- お役立ち記事
- Clean Slit Technology and Its Applications in Manufacturing
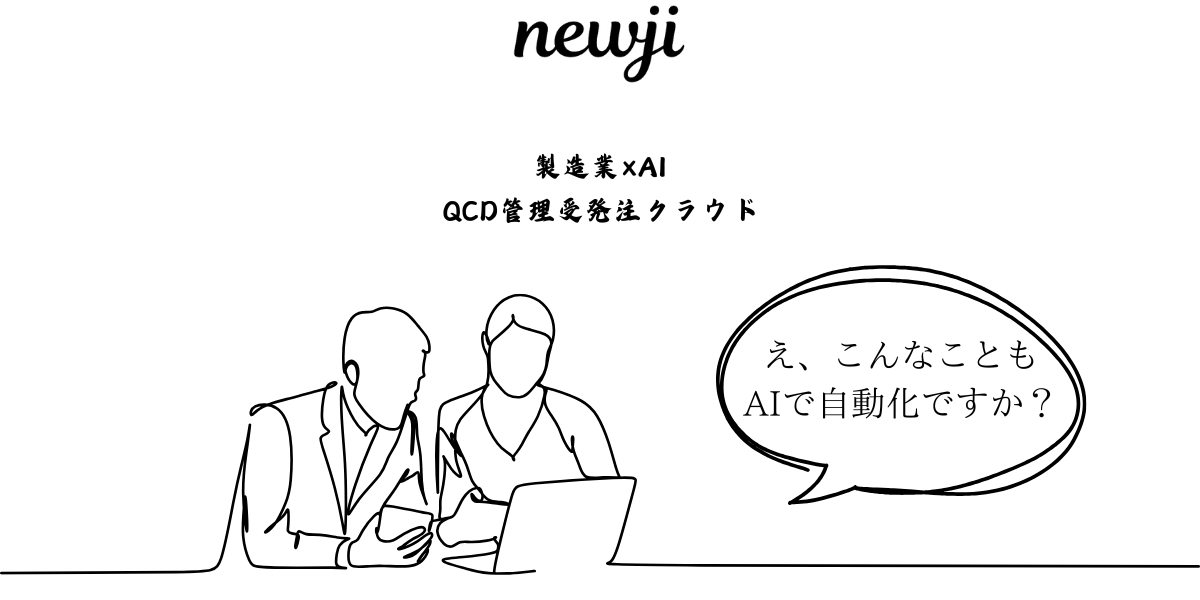
Clean Slit Technology and Its Applications in Manufacturing
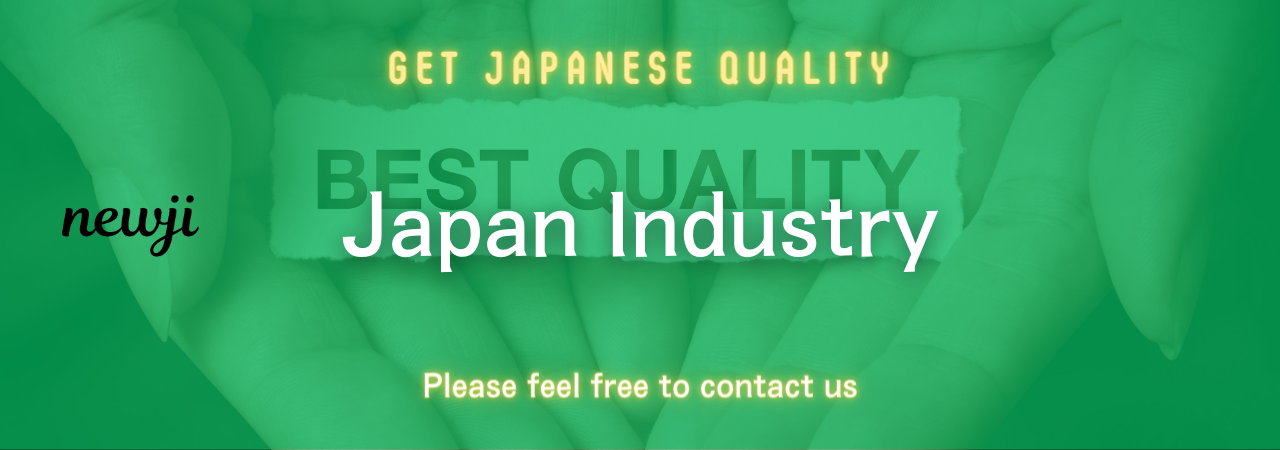
In modern manufacturing, technology plays a crucial role in enhancing precision and efficiency. One such innovative technology that stands out is Clean Slit Technology. It is changing the way various materials are cut and processed, making production lines faster and products better.
目次
What is Clean Slit Technology?
Clean Slit Technology refers to advanced methods and tools used to cut materials with high precision. This technology ensures cuts are smooth, clean, and free of debris. It is particularly vital in industries where material integrity and accuracy are paramount. The main advantage of this technology is that it reduces the amount of waste produced during the cutting process while also increasing the overall quality of the final product.
How Does Clean Slit Technology Work?
The mechanism behind Clean Slit Technology involves the use of specialized tools and machinery. These tools are designed to minimize the friction and heat generated during cutting, which helps preserve the quality of the material being cut. Here’s a closer look at the principles behind it:
Precision Cutting Tools
Specialized blades or lasers are used for cutting. These tools are engineered to create precise cuts without causing significant damage to the material. The use of lasers, in particular, allows for highly accurate cuts that are essential in industries like electronics and aerospace.
Fluid Assistance
Another method incorporates fluid-assisted cutting. Here, a jet of water or other fluids is directed at the cutting point, which helps cool the material and remove debris instantly. This ensures the slit remains clean and smooth.
Minimal Heat Generation
Traditional cutting methods often generate a lot of heat, which can warp or damage the material. Clean Slit Technology aims to reduce this heat through advanced cooling techniques or by using equipment that generates minimal heat.
Applications in Different Industries
Clean Slit Technology has become a valuable asset in several industries. Its ability to make precise, clean cuts has wide-ranging applications.
Electronics Manufacturing
In the electronics industry, precision is key. Clean Slit Technology is used to cut circuit boards and other sensitive components. The clean cuts prevent damage to the delicate parts, ensuring the final product functions correctly. Additionally, reducing waste is a significant benefit, making the manufacturing process more cost-effective.
Aerospace Industry
When it comes to building aircraft, precision and material integrity cannot be compromised. Clean Slit Technology is used to cut metals and composites with great accuracy. This helps maintain the strength and durability of these materials, which is crucial for the safety and performance of the aircraft.
Automotive Industry
In automotive manufacturing, materials such as metals and composites need to be cut with high precision for assembling various parts. Clean Slit Technology ensures that each cut is smooth and consistent, reducing the need for additional finishing work and speeding up the production process.
Medical Device Manufacturing
Medical devices often require extremely precise and clean cuts. Clean Slit Technology is employed here to ensure that components are cut accurately, maintaining the highest standards of safety and quality. This is essential for devices such as surgical tools and implants, where precision can be a matter of life and death.
Packaging Industry
Even in the packaging industry, clean and precise cuts are necessary for creating boxes, containers, and other packaging materials. Clean Slit Technology helps achieve neat cuts, which improves the overall appearance and functionality of the packaging.
Benefits of Clean Slit Technology
The adoption of Clean Slit Technology brings several advantages to manufacturing processes.
Improved Product Quality
The primary benefit is the significant improvement in product quality. By ensuring clean and precise cuts, the technology enhances the structural integrity and appearance of the final product.
Increased Efficiency
Clean Slit Technology reduces the need for additional processing, such as sanding or polishing, which saves time. The machinery used is often faster, meaning production lines can move more quickly.
Cost-Effectiveness
Reducing waste and improving efficiency directly impacts the cost. Less material wastage means lower raw material costs. Faster production speeds reduce labor and energy costs over time.
Environmental Benefits
Less waste production also means fewer resources are needed to manage that waste, contributing to environmental conservation. Clean processes ensure fewer pollutants are released, making manufacturing more eco-friendly.
Challenges and Considerations
While Clean Slit Technology offers numerous benefits, it also presents some challenges that need to be considered.
Initial Investment
The advanced machinery and tools required can be expensive. Companies may need to invest significantly upfront to incorporate this technology into their production lines.
Training Requirements
Operators need to be trained to use the new machinery effectively. This can involve additional time and resource costs for companies during the transition period.
Maintenance
Although the technology increases efficiency, it also requires regular maintenance to function optimally. Keeping the advanced cutting tools in good condition is essential for maintaining precision and quality.
The Future of Clean Slit Technology
The future looks bright for Clean Slit Technology. As industries continue to seek ways to improve efficiency and reduce waste, the demand for this technology is expected to grow. Future innovations may lead to even more refined cutting techniques and wider applications.
In conclusion, Clean Slit Technology is revolutionizing the manufacturing world. Its ability to create precise, clean cuts with minimal waste is invaluable. Despite the challenges, the benefits it offers make it a worthwhile investment for many industries. As technology continues to advance, we can expect even greater enhancements that will further streamline production processes and elevate product quality.
資料ダウンロード
QCD調達購買管理クラウド「newji」は、調達購買部門で必要なQCD管理全てを備えた、現場特化型兼クラウド型の今世紀最高の購買管理システムとなります。
ユーザー登録
調達購買業務の効率化だけでなく、システムを導入することで、コスト削減や製品・資材のステータス可視化のほか、属人化していた購買情報の共有化による内部不正防止や統制にも役立ちます。
NEWJI DX
製造業に特化したデジタルトランスフォーメーション(DX)の実現を目指す請負開発型のコンサルティングサービスです。AI、iPaaS、および先端の技術を駆使して、製造プロセスの効率化、業務効率化、チームワーク強化、コスト削減、品質向上を実現します。このサービスは、製造業の課題を深く理解し、それに対する最適なデジタルソリューションを提供することで、企業が持続的な成長とイノベーションを達成できるようサポートします。
オンライン講座
製造業、主に購買・調達部門にお勤めの方々に向けた情報を配信しております。
新任の方やベテランの方、管理職を対象とした幅広いコンテンツをご用意しております。
お問い合わせ
コストダウンが利益に直結する術だと理解していても、なかなか前に進めることができない状況。そんな時は、newjiのコストダウン自動化機能で大きく利益貢献しよう!
(Β版非公開)