- お役立ち記事
- Improving Manufacturing Processes with IE (Industrial Engineering) Techniques
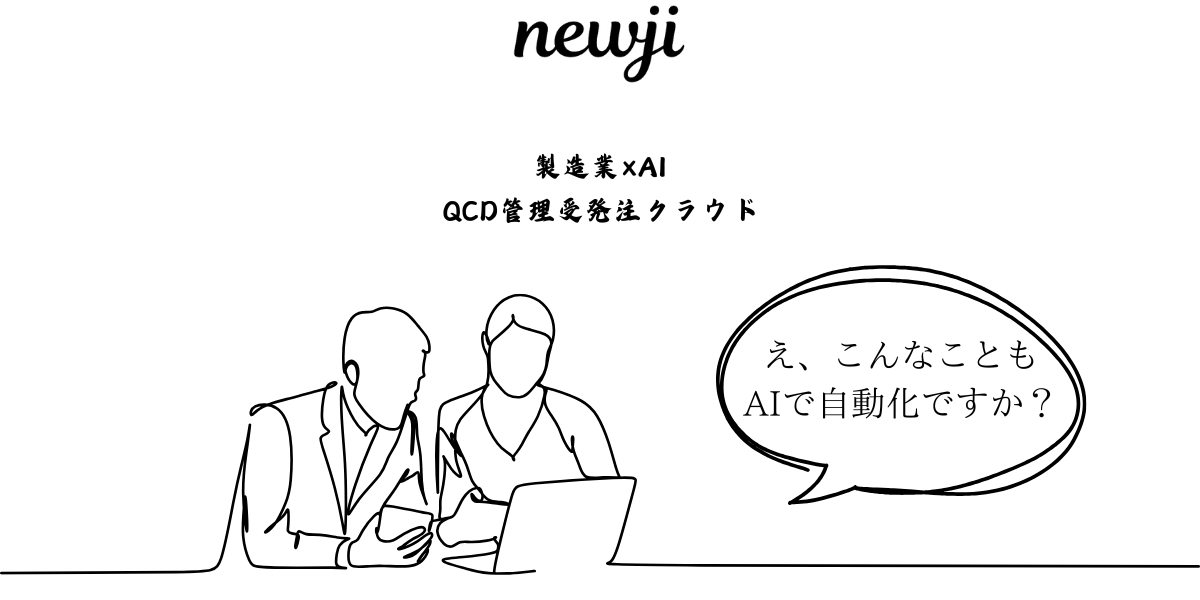
Improving Manufacturing Processes with IE (Industrial Engineering) Techniques
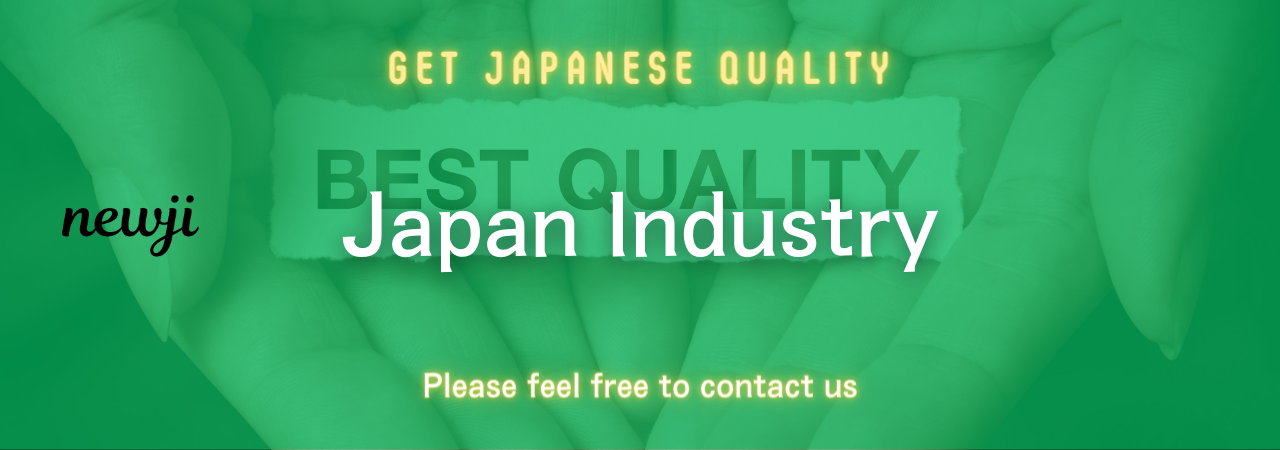
In today’s competitive business environment, optimizing manufacturing processes is crucial for maintaining profitability and ensuring quality.
One of the most effective ways to achieve this is by applying IE (Industrial Engineering) techniques.
IE focuses on improving the efficiency of production processes through systematic analysis and the implementation of innovative solutions.
In this article, we will explore various IE techniques and how they can enhance manufacturing processes.
目次
What is Industrial Engineering?
Industrial Engineering (IE) is a branch of engineering that focuses on optimizing complex processes or systems.
It involves the use of analytical methods to improve productivity, efficiency, and quality in manufacturing and other industries.
IE techniques include process modeling, operations research, quality control, and ergonomics, among others.
The goal is to create efficient systems that integrate workers, machines, materials, information, and energy.
The Importance of IE in Manufacturing
IE is essential in manufacturing for several reasons. First, it helps in reducing production costs by minimizing waste, improving workflow, and enhancing the use of resources.
Second, it increases productivity by streamlining processes and removing inefficiencies.
Third, it ensures high-quality products by implementing consistent and reliable procedures.
Lastly, it improves worker safety and satisfaction by designing ergonomic workstations that reduce the risk of injury.
Key IE Techniques in Manufacturing
Lean Manufacturing
Lean manufacturing is an IE technique that focuses on eliminating waste in production processes.
Waste can come in many forms, such as excess inventory, waiting times, and unnecessary transportation.
By identifying and eliminating these wastes, manufacturers can reduce costs and improve efficiency.
Key principles of lean manufacturing include Just-In-Time (JIT) production, continuous improvement (Kaizen), and value stream mapping.
Six Sigma
Six Sigma is a data-driven approach to improving quality by identifying and eliminating defects in processes.
It uses statistical tools to analyze and improve processes, aiming for a defect rate of no more than 3.4 per million opportunities.
Six Sigma follows the DMAIC methodology—Define, Measure, Analyze, Improve, and Control.
By using this structured approach, manufacturers can ensure consistent quality and reduce variability in their processes.
Time and Motion Studies
Time and motion studies are used to analyze the efficiency of workers and equipment in a manufacturing process.
By observing and recording the time taken for each task, industrial engineers can identify areas of inefficiency and suggest improvements.
These studies help in optimizing labor productivity and reducing unnecessary movements, leading to faster and more efficient production.
Computer-Aided Design and Manufacturing (CAD/CAM)
CAD/CAM systems are used to design products and plan manufacturing processes.
CAD software allows engineers to create detailed 3D models of products, which can then be tested and refined before production.
CAM software translates these designs into instructions for automated machinery, ensuring precise and efficient manufacturing.
The integration of CAD/CAM systems helps in reducing design errors, improving product quality, and speeding up production.
Implementing IE Techniques: A Step-by-Step Approach
Step 1: Identify and Analyze Current Processes
The first step in implementing IE techniques is to thoroughly understand the existing manufacturing processes.
This involves mapping out each step, from raw material procurement to final product delivery.
Data collection and analysis are crucial at this stage, as they help identify bottlenecks, inefficiencies, and areas of waste.
Step 2: Set Clear Goals and Objectives
Once you have a clear understanding of the current processes, the next step is to set specific goals and objectives.
These could include reducing production costs, improving product quality, increasing employee productivity, or enhancing customer satisfaction.
Having clear and measurable goals will help guide the implementation of IE techniques and track progress.
Step 3: Choose the Right IE Techniques
Not all IE techniques will be suitable for every manufacturing process.
Therefore, it is essential to choose the techniques that are most relevant to your specific needs and goals.
For example, if your primary goal is to reduce waste, lean manufacturing principles might be the most appropriate.
If you are focused on improving quality, Six Sigma techniques could be more suitable.
Step 4: Implement the Chosen Techniques
With the right techniques selected, the next step is to implement them.
This may involve training employees, reconfiguring workstations, or investing in new equipment and technology.
It is essential to communicate clearly with all stakeholders and ensure they understand the changes being made and the reasons behind them.
Effective implementation also requires continuous monitoring and adjustment to address any issues that arise.
Step 5: Monitor and Measure Results
After implementing the chosen IE techniques, it is crucial to monitor and measure the results.
This involves collecting data on key performance indicators (KPIs) and comparing them to the goals set in Step 2.
Constant monitoring allows for real-time adjustments and ensures that the implemented changes are delivering the desired outcomes.
Case Study: Improving Efficiency with Lean Manufacturing
Consider a hypothetical automotive parts manufacturer struggling with high production costs and long lead times.
By implementing lean manufacturing principles, the company was able to drastically improve its processes.
First, a value stream map was created to identify areas of waste, such as excess inventory and long waiting times.
Next, Just-In-Time (JIT) production schedules were put in place to reduce inventory costs and shorten lead times.
Continuous improvement (Kaizen) initiatives encouraged employees to suggest and implement improvements, leading to incremental but significant efficiency gains.
As a result, the company reduced its production costs by 20% and cut lead times by 50%.
Conclusion
In conclusion, IE techniques offer a systematic and efficient way to improve manufacturing processes.
From lean manufacturing to Six Sigma, time and motion studies to CAD/CAM systems, these techniques help in reducing waste, improving quality, and increasing productivity.
By following a structured approach to implementing IE techniques—identifying current processes, setting goals, choosing the right techniques, implementing changes, and monitoring results—manufacturers can achieve significant improvements in their operations.
Investing in IE not only enhances manufacturing efficiency but also contributes to overall business success.
資料ダウンロード
QCD調達購買管理クラウド「newji」は、調達購買部門で必要なQCD管理全てを備えた、現場特化型兼クラウド型の今世紀最高の購買管理システムとなります。
ユーザー登録
調達購買業務の効率化だけでなく、システムを導入することで、コスト削減や製品・資材のステータス可視化のほか、属人化していた購買情報の共有化による内部不正防止や統制にも役立ちます。
NEWJI DX
製造業に特化したデジタルトランスフォーメーション(DX)の実現を目指す請負開発型のコンサルティングサービスです。AI、iPaaS、および先端の技術を駆使して、製造プロセスの効率化、業務効率化、チームワーク強化、コスト削減、品質向上を実現します。このサービスは、製造業の課題を深く理解し、それに対する最適なデジタルソリューションを提供することで、企業が持続的な成長とイノベーションを達成できるようサポートします。
オンライン講座
製造業、主に購買・調達部門にお勤めの方々に向けた情報を配信しております。
新任の方やベテランの方、管理職を対象とした幅広いコンテンツをご用意しております。
お問い合わせ
コストダウンが利益に直結する術だと理解していても、なかなか前に進めることができない状況。そんな時は、newjiのコストダウン自動化機能で大きく利益貢献しよう!
(Β版非公開)