- お役立ち記事
- Streamlining Material Management in Manufacturing with MRP Implementation
Streamlining Material Management in Manufacturing with MRP Implementation
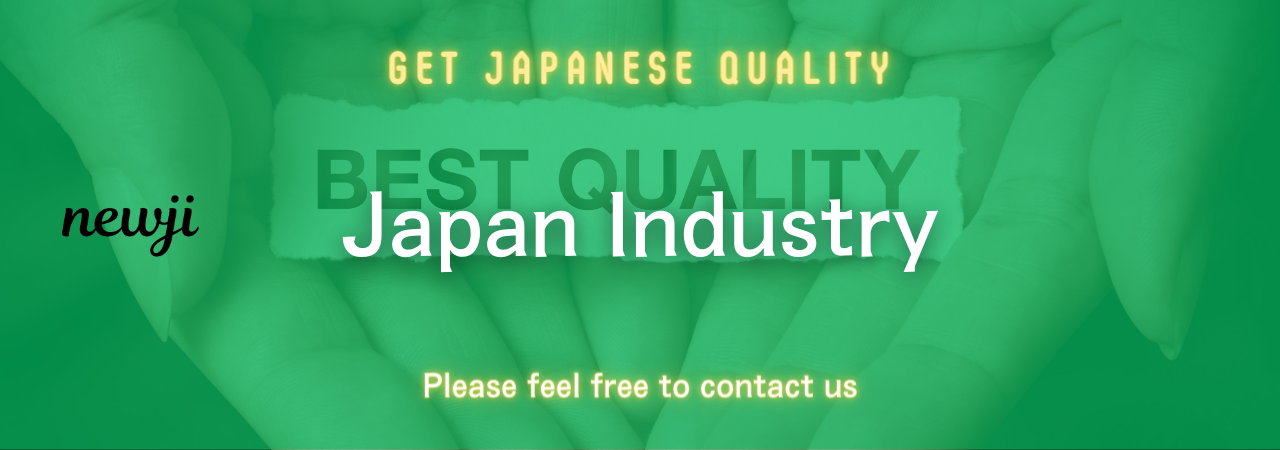
目次
Understanding Material Requirements Planning (MRP)
Material Requirements Planning, or MRP, is a production planning, scheduling, and inventory control system used in manufacturing.
It helps ensure that materials and products are available for production and delivery to customers.
MRP is designed to manage manufacturing processes efficiently by providing critical information on inventory requirements.
What is MRP?
MRP is a computer-based system that calculates the materials needed to produce a product.
It starts with the finished product’s requirements and works backward to determine the raw materials and components needed.
This process helps manufacturers avoid both shortages and excessive inventory, which can lead to higher costs.
Key Components of MRP
There are three main inputs to an MRP system:
1. **Master Production Schedule (MPS):** This schedule outlines the quantity of each product to be produced and the dates for their completion.
2. **Bill of Materials (BOM):** The BOM is a detailed list of all materials and components required to produce a finished product.
3. **Inventory Status Records:** These records keep track of current inventory levels, outstanding orders, and lead times for materials.
Benefits of MRP Implementation
Implementing an MRP system can bring numerous benefits to a manufacturing company.
These advantages can streamline material management and improve overall production efficiency.
Reduced Inventory Costs
MRP helps manufacturers keep inventory levels to a minimum.
By calculating the exact material requirements, businesses can avoid the costs associated with holding excess inventory.
This reduces storage costs and minimizes the risk of materials becoming obsolete.
Efficient Production Scheduling
MRP systems provide a clear production schedule that aligns with customer demand.
This helps manufacturers allocate resources effectively and avoid production delays.
By having a precise timeline, production can proceed smoothly without interruptions.
Improved Order Fulfillment
With accurate material planning, manufacturers can meet customer demands on time.
MRP ensures that the required materials are available when needed, leading to better customer satisfaction.
Timely order fulfillment can enhance a company’s reputation and encourage repeat business.
Implementing MRP in Your Manufacturing Process
To reap the benefits of MRP, manufacturers need to follow a structured implementation process.
Step 1: Analyze Current Processes
Before implementing an MRP system, it’s crucial to analyze existing production and inventory management processes.
Identify any inefficiencies or bottlenecks that could be improved with MRP.
This analysis will provide a clear picture of the current state and highlight areas that need attention.
Step 2: Select the Right MRP Software
Choosing the right MRP software is vital for successful implementation.
There are various MRP solutions available, each with different features and capabilities.
Consider factors such as ease of use, scalability, and integration with existing systems.
Select a solution that aligns with your company’s specific needs and goals.
Step 3: Train Employees
Training employees on how to use the MRP system is essential.
Ensure that all relevant staff understand how to input data, generate reports, and utilize the system’s functionalities.
Proper training will help maximise the benefits of the system and ensure smooth operation.
Step 4: Data Entry and System Testing
Accurate data entry is critical for the success of an MRP system.
Input all necessary information, including the Master Production Schedule, Bill of Materials, and Inventory Status Records.
Once the data is entered, conduct thorough testing to confirm the system’s accuracy.
This step helps identify any issues before the system goes live.
Step 5: Monitor and Optimize
After implementation, continuously monitor the MRP system’s performance.
Regularly review the data and reports generated by the system to identify areas for improvement.
Make necessary adjustments to optimize the manufacturing process and maintain efficiency.
Conclusion
Implementing MRP in manufacturing can significantly streamline material management and improve production efficiency.
By reducing inventory costs, ensuring timely order fulfillment, and providing clear production schedules, MRP systems help manufacturers meet customer demands effectively.
However, successful implementation requires careful planning, the right software, comprehensive training, and ongoing optimization.
With these steps, manufacturing companies can enhance their operations and gain a competitive edge in the market.
資料ダウンロード
QCD調達購買管理クラウド「newji」は、調達購買部門で必要なQCD管理全てを備えた、現場特化型兼クラウド型の今世紀最高の購買管理システムとなります。
ユーザー登録
調達購買業務の効率化だけでなく、システムを導入することで、コスト削減や製品・資材のステータス可視化のほか、属人化していた購買情報の共有化による内部不正防止や統制にも役立ちます。
NEWJI DX
製造業に特化したデジタルトランスフォーメーション(DX)の実現を目指す請負開発型のコンサルティングサービスです。AI、iPaaS、および先端の技術を駆使して、製造プロセスの効率化、業務効率化、チームワーク強化、コスト削減、品質向上を実現します。このサービスは、製造業の課題を深く理解し、それに対する最適なデジタルソリューションを提供することで、企業が持続的な成長とイノベーションを達成できるようサポートします。
オンライン講座
製造業、主に購買・調達部門にお勤めの方々に向けた情報を配信しております。
新任の方やベテランの方、管理職を対象とした幅広いコンテンツをご用意しております。
お問い合わせ
コストダウンが利益に直結する術だと理解していても、なかなか前に進めることができない状況。そんな時は、newjiのコストダウン自動化機能で大きく利益貢献しよう!
(Β版非公開)