- お役立ち記事
- Effective purchasing budget management in manufacturing
Effective purchasing budget management in manufacturing
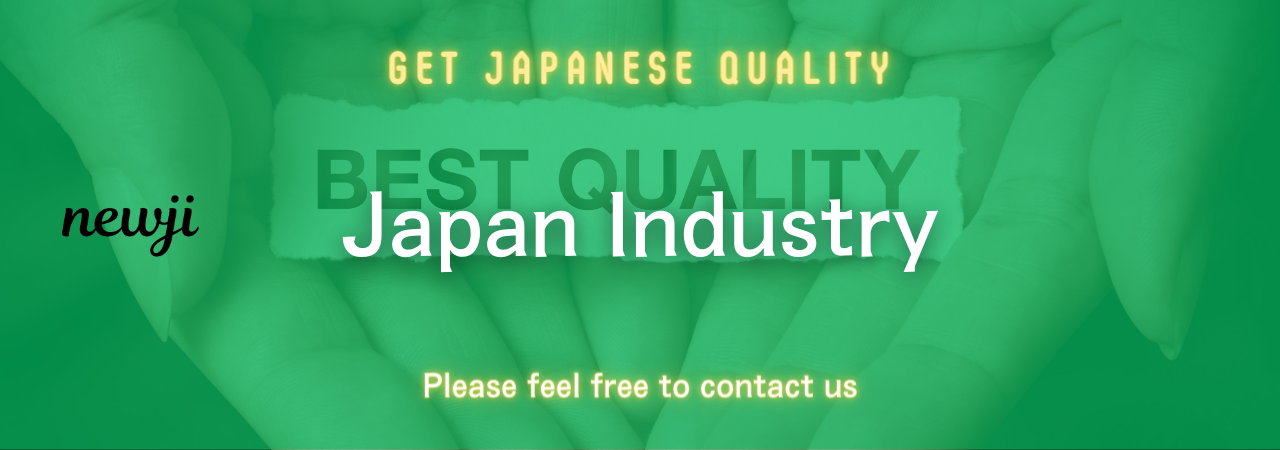
Managing a purchasing budget effectively is crucial in the manufacturing industry. Without a well-managed budget, costs can quickly spiral out of control, impacting profitability and operational efficiency.
In this guide, we’ll explore strategies and tips to ensure that your manufacturing purchasing budget remains in check while supporting productivity and growth.
目次
Understanding the Importance of Purchasing Budget Management
Purchasing budget management in manufacturing involves planning, monitoring, and controlling the money spent on materials, supplies, and services needed for production.
A well-structured budget helps in predicting costs, allocating resources efficiently, and avoiding overspending.
The Role of Budgets in Manufacturing
Budgets serve as a roadmap for financial planning.
They outline expected expenses and help companies prepare for future costs.
In manufacturing, budgets are particularly important because they guide decisions regarding procurement and inventory management.
A good budget ensures that funds are available for essential items while avoiding unnecessary expenditures.
Key Benefits of Effective Budget Management
1. **Cost Control:** Ensures spending stays within limits and helps avoid financial pitfalls.
2. **Resource Allocation:** Allows for better distribution of funds across various departments or projects.
3. **Improved Negotiations:** With a clear budget, purchasing managers can negotiate better terms and prices with suppliers.
4. **Enhanced Productivity:** Guarantees that all necessary materials are available when needed, keeping production lines running smoothly.
Steps to Create an Effective Purchasing Budget
Creating a robust purchasing budget requires careful planning and consideration of various factors.
Here are some steps to follow:
1. Analyze Historical Data
Start by looking at past spending patterns.
Review previous budgets, purchase orders, and invoices to identify trends and areas of overspending.
This historical data provides a foundation for creating a more accurate budget.
2. Identify Needs and Priorities
List all the items and services that will be needed for the upcoming production cycles.
Prioritize these needs based on their importance and urgency.
This step helps in allocating funds appropriately and ensures that critical items are procured first.
3. Set Clear Objectives
Outline clear objectives for your purchasing budget.
These objectives could include reducing costs, improving supplier relationships, or increasing the efficiency of the procurement process.
Having clear goals helps maintain focus and measure success.
4. Estimate Costs
Based on the identified needs, estimate the costs for each item or service.
Consider factors like market trends, supplier pricing, and potential economic changes that could impact costs.
5. Allocate Funds
Distribute the budget across different categories based on the priorities.
Make sure to allocate a portion of the budget for unexpected expenses.
This contingency fund helps in handling unforeseen costs without disrupting the entire budget.
6. Monitor and Adjust
Budget management is an ongoing process.
Regularly monitor actual spending against the budgeted amounts.
If discrepancies arise, adjust the budget accordingly.
This continuous monitoring helps in keeping the budget on track and making informed decisions.
Tips for Effective Purchasing Budget Management
Even with a well-structured budget, management can present challenges.
Here are some tips to streamline the process:
1. Foster Strong Supplier Relationships
Building good relationships with suppliers can lead to better prices, favorable terms, and reliable deliveries.
Long-term partnerships often result in cost savings and better service.
2. Implement a Purchase Approval Process
Establish a system where all purchases need to be approved by relevant authorities.
This step helps in controlling spending and ensuring that all expenditures are necessary and within the budget.
3. Use Technology
Leverage technology for budget management.
There are various software tools available that can help in tracking expenses, generating reports, and forecasting future costs.
These tools enhance accuracy and efficiency in managing the budget.
4. Train Your Team
Ensure that all team members involved in the procurement process are trained in budget management.
This training includes understanding the importance of budgeting, how to track expenses, and the procedures for requesting purchases.
An informed team contributes to effective budget management.
5. Conduct Regular Audits
Regular audits of the purchasing process can help in identifying areas for improvement.
These audits ensure compliance with the budget and help in detecting any discrepancies early.
Common Challenges in Budget Management and How to Overcome Them
Despite best efforts, managing a purchasing budget can be challenging.
Here are some common issues and solutions:
1. Fluctuating Material Costs
Material costs can vary due to market conditions, impacting the budget.
To mitigate this, consider locking in prices with suppliers through long-term contracts.
Additionally, keep an eye on market trends to anticipate price changes.
2. Unexpected Expenses
Unplanned expenses can throw the budget off track.
Having a contingency fund within the budget can help address unanticipated costs without disrupting overall financial plans.
3. Inaccurate Forecasting
Inaccurate predictions can lead to budget shortfalls.
Use historical data and market analysis to improve forecasting accuracy.
Regularly review and update forecasts to reflect current conditions.
4. Inefficient Procurement Processes
Slow or inefficient procurement processes can lead to delays and increased costs.
Streamline processes by using technology and automating where possible.
Ensure that there are clear procedures for making and approving purchases.
Conclusion
Effective purchasing budget management is essential for the success of any manufacturing operation.
By understanding the importance of budgeting, following structured steps to create a budget, and implementing best practices, companies can control costs, improve efficiency, and support business growth.
Regular monitoring, strong supplier relationships, and the use of technology are key elements in maintaining a robust purchasing budget.
資料ダウンロード
QCD調達購買管理クラウド「newji」は、調達購買部門で必要なQCD管理全てを備えた、現場特化型兼クラウド型の今世紀最高の購買管理システムとなります。
ユーザー登録
調達購買業務の効率化だけでなく、システムを導入することで、コスト削減や製品・資材のステータス可視化のほか、属人化していた購買情報の共有化による内部不正防止や統制にも役立ちます。
NEWJI DX
製造業に特化したデジタルトランスフォーメーション(DX)の実現を目指す請負開発型のコンサルティングサービスです。AI、iPaaS、および先端の技術を駆使して、製造プロセスの効率化、業務効率化、チームワーク強化、コスト削減、品質向上を実現します。このサービスは、製造業の課題を深く理解し、それに対する最適なデジタルソリューションを提供することで、企業が持続的な成長とイノベーションを達成できるようサポートします。
オンライン講座
製造業、主に購買・調達部門にお勤めの方々に向けた情報を配信しております。
新任の方やベテランの方、管理職を対象とした幅広いコンテンツをご用意しております。
お問い合わせ
コストダウンが利益に直結する術だと理解していても、なかなか前に進めることができない状況。そんな時は、newjiのコストダウン自動化機能で大きく利益貢献しよう!
(Β版非公開)