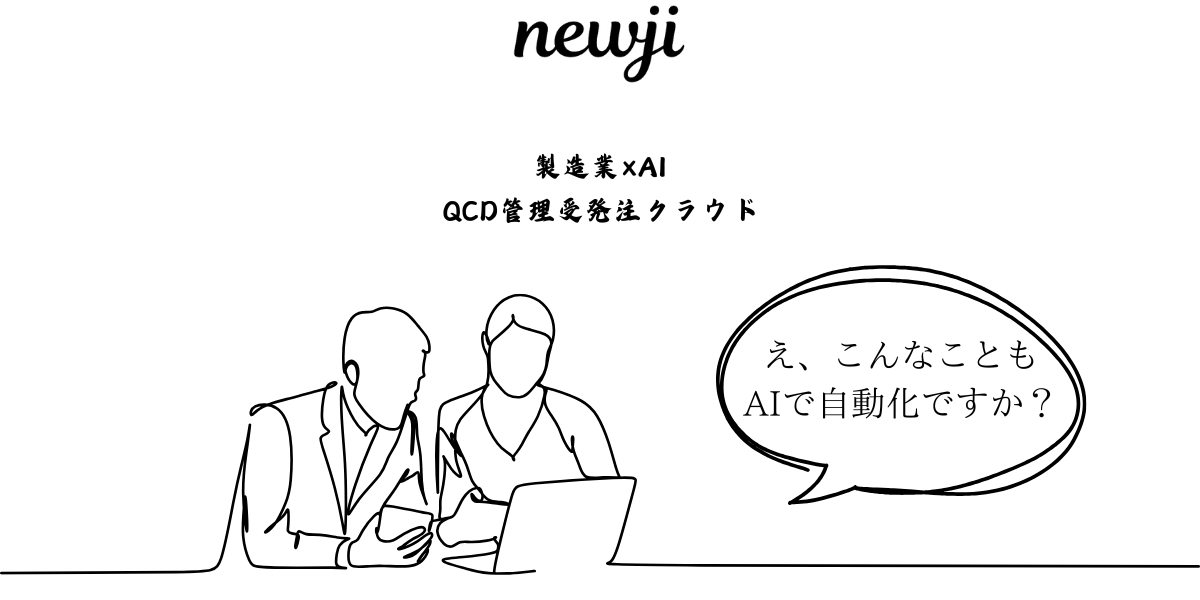
DXing of the joint leaving process ensures uniformity in product quality
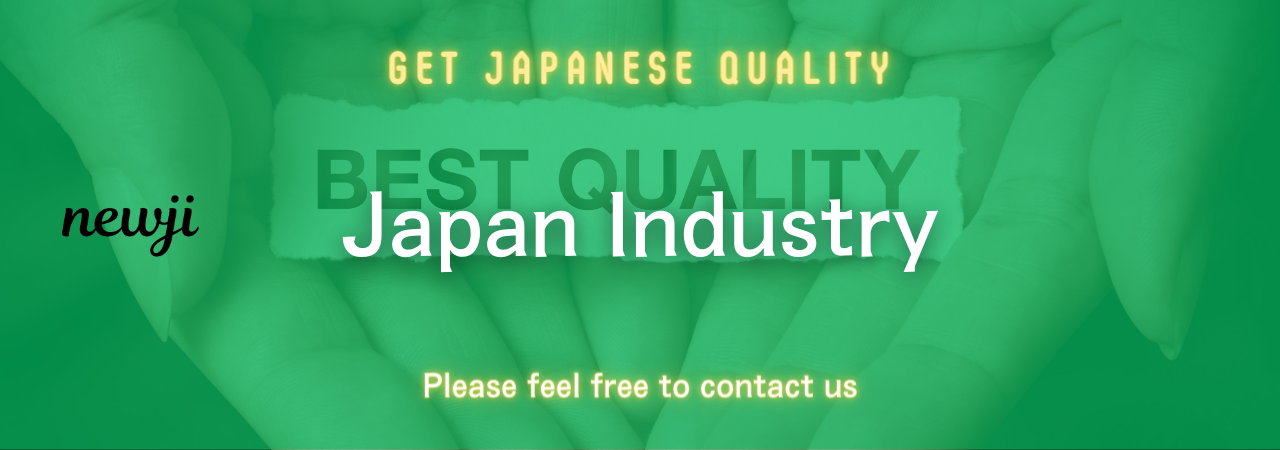
In today’s competitive market, maintaining a high level of product quality is crucial for any manufacturing operation. One of the critical processes that ensure product quality is the joint leaving process. Digital transformation (DX) of the joint leaving process can ensure uniformity in product quality, boosting efficiency, reducing costs, and meeting the ever-increasing customer expectations.
目次
Understanding the Joint Leaving Process
The joint leaving process is a vital step in the manufacturing of products, especially in industries like automotive, aerospace, electronics, and construction. This process involves the precise joining of different components to create a finished product. Ensuring uniformity in this stage is critical to the overall quality and performance of the final product.
Traditionally, the joint leaving process has been monitored and controlled manually by skilled technicians. However, this manual approach often results in inconsistencies due to human error, varying levels of skill, and fatigue. Digital transformation of this process introduces advanced technologies like sensors, artificial intelligence (AI), and data analytics to maintain strict control and uniformity.
Why Digital Transformation (DX) is Essential
Embracing DX in the joint leaving process brings numerous benefits that significantly improve product quality and operational efficiency.
Automation and Precision
Automation technologies like robotic arms and programmable logic controllers (PLCs) can perform repetitive tasks with high precision, reducing the risk of human error. Automated systems can also work round the clock, maintaining consistent quality without breaks or fatigue-related performance drops.
Real-Time Monitoring and Control
Implementing sensors and Internet of Things (IoT) devices allows for real-time monitoring of the joint leaving process. These devices can collect data on critical parameters like temperature, pressure, and alignment. This data is then analyzed using AI to ensure that each joint meets the required quality standards. Any deviation can be detected and corrected immediately, preventing defects.
Data-Driven Decision Making
With digital transformation, vast amounts of data are generated and stored. This data can be analyzed to identify trends, predict potential issues, and optimize the process. For example, machine learning algorithms can identify patterns in joint defects and recommend adjustments to the process, ensuring uniformity in product quality.
Implementing DX in the Joint Leaving Process
To successfully implement digital transformation in the joint leaving process, manufacturers need to follow a systematic approach.
Assessment and Planning
The first step is to assess the current state of the joint leaving process. Identify the manual tasks that can be automated and the critical parameters that need monitoring. Develop a detailed plan outlining the technologies to be implemented, the expected benefits, and a timeline for execution.
Technology Selection
Choose the right technologies that fit your needs and budget. This may include robotic arms for automation, IoT sensors for monitoring, and software platforms for data analytics. Ensure that these technologies are compatible and can be integrated seamlessly into your existing systems.
Integration and Testing
Integrating new technologies into the manufacturing line can be challenging. Start with a pilot project to identify any issues and gather feedback. Test the system thoroughly to ensure it performs as expected and meets quality standards. Make necessary adjustments and improvements before a full-scale rollout.
Staff Training
Even with advanced technologies, skilled technicians are essential for overseeing the process. Provide comprehensive training to your staff on using new tools and interpreting data. Encourage a culture of continuous improvement and adaptability.
Benefits of DX in Joint Leaving Process
Implementing digital transformation in the joint leaving process offers numerous advantages that contribute to uniformity in product quality.
Consistency and Reliability
Automated systems can perform tasks with high accuracy and repeatability, ensuring consistent quality in every product. Real-time monitoring helps identify and correct deviations immediately, reducing the occurrence of defects.
Enhanced Efficiency
Automation reduces the time required for the joint leaving process, increasing overall production efficiency. By minimizing human intervention, manufacturers can achieve faster turnaround times and meet tight deadlines.
Cost Savings
Reducing defects and waste leads to significant cost savings. Manufacturers can produce high-quality products with fewer materials and resources, maximizing profitability. Additionally, predictive maintenance powered by data analytics can prevent costly breakdowns and downtime.
Competitive Advantage
Consistently delivering high-quality products builds trust and reputation in the market. Manufacturers that embrace digital transformation can differentiate themselves from competitors, attract more customers, and secure long-term success.
Real-World Examples
Many leading manufacturers have successfully implemented digital transformation in their joint leaving processes.
Automotive Industry
In the automotive industry, manufacturers like Toyota and BMW have integrated robotics and IoT sensors in their assembly lines. These technologies ensure precise welding and fitting of components, resulting in high-quality vehicles with fewer defects.
Aerospace Industry
Aircraft manufacturers like Boeing and Airbus rely on advanced automation to assemble complex components. Real-time monitoring systems track the condition of joints and detect any anomalies, ensuring the safety and reliability of aircraft.
Electronics Industry
Companies like Apple and Samsung use robotic arms and AI-driven inspection systems to assemble and test electronic devices. This approach guarantees consistent performance and durability in their products.
Future Trends in the Joint Leaving Process
The digital transformation of the joint leaving process is continuously evolving, with new trends emerging to further enhance product quality.
Artificial Intelligence and Machine Learning
AI and machine learning will play an increasingly significant role in optimizing the joint leaving process. These technologies can analyze vast amounts of data and make real-time adjustments to improve quality and efficiency.
Augmented Reality (AR)
AR can provide real-time guidance and visualization to technicians, ensuring precise alignment and assembly of components. This technology can also be used for remote inspections and troubleshooting, reducing the need for on-site visits.
Blockchain Technology
Blockchain can enhance transparency and traceability in the joint leaving process. By creating a tamper-proof record of each stage, manufacturers can ensure accountability and detect any issues in the supply chain.
Digital transformation of the joint leaving process is essential for ensuring uniformity in product quality. By embracing advanced technologies like automation, IoT, and AI, manufacturers can achieve consistent, high-quality results, enhance efficiency, and gain a competitive edge in the market.
Start your digital transformation journey today and unlock the full potential of your manufacturing operations.
資料ダウンロード
QCD調達購買管理クラウド「newji」は、調達購買部門で必要なQCD管理全てを備えた、現場特化型兼クラウド型の今世紀最高の購買管理システムとなります。
ユーザー登録
調達購買業務の効率化だけでなく、システムを導入することで、コスト削減や製品・資材のステータス可視化のほか、属人化していた購買情報の共有化による内部不正防止や統制にも役立ちます。
NEWJI DX
製造業に特化したデジタルトランスフォーメーション(DX)の実現を目指す請負開発型のコンサルティングサービスです。AI、iPaaS、および先端の技術を駆使して、製造プロセスの効率化、業務効率化、チームワーク強化、コスト削減、品質向上を実現します。このサービスは、製造業の課題を深く理解し、それに対する最適なデジタルソリューションを提供することで、企業が持続的な成長とイノベーションを達成できるようサポートします。
オンライン講座
製造業、主に購買・調達部門にお勤めの方々に向けた情報を配信しております。
新任の方やベテランの方、管理職を対象とした幅広いコンテンツをご用意しております。
お問い合わせ
コストダウンが利益に直結する術だと理解していても、なかなか前に進めることができない状況。そんな時は、newjiのコストダウン自動化機能で大きく利益貢献しよう!
(Β版非公開)