- お役立ち記事
- Exploring Japanese Excellence in Tool Set OEM Manufacturing
Exploring Japanese Excellence in Tool Set OEM Manufacturing
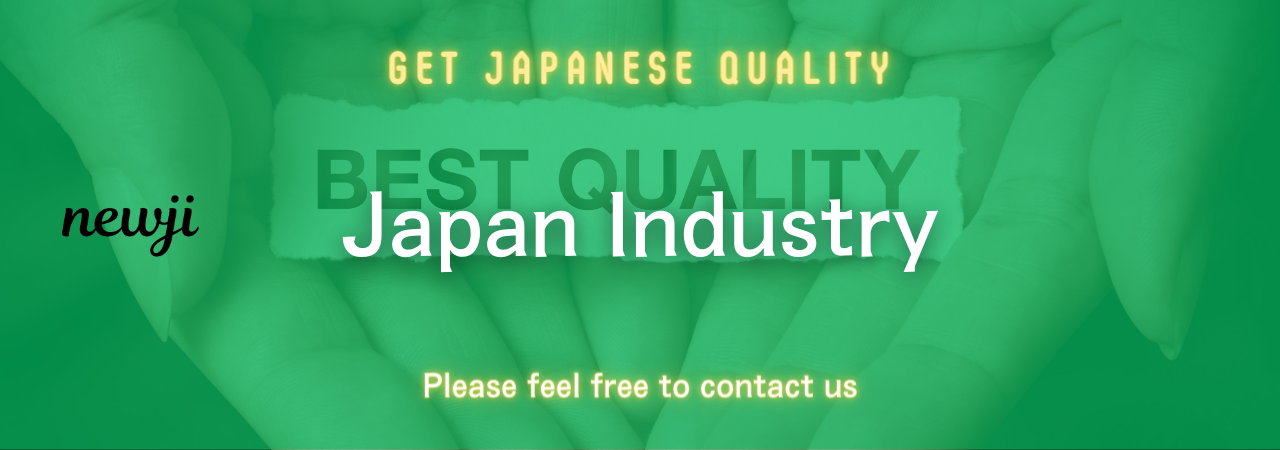
目次
Understanding Japan’s Tool Set Manufacturing Landscape
Japanese manufacturing has long been celebrated for its relentless commitment to quality, innovative practices, and meticulous attention to detail.
Tool set OEM (Original Equipment Manufacturer) manufacturing is a facet of this exceptionally high standard.
As multinational companies seek to collaborate with Japanese suppliers, understanding the intricacies of this specialized sector becomes paramount.
History and Evolution of Tool Set Manufacturing in Japan
Japanese tool manufacturing traces its roots back to centuries-old traditions.
Starting with simple hand tools, the industry has evolved into a highly advanced segment driven by sophisticated technology.
Companies like Makita, Panasonic, and Hitachi have shaped the global tool industry, embedding precision, durability, and reliability into their manufacturing ethos.
The post-World War II era marked a significant turning point.
Japan’s focus on rebuilding its economy through industrial advancement led to significant strides in manufacturing quality and efficiency.
Today, Japanese tool manufacturers are synonymous with top-notch craftsmanship and innovative engineering.
Advantages of Partnering with Japanese Tool Set Manufacturers
Unrivaled Quality and Precision
Japanese manufacturers adhere to strict quality control standards.
Their philosophy of ‘Kaizen’ or continuous improvement permeates every facet of production, ensuring sustained excellence.
This emphasis on quality results in tools that offer superior performance and longevity, making them highly attractive to businesses seeking reliable OEM partners.
Innovative Technology and Engineering
The competitive edge of Japanese tool manufacturers lies in their ability to integrate state-of-the-art technology with traditional engineering principles.
Whether it’s the implementation of automation in production lines or leveraging advanced materials, these manufacturers remain at the forefront of innovation.
Skilled Labor Force
Another significant advantage is the presence of a highly skilled and dedicated workforce.
Japanese craftsmen often undergo rigorous, years-long training programs.
Their expertise manifests in the flawless execution of complex manufacturing processes and stringent quality assessments.
Disadvantages and Challenges
Higher Production Costs
One of the primary challenges of partnering with Japanese tool manufacturers is the relatively higher production cost.
This is often due to the high quality of materials used, advanced technologies implemented, and the comprehensive training of labor.
However, the initial investment typically translates into better durability and lower long-term costs.
Geographical Distance and Logistics
For Western companies, the geographical distance can pose logistical hurdles.
Shipping costs, lead times, and tariffs are factors that might complicate procurement processes.
Nevertheless, many Japanese companies have established international subsidiaries to mitigate these challenges.
Cultural and Communication Barriers
Language and cultural differences can also affect negotiations and day-to-day operations.
Understanding Japanese business etiquette and fostering mutual respect are key to ensuring smooth collaboration.
Hiring local experts or interpreters can significantly bridge these gaps.
Effective Supplier Negotiation Techniques
When negotiating with Japanese suppliers, it is essential to appreciate and respect their business culture.
Japanese business negotiations tend to be more formal and relationship-oriented compared to the Western approach.
Building Long-Term Relationships
Prioritize establishing a long-term relationship over short-term gains.
Japanese suppliers value trust and loyalty.
Take time to build rapport and demonstrate a genuine commitment to the collaboration.
Clear and Detailed Communication
Ensure that all communications are clear and detailed.
Provide comprehensive specifications, timelines, and quality expectations up front.
Avoid ambiguity to prevent misunderstandings.
Patience and Persistence
Japanese companies often take a meticulous and measured approach in their decision-making process.
Patience is necessary, as pushing for rapid decisions may be viewed as disrespectful or hasty.
Embrace Formalities
Respect traditional business formalities such as bowing, exchanging business cards with both hands, and using formal titles.
These gestures go a long way in establishing a respectful and professional relationship.
Current Market Conditions
The global market for tool set manufacturing is experiencing dynamic shifts.
Technological advancements, shifting economic conditions, and evolving consumer preferences continually shape the landscape.
Technological Integration
Emerging technologies such as IoT (Internet of Things), AI (Artificial Intelligence), and machine learning are increasingly being integrated into tool manufacturing.
Japanese manufacturers, known for their technological prowess, are leveraging these advancements to produce smarter, more efficient tools.
Automation and Robotics
Automation and robotics are revolutionizing production lines.
Japanese factories often feature robotic assembly and inspection systems that enhance precision and efficiency.
This trend is set to grow, furthering Japan’s leading position in the market.
Sustainability and Environmental Concerns
Sustainability is becoming a critical factor in manufacturing decisions.
Japanese companies are pioneers in implementing eco-friendly manufacturing practices.
From minimizing waste to using recyclable materials, these initiatives appeal to eco-conscious consumers and partners.
Global Supply Chain Disruptions
Recent events like the COVID-19 pandemic have highlighted vulnerabilities in global supply chains.
Japanese manufacturers are responding by diversifying their supply chains and increasing local production capacities where feasible.
Best Practices for Collaborating with Japanese Manufacturers
Successful collaboration with Japanese tool set manufacturers requires adherence to certain best practices.
Due Diligence and Supplier Selection
Conduct thorough due diligence when selecting a supplier.
Evaluate their production capabilities, quality control processes, and financial stability.
Site visits, third-party audits, and references can offer valuable insights.
Aligning Expectations
Ensure that both parties have a clear and mutual understanding of expectations.
This includes specifications, timelines, quality standards, and pricing structures.
Regular reviews and updates can prevent potential conflicts.
Leveraging Technology for Communication
Utilize technology to streamline communication.
Video conferencing, collaborative platforms, and instant messaging tools can enhance real-time interaction and decision-making.
Fostering Continuous Improvement
Embrace the philosophy of continuous improvement, or ‘Kaizen.’
Encourage regular feedback sessions and collaborative problem-solving to enhance processes and outcomes.
Case Studies of Successful Collaborations
Examining real-world examples can provide invaluable insights into the practical benefits of partnering with Japanese tool set manufacturers.
Case Study: Partnership with Makita
A US-based construction equipment company teamed up with Makita to develop a new line of cordless power tools.
Through detailed discussions and iterative prototyping, they achieved tools that offered superior battery life and performance.
The collaboration not only elevated product quality but also reinforced the company’s market position.
Case Study: Collaboration with Hitachi
An Australian mining firm collaborated with Hitachi to enhance their toolsets used in mining operations.
The partnership focused on integrating IoT capabilities to track tool usage and maintenance schedules.
This led to a significant reduction in downtime and maintenance costs, illustrating the benefits of technological integration.
Conclusion
Collaborating with Japanese tool set OEM manufacturers offers numerous advantages, from superior quality and innovation to a skilled workforce and robust management practices.
However, one must also navigate challenges such as higher costs, logistical complexities, and cultural differences.
By understanding the market landscape, employing effective negotiation techniques, and adhering to best practices, companies can maximize the benefits of Japanese manufacturing excellence.
Ultimately, these partnerships can lead to groundbreaking products and long-term success in the competitive global market.
資料ダウンロード
QCD調達購買管理クラウド「newji」は、調達購買部門で必要なQCD管理全てを備えた、現場特化型兼クラウド型の今世紀最高の購買管理システムとなります。
ユーザー登録
調達購買業務の効率化だけでなく、システムを導入することで、コスト削減や製品・資材のステータス可視化のほか、属人化していた購買情報の共有化による内部不正防止や統制にも役立ちます。
NEWJI DX
製造業に特化したデジタルトランスフォーメーション(DX)の実現を目指す請負開発型のコンサルティングサービスです。AI、iPaaS、および先端の技術を駆使して、製造プロセスの効率化、業務効率化、チームワーク強化、コスト削減、品質向上を実現します。このサービスは、製造業の課題を深く理解し、それに対する最適なデジタルソリューションを提供することで、企業が持続的な成長とイノベーションを達成できるようサポートします。
オンライン講座
製造業、主に購買・調達部門にお勤めの方々に向けた情報を配信しております。
新任の方やベテランの方、管理職を対象とした幅広いコンテンツをご用意しております。
お問い合わせ
コストダウンが利益に直結する術だと理解していても、なかなか前に進めることができない状況。そんな時は、newjiのコストダウン自動化機能で大きく利益貢献しよう!
(Β版非公開)