- お役立ち記事
- Cavity Design and Management in Manufacturing
Cavity Design and Management in Manufacturing
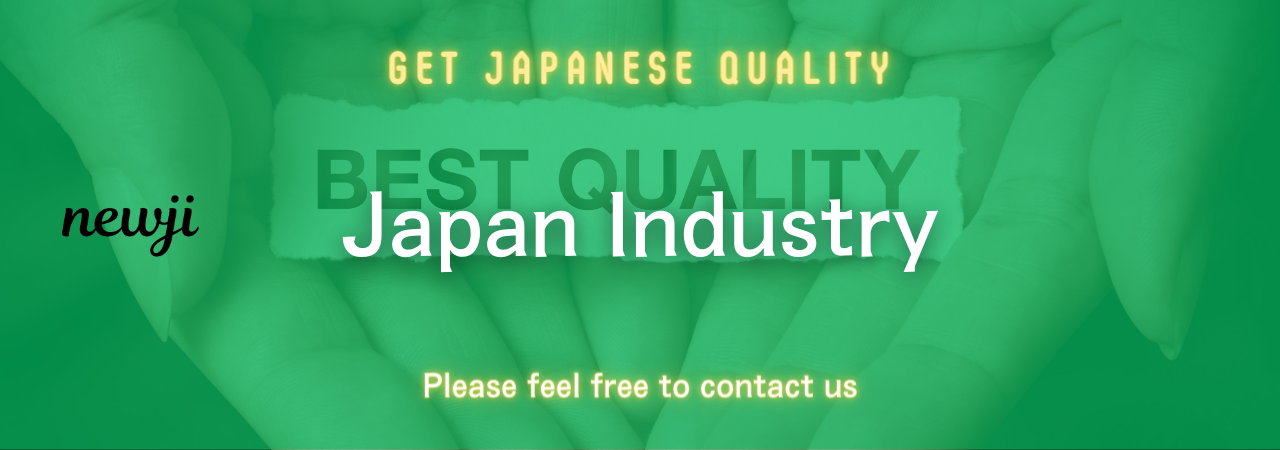
In the realm of manufacturing, often overlooked but crucial parts of the process are cavity design and management.
Understanding these components can significantly impact both the efficiency and quality of production.
This article delves into essential concepts and strategies to perfect cavity design and management in manufacturing.
目次
What is Cavity Design?
Cavity design refers to the layout and shaping of spaces within molds or dies used in various manufacturing processes.
These cavities are essential for material shaping, whether it’s for plastic injection molding, metal casting, or other methods.
They determine the final product’s shape, size, and features.
Why Cavity Design is Crucial
A well-designed cavity ensures that the final product meets specific standards and functions as intended.
Conversely, a poor design can lead to defects, waste, and higher production costs.
Here are some key reasons why cavity design is fundamental:
– **Precision:** It ensures that each product is created to exact specifications.
– **Efficiency:** A good design streamlines the production process, reducing cycle time and costs.
– **Quality:** Minimized defects and inconsistencies in the final products.
– **Durability:** A well-designed cavity prolongs mold life, reducing the need for frequent replacements.
Main Factors Influencing Cavity Design
Several factors must be considered during the cavity design phase to ensure optimal performance and product quality:
Material Selection
Choosing the right material for both the mold and the final product is critical.
The material affects the mold’s durability, the ease of shaping the cavity, and the product’s final properties.
Product Requirements
Understanding the end product’s requirements, such as dimensions, features, and tolerance levels, guides the cavity design.
The more specific the details, the more accurate the cavity and the resulting product.
Flow Dynamics
In processes like plastic injection molding and metal casting, it’s essential to ensure even and efficient flow of material into the cavity.
Poor flow dynamics can result in incomplete fills, voids, and weak spots in the product.
Cooling Systems
Effective cooling systems are necessary to regulate the mold’s temperature and ensure that the material sets properly.
Inadequate cooling can lead to warping, shrinkage, and other defects.
Mold Wear and Tear
Any design must account for the wear and tear that molds experience over time.
Including features that mitigate wear can help prolong mold life and maintain consistent product quality.
Effective Strategies for Cavity Management
Once a cavity design is perfected, managing production processes is the next crucial step.
Here are some strategies for effective cavity management:
Regular Maintenance
Regularly inspecting and maintaining molds ensures they remain in good working condition.
Scheduled maintenance can prevent unexpected breakdowns and costly downtime.
Data Collection and Analysis
Collecting data during the production process helps identify trends and potential issues quickly.
Analyzing this data can pinpoint areas for improvement, from reducing cycle times to decreasing defect rates.
Adopting Advanced Technologies
Leverage technologies such as computer-aided design (CAD) and simulation software.
These tools help refine cavity designs and predict potential problems before mass production starts.
Training and Skill Development
Investing in training for the workforce ensures that everyone understands the importance of cavity management and understands how to maintain and troubleshoot molds.
Well-trained staff can catch issues early, maintaining high-quality production standards.
Case Study: Success in Cavity Design and Management
To illustrate the impact of effective cavity design and management, let’s consider a case study.
A manufacturer specializing in automotive parts faced frequent defects and high waste due to poor cavity design in their injection molding process.
By collaborating with a design expert, they revamped their cavity design, focusing on better flow dynamics and cooling efficiency.
This led to a significant reduction in cycle times and a 30% decrease in defect rates.
In addition, implementing a robust maintenance schedule and utilizing data analytics to monitor production further optimized their process.
The result was not only improved product quality and consistency but also considerable cost savings.
Conclusion
Cavity design and management are critical yet often underappreciated elements of manufacturing.
By investing time and resources into these areas, manufacturers can enhance precision, efficiency, and quality, ultimately leading to higher customer satisfaction and better market competitiveness.
With proper focus on material selection, product requirements, flow dynamics, cooling systems, and maintenance, manufacturers can ensure a smooth production process and longer mold life.
Employing advanced technologies and ensuring the workforce is well-trained are also key strategies for effective cavity management.
Efficient cavity design and management lead to a more streamlined manufacturing process, reducing costs and increasing profits.
資料ダウンロード
QCD調達購買管理クラウド「newji」は、調達購買部門で必要なQCD管理全てを備えた、現場特化型兼クラウド型の今世紀最高の購買管理システムとなります。
ユーザー登録
調達購買業務の効率化だけでなく、システムを導入することで、コスト削減や製品・資材のステータス可視化のほか、属人化していた購買情報の共有化による内部不正防止や統制にも役立ちます。
NEWJI DX
製造業に特化したデジタルトランスフォーメーション(DX)の実現を目指す請負開発型のコンサルティングサービスです。AI、iPaaS、および先端の技術を駆使して、製造プロセスの効率化、業務効率化、チームワーク強化、コスト削減、品質向上を実現します。このサービスは、製造業の課題を深く理解し、それに対する最適なデジタルソリューションを提供することで、企業が持続的な成長とイノベーションを達成できるようサポートします。
オンライン講座
製造業、主に購買・調達部門にお勤めの方々に向けた情報を配信しております。
新任の方やベテランの方、管理職を対象とした幅広いコンテンツをご用意しております。
お問い合わせ
コストダウンが利益に直結する術だと理解していても、なかなか前に進めることができない状況。そんな時は、newjiのコストダウン自動化機能で大きく利益貢献しよう!
(Β版非公開)