- お役立ち記事
- Revolutionizing Japanese Manufacturing: The Impact of Advanced Simulation Software
Revolutionizing Japanese Manufacturing: The Impact of Advanced Simulation Software
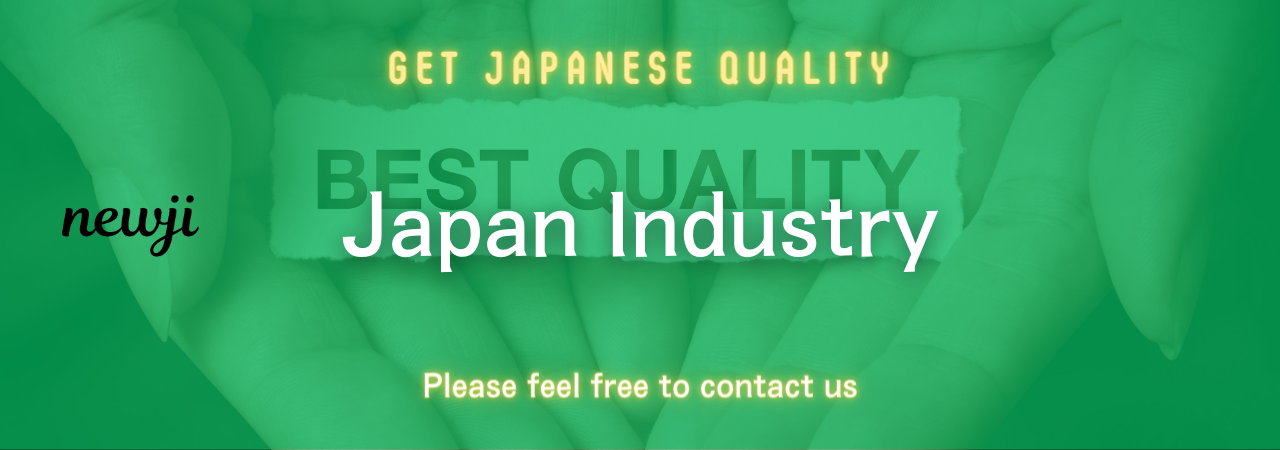
The advent of advanced simulation software has marked a significant turning point in the realm of Japanese manufacturing. With its roots deeply embedded in a culture that values precision, detail, and continuous improvement, Japanese manufacturing has always been at the forefront of innovation. However, the integration of sophisticated simulation tools is set to revolutionize the industry even further. This article delves into the practical implications, advantages, and disadvantages of advanced simulation software, and offers insights into negotiation techniques, market conditions, and best practices from the vantage point of procurement and purchasing professionals.
目次
Understanding Advanced Simulation Software
The Evolution of Simulation Tools
Simulation software has evolved drastically over the past few decades. Initially, these tools were rudimentary and used primarily for academic purposes. However, advancements in computing power and algorithms have enabled the development of highly sophisticated simulation software. These tools can now accurately predict a wide range of manufacturing processes, from the behavior of materials under stress to the outcomes of complex production workflows.
Key Features of Advanced Simulation Software
Modern simulation software offers several key features that make it indispensable for manufacturers:
– **High-Resolution 3D Modeling**: These tools can create intricate, high-definition models that allow for detailed analysis.
– **Real-Time Analysis**: Immediate feedback on the effects of changes in the manufacturing process.
– **Integration with CAD/CAM**: Seamless integration with Computer-Aided Design (CAD) and Computer-Aided Manufacturing (CAM) systems.
– **Scalability**: Can be used for small, single-component simulations or extensive, multi-faceted production lines.
– **Multi-Physics Capabilities**: Ability to simulate different physical phenomena such as thermal, mechanical, and fluid dynamics.
Advantages of Advanced Simulation Software in Japanese Manufacturing
Enhanced Precision and Accuracy
Japanese manufacturing is renowned for its pursuit of precision and accuracy. Advanced simulation software allows engineers to test various scenarios and identify the most efficient and error-free processes. This leads to higher-quality products and reduces the likelihood of defects.
Cost Efficiency
Simulation software can significantly reduce costs associated with prototyping and testing. Manufacturers can identify and rectify issues in the virtual environment before they appear in the physical world. This not only saves time but also minimizes material wastage.
Design Optimization
Engineers can use simulation software to explore different design configurations quickly. This level of flexibility enables the creation of optimized designs that meet stringent performance criteria. The end result is a product that is not only more reliable but also often less expensive to produce.
Speed to Market
By streamlining the design and testing phases, advanced simulation software can dramatically reduce the time it takes to bring a product to market. This agility is particularly crucial in highly competitive markets where being first can provide a substantial advantage.
Sustainability
Simulation tools help in understanding the environmental impact of different manufacturing processes. This allows companies to choose the most sustainable methods, thereby aligning with global sustainability goals and customer expectations.
Challenges and Disadvantages
Initial Investment
One of the significant barriers to adopting advanced simulation software is the initial investment required. High-quality simulation tools can be expensive, both in terms of software licenses and the hardware necessary to run them effectively.
Complexity
While these tools offer powerful capabilities, they are also complex to operate. Proper training is essential to maximize their potential. This often requires a dedicated team of specialists, which can be a substantial investment for smaller companies.
Integration Issues
Integrating advanced simulation software with existing systems can be challenging. Discrepancies in data formats and incompatibility with older software can pose significant hurdles. It is crucial to carefully plan the integration process to minimize disruptions.
Over-Reliance on Software
There is a risk that companies might become overly reliant on simulation software, relegating the intuition and experience of engineers to the background. While simulations are powerful tools, they are not infallible and should be used to supplement, rather than replace, human expertise.
Supplier Negotiation Techniques
Leverage Data-Driven Insights
With the information gleaned from simulations, procurement professionals can approach suppliers with detailed, data-driven insights. This provides a strong foundation for negotiations, as it demonstrates a thorough understanding of the required specifications and potential challenges.
Collaborative Approach
Simulations allow for a more collaborative approach with suppliers. By sharing simulation results, manufacturers and suppliers can work together to optimize the production process. This can lead to better pricing and improved product quality.
Focus on Long-Term Partnerships
Given the complexity and investment involved in adopting advanced simulation software, it is often beneficial to focus on building long-term partnerships with suppliers. This ensures that both parties are aligned in terms of expectations and capabilities, leading to more seamless integration and collaboration.
Market Conditions
Growing Demand for Precision
The global market is increasingly demanding precision and customization, driving the adoption of advanced simulation software. Japanese manufacturers, with their reputation for high quality, are well-positioned to meet these demands using simulation tools.
Technological Advancements
Continuous advancements in computing technology are making simulation software more powerful and accessible. This trend is expected to continue, reducing the entry barriers for smaller manufacturers and driving broader adoption.
Regulatory Compliance
Regulations around product safety and environmental impact are becoming more stringent. Advanced simulation software helps manufacturers ensure compliance by enabling thorough testing and optimization of processes.
Best Practices for Implementing Advanced Simulation Software
Comprehensive Training Programs
Investing in comprehensive training programs for your team is crucial. This ensures that the software is used to its full potential and can significantly enhance productivity and accuracy.
Pilot Projects
Before full-scale implementation, it is advisable to start with pilot projects. This allows for the identification and resolution of potential issues in a controlled environment, minimizing the risk of disruptions during broader deployment.
Close Collaboration with Software Vendors
Maintaining a close relationship with software vendors can be highly beneficial. They can provide ongoing support, updates, and training, ensuring that the software remains up-to-date and effective.
Continuous Monitoring and Improvement
Finally, it is essential to continuously monitor the performance of the simulation software and the outcomes of its applications. This allows for ongoing improvements and ensures that the software continues to deliver value.
Conclusion
The integration of advanced simulation software is poised to revolutionize Japanese manufacturing. By enhancing precision, reducing costs, and speeding up time to market, these tools offer substantial advantages. However, companies must navigate challenges such as initial investment and complexity to fully realize these benefits.
For procurement and purchasing professionals, leveraging data-driven insights and fostering collaborative relationships with suppliers are crucial strategies. The market conditions, marked by a growing demand for precision and stricter regulatory compliance, further underscore the importance of adopting advanced simulation tools.
By following best practices such as comprehensive training, pilot projects, and close collaboration with software vendors, manufacturers can successfully implement these tools and achieve significant improvements in efficiency and product quality.
As the global manufacturing landscape continues to evolve, Japanese manufacturers equipped with advanced simulation software will be well-positioned to lead the way, setting new standards for excellence and innovation.
資料ダウンロード
QCD調達購買管理クラウド「newji」は、調達購買部門で必要なQCD管理全てを備えた、現場特化型兼クラウド型の今世紀最高の購買管理システムとなります。
ユーザー登録
調達購買業務の効率化だけでなく、システムを導入することで、コスト削減や製品・資材のステータス可視化のほか、属人化していた購買情報の共有化による内部不正防止や統制にも役立ちます。
NEWJI DX
製造業に特化したデジタルトランスフォーメーション(DX)の実現を目指す請負開発型のコンサルティングサービスです。AI、iPaaS、および先端の技術を駆使して、製造プロセスの効率化、業務効率化、チームワーク強化、コスト削減、品質向上を実現します。このサービスは、製造業の課題を深く理解し、それに対する最適なデジタルソリューションを提供することで、企業が持続的な成長とイノベーションを達成できるようサポートします。
オンライン講座
製造業、主に購買・調達部門にお勤めの方々に向けた情報を配信しております。
新任の方やベテランの方、管理職を対象とした幅広いコンテンツをご用意しております。
お問い合わせ
コストダウンが利益に直結する術だと理解していても、なかなか前に進めることができない状況。そんな時は、newjiのコストダウン自動化機能で大きく利益貢献しよう!
(Β版非公開)