- お役立ち記事
- DX of Oxidation Process Ensures Reliability of Semiconductor Operation
DX of Oxidation Process Ensures Reliability of Semiconductor Operation
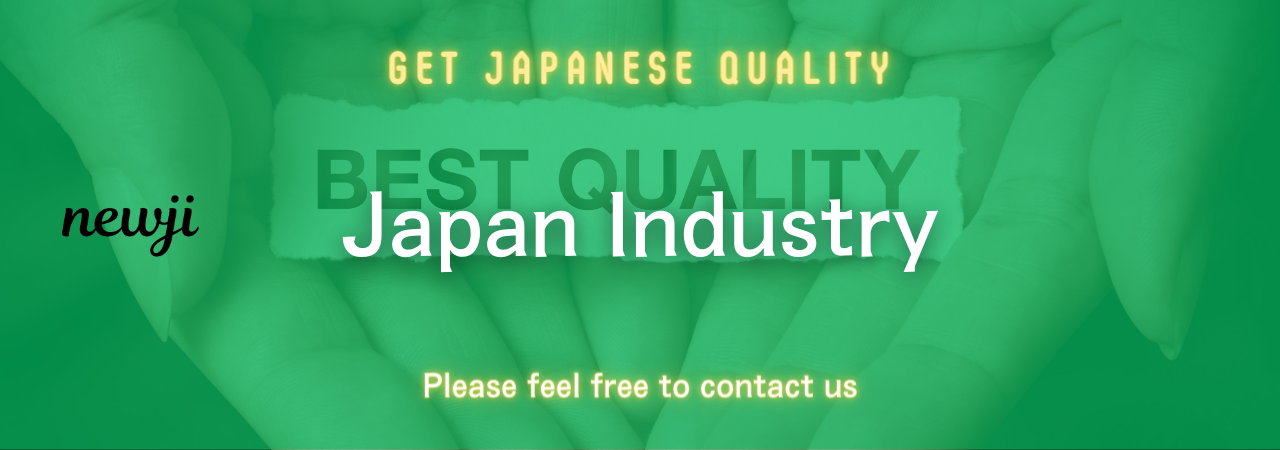
With the continuous advancements in technology, the semiconductor industry remains key to powering a range of devices from smartphones to complex computer systems.
However, achieving reliable performance in semiconductor operations hinges on a finely tuned manufacturing process, with oxidation playing a critical role.
In recent years, the Digital Transformation (DX) of the oxidation process has become an essential factor in ensuring the reliability and efficiency of semiconductor operations.
目次
Understanding Oxidation in Semiconductors
Oxidation is a chemical process in which a material, typically silicon in semiconductor manufacturing, reacts with oxygen to form silicon dioxide.
This process creates an insulating layer that is vital for device functionality and reliability.
While it seems simple, the oxidation process demands precise control to achieve the desired properties.
Any variation can lead to reduced device performance or even failure.
The Importance of Oxidation
The oxidation layer acts as an insulator, providing electrical isolation between different components of the semiconductor.
A high-quality oxide layer ensures that there is minimal leakage current, which is crucial for the device’s efficiency and longevity.
Moreover, the thickness and uniformity of this layer need to be meticulously controlled.
A deviation can significantly impact the transistor’s threshold voltage and, consequently, the overall device performance.
Challenges in Traditional Oxidation Processes
Traditional oxidation processes often rely on manual control and monitoring, introducing a degree of variability and inconsistency.
These methods can be labor-intensive and prone to human error.
As technology nodes shrink, the room for error becomes minimal.
Therefore, semiconductor manufacturers are adopting more advanced methods to control and monitor the oxidation process, ensuring greater accuracy and reproducibility.
Manual Intervention and Its Pitfalls
In manual oxidation processes, operators oversee the conditions within the oxidation furnace, adjusting parameters based on experience and visual cues.
This introduces a significant risk of subjective judgment errors.
Even slight discrepancies in temperature or gas flow can lead to non-uniform oxide layers, directly affecting semiconductor performance.
Such variability is unacceptable in high-stakes applications like aerospace or medical devices where reliability is non-negotiable.
The Need for Precision
In the era of nanotechnology, semiconductor feature sizes are in the nanometer range.
Even minor deviations in oxide layer thickness can result in exponential changes in device behavior.
To ensure uniformity and consistency, the industry requires a transformation that leverages digital technologies for better control, accuracy, and repeatability.
The Role of Digital Transformation (DX) in Oxidation
Digital Transformation (DX) leverages advanced data analytics, automation, and intelligent algorithms to enhance traditional processes.
In the realm of semiconductor oxidation, DX ensures better precision, control, and efficiency.
By integrating digital technologies, manufacturers can monitor, adjust, and optimize the oxidation process in real time, resulting in a more reliable semiconductor operation.
Advanced Data Analytics
Data analytics plays a pivotal role in the digital transformation of the oxidation process.
By collecting and analyzing large volumes of data from various stages of the oxidation process, manufacturers can identify patterns, trends, and anomalies.
Predictive analytics allows for proactive adjustments, ensuring that the oxidation environment remains within optimal parameters.
This data-driven approach minimizes manual intervention and reduces the likelihood of errors, thereby enhancing the overall quality of the oxide layer.
Automation and Intelligent Control
Automation is a key component in the DX of oxidation processes.
With automation, various parameters such as temperature, gas flow, and oxidation time can be precisely controlled without human intervention.
Intelligent control systems use algorithms and machine learning to continuously monitor these parameters and make real-time adjustments.
This ensures that the oxidation process is consistent and meets the stringent requirements of modern semiconductor manufacturing.
Benefits of DX in Oxidation Processes
The DX of the oxidation process presents multiple benefits, including improved precision, reduced variability, and enhanced efficiency.
These improvements collectively ensure the reliability of semiconductor operations, supporting advancements in technology and maintaining industry standards.
Enhanced Precision
DX technologies allow for micro-level adjustments and monitoring, ensuring that the oxide layer formed is uniform and consistent.
With precise control over the oxidation conditions, manufacturers achieve an exceptional level of detail, directly contributing to the quality and reliability of the final semiconductor product.
Reduced Variability
Traditional methods are susceptible to variability due to human intervention and environmental factors.
DX minimizes these inconsistencies by automating the process, resulting in a more stable and predictable outcome.
Reducing variability is crucial for producing semiconductors that perform reliably across different applications.
Increased Efficiency
By automating the oxidation process and leveraging advanced analytics, the time required for oxidation can be significantly reduced.
This leads to faster production cycles and reduced operational costs.
Moreover, real-time monitoring and adjustments ensure optimal resource usage, further improving efficiency.
Case Studies and Implementation
Several semiconductor manufacturers have successfully implemented DX in their oxidation processes, leading to improved reliability and performance.
Examining these case studies provides insights into the practical benefits and the potential for further advancements in semiconductor manufacturing.
Case Study 1: XYZ Semiconductors
XYZ Semiconductors implemented an automated oxidation control system, integrating data analytics and intelligent algorithms.
The result was a 20% reduction in oxidation variability and a 15% increase in production throughput.
The company reported improved device performance and reliability, making their products more competitive in the market.
Case Study 2: ABC Microelectronics
ABC Microelectronics adopted a fully digitalized oxidation process, incorporating machine learning for predictive maintenance.
This allowed them to anticipate and address oxidation issues before they impacted production.
As a result, ABC Microelectronics experienced a 30% decrease in production downtime and a significant improvement in oxide layer uniformity.
The Future of DX in Semiconductor Oxidation
The ongoing digital transformation of the oxidation process in semiconductor manufacturing is poised to bring about even greater advancements.
As technologies like artificial intelligence and Internet of Things (IoT) continue to evolve, the potential for even more precise and efficient oxidation processes grows.
Artificial Intelligence and Machine Learning
Future advancements in AI and machine learning can further enhance the capabilities of oxidation control systems.
These technologies will enable even more predictive and adaptive control mechanisms, ensuring that the oxidation process remains within optimal parameters at all times.
The integration of AI will also facilitate continuous learning and improvement, adapting to new materials and process requirements.
Internet of Things (IoT)
IoT devices can provide a wealth of real-time data from various stages of the oxidation process.
By connecting different stages of production, IoT can enable a more holistic and synchronized approach to oxidation control.
This interconnectedness will enhance overall process efficiency and ensure consistent quality across different manufacturing sites.
In conclusion, the digital transformation of the oxidation process is crucial for ensuring the reliability of semiconductor operations.
By leveraging advanced data analytics, automation, and intelligent algorithms, manufacturers can achieve precise control, reduce variability, and enhance efficiency.
As the semiconductor industry continues to evolve, DX will remain a vital component in maintaining high standards and driving technological advancements.
資料ダウンロード
QCD調達購買管理クラウド「newji」は、調達購買部門で必要なQCD管理全てを備えた、現場特化型兼クラウド型の今世紀最高の購買管理システムとなります。
ユーザー登録
調達購買業務の効率化だけでなく、システムを導入することで、コスト削減や製品・資材のステータス可視化のほか、属人化していた購買情報の共有化による内部不正防止や統制にも役立ちます。
NEWJI DX
製造業に特化したデジタルトランスフォーメーション(DX)の実現を目指す請負開発型のコンサルティングサービスです。AI、iPaaS、および先端の技術を駆使して、製造プロセスの効率化、業務効率化、チームワーク強化、コスト削減、品質向上を実現します。このサービスは、製造業の課題を深く理解し、それに対する最適なデジタルソリューションを提供することで、企業が持続的な成長とイノベーションを達成できるようサポートします。
オンライン講座
製造業、主に購買・調達部門にお勤めの方々に向けた情報を配信しております。
新任の方やベテランの方、管理職を対象とした幅広いコンテンツをご用意しております。
お問い合わせ
コストダウンが利益に直結する術だと理解していても、なかなか前に進めることができない状況。そんな時は、newjiのコストダウン自動化機能で大きく利益貢献しよう!
(Β版非公開)